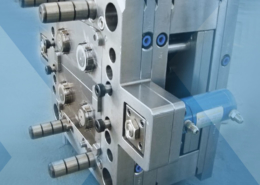
Injection Molding Material Selection Guide - polyester injection molding
Author:gly Date: 2024-10-15
– Reduced unit cost per part – Elimination of assembly step – Single production phase (reduced lead times) – Complex geometries possible – Improved integrity and durability
A very common application of the bi-injection process is to produce parts made of two similar materials but with different masstinted colours – in this case, creamy white with red.
Whether or not to use bi-material injection depends on various inherent constraints of your project and a preliminary study to validate your selection is generally required. Bi-injection is often used for large-volume production, complex geometries or in cases where over-molding is not suitable. Below we present some of the advantages and disadvantages of this process compared to mono-injection or over-molding:
For PBTinjection molding parts, most gates are applicable to melt’s rapid mold filling, which just requests the bigger caliber to prevent the contraction of the melt to reduce the loss of pressing force.
A third application of bi-material injection is to develop sealing functions with molding of joints directly on the part without the need for an assembly step after injection.
In single-material injection, resin is injected into a cavity and then, after an appropriate cooling time, the two mold halves are opened, and the part is ejected. In biomaterial molding, the two resins are injected into the mold. For this purpose, a space must be created in the mold to accommodate the additional resin. To do this, several bi-injection methods for tooling are available: transfer molds, molds with rotatory plate, molding with a rotating base, molding with core-back process.
Bi-injection molding, or 2k injection molding, is a plastic injection process allowing the production of a part made of two materials with different characteristics using a single press and a single tool. Examples of its use include parts requiring two colors or two different hardness levels. As a specialist in plastic injection molding, we’ve developed advanced know-how in dual injection molding of plastic materials.
In general, the process is fairly similar to conventional (single material) injection molding. The materials are brought to their melting point and then fill the mold cavities.
In the state of melting for PBT, because of its low viscosity, perfect liquidity (inferior to the nylon) and better mold shrinkage, it needs to prevent the phenomena of edge flowing and flashing of products.
Sincere Tech offers PBT injection moulding & custom molds, if you are interested in our service, contact us to get price by sending us an email.
PBT is a kind of crystalline polymer with a sharp melting point (225-235 Celsius degree). Crystallinity can reach 40%. When the temperature rises above the melting point, the liquidity of melt will become obvious. However, when changing from the molten state to the gruel state, it not only has the fast rate of cooling rate but has a fast crystalline speed.
The revolving speed of screw should be controlled to some extent to avoid friction heat impacting on the resin and screw speed generally doesn’t exceed 80r/min, mostly ranging from 25 to 60r/min. In order not to obstruct plasticizing of materials and make sure the air among particles of fabric materials can be discharged in time, during PBT’ shaping, the screw packing should be controlled at 10-15% of the injection pressure.
Our injection workshop is equipped with automated presses and is suitable for this type of process (up to 480 tones). Molds used for bi-injection are also manufactured in our in-house mechanical workshop.
In the actual operation, the temperature of PBT ranges from 240 to 260 Celsius degree. Owning to PBT’s fast cooling speed, injection speed should be slightly faster in order to prevent short shot of the products, obvious welding, and poor surface fineness caused by premature condensation during the filling process. However, it needs to prevent inadequate air exhausting and the flashing of products.
Specialist in plastic injection in China for more than 15 years. From the study to industrialization of parts and sub-assemblies, we can guarantee you secure, easy, qualitative and competitive cooperation.
This solution can be advantageous (in time and cost terms) while also satisfying very precise constraints. Bi-material injection molding involves a certain technicality and requires good mastery of tool design, materials selection and the injection phase itself. For this reason, we can support you upstream of your project to guarantee that it remains feasible and viable.
Bi-injection uses a press equipped with a second screw and hopper to inject the complementary material at the same time. The definition of the parting line is generally validated during the part analysis phase.
All in one service for new product development from part design, PCB design, prototyping, testing, mold/die/tooling making, massive production, assembly, inspection, and packing.
In view of PBT’s low viscosity, good fluidity, fast cooling and solidifying in the molding, most products don’t need a long molding cycle.
“We are very happy with your management & English communication, you are outstanding in issue solving and fast replier, frankly say you are the best plastic mold maker and the molding company I have been working up to know”
Influenced by factors of crystallinity, technology, mould, PBT has anisotropy to makes products warping and distorted during the molding process. Therefore, it should pay attention to proper process conditions and mold design.
In general, all thermoplastic polymers, from the simplest to the most technical, are compatible with the bi-injection process. In the case of flexible materials, the over-molded material is generally SEBS/TPE (Styrene-ethylene-butylene-styrene) or TPU (thermoplastic polyurethane) with different Shore hardnesses and possible textures. Most often, the two assembled components are different but similar and show good chemical compatibility.
Sincere Tech is Contract mould supplier in China that offers electronic new product research and development services as well as assembly company services. Contact us for more information.
Another application of bi-injection is injecting a material with another material to create a soft or grip effect in a functional gripping area (flexible or rigid material) – tactile grip effect on matte red.
– Feasibility study – Part analysis – In-house tooling design and development – Mold flow analysis – Machining of tools – Testing and validation – Series production
PBT contains esters gene and it will hydrolyze under the high temperature with the presence of moisture. Therefore, before starting the processing, it has to conduct the drying process.
To get products with better performance and good fineness as well as the smaller deformation in the molding, PBT’s appropriate temperature is 70 -80 Celsius degree.
Polybutylene terephthalate (PBT) has advantageous combination properties such as a convenient source of raw materials, and mature polymerization process has gotten easier, low cost and easily forming and processing. Nylon, polycarbonate (PC), polyoxymethylene and modified polyphenylene oxide are five major engineering plastics.
Depending on the properties of the part and the project constraints, our team of designers and engineers is responsible for determining the most suitable solution for you from among these different tools.
We regularly produce all types of bi-material parts according to our customers’ needs. Below are 3 examples of parts we have produced, illustrating the 3 primary applications of bi-material thermoplastic injection:
Before including a bi-injection solution in your specifications, please contact us to determine that it is feasible and cost-effective. Our internal organization allows us to support you in your analysis since we benefit from having a design office and mechanical workshop in house.
Other applications are also possible, depending on the type of part and the specifications of your product. Bi-injection molding also allows the production of transparent parts comprising an opaque zone (colored or not) to create colorful graphics and elegant finishes that enhance product functionality and added value. It’s possible to create rigid zones with flexible zones: hinge effect, shock-absorbing zones, push buttons, etc.
Nous utilisons des cookies pour optimiser notre site web et notre service.Conformément à vos choix, certains partenaires et nous pouvons accéder à votre terminal pour vous reconnaître via des traceurs comme des cookies, collecter, stocker, croiser, et transférer des données comme vos adresses IP et email, vos paramètres de logiciels, votre navigation ou votre localisation, à ces fins : Publicités standards et mesure de performance des publicités, Profil de publicités personnalisées et affichage, Contenu personnalisé et Mesure de performances du contenu, données d'audience, et développement produit.Nous vous en remercions et vous proposons d'appliquer vos choix à ces partenaires également. Vous pouvez bien sûr refuser leurs traceurs et traitements.
Applications of bi-injection molding are quite numerous in a variety of industries such as household, cosmetic and electrical products and increasingly in the automotive sector.
GETTING A QUOTE WITH LK-MOULD IS FREE AND SIMPLE.
FIND MORE OF OUR SERVICES:
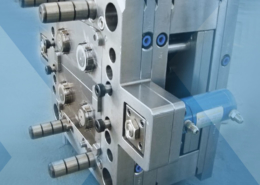
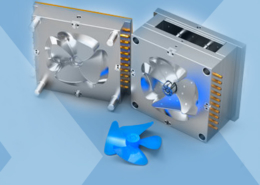
Plastic Molding

Rapid Prototyping
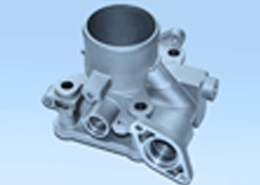
Pressure Die Casting
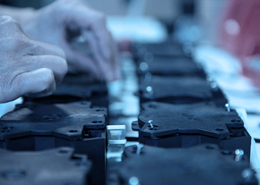
Parts Assembly
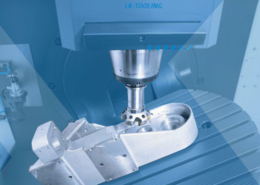