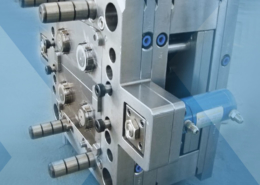
Injection Molding Cost - Prototool - plastic injection molding cost
Author:gly Date: 2024-10-15
Plastic mold manufacturing is a technological process that takes place with the completion of various stages. Plastic Injection Mold Manufacturing Production stages:
3D printing: 3D printing is a powerful and swift moulding solution that can create many moulds at a fast pace for a very low cost. The advantage of 3D printing is that it takes away a lot of the human labour requirements that CNC machining requires. This is another avenue of saving costs.
Although the coloring processes are optional in the plastic injection mold manufacturing stages, today, the color preferences are among the processes that are decided before the manufacturing process. In addition, the most common rules that should be known in the manufacture of plastic molds are as follows;
Plastic injection mold manufacturing is a very popular technological process that facilitates plastic production. Plastic molding, which is increasing day by day, is defined as the creation of product templates by combining the determined parts with the help of machinery. Construction phase of plastic injection molding is the process of melting plastics in a plastic injection molding machine and then injecting them into a mold under high pressure. In this process, the material is cooled, solidified, and then the two halves of the mold are opened and released. Plastic molds are obtained in desired sizes and molds.
The most cost-effective injection moulding solution is to produce low volume parts with smaller injection moulding machines and 3D printed moulds. There are many manual injection moulding machines that can sit on a bench. Although, if you are looking for a bigger production operation, there are bigger, industrial level machines.
The process itself is fast, intensive, and requires a lot of energy. The heated plastic is quickly introduced to a mould inside, which takes shapes. The exact kind of plastic that is used depends upon the kind of thing that is being manufactured. Many different thermoplastics are used in the injection moulding process, such as ABS, PS, PE, PC, PP, and TPU. But the injection moulding process isn’t limited to thermoplastics, as certain metals and ceramics can be introduced to a mould too in some circumstances.
Due to the intensity of this process, many wonder how much the entire injection moulding process costs. The biggest factor in the process is the cost of the mould itself. The designing and building of the mould can be time-intensive and take intricate work, depending upon requirements.
Electrical Discharge Machining (EDM): The priority use of the EDM method is to create highly complex mould designs that even CNC machining has trouble achieving. This method uses electricity and diodes in a dielectric fluid to shape a mould. EDM has a high level of accuracy and almost never requires any post-processing that other machining and printing methods might require. This is due to the freeform nature of the moulding process.
Due to the costs and the headache that is required to set up an injection moulding process in-house, it is recommended that this process is outsourced. So, contact us at 3DPrintings.com.au. We offer plastic injection moulding in Australia at affordable rates.
CNC Machining: This is arguably the most commonly used process for producing moulds. CNC machining can work with many different materials. But it is mainly responsible for producing stainless steel or aluminium moulds that can handle the repeatability factor that mass-production requires. CNC machining is also very precise and capable of producing very accurate and intricate moulds. But the one drawback to this method is that it is quite time-intensive, which can sometimes be an issue.
Injection moulding, as you can gather by the name, is a process that is used to manufacture plastics. Mass-production of plastic products with tight tolerance through injection moulding has become quite common. It’s a cost-effective, quick, and efficient solution. Injection moulding has high repeatability, which is why it is the leading mass-producing technique for plastic products.
There is also the factor of labour costs that comes with operating EDM machines and CNC machines. Even 3D printing requires an operator and a designer to get the job done.
The parts involved in the mold manufacturing process need to be carefully designed to facilitate production. Products made in plastic injection machines are primarily designed by an industrial engineer or a designer. The advantages of plastic injection mold manufacturing provide long-term convenience. It minimizes the need for maintenance, especially by enabling mass production and being manufactured from special steel. Mold manufacturing, which also offers the opportunity to obtain many products, is very popular in every sector. The first disadvantage that we come across is the cost. Production process of the plastic molds can take some time. The requirement for a qualified workmanship, expensive workbenches and equipment increase the costs. Another disadvantage is that the plastic mold period is long in cases where the production phase needs to be accelerated. For detailed information about plastic injection mold manufacturing, you can contact the Moldmore expert team.
Injection moulding requires special-purpose machines that can handle the injection process. These machines can range from small in-house machines to massive industrial moulding machines that are used in mass production.
Moldmore is a company that has been manufacturing molds for over thirty years. It is specialized in thin wall plastic containers and lids. Most of these molds are manufactured according to the in-mold labeling system.
The cost of an individual process is hard to track as it depends on many factors. The price can be as little as 100 dollars and up to 100,000 dollars. The exact cost will depend on your requirements and the kind of material that is used. However, variable costs in injection moulding are low and therefore stay consistent. And, of course, getting many units of a product is bound to reduce the overall costs of each individual unit.
There are many injected materials that are used in the injection moulding process, as discussed above. The total cost of the operation depends upon the kind of thermoplastics being used. ABS, PS, PE, PC, PP and TPU are some of the main thermoplastics that are widely used.
We currently support .3mf, .iges (.igs), .obj, .step (.stp), .stl, .wrl and .zip (with models and textures) files up to 25mb. If you have multiple files please send us on info@caddeziners.com.au or you can upload zip file here.
LocationNew South WalesVictoriaQueenslandSouth AustraliaWestern AustraliaTasmaniaNorthern TerritoryAustralian Capital Territory
GETTING A QUOTE WITH LK-MOULD IS FREE AND SIMPLE.
FIND MORE OF OUR SERVICES:
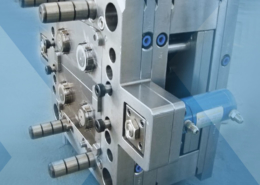
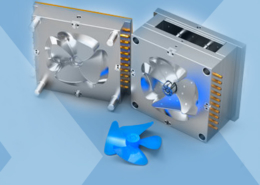
Plastic Molding

Rapid Prototyping
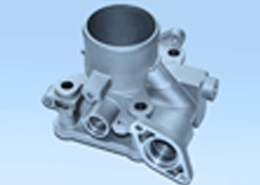
Pressure Die Casting
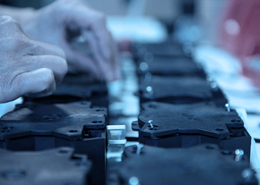
Parts Assembly
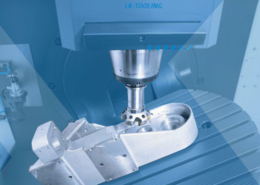