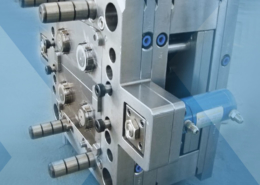
Injection Molding Costs: Tips and Facts You Need to Know - injection mold toolin
Author:gly Date: 2024-10-15
Injection molding machine is divided into 2 units i.e. a clamping unit and an injection unit. The functions of the clamping unit are opening and closing a die, and the ejection of products. There are 2 types of clamping methods, namely the toggle type shown in the figure below and the straight-hydraulic type in which a mold is directly opened and closed with a hydraulic cylinder.
The screw is rotated to melt plastic introduced from the hopper and to accumulate molten plastic in front of the screw ( to be called metering ) . After the required amount of molten plastic is accumulated, injection process is stared.
The process of how to get plastic parts made involves four basic steps: come up with a design, decide on a manufacturing process, build a prototype, and then produce the design. Choosing an experienced plastic parts manufacturer who can provide support and feedback through every step of the process increases your chance of success. At Reading Plastic, we’ve been helping clients turn their plastic part designs into finished products for over three decades.
A mold is a hollow metal block into which molten plastic is injected to from a certain fixed shape. Although they are not illustrated in the figure shown below, actually there are many holes drilled in the block for temperature control by means of hot water, oil or heaters.
Molding condition means cylinder temperature, injection speed, mold temperature etc. set in a molding machine to obtain required moldings, and the number of combinations of conditions is innumerable. Depending on the conditions selected, the appearances, dimensions, and mechanical properties of the molded products change considerably.
Injection molding is a method to obtain molded products by injecting plastic materials molten by heat into a mold, and then cooling and solidifying them.
Molten plastic flows into a mold through a sprue and fills cavities by way of runners and gates. Then, the mold is opened after cooling process and the ejector rod of the injection molding machine pushes the ejector plate of the mold to further eject moldings.
The position of change from speed control to pressure control is set at the point where either screw position or injection pressure reaches a certain fixed value.
The method is suitable for the mass production of products with complicated shapes, and takes a large part in the area of plastic processing.
At Reading Plastic, we know how to get plastic parts made. We’ve helped clients in nearly every industry get the precision plastic parts they need, on-time and on-spec. If you have a project in mind, call us today at 610-926-3245 or email site2@readingplastic.com. We look forward to making your designs a reality!
For the properties when reprocessed materials are used, please refer to "reprocessing capability" in the plastic data base.
Sprues and runners among moldings are not products. These portions are sometimes discarded, but in other cases they are finely reground and reused as materials for molding. These materials are called reprocessed materials.
The standard molding conditions for our materials are shown below. Please click the mouse at the following names of plastics.
A molding consists of a sprue to introduce molten resin, a runner to lead it to cavities, and products. Since obtaining only one product by one shot is very inefficient, a mold is usually designed to have multiple cavities connected with a runner so that many products can be made by one shot.
If the length of the runner to each cavity is different in this case, the cavities may not be filled simultaneously, so that dimensions, appearances or properties of the moldings are often different cavity by cavity. Therefore the runner is usually designed so as to have the same length from the sprue to each cavity.
While molten plastic is flowing in a mold, the machine controls the moving speed of the screw, or injection speed. On the other hand, it controls dwell pressure after molten plastic fills out cavities.
We use cookies on this website to ensure your user experience. Please click the button if you agree to the use of cookies. When you keep browsing this website, this will also mean that you are giving consent to the use of cookies.
Reprocessed materials are not solely used as materials for molding but usually used after blending with virgin pellets, since there is possibility of deterioration in various characteristics of the plastics because of the initial molding process. The maximum allowable limit for the ratio of reprocessed materials is about 30 %, because too high ratio of reprocessed materials may spoil the original properties of the plastics used.
GETTING A QUOTE WITH LK-MOULD IS FREE AND SIMPLE.
FIND MORE OF OUR SERVICES:
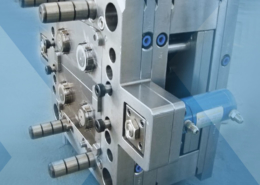
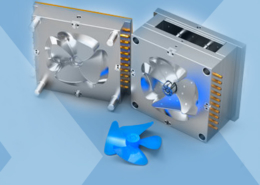
Plastic Molding

Rapid Prototyping
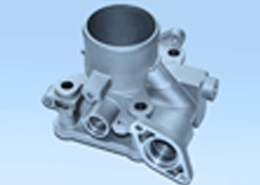
Pressure Die Casting
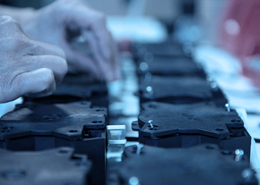
Parts Assembly
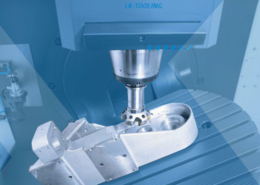