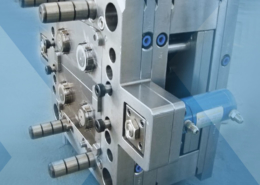
Injection Molded Parts for Medical & Pharmaceutical - medical molding
Author:gly Date: 2024-10-15
These three materials are used so often because they are affordable and durable. The material used to create a product should be determined by the product itself, and what it will be used for. To read more about different injection molding materials and their features, check out our materials blog here.
Materials with the lowest cost, generally polypropylene and polyethylene, are incredibly versatile and are used to make everything from milk jugs to car batteries. These are the materials most people use every day and low material costs help make mass production possible.
Hey I was looking for useful information on Plastic Surgery and just came across your blog and found it quite interesting, can’t wait to see your post. You’ve been sharing really insightful posts and I’m an avid reader of your posts. Keep sharing the knowledge and adding value to our lives.
In this article, we have not listed every factor, but these represent the main considerations for selecting the proper injection molding machine clamp tonnage. Texas Injection Molding is one of the largest custom injection molding companies in Texas and has made the strategic decision to position our company to offer a broad range of capabilities at a single location. Texas Injection Molding works closely with our customers during initial stages of product development to ensure part performance and efficient manufacturing. We are certified to the standards of ISO 9001-2015 and have a full-service tool and die shop to complete routine maintenance, engineering changes and repairs in a cost-effective and timely manner. In addition to our fleet of small to medium tonnage machines, we have several large tonnage machines and have planned our building, utilities, material handling and lifting capabilities to meet these broad manufacturing requirements.
These materials are generally stronger or have special properties that make them suitable for specialized functions. Additives and other components can make these plastics even more durable but do add to the price.
An injection mold generally costs between $1,000 and $80,000. A number of factors, including size and complexity, impact the final price. At Rex Plastic, the average price for an injection mold is $12,000. To read more about the cost of injection molding, check out our blog.
There are many different grades of plastic resin. Plastic resins are generally specified by the physical, environmental and chemical resistance properties required of the finished parts. Each grade of resin has an ideal processing temperature range without degrading the properties during manufacturing. Each different grade of resin will have different rate at which the plastic melt flows. The Melt Flow Index (MFI) is a measure of the ease of flow of the melt of a thermoplastic polymer. It is defined as the mass of polymer, in grams, flowing in ten minutes through a capillary of a specific diameter and length by a pressure applied via prescribed alternative gravimetric weights for alternative prescribed temperatures. Thermoplastic resin manufacturers can formulate the thermoplastic resin to have a range of MFI within a specific grade. The higher the MFI, the easier the melt flows. The higher the MFI the less injection pressure is required to fill the cavity and less clamp tonnage required by the molding machine.
Do you need design-for-manufacturing (DFM) assistance? Or, are you ready for production? We have a full suite of services to offer and a lifetime mold guarantee.
Injection pressure is a measure of pounds per square inch (PSI) required to inject the melted plastic resin to displace the air and fill the cavity under adequate pressure for form a quality part. The clamp on an injection molding machine “clamps” the two halves of the mold together during injection, packing and cooling process of manufacturing a plastic part. The greater the injection pressure pushing plastic melt into the cavities the greater the clamp force required to hold the mold together.
During the injection molding process hydraulic cylinders push the screw forward injecting melted plastic resin into the cavity of the mold at extremely high pressures. Pressures exceeding 20,000 p.s.i. during injection push the two halves of the mold apart. Injection molding machines are rated by “clamping force” in tonnage. The tonnage of force clamping the two halves of the mold together. The larger the surface area of the molded part, the greater the tonnage is required. Generally “large tonnage” machines are machines rated with 500 or more tons of clamping force.
If you spend $20,000 on a steel mold and then use that mold to create 400,000 parts, the cost per part would end up at 5 cents. There’s more to it than that, however, as the labor and material used will also have an impact on the total investment.
A large tonnage injection molding machine requires a large amount of resources. The footprint of a large tonnage machine is approximately 40’ x 8’ x 8’. The capital cost of a large machine can start at $250,000 and can exceed $1MM. The injection molds that are processed in these machines exceed 10,000# and require special lifting equipment. The facility foundations must be suitable for machines exceeding 100,000 lbs. The utilities required to operate a large machine are great and are expensive to bring to the building. Large tonnage machines typically run larger parts. Handling and storing large quantities of large parts requires considerable space for staging, packaging and storing parts. As a result of these considerations, there are fewer companies that choose to offer machines >500 tons.
When thinking about what material to use for your plastic injection project, it’s important to remember that the function of the product should determine the material used. Having an understanding of the options available and the prices associated with those materials will help you to make an informed decision.
As plastic melt is injected into the steel cavity of the mold, heat is transferred into the steel and the plastic begins to cool. If the resin cools (“freezes off”) before reaching end of fill for the cavity, you will have a “short shot”. Increasing the temperature of the mold will help the plastic material flow better and require less pressure and thereby less clamping force to hold the mold closed during fill.
I am looking to mold a cat sculpture for our local Humane Society. I have the model, formerly done in a 6 piece mold using fiberglass. I need about 50 cats, they stand 22″ floor to top of head, 30″ to top of tail, 6″ wide sideways and 16″ chest to rear. I also could use many more if the ideas goes to other HS.locations. The fiberglass ones were pure white, solid, but now I am thinking of technocats, clear plastic or solid white, hollow so that artists can utilize some tech including audio.
Thicker wall sections provide more volume for the plastic melt to flow. As plastic melt travels to the end of the mold cavity, the steel is removing heat. Thicker wall sections provide insulation for the melt and allow it to travel further with less pressure. Similarly, the thinner the wall the faster heat is transferred from the plastic melt and more pressure is required to push the melt flow into thin sections.
A general rule of thumb is 2-8 tons per square inch. For example, a 10” x 10” part (100 square inches x 2 tons/sq. in.) = 200 tons. The larger the part the more clamp force is required to hold the two halves of the mold together during the injection process. There are several factors that influence the amount of clamping force required including wall thickness, geometry, gating of part, viscosity of resin and temperature of injection mold.
The more tortuous the path and further the distance the plastic melt travels, the greater volume of melt is being pushed and greater transfer of heat from the melt flow to the steel cooling the plastic. The additional material and resistance to flow as travel distance increases requires additional injection pressure and clamp tonnage.
GETTING A QUOTE WITH LK-MOULD IS FREE AND SIMPLE.
FIND MORE OF OUR SERVICES:
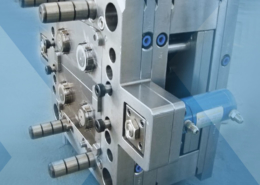
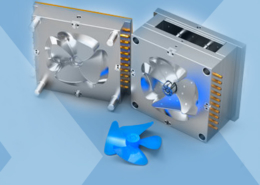
Plastic Molding

Rapid Prototyping
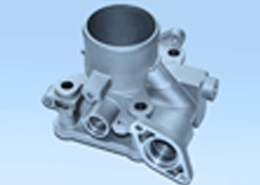
Pressure Die Casting
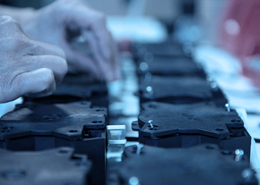
Parts Assembly
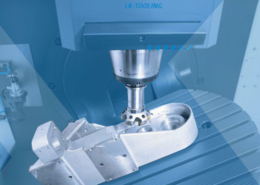