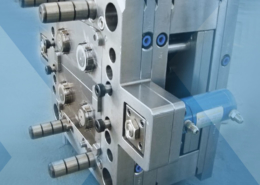
Injection molding of isotactic polypropylene - pp injection moulding
Author:gly Date: 2024-10-15
Extrusion molding is where the plastic is pushed out and out of the extrusion (die) section. A typical product is vinyl chloride pipe. This type of mold is a type of die that has various cross-sectional shapes, such as round and square, depending on the shape of the product.
Extrusion and injection molding are just two methods of plastic processing. Injection molding is suitable for three-dimensional product manufacturing whereas extrusion molding is only suitable for two-dimensional product manufacturing.
Relying on the screw for plasticizing and injection, it has good mixing and plasticizing properties and is used most often.
Except for a few thermoplastics, almost all thermoplastics can be molded by this method. Injection molding can also process some thermosetting plastics, such as phenolic plastics, etc.
The second stage is to make the extruded continuum lose its plastic state and turn into a solid, i.e., the desired product, by an appropriate method.
The cycle time of injection molding varies from a few seconds to a few minutes. The length of the cycle depends on the wall thickness, size, and shape of the product, the type of injection molding machine, as well as the type of plastic used, and the process conditions.
Simple operation, easy adjustment and update of molding molds, fully automatic production, and high production efficiency.
Wide range of applications, simple operation equipment, low investment, fast results, hygienic production environment, low labor intensity, and suitable for mass production.
MoldWiz®; XTEND®; PasteWiz® and CleanWiz® are registered trademarks of Axel Plastics Research Laboratories Inc. © 2012-2024 Axel Plastics Research Laboratories, Inc. All rights reserved. Sitemap | Privacy Policy | Cookie Policy | Human Rights Commitment Statement
Strong adaptability, except for fluorine plastics, all thermoplastics can be extruded, and some thermosetting plastics can also be extruded. The shape and size of the cross-section of the product can be changed accordingly by changing the head and mouth die so that various plastic parts with different specifications can be produced.
An injection molding machine (injection molding machine or injection molding machine) is the main molding equipment to make thermoplastic or thermosetting materials into various shapes of plastic products using plastic molding molds, injection molding is realized by injection molding machine and molds.
Most thermoplastics and thermosets, such as PVC, PS, ABS, PC, PE, PP, PA acrylic resins, epoxy resins, and mylar resins, etc.
Injection molding is to feed granular or powdered plastic from the hopper of the injection molding machine into the machine brief after heating and melting plasticization, under the pressure of a plunger or screw, the material is compressed and moved forward, through the nozzle at the front of the machine brief, injected into the closed mold with the low temperature at a very fast speed, after a certain time of cooling and shaping, open the mold to get the product. This molding method is an intermittent operation process.
Injection molding is molded in the mold, there are geometric limitations of the mold composition, and the melt strength requirements are not high. Although extrusion molding also has the geometric limitation of the mouth die, it is not fully cured after the exit of the die, and in this free state, it is sometimes not well formed due to the low melt strength, such as spinning.
In addition, after extrusion is often accompanied by subsequent free-state processing molding, such as thermoforming, and hollow blow molding, in these molding processes there are often different degrees of melt stretching, if the melt strength is low, it is easy to pull through. Therefore, injection molding generally does not require high melt strength, while extrusion is generally required.
DGMF Mold Clamps Co., Ltd mainly offers a wide range of Mold Clamps and Mold Components. Used in processing machinery especially on plastic injection molding machines, and pressure dies casting machines.
Axel Plastics Research Laboratories, Inc. | info@axelplastics.com | 50 Cambridge Drive | Monroe, Connecticut 06468 | 1 (800) 332-AXEL | (203) 590-2000
(3) Screw-plunger type plastic injection molding machine relies on the screw for plasticization and relies on the plunger for injection, the two processes are separated.
Extrusion mainly refers to the extrusion of the screw or plunger, so that the heat-melted polymer material is forced through the head die under pressure and formed into a continuous profile with a constant cross-section. The extrusion process mainly includes the processes of material addition, melt plasticization, extrusion, shaping, and cooling.
investment in injection molding equipment is relatively large, mold manufacturing costs are high, and product molding process conditions need to be strictly controlled.
Injection molding can be divided into the injection molding method and die-casting method. An injection molding machine, referred to as an injection molding machine or injection molding machine, is the main molding equipment for making thermoplastic or thermosetting materials into various shapes of plastic products using plastic molding molds, injection molding is achieved through injection molding machine and molds.
Injection molding is mostly used for thermoplastics. It is similar to extrusion molding, except that the molten plastic enters the closed mold through the nozzle, and the product is formed by solidifying inside the mold.
The following products represent those that are most commonly used in rotational molding. These releases are suitable for use with fabricated and cast aluminum and steel molds and plated metal surfaces. Solvent-based mold releases are generally preferable for cast iron molds.
The last thread at the mouth of the material is called the beginning of the transport section: the material here requires not plasticized, but to preheat, pressed, and squeezed solid, the old extrusion theory in the past that the material here is loose body, and later by proving that the material here is actually a solid plug, that is to say, the material here is solid after extrusion like a plug, so as long as the task of conveying is its function.
Injection molding is a cyclic process, each cycle mainly includes: dosing – melt plasticization – pressure injection – mold filling and cooling – mold opening and removal. After taking out the plastic parts, the mold is closed again for the next cycle.
Besides the Extrusion vs. Injection Molding, What Is The Difference article, you may also be interested in the below articles.
The first stage involves plasticizing the solid plastic (i.e., turning it into a viscous fluid) and passing it under pressure through a specially shaped mouth die into a continuous body with a cross-section similar to the shape of the mouth die.
Please note, AXEL can provide other types of internal mold release for resins other than polyolefins. If you are rotationally molding nylon or other types of resin, please contact us for a recommendation.
Injection molding generally does not have strict requirements for exit expansion. Extrusion has a nasty exit expansion. Therefore, the control of viscoelasticity of injection molding and extrusion materials will be different.
Plastic extruders go through three stages in the extrusion of plastics, namely, plasticization of raw materials, molding, and cooling. The length of the cycle depends on the wall thickness, size and shape of the product, the type of extruder, the variety of plastics used, and the process conditions.
Extrusion molding is also known as extrusion in plastic processing, in which the pressure of the hydraulic press is used to press out the die itself. It is a processing method in which the material is thermoplasticized by the action between the extruder barrel and the screw while being pushed forward by the screw, and is continuously pushed through the head to make various cross-sectional products or semi-products.
Injection molding requires high fluidity, especially for thin-walled products and large products. Extrusion is more relaxed because extrusion is open and there is no huge resistance to die reversal.
Sometimes, the easiest and best explanation comes from just seeing it, and that’s why we have this video portal. More here.
The injection molding machine uses the nature of plastic to melt into a liquid when heated to a certain temperature, injects the molten liquid into the closed cavity with high pressure, cools and sets the mold, then opens the mold and ejects to get the desired plastic product.
Extruders in extrusion should pay attention to the safety items are electricity, heat, mechanical rotation, and loading and unloading of bulky parts. The extruder workshop must be equipped with lifting equipment, loading and unloading the head, screw, and other bulky parts to ensure safe production.
Plastic films, nets, products with cladding, tubes, plates, sheets, rods, packing tapes, monofilaments, and profiles of a certain length continuous in cross-section, etc. Also used for powder granulation, dyeing, resin blending, etc.
Extrusion is mainly used to produce plates, tubes, rods, shaped materials, films, and other materials that can be produced continuously. In contrast, the injection molding process can only be produced intermittently, one mold at a time, beating the product.
The injection device and the clamping device are located on the same vertical center line, and the mold is opened and closed in the up and down direction. Its floor space is only about half that of a horizontal machine, so it is about twice as productive in terms of floor space.
A single screw is generally divided into three sections in terms of effective length, according to the size of the screw diameter, pitch, and depth to determine the effective length of the three sections, generally divided by one-third each.
GETTING A QUOTE WITH LK-MOULD IS FREE AND SIMPLE.
FIND MORE OF OUR SERVICES:
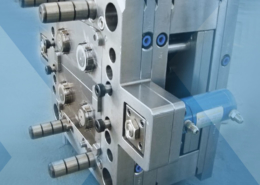
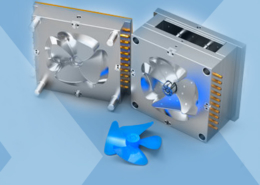
Plastic Molding

Rapid Prototyping
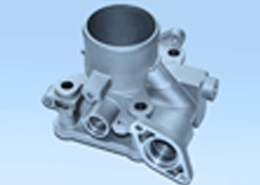
Pressure Die Casting
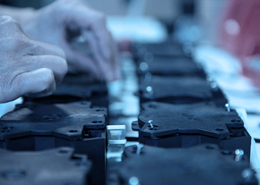
Parts Assembly
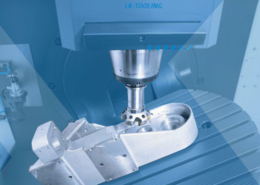