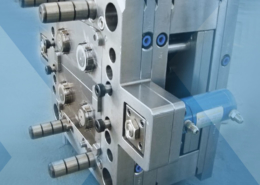
Injection Molding - industrial injection molding
Author:gly Date: 2024-10-15
Advantages: High strength, excellent heat resistance, chemical resistance, and dimensional stability. It offers good impact resistance and can withstand high temperatures.
It is important to consult with material suppliers and consider specific automotive industry standards and regulations while selecting materials for injection molding. Conducting mechanical testing and evaluating material performance in the intended application conditions are also recommended to ensure optimal material selection.
Advanced Materials: Utilizing high-performance thermoplastics, composites, and bio-based materials for stronger and more durable automotive components.
Material Availability: Injection molding supports a wide range of plastic materials, providing automotive manufacturers with abundant options to select materials that best meet their performance, safety, and cost requirements.
Advantages: High flexibility, abrasion resistance, and good impact resistance. It offers excellent cushioning properties and can be molded into various shapes.
Repeatability: Injection molding ensures consistent and repeatable production of automotive parts, maintaining dimensional accuracy and minimizing variations between each part.
Cost-effectiveness: Injection molding offers cost advantages for high-volume production, as it enables efficient and rapid manufacturing of automotive components, reducing overall production costs.
Smart and Connected Components: Incorporating sensors, electronics, and connectivity features directly into injection-molded parts for intelligent and interconnected systems.
Components Under the Hood: It is included engine covers, air intake systems, cooling system components, fuel system components, brackets, housings, and electrical connectors. These parts are exposed to high temperatures, engine fluids, vibrations, and mechanical stresses. So we should choose heat-resistant engineering plastics such as PA6/PA66, PPS, PEEK, and reinforced composites.
As a manufacturer offering injection molding services, Zhongde specializes in automotive injection molding. Our automotive injection molding services cater to the specific needs of the automotive sector, providing high-quality components that meet the industry’s stringent requirements. We utilize advanced injection molding technology and processes to manufacture parts such as interior trims, door panels, dashboard components, exterior body parts, lighting components, and more.
Injection molding can still be cost-effective for small-volume production of automotive parts if the tooling costs can be spread across multiple units and the benefits of injection molding, such as high efficiency and repeatability, outweigh alternative manufacturing methods.
Selecting materials for automotive injection molded parts depends on factors such as temperature resistance, chemical resistance, impact resistance, UV stability, aesthetics, mechanical properties, cost, specific application requirements and regulatory compliance. Manufacturers must consider these factors to ensure the parts can withstand the specific environmental conditions they will encounter while delivering the desired performance and longevity.
Color Options: Injection molding allows for the incorporation of a vast array of colors into automotive components. By utilizing colorants and masterbatches, manufacturers can achieve consistent and vibrant color options to match branding, styling, or functional requirements.
Yes, injection molding is capable of accommodating complex and intricate automotive part designs, thanks to advanced mold design and manufacturing techniques that enable the production of highly detailed and intricate features with precision and consistency.
Advantages: Offer high strength-to-weight ratios, stiffness, and thermal stability. Reinforcements such as glass fibers, carbon fibers, or natural fibers enhance the material properties.
Advantages: Transparent, excellent optical properties, good weather ability, and high surface gloss. It provides good impact resistance and can be easily molded.
Our team of skilled engineers and technicians works closely with automotive clients to develop and produce components that meet their exact specifications and quality standards. By choosing our automotive injection molding services, automotive manufacturers and suppliers can benefit from our expertise, quality assurance, and timely delivery. We are dedicated to supporting the automotive industry by providing innovative and reliable injection molding solutions for their specific application needs.
Interior Components: Included interior components included Instrument panels, consoles, steering wheels, seating components (seat frames, armrests, headrests), door trims, dashboard components, interior handles, air vents, storage compartments, and trim panels. These parts experience temperature fluctuations, sunlight exposure, mechanical loads, and passenger comfort requirements. So we should choose aesthetic and high-quality thermoplastics like ABS, PC/ABS blends, PP, TPO, TPU, and soft-touch materials for enhanced comfort and durability.
Automotive manufacturers choose injection molding because it offers lightweight components, design flexibility, cost efficiency, durability, and improved aesthetics. It allows for the production of complex designs, integrated functionalities, and high-volume production. Injection molding provides durability, resistance to harsh conditions, precise surface finishes, and rapid prototyping capabilities. It also supports environmental sustainability through the use of recycled materials and reduced waste. These factors make injection molding a preferred choice for automotive manufacturing.
Advantages: Good chemical resistance, flame retardancy, and electrical insulation properties. It is durable and provides good weather ability.
High Precision and Surface Finish: Injection molding delivers high precision in the production of automotive parts, ensuring tight tolerances and dimensional accuracy. It also enables the creation of smooth surface finishes, enhancing the visual appeal and aesthetics of the final products.
High Quality and Durability: Injection-molded automotive parts exhibit excellent quality and durability, meeting the demanding performance requirements of the automotive industry, including strength, impact resistance, and chemical resistance.
Digitization and Simulation: Employing digital tools like CAD, CAE, and simulation software for optimized design and faster development cycles.
Process Optimization and Automation: Implementing automation and robotics to enhance efficiency, precision, and consistency while reducing labor costs.
These advancements in automotive injection molding focus on creating lighter, stronger, smarter, and more sustainable components that meet industry standards and customer demands.
Different automotive parts has different environments. Then we should used different materials to meet the various working condition.
Advantages: Good impact resistance, toughness, and dimensional stability. It can be easily processed, has excellent surface finish, and is cost-effective.
Advantages: Lightweight, high chemical resistance, good impact strength, and flexibility. It is cost-effective and offers good processability.
Typical production timelines and lead times for injection molded automotive parts can vary depending on factors such as part complexity, quantities, tooling requirements, and supplier capabilities. However, they generally range from a few weeks to a few months.
Improved Surface Finishes: Enhancing aesthetics through advanced mold design, texturing techniques, and high-gloss finishes.
Exterior Components: It is included bumpers, grilles, body panels, fenders, door handles, mirror housings, lighting components (headlamps, taillights), wheel covers, and aerodynamic components. These parts face varying weather conditions, UV exposure, impacts, and aerodynamic forces. So we should choose weather-able thermoplastics like ABS, PC/ABS blends, PC, PMMA, and reinforced composites for strength and impact resistance.
Design Flexibility: Injection molding allows for intricate and complex part designs, enabling automotive manufacturers to create innovative components with integrated functionalities, optimizing space utilization, and achieving light-weighting goals.
Plastic injection molding started being used in the auto industry in the mid-20th century. It gained popularity as a lightweight alternative to metal components. Advancements in materials and technology allowed for the production of more complex automotive parts. Over time, injection molding became dominant, driven by light-weighting initiatives and stricter regulations. Today, it plays a crucial role in producing various automotive components.
Multi-Material and Overmolding: Combining different materials in a single injection molding process to create complex and integrated parts.
Have you ever noticed a whitening phenomenon in PVC product whitening? Some of your transparent PVC products, like shower curtains
Sustainable Manufacturing: Emphasizing eco-friendly practices by using recycled materials, reducing energy consumption, and managing waste efficiently.
The injection mold structure and design directly influence various aspects of the final product, including its dimensional accuracy, surface finish,
These three injection molding techniques offer distinct advantages and are chosen based on the specific requirements of automotive components, including material properties, performance characteristics, and desired end-use applications.
Injection molding flow marks are a common injection molding defect. While flow marks generally do not influence the structural integrity
Injection molding services find extensive application in the automobile industry for producing a wide range of components. These include interior parts like dashboards, door panels, and seating components, exterior parts like bumpers and body panels, as well as under-the-hood components. There is a comprehensive guide to automotive injection molding.
GETTING A QUOTE WITH LK-MOULD IS FREE AND SIMPLE.
FIND MORE OF OUR SERVICES:
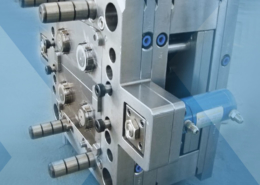
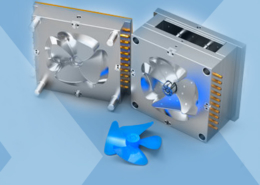
Plastic Molding

Rapid Prototyping
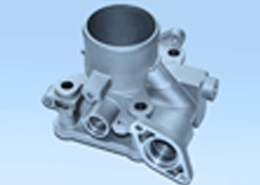
Pressure Die Casting
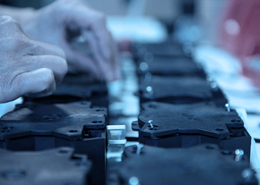
Parts Assembly
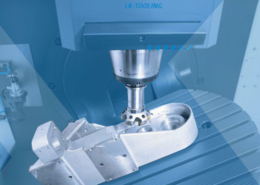