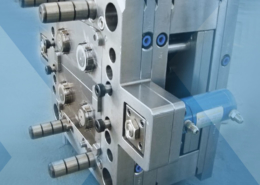
Injection Molding - injection molding product
Author:gly Date: 2024-10-15
Tomorrow I've got the day to myself, so I'm going to make a box and put a random plastic and foam object in there and see if I can make a mould of it. If it works, it might just be a really cheap good way to make my own injection parts. Even if the mould is good for say 10-20 uses it's still a really cheap way to make some high temp moulds.It might be a terrible idea, if so then I've got some gasket sealant for my 61' Alpine mk2 I'm restoring, if it does work then welcome to cheap high temp silicone moulds :)
Then yesterday in Canadian Tire I saw RTV gasket silicone, just happend to randomly walk down that isle and past silicone stating "High Temp" on it, it caught my eye. It's good to 600 deg, so well within the range of molten plastic in an injector and that tube just went right in the basket.
Above is alink to a piece I did on using sprue and silicone. I've been doing this sort of stuff for twenty plus years and if you don't mind a little clean up time it works great and is very cheap.
Also looking around and saw this stuff Mold Max 60, the site shows them pouring pewter into it, so I figured, heck if it can do pewter it should be good for plastic right?https://www.smooth-on.com/tutorials/casting-pewter-mold-max-60/
Hi all, I figured this might be a good place for this conversation.DIY Injection Moulding.Has anyone here done it? How did you do your moulds and what was the result like?
My impression is that injection molding takes a pretty expensive setup. In addition to the molding machine, the dies are usually metal, and a reverse of the part.
Alternately does anyone have any experience in having moulds and sprues made from a local or offshore place? Short run stuff?
If you can produce masters, then you can produce sillicon/RTV/Vulcanising rubber moulds and produce your parts in resin, plaster, etc.
The high capital costs of injection molding is why so many small firms go for resin casting. For the individual, or for a low capital startup, this seems to be the way to go. You use RTV to encase your pattern and create a mold. In addition to the standard urethane resins for casting the parts, the RTV molds will stand up to a limited number of casts of low temperature metals like those Micro Mark sells. Micro Mark also sells a kit to get started in urethane plastic- the kit includes RTV for molds, the urethane casting resin, and some mixing supplies. Such a kit is a good way to get started, and you can then buy the resins and rtv individually once you have caught on to the process.
Nowadays all the rapid prototyping is CNC cut/lathed, or LASER cut, or 3D printed, but knowledge of 3D design is needed, as is access to printers, but there are companies like Shapeways if you don't have the printers etc.
GETTING A QUOTE WITH LK-MOULD IS FREE AND SIMPLE.
FIND MORE OF OUR SERVICES:
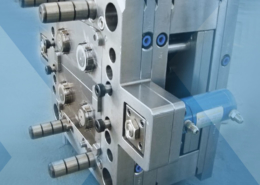
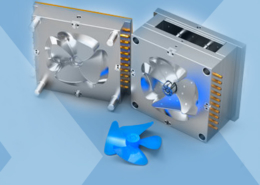
Plastic Molding

Rapid Prototyping
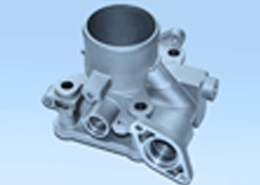
Pressure Die Casting
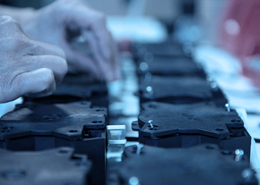
Parts Assembly
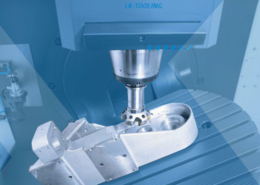