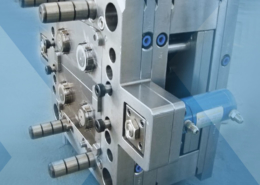
Injection molding machine - plastic press molding
Author:gly Date: 2024-10-15
The amount of material injected into the mold to fill the mold, including the feed system, is known as the “mold shot weight” or “product shot weight.” Spruce, runner, and gate weight are the components of shot weight, on the other hand. The distance the screw covers to fill the product, including the feed system, is known as the mold/product shot size.
Apart from wood and leather, the dashboards of automobiles are basically plastic, but there are differences between hard and […]
Maximum injection volume per cubic unit X maximum injection pressure (bar per cubic unit)/1000 = shot capacity of the injection unit.
According to the product appearance requirements, determine the parting surface. The position of parting surface should be beneficial to die processing, exhaust, demoulding, etc. The more products, the greater […]
This clamping unit’s benefits include electricity only being required during the magnetization and demagnetization phases, not while clamping, real-time clamp force measurement with many safety features and free maintenance.
The total weight or volume that the screw injects during one molding cycle is expressed as machine shot capacity (g)/machine shot size (mm), also known as the machine injection capacity.
The duration of residence times is influenced by the size of the shot and barrel, which may also impact the final product’s quality. Long residence durations and polymer degradation may come from small shot sizes that require little barrel capacity.
Weld Lines The flowing defects on product surface or the linear defects that are caused when melt fronts meet each other after splitting. Weld lines refer to the lines that occur on a plastic product surface when the cold slug melts. In areas of mold cavity where the molten plastic meets inserts or holes, areas with inconsistent flow speed/flow interruptions, where multiple flows meet or when jetting happens during mold filling, linear weld marks tend to occur due to imperfect bonding. […]
To stop melt from flowing back down the screw flights, a valve system may be installed at the screw’s downstream end. This is the injection or mold-filling stage.
Djmolding is a professional china plastic injection molding or moulding company with mould and dies development and manufacturing
Although it still exists in tiny machines and some specialized equipment, the single-stage ram unit is essentially obsolete due to its ineffectiveness in heating, mixing, and pressure transmission. It benefits from simplicity and affordability.
The largest amount of plastic injection mold that may be injected during a molding cycle is known as the shot size. Pellets are fed into the barrel and screw assembly through the hopper.
Some advantages of hydraulic clamping include easy control of clamp speed and support at any angle, simple measurement of clamping force, easy mode setup and clamp force adjustment, and its simplicity in maintenance.
Using the injection molding technique, raw plastic is melted, injected into the mold, allowed to cool and solidify, and then the finished object is expelled. The shot size is crucial because it prevents polymer underfill and flash. Other factors, such as the barrel capacity, also affect the general injection molding process.
The benefits of toggle type clamping include that it requires less money and horsepower to be done and provides a positive plan of the mold. Further, the setbacks of the toggle type clamping are that it requires high maintenance and is difficult to do.
According to the size of the machine, how much per injection, so as to determine the product ranking mode and the number of holes. The more the number of moulds produced, the lower the cost of injection moulding. Because the cost of injection moulding is calculated according to injection order.
To be safe, you can consider placing a two-barrel order. Even more, molds can be used with two barrels. When you order a second barrel with the new machine, you can be pleasantly pleased by its inexpensive cost. Barrels can be switched in under 30 minutes with the right specifications and an experienced operator, even if the barrel is hot.
Select the appropriate molding equipment, determine the reasonable process conditions, if the injection molding machine is too small to meet the requirements, too […]
Up until enough melt has accumulated to manufacture the next molding, the collecting melt forces the still-rotating screw back against a controlled resistance (the back pressure). The rotation of the screw halts here. It’s time to be ready for the melt.
On the other hand, big shot sizes and barrel fill levels greater than 50% may cause uneven melting and slow screw recovery.
The drawbacks to this type of clamping are that it costs more and is more expensive than a toggle system and a positive noun clamp.
The main determinant is the total number of products that customers need to produce. It takes about the same time to produce a product. Multiply the time to produce a product by the total amount of production the customer needs to produce to figure out how long it takes. Material and machine preparation time should also be taken into account before formal production. The preparation time of the machine is very short, because the equipment of the injection moulding factory […]
The purpose of the injection unit is to melt the plastic material uniformly before injecting it into the mold at a predetermined pressure and flow rate. These are demanding activities because fluoropolymers have limited thermal conductivity, a high specific heat, and high melt viscosity.
In the process of plastic injection molding, the raw material is introduced into the barrel, melts, and plastic is then injected into the cavity of the mold for cooling and solidification after the mould is closed. Finally, the mold opens, and the components are expelled.
Compared with other moulds, the structure of injection moulds is more complex and precise , the operation and maintenance of the product requirements are higher, so in the entire production process, the use of positive solutions and careful maintenance, maintenance to maintain the normal production of enterprises, improve the efficiency of enterprises, has a very important significance.
Oil pushes the RAM forward when it enters the cylinder under pressure, causing the moving platen and mold to shut. Additionally, the RAM comeback and mold are open when oil is released from the cylinder.
Further, the injection unit is often rated using the maximal injection pressure and available injection volume. The greatest possible pressure at the screw’s downstream end is called the injection pressure. This depends on the screw’s diameter and the force pushing against it.
Also known as “bumper”, but in fact it is only the auxiliary shell outside the bumper, not the body of the bumper. Bumper housing plays the role of cushioning and energy absorption, the working environment is relatively complex, and the volume is larger, so it is generally made of polypropylene (PP), because of its lighter weight and better corrosion resistance.
Magnetic modules inside the magnetic mold clamping plates or platens produce the clamping force. The interface panel can control mold clamping, mold changing, and magnetizing and demagnetizing the platens.
A mechanical device that amplifies force is a toggle. Two bars are connected and end with a pivot in a molding machine. One bar’s end is connected to a fixed platen, while the other is connected to a mobile platen. The toggle has a V-shaped shape when the mould is opened. The two bars form a straight line when pressure is applied to the pivot.
The two-stage screw/ram unit further separates the roles of flow and heat by using a ram for injection instead of a screw for mixing and heating. The idea is appealing because both are effective tools for their respective tasks.
With the continuous development of automotive electronics, higher requirements for product modeling, JasonMould here shares the five steps in the injection molding process. 1. The mold structure design A set of high-quality molds requires not only good processing equipment and skilled mold making workers. Another very important factor is good mold design, especially for complex molds. The mold design accounts for more than 80% of the mold quality. An excellent mold design is: under the premise of meeting the requirements of customers, the […]
Using the injection molding technique, molten material is injected into the mold’s cavity to create large quantities of plastic parts.
Again, numerous variations have been developed to address the complex issues at hand. A general classification of the variations can be made into four primary injection unit concepts:
Excellent weather resistance, guaranteeing long-term use without color, aging cracks (including heat and oxygen aging and light aging); Good chemical resistance, to resist the erosion of oil and daily chemicals; Easy moulding, the injection grade material should have enough fluidity to ensure the moulding of complex components and improve production efficiency. Economy requires material with high performance-price ratio. Material requirements for exterior accessories Weather resistance: Weather resistant materials such as AES, ASA (AAS), PC/PBT (PET) should be selected for parts that are not coated […]
Automotive plastic parts are used more and more widely. Automotive plastic parts are not only cheap, but also environmentally friendly, beautiful, convenient and durable. Nowadays more and more automobile metal parts are replaced by plastic parts. In order to ensure the normal operation of various parts, the maintenance and maintenance of automobile plastic parts are also very important. Maintenance methods of automotive plastic parts:
However, ensure that you don’t confuse it with the pressure in the hydraulic line acting on the injection cylinder, which drives the screw, nor should it be interpreted as the pressure required to fill the mold cavities. Due to pressure losses in the nozzle and mold feed systems, this is substantially less.
Additionally, larger screws typically have lower plastic pressure capabilities. Large shot sizes, which occupy more than 65% of the barrel’s capacity, frequently cause melt-quality problems, such as unmelt, poor melt uniformity, and long screw recovery times.
There are significant pressure drops when the plastic melt is forced into the injection nozzle and subsequently through the mold feed system and cavities. Simple rules cannot be used to calculate these pressure losses.
In this instance, the RAM of the hydraulic system is tied to the moving platen, and a clamping unit powered by a hydraulic cylinder is directly connected to the closed moving mold. The hydraulic cylinder has two sections: the oil input and the exit.
What is the injection mold? Injection mold is a tool for producing plastic products; it is also a tool for imparting complete structure and precise size of plastic products. Injection molding is a processing method used in mass production of complex parts of certain shapes, specifically refers to plastics that melt by heat from injection molding machines. High pressure is injected into the cavity, and after cooling and solidification, a molded article is obtained. Mold application: Mold is the basic process equipment for […]
Small shot sizes that occupy less than 20% of the barrel’s capacity frequently result in extended residence times, which in turn cause polymer degradation and inadequate process control.
Additionally, the two-stage ram is all but obsolete. The ram is still an ineffective mixer and heater despite an attempt to enhance it by separating the heating and pressure flow operations.
Mold closure is maintained against forces created when plastic is pushed into a closed mold by injection pressure using a clamping unit for an IMM. It has a drive system that can move the injection molding machine’s moving platen in at least one direction.
A short shot is the incomplete filling of a mold cavity which results in the production of an incomplete part. If a part short shots, the plastic does not fill the cavity. The flow freezes off before the flow paths have completely filled. To ensure the finished part is of good quality, the part must also be adequately packed with plastic. Therefore the question to ask is not only, “Will the part fill?” but also, “Can a good quality part be made?” Causes
GETTING A QUOTE WITH LK-MOULD IS FREE AND SIMPLE.
FIND MORE OF OUR SERVICES:
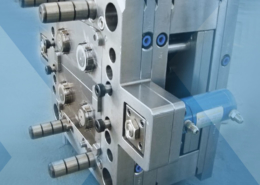
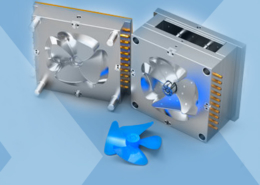
Plastic Molding

Rapid Prototyping
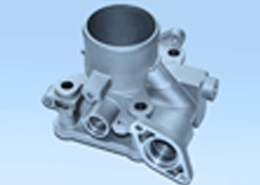
Pressure Die Casting
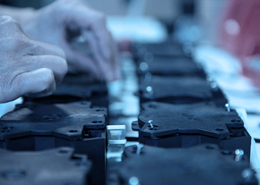
Parts Assembly
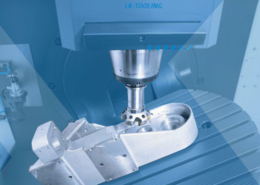