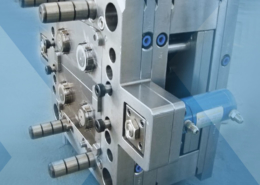
Injection Molding for Medical Devices in a Nutshell - medical injection moulding
Author:gly Date: 2024-10-15
At Bennett Plastics, we offer decades of expertise in full-service custom plastic injection molding which is suitable for customers large and small. Contact us today to learn more about our complete range of in-house capabilities.
Standard production runs for injection molding normally run from hundreds of thousands into even millions of parts, so the time and cost of mold creation are minimal compared to the value they provide. Short runs tend to be 10,000 parts or fewer, even into the hundreds. Costs for these smaller runs are usually reduced by using less expensive materials for molds, such as aluminum or a lower grade of steel. These molds produce the same quality products but are usable for a shorter number of products.
Founded in 1950, Thogus is an established, family-owned custom plastic injection molder and contract manufacturer headquartered in Avon Lake, Ohio.
At Thogus, we understand the demands of the medical device industry and can advise you on the regulatory requirements, validation processes, and material selection for your medical plastic injection molding project. We have the experience to provide support during each phase of a project’s life cycle; from our manufacturing by design process to selecting materials capable of withstanding harsh conditions to cleanroom assembly, we are here to help you succeed.
With your patients’ health and lives on the line, medical practitioners need reliable, high-quality devices and equipment. We have collaborated with healthcare professionals for decades to develop and manufacture plastic injection molding for medical parts and devices for a variety of applications, including:
Plastic injection molding is a growing, cost-effective method of manufacturing medical devices and parts. Along with its ability to produce complex designs that meet the stringent cleanliness requirements, medical-grade plastic injection molding offers high tensile strength as well as chemical and high-temperature tolerances. Since its inception, medical devices that are manufacturing with injection-molded plastic have contributed to a reduction in medical costs and increased patient safety.
Plastic injection molding is one of the most popular manufacturing techniques in use worldwide, in large part because a high volume of identical parts can be rapidly created from a single mold without a loss in quality. Its main drawback is tied to the expense and time necessary to design and produce the steel mold used in production. While these costs are inconsequential over a long production run, they can be high for small runs, so adapted techniques for short production runs can make small volumes just as worthwhile.
The healthcare industry depends on medical parts and devices using medical-grade plastic injection molding that is durable, reliable, and meets regulations.
GETTING A QUOTE WITH LK-MOULD IS FREE AND SIMPLE.
FIND MORE OF OUR SERVICES:
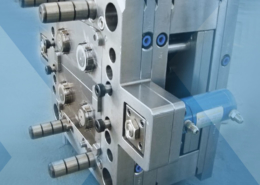
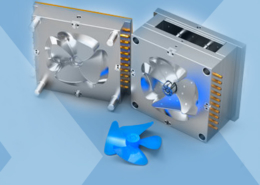
Plastic Molding

Rapid Prototyping
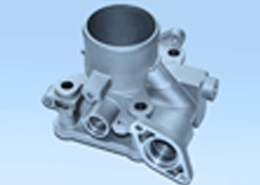
Pressure Die Casting
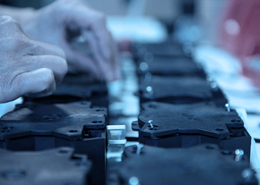
Parts Assembly
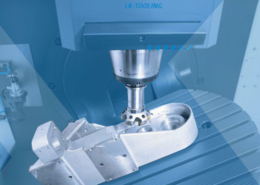