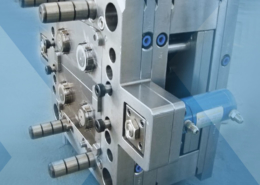
Unveiling the Versatility of Rubber Plastic Molding: A Comprehensive Exploration
Author:gly Date: 2024-06-08
Rubber plastic molding stands as a cornerstone of modern manufacturing, combining the flexibility of rubber with the durability of plastic to create a diverse range of components vital to numerous industries. From automotive seals and gaskets to medical devices and consumer electronics, rubber plastic molding offers unparalleled versatility, precision, and performance. In this comprehensive exploration, we delve into the world of rubber plastic molding, unraveling its significance, applications, and impact on global manufacturing.
Introduction: Blending Strength with Flexibility
In the realm of manufacturing, the marriage of rubber and plastic through molding processes represents a fusion of strength, flexibility, and durability. Rubber plastic molding techniques, such as injection molding and compression molding, enable the creation of complex geometries, intricate details, and customized features that meet the exacting requirements of diverse applications. As such, rubber plastic molding has become indispensable in industries where resilience, sealing capabilities, and chemical resistance are paramount.
Applications Across Industries
The applications of rubber plastic molding span a wide spectrum of industries, each leveraging the unique properties of the material blend to address specific challenges and performance criteria. In the automotive sector, rubber plastic molded components play a vital role in sealing systems, vibration damping, and interior trim, contributing to vehicle safety, comfort, and performance. Similarly, in the healthcare industry, rubber plastic molding is utilized in the production of medical devices, surgical instruments, and drug delivery systems, where biocompatibility, sterilizability, and durability are critical considerations.
Material Selection and Performance
The choice of materials in rubber plastic molding is guided by the desired performance characteristics, environmental conditions, and regulatory requirements of the application. From thermoplastic elastomers (TPEs) to silicone rubber blends, manufacturers have a wide array of material options at their disposal, each offering distinct advantages in terms of flexibility, resilience, chemical resistance, and cost-effectiveness. By selecting the appropriate material blend and optimizing processing parameters, manufacturers can achieve the desired balance of properties to meet the functional and performance requirements of the molded components.
Process Optimization and Efficiency
Achieving consistency, repeatability, and cost-effectiveness in rubber plastic molding requires careful process optimization and control. By leveraging advanced molding technologies, such as multi-shot molding and overmolding, manufacturers can produce complex assemblies with integrated seals, gaskets, and functional features in a single operation, reducing production lead times and assembly costs. Moreover, the integration of automation and robotics streamlines production workflows, minimizes human error, and enhances overall process efficiency, enabling manufacturers to meet stringent quality standards and customer expectations.
Quality Assurance and Regulatory Compliance
Ensuring the quality and reliability of rubber plastic molded components is paramount in industries where safety, performance, and regulatory compliance are non-negotiable. Through rigorous quality control measures, including dimensional inspection, material testing, and functional validation, manufacturers uphold the highest standards of product integrity and performance. Moreover, adherence to regulatory requirements, such as FDA approvals and ISO certifications, demonstrates a commitment to quality management systems and product safety, instilling confidence in customers and end-users alike.
Economic Considerations and Market Dynamics
The economic viability of rubber plastic molding is influenced by a myriad of factors, including material costs, production volumes, labor rates, and market demand. While economies of scale and process optimization can drive down unit costs for high-volume production runs, niche markets and specialized applications may require customized solutions and higher upfront investments. Furthermore, fluctuations in raw material prices, currency exchange rates, and geopolitical factors can impact production costs and profitability, underscoring the importance of strategic planning and risk management.
Conclusion: Embracing Innovation and Opportunity
In conclusion, rubber plastic molding represents not just a manufacturing process but a gateway to innovation, efficiency, and performance across industries. By harnessing the unique properties of rubber and plastic, manufacturers can create components that meet the evolving needs of customers and markets, driving progress and prosperity in a dynamic global economy. Looking ahead, the future of rubber plastic molding holds promise for further advancements in materials science, process technologies, and product design, paving the way for a new era of manufacturing excellence and opportunity.
GETTING A QUOTE WITH LK-MOULD IS FREE AND SIMPLE.
FIND MORE OF OUR SERVICES:
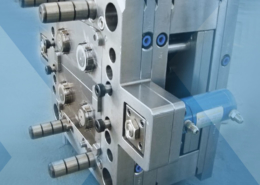
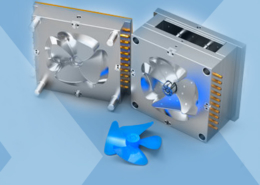
Plastic Molding

Rapid Prototyping
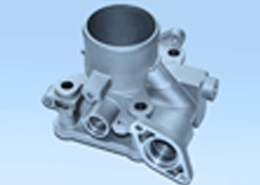
Pressure Die Casting
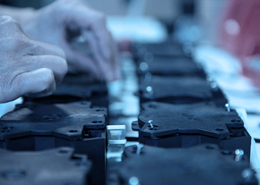
Parts Assembly
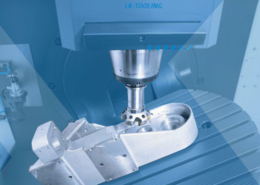