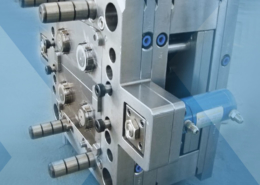
Injection Mold Slide Design for Complex Parts - BOYI - slide injection molding
Author:gly Date: 2024-10-15
Choosing the right molding process for your project is crucial for achieving the desired results. Both 2K molding and over-molding offer unique benefits, but they are suited to different applications.
The sequence of operations varies between the two methods. Overmolding starts with a base layer, or substrate, which is typically made from a material with a higher melting point, like PC/ABS or Nylon. The second material is then molded over this layer.
You will gain insights into choosing the right process for their production needs, overcoming technical challenges, and optimizing material selection for product excellence.
Overmolding revolutionizes manufacturing by merging materials for improved design and function, setting new standards in product quality and performance.
The choice between 2K molding and over-molding depends on your specific project needs. If you require high-volume production with complex designs, 2K molding is likely the better option.
2K injection molding represents a leap in manufacturing technology, enabling the creation of dual-material products with enhanced features, precision, and efficiency.
HQC saves you time, money and effort in bringing your best product to market. We achieve this by diversifying beyond our core manufacturing by listening to you. The supporting capabilities that we constantly improve give you greater choices in managing your chain of production. In this way, we become much more than a task-based resource – we are a full-service, problem-solving relationship that evolves with you as you grow.
This innovative approach redefines product design, blending functionality, beauty, and resilience in diverse industry applications.
On the other hand, 2K molding is designed to use exactly two materials, making it ideal for combining different textures or colors in one product.
Overmolding and 2K molding differ in the number of materials they use. Overmolding typically involves two or more materials, allowing for more complex designs.
Their expertise ensures high-quality, innovative solutions tailored to meet the unique needs of each product, solidifying their position as a leader in the injection molding industry.
These processes, along with the comparative analysis of 1K to 4K molding methods, underscore the importance of selecting the right approach based on product requirements, material compatibility, and production challenges.
In conclusion, over-molding and 2K injection molding are pivotal techniques in modern manufacturing, offering unparalleled design flexibility, improved product functionality, and enhanced aesthetic appeal.
HITOP is committed to assisting customers by offering a comprehensive one-stop solution, encompassing product design enhancement, initial sample creation, mold fabrication, injection molding, and product assembly.
This sophisticated process exemplifies innovation in manufacturing, delivering high-quality, complex products with streamlined efficiency and consistency, setting new industry standards.
Overmolding stands as a transformative manufacturing approach, offering both ergonomic and aesthetic enhancements to a variety of products.
For products that need functional enhancements or are produced in smaller quantities, over-molding offers the flexibility and precision you need.
The most complex, 4K molding integrates four distinct materials. This process is reserved for highly specialized applications demanding the utmost in precision and material variety, like intricate multi-functional devices.
When choosing between overmolding and 2K molding for your project, it’s essential to understand their key differences. These processes may seem similar but serve different purposes and involve distinct techniques.
These examples showcase overmolding’s versatility in improving product design, safety, and functionality across diverse applications.
Advancing from 1K to 4K injection molding enables unparalleled product customization, meeting diverse functional and aesthetic demands in modern manufacturing.
The simplicity of 1K molding makes it cost-effective and suitable for a wide array of products needing consistent material properties.
In contrast, 2K molding machines are designed to efficiently handle the two-material injection process in one cycle, making them ideal for high-volume production of dual-material products.
Different machinery is required for each process. Overmolding requires specialized equipment like vertical or rotary table machines to handle the multiple stages of molding.
By doing so, it crafts single-piece products with high user satisfaction. It is celebrated for its ability to enhance product design and functionality.
HiTop Injection Molding Services excels in these areas, providing expert guidance and execution in over-molding and multi-material injection molding projects.
It allows for the addition of multi-color designs and intricate patterns, elevating product aesthetics and practicality.
2K injection molding is a cutting-edge process that creates complex parts by using two distinct materials. This method enhances both the functionality and appearance of plastic components.
The over-molding process showcases precision and innovation, delivering products that surpass expectations in design and usability.
We are committed to helping you elevate quality standards, fostering enterprise growth, and actualizing your internationalization strategy.
Initial Material Preparation: Materials are loaded into two heaters, becoming viscous for molding. The first Material is injected into an open mold cavity while the second waits.
2K molding, however, is mainly used for aesthetic reasons, such as combining two colors or different textures in a single part, making it popular for consumer electronics, automotive parts, and handheld devices.
Expanding to three materials, 3K molding enables more complex product designs. This technique is used in applications requiring a combination of hard and soft plastics alongside additional functionality, such as waterproofing or impact resistance.
In contrast, 2K molding injects both materials in a single process, which speeds up production and is more efficient for simpler, dual-material products.
Over-molding stands out as a top choice in manufacturing for its efficiency and reliability. This process seamlessly merges multiple components into a unified item.
This is the foundational method, employing a single type of plastic. It’s efficient for mass-producing uniform components like containers and toy parts.
Hi, I am Sparrow Xiang, COO of the HiTop company, me and my team would be happy to meet you and learn all about your business, requirements and expectations.
Incorporating two different plastics, 2K molding allows for the production of parts with varied textures or colors in a single manufacturing cycle.
Ideal for creating products like power tool handles or automotive dashboard components, it enhances functionality and aesthetic appeal without the need for assembly.
Understanding these differences can help you choose the right molding process for your project, ensuring that your product meets both functional and aesthetic requirements.
The purpose behind using these methods also sets them apart. Overmolding is often chosen for adding functionality, such as creating ergonomic grips or adding soft-touch surfaces to handles.
These techniques offer versatile solutions to manufacturing challenges, scaling from simple to complex material integrations.
In the world of manufacturing, over-molding and 2K injection molding stand as innovative processes that enhance product design and functionality. Through these techniques, manufacturers can seamlessly integrate multiple materials into a single component, offering superior ergonomics, aesthetic appeal, and durability. This article delves into the processes, advantages, and applications of over-molding and 2K injection molding, along with a comparative analysis of 1K to 4K methods.
GETTING A QUOTE WITH LK-MOULD IS FREE AND SIMPLE.
FIND MORE OF OUR SERVICES:
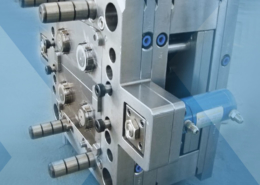
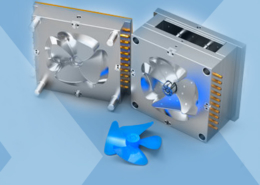
Plastic Molding

Rapid Prototyping
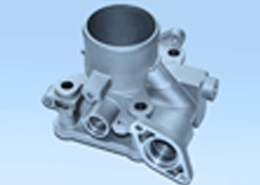
Pressure Die Casting
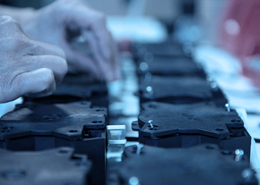
Parts Assembly
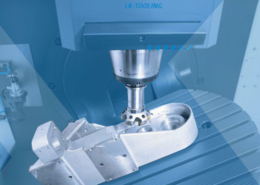