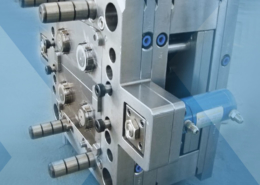
Injection Molding PLA From China - Topworks Plastic Mold - pla injection
Author:gly Date: 2024-10-15
The gas carves a hollow path through the middle of these thicker sections and creates the pressure needed to force the resin tightly against the walls of the mould, creating a smooth part that is structurally sound with no sink marks.
If you have a great idea, we can help bring it to life. We’ve done this before and enjoy becoming partners throughout product creation. From advising you through the mold sourcing process, to delivering your new product to customers, we want to work with you every step of the way.
Thin walls are often found in wearable devices and micro surgical tools, but can also be used in invasive equipment like catheter ablation tools and endoscopes.
According to a recent report from market insight firm 360 Research Reports, the global market for plastic injection moulding for medical devices is projected to reach over $42bn by 2026, up from $31.6bn in 2020.
The technique requires regular injection moulding equipment, but in order for walls to retain their structural integrity as they are created thinner, the base material used tends to be plastics like LCP, polypropylene and nylon – although silicone and metal can also be moulded this way.
But there are several techniques used by companies that produce these parts for medical devices, as well as specific materials better suited to some methods than others, like metals and composites.
Gas-assisted injection moulding is used to solve this issue by running gas (usually nitrogen) through channels built into the mould.
For certain medical device parts, metal isn’t necessary to create a mould for the injection moulding process, so 3D printing is commonly used to create moulds out of plastic instead.
“We looked for a US manufacturing partner for a full year before we finally found Extreme Molding. They found creative ways to help us bring costs down so that we could afford to manufacture in the US, and the fact that they also do fulfillment helps us realize additional savings as well. The Extreme Molding Team has integrity, tons of expertise, and maintains a high standard of quality in everything they do. All in all, they are excellent partners, and amazing people.”
While surface-borne infection is a general concern in hospitals, some medical devices have a greater need to remain hygienic than others, like tubes and respiratory masks.
Our range of in-house capabilities means that attention to detail will follow your product from start to finish, which means that each item has complete manufacturing traceability.
One of the most unique aspects about Extreme Molding is our full-service production model. Our model saves our clients time, money, and warehouse space. We mold your silicone products and take care of any post-production operations, such as assembly, packaging, and fulfillment.
Extreme Molding is a unique silicone molding company formed in 2002 outside Albany, N.Y. We pride ourselves on being one of the longest-tenured women-owned molders operating in the United States
Extreme Molding is the top choice for high-end consumer and life science products made from high-performance silicones. From our home just outside of Albany, NY, we partner with both small and large businesses throughout the United States, Canada and Europe.
In metal injection moulding, a powder made from the desired mix of metals is created using atomisation technology, and this powder is made into a pellet-like form called feedstock, which includes a plastic binding agent to make the substance easier to mould during the injection process.
The most recognisable technique on this list, 3D printing is not technically a form of injection moulding, but it does tend to be used to create prototypes to test a design before it goes into production using injection moulding.
At Extreme Molding, you will find between 75-100 professionals ready to be your partners in making your products successful. We are one of the few U.S. molders that are women owned and operated.
As one of the few American molders owned and operated by women, Extreme Molding is particularly passionate about partnering with the manufacturers of quality health care products for women and babies. We have been producing LilyPadz, self-adhesive silicone breast shields for nursing mothers, for more than a decade. Hospital-issued neonatal pacifiers also have been a core product for many years. When it became necessary to find an alternative to polycarbonate, we were first in the nation to mold BPA-free Eastman Tritan co-polyester with silicone to make a safer pacifier.
Another benefit is that silicone is biologically inert, meaning it doesn’t react with biological tissue and can be implanted safely in the body.
The 3D printing method can also be used to print actual injection moulds, using plastic or metal, but currently available technology is not advanced enough to print with the narrow part tolerances required in an injection mould – although many expect this will change in the future.
Extreme Molding has the technical capabilities to handle any complex silicone molding application. Over the years we have developed expertise in the markets of non-regulated healthcare products (specifically for women and infants), specialty consumer/light industrial products, pet supplies, and medical components.
Much like consumer products, medical device technology is becoming smaller as manufacturing processes become more advanced, and injection moulding has allowed the size of parts to keep pace with this demand for smaller devices.
From thin wall moulding with liquid crystal polymers (LCP) to the more commonly known 3D printing technique, we look at five types of injection moulding technology used to manufacture medical devices.
Once the mixture is injected, the binder is removed using solvent, thermal furnaces, a catalytic process, or a combination of methods, leaving only the metal and resulting in close to 100% density.
Although traditional injection moulding and even gas injection moulding have numerous uses in medical device manufacturing – sometimes the small size coupled with both manoeuvrability and strong mechanical properties necessitates the use of metal over plastic.
The term itself simply means creating the walls of a device in a way that makes them thin relative to the whole piece, but in practice this tends to mean walls thinner than 1mm.
The basic raw material for silicone rubber is sand, or silicon dioxide, which is processed into pure silicon and reacted with methyl chloride, after which a range of processing steps are used depending on the properties desired for the silicone.
When parts are created with regular injection moulding there’s a risk that sink marks can occur, making the final product look unsightly and potentially structurally weaker than it needs to be.
Material selection will depend on the device being produced and will have undergone testing at different levels of physical pressures and temperatures to ensure they can do the job.
Liquid silicone injection moulding is used for devices like these because of the chemical resistance of the rubber-like substance produced using this method, as well as the use of a clean production room so that no ambient air makes contact with the mould and lets dust and moisture into the mixture as it sets.
This method is used to create complex parts without any visual blemishes, but because the pressure exerted by the gas lessens if it doesn’t flow in a relatively straight line, it isn’t recommended for parts with sharp corners in their design.
The reason this happens is because thick areas of a mould cool more slowly than thin ones when the resin is injected, and without enough pressure to pack these areas tightly against the walls, the uneven distribution can cause a sunken appearance.
GETTING A QUOTE WITH LK-MOULD IS FREE AND SIMPLE.
FIND MORE OF OUR SERVICES:
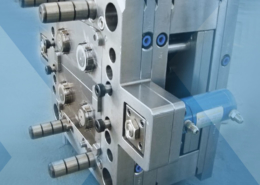
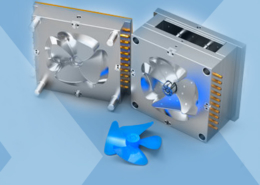
Plastic Molding

Rapid Prototyping
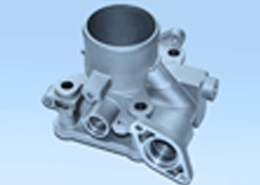
Pressure Die Casting
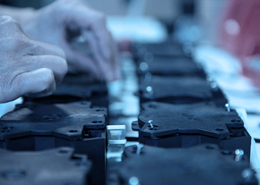
Parts Assembly
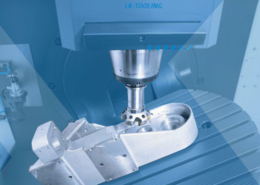