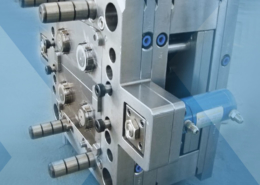
Injection Molding - polypropylene injection molding
Author:gly Date: 2024-10-15
Now that we’ve talked about how additives can really up the game in ABS molding, let’s tie it all together. ABS plastic is a real champ—it’s tough, flexible, and doesn’t break the bank. Even its kryptonite, UV light, can be handled with the right additives, opening up even more ways to use it.
Since it is a strong plastic, ABS is everywhere! Cars love it for parts like bumpers because it’s tough. Cool gadgets and electronics wear it as a durable outfit. Toys like LEGOs brag about it because it’s strong and safe. Even the medical world gives it a thumbs up for being easy to clean and tough. ABS in injection molding is like a celebrity, famous for being amazing and versatile!
To really nail ABS molding, team up with a pro injection mold maker. They’ll guide you through the ABCs of ABS, making sure you get awesome parts without spending a fortune. So, jump on the ABS bandwagon and watch your production soar!
Jumping from the nitty-gritty of the ABS injection molding process to the crucial role of temperature control, it’s crystal clear that precision is king. Next, we’ll jump into how keeping the heat in check is essential for pumping out primo ABS parts.
ABS is like a magical mix. It’s a thermoplastic polymer that brings together three awesome ingredients: acrylonitrile, butadiene, and styrene. Acrylonitrile is like the tough guy, adding chemical resistance. Butadiene is the muscle, giving it impact resistance. And styrene is the show-off, making things shiny with a high gloss. Together, they make ABS parts sturdy and stable.
But ABS isn’t just strong; it’s a powerhouse! It’s got muscle (tensile strength) and can take a hit (high impact resistance). Plus, it’s flexible and doesn’t get tired, whether it’s hot or cold. It’s like the ultimate athlete in the plastic world!
To make sure every ABS part is a carbon copy of the last one, you gotta pay attention to the nitty-gritty. Keeping an eye on the injection process and giving the machines and molds some TLC are keys to nailing this manufacturing process. It’s about keeping customers happy with parts that are just what they expected, every single time.
Cold weather? No problem! ABS doesn’t crack easily, even if it’s freezing. Think about cars – they need parts that are tough and work all the time. That’s where ABS molding steps in. It gives us safe and high-performing parts that don’t give up.
ABS isn’t just tough; it’s super flexible too! It’s easy to add color to it, and it stretches like a champ. From cars to toys, ABS is everywhere. Manufacturers love it because they can mold it into fancy shapes super fast with high injection molding speeds. That means making stuff quicker!
Not all ABS is created equal. Different grades of ABS require different molding temperatures. For instance, while working on a project for household appliances, I discovered that a specific grade of ABS needed a slightly higher temperature than the standard. It’s these nuances that make the process both challenging and rewarding.
In Electro Terminal's Plastics Molding Department, the housings for our electrical connection terminals, among other things, are injection molded from raw granulate.
Back in my earlier dayss, I remember standing in front of a massive injection molding machine, its mechanical arms moving in a dance of precision. The process begins by feeding the ABS pellets into a dry hopper. These raw materials get melted, and the molten ABS is then injected into a mold at high pressure, solidifying into the desired shape.
After chatting about the big role temperature plays in ABS molding, it’s cool to know there are extra bits (additives) that can really help this plastic material shine even more.
The whole ABS injection molding game also hinges on the mold and gate design. You’ve got to get the wall thickness on point for even cooling, so the ABS part stays stable in shape and size. The gate needs to be spot on too, making sure the ABS flows smoothly and quickly into the mold, without putting stress on the part. It’s all about crafting top-notch quality.
So, one tiny hiccup with ABS parts? They’re not best buddies with UV light. Too much sun can make them feel a bit off. But, guess what? There are some nifty additives to save the day! By adding stuff like acrylics or even slapping on coatings like glass, the surface of the product can totally block out those UV rays. This means your ABS parts, like outdoor toys or garden tools, can chill outside and still last a long time without getting all worn out by the sun.
On 31 injection molding machines, 45 different plastics are processed. Even cold sprue waste is reused. We ground it in-house and return it to the production cycle.
As we’ve explored the pros and cons of ABS, it’s clear that while it offers many advantages, it’s not without its challenges. Let’s summarize:
Want to make ABS even more awesome? Additives to the rescue again! By mixing in the right extras, you can make ABS stretchier and more bendy. And if you pair ABS with some metal coatings? Here! The strength and toughness of the injection mold product go way up. Like, imagine car parts made from ABS getting a metal boost. They can take hits and keep on going, making them super safe and long-lasting.
And here’s a cool fact: Even though ABS parts might not love too much sun (UV light makes them break down faster), it’s kind of a good thing for Mother Earth. They break down faster than other plastics, which means they’re easier to recycle. So, ABS is doing its part to keep our planet happy! For those intrigued by the versatile and recyclable nature of ABS and considering other materials for their injection molding projects, understanding how different materials impact the outcome is crucial. Dive deeper into the selection process with our comprehensive guide on choosing the right injection molding materials.
In my years of experience, I’ve seen how temperature can be both a friend and a foe. Too high, and you risk thermal degradation; too low, and the ABS might not flow properly. Achieving the right temperature ensures the ABS maintains its excellent dimensional stability and high gloss finish.
Another concern is the fatigue resistance of ABS parts. Under prolonged heavy loads, stress concentration can occur, leading to fatigue and eventual damage. As time goes on, ABS can wear out, especially if it’s subjected to repetitive stress. Moreover, the initial investment for ABS plastic molding can be high due to the complexity of certain designs. This might make small-scale production a tad expensive. For instance, producing a batch of 100 intricate ABS parts might cost 20% more than simpler designs.
One of the most notable challenges with ABS is its poor weathering resistance. Continuous exposure to UV light can lead to fading and a decrease in the material’s impact strength. For products meant for outdoor use or those frequently exposed to sunlight, this can be a significant drawback. Imagine a garden chair made of ABS. Over time, under the sun’s relentless rays, it might lose its vibrant color and even become brittle.
As we keep getting better at making stuff, ABS’s popularity is only going to skyrocket. It’s already a go-to for making all kinds of plastic products. If you’re in the biz of cranking out high-quality items, ABS injection molding is your golden ticket. It’s a speedy, wallet-friendly way to pump out loads of parts, making your production line hum. In this case, ACO mold has various plastic materials, including PVC, ABS, and so on. Contact us for your injection mold project!
Temperature, ah, the unsung hero of the ABS molding process. It’s a factor that’s often underestimated, but its influence is undeniable.
After diving deep into the world of ABS and all the tricks to make it even better, it’s easy to see how, with a bit of know-how, ABS molding can be top-notch. Stick around, and next, we’ll chat about the top tips for rocking ABS injection molding.
When I first touched the world of materials, there’s one plastic type that caught my intrigue – acrylonitrile butadiene styrene, or more commonly known, ABS plastic. Now, as someone with decades under his belt in the tech industry, ABS remains one of those fascinating materials that’s everywhere, yet often overlooked. The gentle hum of my vintage record player reminds me: even musical instruments have parts made from this versatile plastic.
This web site collects cookies and locally saved data to improve your user experience during the navigation. If you want to know more about cookies, please refer to the cookies policy. By continuing to browse this web site, you agree to the use of cookies and local storage of data.
Next up, let’s chat about a few things ABS might not be the best at. Stick around as we dive into the not-so-awesome sides of ABS injection molding, so you get the full picture of this fab material.
When you think about plastic injection molding, ABS injection molding is like a superhero. Why? It’s got awesome tensile strength and can take a beating! This cool mix of acrylonitrile, butadiene, and styrene combines the best stuff to make something super tough. Once you mold ABS parts, they stick around and can handle a lot. They’re great for jobs where things need to stay strong and keep working hard.
Before diving into making cool ABS parts, you gotta prep and dry the ABS material just right. This is super important to stop any pesky moisture from messing up the final product—nobody wants bubbles or streaks in their stuff. Usually, you’d dry ABS at around 80–85 °C for a few hours to make sure it’s got good resistance to these problems.
Every plastic has its own playbook for how to mold it, and ABS plays by its own rules. You have to get the injection pressure and speed just so, to match ABS’s flowy nature. For a perfect fill, you crank up the injection molding pressure, and to avoid wonky defects, you keep the injection speed in check. It’s all about making sure the final ABS part comes out looking sharp, without any twists or warps.
With a clear understanding of ABS’s strengths and weaknesses, let’s delve deeper into the ABS injection molding process, ensuring we harness its potential while being aware of its limitations.
GETTING A QUOTE WITH LK-MOULD IS FREE AND SIMPLE.
FIND MORE OF OUR SERVICES:
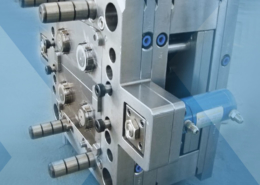
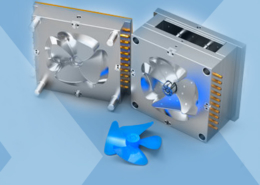
Plastic Molding

Rapid Prototyping
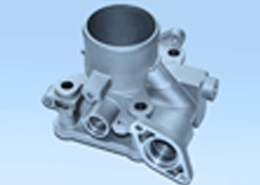
Pressure Die Casting
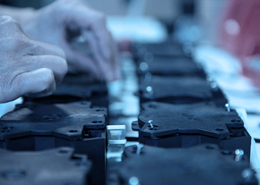
Parts Assembly
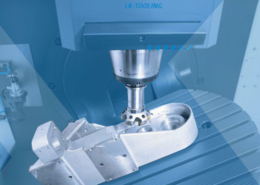