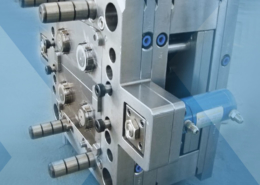
Injection molding and characterization of PMMA-based ... - pmma injection moldin
Author:gly Date: 2024-10-15
Simple geometric molds can be efficiently machined using larger milling tools, requiring less time. In contrast, molds with complex shapes necessitate the use of smaller milling tools for detailed work, and some parts may require EDM (Electrical Discharge Machining), significantly extending the machining time.
There are many types and grades of hot runners, with prices ranging from a few hundred to several thousand dollars, and they require the use of a temperature control unit. While hot runners offer significant benefits, they also lead to an increase in costs.
Based on the size of the plastic parts, the number of cavities, and the basic structure (whether there are sliders, cores, two-plate molds or three-plate molds, etc.), we can calculate the size and weight of the steel plates and then get the cost of them.
The mold assembly is time-consuming work. It includes adjusting the dimensions that are not in place during machining, making all the moving parts fit with appropriate tightness, and debugging the issues that were not anticipated in the design stage. The more complex or the more expensive the mold is, the longer it takes to match the mold. For example, a 10,000-dollar worth of mold may take 50-100 hours to match.
To learn more about our injection molding capabilities, contact us today at info@uftooling.com to discuss your project with one of our team members, request a quote. Let UFtooling be your trusted partner for your plastic injection molding needs.
This is due to the fact that pricing is based on the mold’s net weight, yet the actual material used often exceeds this amount. Furthermore, the pricing doesn’t account for mold accessories, which are sold as complete products not priced by weight, nor does it include the materials for electrical discharge machining (EDM), such as copper or graphite electrodes. These factors add complexity to the mold’s pricing structure.
Medium-sized manufacturers might offer less focus on your project and cannot guarantee their technical proficiency, similar to smaller factories.
Material costs generally constitute 20-35% of the total mold price. However, for some larger and simpler molds, the material costs can represent 60-70% of the total cost, such as the chair shown in the example below.
The hardness of standard mold steel ranges from HRC28 to HRC54. Mold steels with higher hardness require heat treatment followed by precision machining, making the harder molds more expensive due to the longer processing time.
Since the steel for the Core and Cavity are made of more expensive steel, they are often embedded into the A/B plates so they can be made smaller.The calculator will automatically compare the results of embedded and single-piece designs and choose the better option.
The rationality of the design, such as the design of the gate and the arrangement of cooling channels; the precision of the machining, with minimal marks from later refinements; and a manual test of pushing the ejector plate, which should move smoothly, indicating overall machining accuracy.
As the mold size increases, the Price Factor decreases. Small molds have lower material costs, yet the reduction in other expenses is not as significant. Conversely, with larger molds, the increase in other costs does not scale proportionally with the rise in material costs.
If a small mold manufacturer quotes a base price, a medium-sized manufacturer may quote 1.5 to 2 times that amount, while a large manufacturer might quote 2 to 2.5 times the base price. This variation is due to differences in overhead costs and profit expectations among the manufacturers.
A skillful designer’s hourly rate can be 30 to 40 dollars, this sounds a bit high, but they can finish the design of 8-10 simple injection molds in a day (12 hours), so their charge is reasonable for their output.
Lower Tooling Costs and Shorter Turnaround Times: Aluminum tooling is much easier and cheaper to manufacture than steel tooling, reducing initial costs and speeding up the production process. Greater Design Flexibility: The lower costs and faster production times for aluminum tooling allow for more frequent and cost-effective design changes, accommodating modifications in component design with ease. Easier Entry to Market: The reduced initial costs and shorter lead times make low-volume injection molding an attractive option for startups and small businesses with limited budgets, facilitating quicker market entry.
Tax and profit: Except for the tax and other overhead fees, a reasonable profit margin should be around 15-30%. Sometimes it may be a little higher for more challenging jobs, the extra profit is for the risk (uncertainty) the mold maker is going to take. Remember the mold manufacturer is responsible for delivering the final result, which is the injection mold that can smoothly produce the plastic parts with good quality, but not merely making a mold that ends up with excessive molding defects.
However, for some plastic parts with special requirements, the price calculated by this calculator will be low, such as this LED lamp lens, which will give a much lower price than the actual price. This is because the lens has high requirements for the projected light pattern, and its geometric shape accuracy is very high.
Due to the common occurrence of undercuts in the designs of plastic parts, injection molds frequently include sliding mechanisms. These mechanisms are primarily of two types: one that transforms vertical movements into horizontal ones using inclined rails, and another that employs hydraulic or pneumatic cylinders for movement.
Certain features require EDM (Electrical Discharge Machining) to be completed, utilizing electrodes made from copper or graphite.
Greater Capacities at Faster Speeds: High-volume operations can produce hundreds of thousands or millions of pieces efficiently, making it suitable for mass production. Lower Unit Costs: Although the initial tooling costs for high-volume injection molding are higher, the durability of steel molds allows for extensive production runs before replacement is needed. This durability leads to lower unit costs as the volume of production increases. Better Suitability for Automation: High-volume injection molding is well-suited for automation, which can further enhance production capacities and reduce unit costs, contributing to greater overall efficiency.
Here are some examples of mold prices to verify the accuracy of the mold price calculator. It can be seen that for plastic products with general complexity and accuracy, its valuation is still close.
This is because achieving higher accuracy necessitates the use of more sophisticated and expensive equipment, as well as slowing down the tool’s movement (feeding) to reach the desired level of precision.
Make sure the length (L) is bigger than the width (W), otherwise, their values will switch automatically.Note: Maximum value for L, W and H: 600mm Minimum value for L, W and H: 8mm (please use 8mm if the value is smaller)
Although the price of mold steel, which ranges from $2 to $20 per kilogram, might suggest that mold costs are relatively high, this isn’t necessarily the case. Material costs alone can make up 20% to 35% of the total mold price, and can even surpass 50%.
The cost of molds based on weight typically ranges from $8 to $50 per kilogram. This variation is influenced by the type of steel used for the mold, as well as the mold’s complexity and size.
High-volume injection molding operations typically involve producing several hundred thousand to millions of pieces. This process uses hardened steel tooling, which is more durable and suitable for large-scale production.
If you’re considering outsourcing a plastic injection molding project, you might be curious about how to secure a reasonable price for the injection mold. In this article, we’ll break down the cost calculation for an injection mold. We’ll delve into the hourly rates associated with each manufacturing process, along with the key factors that influence the mold’s cost.
Where P20 – low end; 718H (medium); H13 (high end), these mold steels are the most commonly used.C45 is also sometimes used in low-end applications.
Tip: The hardness of through-hardened molds generally falls between HRC46 – 54. They are used exclusively for high-volume production or with high-temperature plastics such as PPS, PEEK, and PES.
For instance, the type of injection mold depicted in the right-hand image, used for manufacturing dispenser caps, typically costs between $12,000 and $18,000.
The majority of mold prices fall between $1,000 and $10,000. However, the cost of some large-scale molds, such as those used for automotive parts, can reach several hundred thousand dollars.
When calculating the raw material dimensions, some allowance needs to be added to the length, width, and height. Then we have the material weight of the Cavity Plate.
Machining is the most expensive part of the mold. The cost also depends on the type and grade of the machining equipment. The hourly rate of top brand equipment is 2-3 times higher than that of ordinary equipment.
In the above quotation methods, each cost is estimated separately. But in actual operation, mold factories often use simpler methods, that is to calculate material costs first and multiply by a price factor according to the mold size, complexity of the mold and so forth.
These are the results obtained from the simulation calculator. If you would like a more accurate and realistic manual quote, please contact us
Our online mold cost calculator will help you determine an appropriate price for your mold and explore ways to potentially reduce the mold investment.
This calculator will give 2-3 prices, each corresponding to a different complexity level, so that you can get a price range that provides a better reference. Each price provides a cost breakdown and their percentage.
This online injection mold cost calculator uses the part dimensions, the number of cavities, and the number of slides to calculate the mold dimensions and then estimate the mold price. It is not 100% accurate but can provide a close enough estimation.
Although the complexity of injection molds may differ, with some displaying elaborate designs and multiple moving parts, their fundamental structure remains unchanged.
Molds featuring a higher number of cavities often employ hot runners to ensure even pressure and flow distribution at each gate. Such molds demand greater dimensional uniformity across cavities, posing higher risks for the mold maker. These elements contribute to an increase in pricing.
Injection molding is a manufacturing process used to create a wide range of plastic parts and products. When planning an injection molding project, one of the first considerations is determining the production volume, as this helps narrow down which companies have the necessary resources to accommodate your project. Production volume can be classified into three categories: low-volume, mid-volume, and high-volume. This article highlights the differences between low-volume and high-volume injection molding, helping you make an informed decision for your manufacturing needs.
Tall ribs/posts are equivalent to deep grooves/holes within the mold, requiring the application of Electrical Discharge Machining (EDM). Additionally, this will present challenges during the injection molding process and elevate the manufacturing cost of the components.
As the ejector plates move upwards, they drive the ejector pins, which then eject the cooled plastic part from the mold.
It makes sense to know what are the most common percentage of each cost, so you will know if the quotes you receive are calculated properly, and if the prices are competitive:
Processing costs depend on the type of equipment used and the time it takes to complete the process. Accurately predicting processing time is difficult, whether through human estimation or using 3D simulation software. As a result, mold pricing often relies on estimates.
Low-volume injection molding generally involves the production of fewer than 10,000 pieces of a component, depending on the method used. This process typically uses tooling made from aluminum rather than the hardened steel used in high-volume production.
The top ejector plate has many holes for installing and positioning the ejector pins, whereas the bottom ejector plate lacks holes and serves to push the ejector pins.
The complexity levels are divided into five categories: very simple, simple, medium, complex, and very complex. A “simple” classification indicates minimal small details, lower precision requirements, fewer and smaller sliders, and lower ribs. On the other hand, a “complex” classification suggests the presence of more intricate details, higher precision, larger and more sliders, and taller ribs, essentially the reverse of the simple category.
As mentioned above, some costs, especially machining and assembly fees, cannot be precisely estimated when calculating quotations. Only the fuzzy quotation method can be used. The so-called fuzzy quotation is that it will be the quotation actually slightly upward than the actual cost, but there is also the possibility of downward fluctuation. And the upward and downward fluctuations between different costs may offset each other, to achieve the overall fluctuation is not very large.
Now, to help you better understand how the mold cost is calculated, let’s take a look at an example in the table below. Please note that we have given the hourly rate of different processes, so that you can understand how each cost is calculated.
Large mold manufacturers possess strong technical capabilities, yet they may not prioritize your project as highly. Although the risk is lowest with large manufacturers, collaboration with them might lack flexibility and adaptability.
When choosing a plastic injection molding provider for your project, it's crucial to verify that they have the resources to meet your volume requirements. For low-volume or high-volume manufacturing projects, UFtooling is your ideal partner. Our expertise and advanced capabilities ensure that we can handle your small to large-scale production needs efficiently and cost-effectively.
Since it is hard to estimate the machining time accurately, we can only make an approximation based on the size of the plastic part and the actual processing cost of similar parts in the past.
The cost calculation of the injection mold starts from the material cost. First, we will calculate the costs of the main steel plates.
In contrast, the hardness of pre-hardened tools typically ranges from HRC28 – 40. These are made from steel that has undergone a pre-hardening process, eliminating the need for heat treatment and allowing for direct machining to the final dimensions.
The ejecting mechanism consists of ejector pins and the top and bottom ejector plates, playing a crucial role in seamlessly releasing the formed parts from the mold.
Mass Production: High-volume injection molding is ideal for producing parts and products in quantities ranging from 750,000 to over 1,000,000, making it the preferred choice for large-scale manufacturing projects.
A mold consists of many parts, each requiring various machining processes, making its cost calculation complex. While determining the cost of materials can be relatively straightforward and precise, calculating processing costs is more challenging.
Upon closing, the Core Plate, Cavity Plate, and Slider form a sealed compartment where the plastic material is molded and solidified. Once the mold opens, these parts disengage, allowing the release of the solidified plastic item.
A successful plastic molding project starts from a good mold design, which requires a lot of skill and experience and often involves teamwork. Designers, mold makers, and others collaborate and combine their input to find the best option.
When the product size is L*W, and there are 2 cavities, then the distance between cavities R, and the distance from cavities to edges T1, T2 can be obtained from empirical formulas, so we can get the length and the width of the cavity plate Lca and Wca,
Likewise, we will do the same calculation for the other steel plates and sliding components to get their weight and costs, and add them together.
There are 3 options here: no slider, 1 side of sliders and 2 sides of sliders Note: If there are multiple sliders on the same side, they are considered 1 side of sliders.
An injection mold consists of several precision-engineered steel parts. These parts are meticulously shaped and honed to specific dimensions and tolerances, then assembled to form a complete mold. This assembly serves as the vessel for injecting, shaping, cooling, and solidifying of molten plastic to form the finished part.
Small mold manufacturers may devote more attention to each project, but their capabilities vary widely. Some may lack the necessary skills to achieve quality results, so discernment is crucial.
Before you make the final decision to place the order, it makes sense to ask 2 or 3 suppliers to submit you the cost break down for the mold, so you will know whether the costs have been calculated correctly, and which supplier appears to be more professional in the quote process.
Prototyping: Low-volume injection molding is perfect for creating prototypes used to test form, fit, and function due to its speed and cost efficiency. Market Testing and Pilot Production: This approach is ideal for producing small quantities for market testing or pilot runs, allowing businesses to gauge demand and refine their products before scaling up production. Low-Volume Production Runs: Suitable for projects that do not require the production of hundreds of thousands or millions of units, low-volume molding is perfect for specialized or niche products.
Sometimes, electrodes can be made small, but at other times, they must be as large as the entire part. The material costs and machining expenses of these electrodes contribute to an increase in the mold’s cost.
To provide a quotation for a mold, it’s necessary to first design the mold structure. Following that, you calculate the cost of materials, estimate machining and additional costs, and then finalize a quote for the mold.
♦ Product material: PP♦ Product dimension: 150*150*15mm♦ Mold material: 718H♦ Number of cavities: 1♦ Ejection method: ejection plate
Depending on the size and complexity of the mold, the design fee usually ranges from $100 to $300, sometimes could be even higher.
GETTING A QUOTE WITH LK-MOULD IS FREE AND SIMPLE.
FIND MORE OF OUR SERVICES:
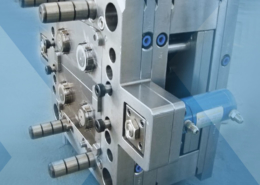
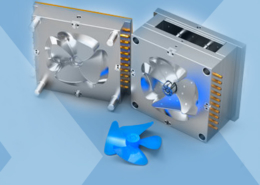
Plastic Molding

Rapid Prototyping
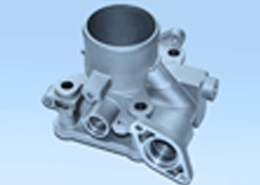
Pressure Die Casting
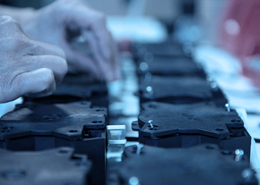
Parts Assembly
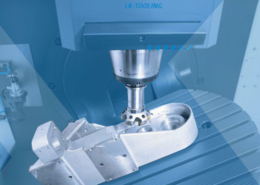