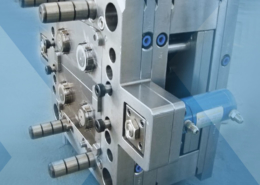
Injection Molding for Medical Devices in a Nutshell - medical injection molding
Author:gly Date: 2024-10-15
Whether the job calls for an intricate or simple part, tooling determines the quality of the plastic injection molding process and the components created.
Since they are the foundation of the plastic molding process, tool design requires time, effort. And expertise. The suitable mold material is the first consideration. Most plastic injection molds are made of steel, aluminum, or alloys.
This first tool is put through its paces to test its functions properly and produce the specified part. During this stage, modifications and mold texturing can occur. Once this stage is complete, the samples are sent to the contract manufacturer.
After the heated material fills the pre-formed mold, it begins to harden as it cools. Then, the hardened plastic and the tool can separate, leaving a new part and a tool that is ready for re-filling.
Think about it. Plastic injection molding involves the science of shooting hot, molten resin into the cavity of a mold. However, the design process is undertaken through a process of intuition, technique, and plain old trial and error.
Get an injection mould worth its weight (without the wait). Send us a message or lock in a meeting with a CNC prototyping professional.
As you can see, there is more that goes into the manufacture of precision molded parts than meets the eye. Plastic injection tooling is both a scientific and a creative process.
For example, tool design engineers use flow analyses to optimize the mold, including finding the best locations for parting lines, gates, and ejection locations. Design engineers then collaborate with toolmakers in creating a tool sample.
Add agility to your prototyping with this exciting additive manufacturing technology. Our advanced 3D printing services make ideas materialise before your eyes, efficiently and cost-effectively. In expert hands, 3D printers are ideal for producing NPI (new product information) models for products comprising plastic components, quickly delivering a prototype you can present, test, and refine.
Just as a baker pours their batter into the right baking pan, a skilled machinist pours liquidized plastic into a mold that is in the shape of a part. This mold, typically known as tooling, is the key to the creation of a high-quality precision component.
Sensors placed on the surface of the tool can monitor the cooling rate and the cavity pressure profile. Tooling engineers also pay close attention to the following factors:
Ready to step into the next dimension of plastic prototyping? Get in touch or book a meeting with our team to discuss your project.
Ready for a rapid assembly of your prototype that will progress your project to the next phase? Send us a message, give us a call, or arrange a time for an obligation-free consultation with an expert.
When only the highest-grade plastic prototype will do, or multiple prototypes are required for distribution to various stakeholders, it can be worth making a custom injection mould. Achieve near-perfect precision and repeatability with the most professional plastic prototyping method available.
Since steel can tolerate high temperatures and pressure, steel tooling can produce millions of plastic parts. On the other hand, aluminum tooling is less expensive to create but can only produce in the thousands of plastic parts.
The ultimate goal of this complex interaction is to create a high-quality precision part that is on time and on budget. If you have questions about plastic injection tooling and how it can work for your company, please contact us today.
Tooling for a plastic injection mold project also includes acquiring all the components and machinery needed for the job, including gauges, jigs, fixtures, and other equipment. The effort and efficiency of this process have much to do with the quality and the cost of the end part.
The process from prototype to production line can take months to complete, but each step creates more value in the long run. In fact, once the design and testing process is complete, the actual manufacturing process is automated and efficient.
The steps involved in prototyping may vary depending on the product or service being developed, but generally include the following:
Additionally, prototyping can help to communicate design concepts to stakeholders, such as investors, clients, or team members. It can also help to generate excitement and interest in a product, which can be important for marketing and fundraising efforts.
Backed by in-house 3D CAD and industrial design proficiency, our custom prototyping services can accommodate differing levels of concept maturity. Whether you have full CAD files, a few sketches, or need help getting the idea on paper (then into a computerised format), we can convert your assets into production-ready files for plastic and metal component manufacturing.
Plastic molding tooling can produce molded parts that meet the unique requirements of each project. Tooling design begins with the prototype phase.
Sophisticated components demand sophisticated tooling. The tooling process requires accurate monitoring for consistent, reliable part production.
Manage the demands of prototypes with metal parts with our prompt and precise CNC machining. Expertly automated to turn out metal components for instant assembly, or in combination with additional plastic parts as per your prototype’s requirements.
Prototyping is important because it helps to identify potential issues in a product or service early in the development process. This can save time and money by allowing design flaws to be corrected before a final product is produced.
Want to set the highest standard from prototype to mass production? Send us some details of your prototyping project or arrange a one-on-one with an expert today.
Low-volume prototype tools are created through 3D printing, machining, and cast urethane. With these prototype tools, machinists can troubleshoot the tooling design, reducing the chance for error in the manufacturing and assembly process – and saving time and expense — later.
The next step is to place the new design on the production line. Here the tool is carefully observed and validated. After it passes this scrutiny, the mold enters a regular production schedule, where it is routinely monitored for wear and tear and any other issues that could affect part quality.
At ASPM, we showcase our established history of quality tooling and molding by implementing our rigorous approach to plastic product development. We offer complete support from product design and feasibility, through routine injection mold maintenance and repair. Our highly trained staff is prepared to handle plastic projects with varying complexity in our robust 24-hour facility. Contact us today to discuss your next project.
Establishing a prototype can be critical to your manufacturing project and demands speed and precision in equal measure. With comprehensive capabilities across plastic and metal component manufacturing, we’ll swiftly lay down building blocks for your success while ensuring quality control.
Need physical proof of your latest and greatest invention? Something you can present to management, a client, potential investors, or even just show off to your friends? Our rapid prototyping services can help. Drawing on our 3D printing capabilities, our efficient experts deliver punctual prototypes to your specifications.
We offer constructive feedback and innovative inputs because we think your prototype deserves no less! Our experience has gifted us unique insights into what works (and what doesn’t) in modern manufacturing, and we readily share these with you, while recognising your right to make the final call.
It’s important to note that prototyping is an iterative process, and multiple rounds of testing and revisions may be necessary before a final product is produced.
GETTING A QUOTE WITH LK-MOULD IS FREE AND SIMPLE.
FIND MORE OF OUR SERVICES:
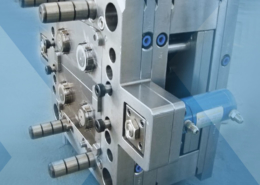
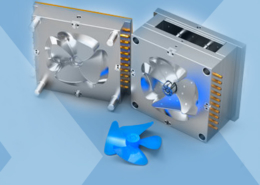
Plastic Molding

Rapid Prototyping
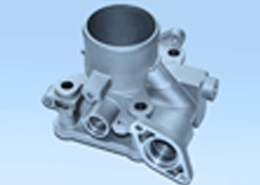
Pressure Die Casting
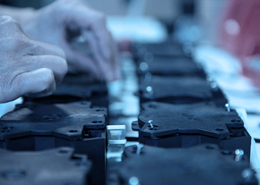
Parts Assembly
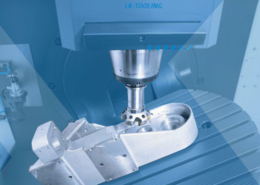