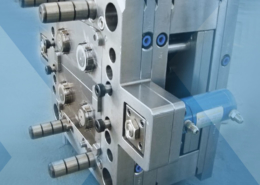
In-Mold Labeling (IML) - Prototool - in mold labeling injection molding
Author:gly Date: 2024-10-15
HDPE molding is also ideal for creating storage containers due to its durability and resistance to moisture. It can be molded into various shapes and sizes, making it versatile for different storage needs. It is commonly used to make storage boxes, bins, and containers for both indoor and outdoor use.
The mechanical properties of HDPE make it a highly versatile material that can be used in a wide range of applications, including packaging, pipes, automotive parts, and more.
HDPE material appearance is opaque white waxy, specific gravity of 0.941 ~ 0.960, soft and tough, but slightly harder than LDPE, also slightly elongated, non-toxic, odorless.
HDPE molding is used in a range of sporting goods due to its durability and ability to withstand impact. It is commonly used in the production of helmets, protective gear, and equipment such as kayaks, canoes, and paddleboards.
HDPE has a high melting point, which means that it can withstand high temperatures without deforming. HDPE also has a low thermal expansion coefficient, meaning it does not expand or contract significantly when exposed to temperature changes. Additionally, it has low thermal conductivity, which does not allow heat transfer.
For instance, trimming may involve removing any excess material or flash that may have formed around the part’s edges during the injection molding process.
They can be molded into a wide range of shapes and sizes using injection molding processes. Injection molding allows for complex shapes to be created with precise details, making HDPE ideal for parts that require specific dimensions or features. This makes HDPE a popular choice for manufacturers looking to create custom parts in large quantities.
HDPE can also be manufactured to meet specific standards and requirements, including FDA and medical-grade standards. These standards ensure that the material is safe for use in food, beverage, pharmaceutical, and medical applications and that it meets strict purity, biocompatibility, and other properties.
During solidification, the HDPE material is cooled rapidly to promote efficient solidification. The cooling rate is crucial and should be controlled to prevent warping, distortion, or cracking of the part.
This decrease in viscosity allows the material to flow more easily through the mold, filling in all of the mold’s cavities and contours.
High-density polyethylene (HDPE) is a thermoplastic material widely used in the injection molding process due to its excellent properties, such as high strength, durability, and chemical resistance. The injection molding process involves melting HDPE pellets, injecting them into a mold, and solidifying them to create a specific shape.
Besides, the excellemt UV resistance is another advantage of this material, that means it can withstand prolonged exposure to sunlight without degrading or losing its properties. This makes it an ideal material for outdoor applications, such as pipes, fencing, and playground equipment.
The melting process requires a controlled temperature to prevent material degradation. This process can be achieved by using a screw and barrel system, where the HDPE pellets are fed into the barrel and then melted by the screw.
Post-processing may be necessary to achieve the desired surface finish or functional properties of the part. The post-processing stage may involve operations like trimming, sanding, polishing, or coating the final part to improve its appearance and function.
They are a strong and durable material that is resistant to impact, chemicals, and environmental factors. This means that HDPE products have a longer lifespan and require less frequent replacement, reducing overall costs in the long run.
HDPE plastic is a widely used material that offers various benefits, including high strength, durability, chemical resistance, and versatility. Injection molding is a popular manufacturing process used for producing high-quality HDPE plastic parts with complex geometries.
In the production of hardware like hinges, handles, and knobs, etc., HDPE is also a great choice as it’s a durable and lightweight material that is resistant to impact and chemicals.
Injection molding is a popular manufacturing process used to produce various plastic parts, including those made from HDPE. Injection molding offers numerous advantages when it comes to producing HDPE parts, such as cost-effectiveness, high customization, and high malleability. High-quality mold should be used in injection molding to avoid molding splay.
ACIS®, Autodesk Inventor®, CATIA® V5,Creo™ Parametric, IGES, Parasolid®, Pro/ENGINEER®,Siemens PLM Software’s NX™, SolidEdge®, SolidWorks®, STEP
This blog will explore the properties of HDPE materials, the injection molding process of the plastic, its advantages, and its applications.
Also, HDPE is a great choice to meet specific design requirements since this material can be easily colored, painted, printed, or laser-engraved. This advantage gives manufacturers a wide range of options to customize the material. Desired finishes can be easily applied on the surface of the designed HDPE material to give the user the desired aesthetics.
This plastic is used in a variety of products and industries, including packaging (such as bottles and containers), construction (pipes, geomembranes), automotive (fuel tanks), agriculture (water pipes, irrigation systems), and consumer goods (toys, furniture).
HDPE is a relatively smooth material with a uniform texture, and it can be easily molded into various shapes and sizes. It has a slightly waxy feel and is not sticky to the touch. The surface of HDPE can be easily decorated or printed with logos, text, or other graphics.
Some factors come into play in deciding how cost effective a material is. These factors include the cost of production, durability, recyclability, and a lot more. Overall, HDPE is a relatively low-cost material. The manufacturing process for HDPE is straightforward and requires a lower cost.
Whether you are looking for a partner to design and produce custom HDPE injection molds, or you need finished POM products, FOW Mould has the expertise and resources to meet your needs. Contact us today to learn more about our services, or get a quote from us today!
HDPE can be easily machined using traditional machining techniques such as milling, drilling, and turning. Its versatility makes it popular for use in various applications where reshaping and modification are required. In addition, they can be easily customized to achieve any mold texture.
The post-processing stage is also the time for incorporating appropriate post-processing techniques and quality control checks. Manufacturers ensure that the final parts meet the desired specifications and standards, resulting in high-quality HDPE parts.
As one of the most commonly recycled plastics, HDPE can be recycled multiple times without losing its properties. This means that HDPE products can be recycled and turned into new products, reducing the need for virgin materials and minimizing waste.
As an ideal material for creating custom parts, HDPE resin molds are versatile and easy to modify. Its high strength-to-density ratio makes them suitable for designs that seem impossible.
Our experienced engineers and technicians work closely with clients to understand their unique requirements, providing tailored solutions that meet their specific needs. We use state-of-the-art technology and equipment to design and produce high-quality HDPE injection moulds that deliver consistent, reliable results.
HDPE hardware is also easy to clean and maintain, making it ideal for outdoor use. The material can also be molded into various shapes and sizes, allowing for customization to fit specific hardware needs.
High-Density Polyethylene has a distinctive appearance. It is typically translucent to opaque and has a white color, but it can also be manufactured in various colors by adding pigments or dyes. The surface of HDPE can be either glossy or matte, depending on the manufacturing process and the desired finish.
HDPE is highly resistant to a wide range of chemicals, including acids, bases, and solvents. It is commonly used in the chemical processing industry, where it is exposed to highly corrosive substances.
The pseudoplastic stage occurs during the injection stage, where the melted HDPE material is forced into the mold cavity through a nozzle. The material experiences high shear rates as it passes through the narrow nozzle, causing it to decrease in viscosity.
This material is strong and durable while remaining lightweight, in other words, it has a high strength-to-weight ratio. This makes it an ideal material for products that need to be both strong and lightweight, such as pipes, pressure vessels, and lightweight packaging materials.
Its lightweight and great strength sometimes makes it an alternative to aluminum. They are suitable when the product to be designed is expected to be light and strong enough for its intended purpose.
HDPE solidification is an essential step in the injection molding process, where the melted material transforms into a solid part. This stage is critical as it determines the final properties and dimensions of the part.
This makes HDPE an attractive option for manufacturers looking to reduce their production costs without compromising on quality.
Polyethylene injection molding is commonly used to make toys due to its durability and resistance to impact. It is a safe and non-toxic material that is ideal for children’s toys, including building blocks, action figures, and dolls.
At FOW Mould, we are committed to providing the highest quality products and services. We adhere to strict quality control measures to ensure that every product that leaves our facility meets the highest industry standards. Moreover, we offer competitive pricing, guaranteeing our clients the best value for their investment.
HDPE resin molds can also be easily molded into various shapes and sizes, making them a popular choice for products that require custom designs. It is resistant to cracking and has good impact strength, making it an ideal material for containers, crates, and pallets.
In addition to making consumer products for everyday use, HDPE’s properties make it ideal for manufacturing industrial components and so on.
When choosing the plastic material for producing pipe thread protectors, HDPE may be one of the best options. These protectors are used to protect the ends of pipes during storage and transportation so that they are supposed to be durable and resistant to impact, ensuring that pipes are not damaged during handling.
FOW Mould is a trusted manufacturer of HDPE injection moulds and offers comprehensive HDPE injection moulding services. Our expertise in mold designing, producing, and delivering molded polyethylene products makes us a reliable partner for all your injection moulding needs.
Polyethylene injection molding is widely used in the construction industry to produce a range of products, such as plastic sheets, pipes, and fittings. It is a cost-effective and durable material that is resistant to chemicals, moisture, and impact. HDPE is also easy to work with, allowing for customization to fit specific construction needs.
HDPE products can be used in industries including but not limited to: toy production industry, sports equipment production industry, etc.
HDPE has high tensile strength that allows it can withstand high levels of stress or force without breaking or deforming. The tensile strength of HDPE ranges from 20-37 MPa. Their high flexural modulus makes them resistant to bending and deformation. The flexural modulus of HDPE ranges from 800-1400 MPa.
HDPE moulding involves melting the material and injecting it into a mold cavity to create a specific shape or form. This process is used to manufacture a variety of products, such as plastic bottles, containers, pipes, and automotive parts. HDPE molding is a cost-effective and efficient way to produce high-quality products with complex designs.
As a raw material for injection molding, HDPE is an excellent choice. Not only does this plastic have all the advantages mentioned above, it also has many other plastic options in terms of price.
HDPE is easy to process, making it an ideal material for manufacturing. It can be molded into various shapes, such as bottles and containers, using blow molding or injection molding processes. HDPE can also be extruded into pipes or sheets. It has good weldability and can be easily joined using various welding techniques.
It’s also able to molded into various shapes and sizes, allowing for the customisation of sporting goods to fit specific needs.
The decrease in viscosity is helpful because it reduces the amount of pressure required to inject the material into the mold, which helps to extend the lifespan of the injection molding machine.
To meet FDA and medical-grade standards, HDPE must be manufactured using materials that are safe for food contact and medical use. The manufacturing process must also meet rigorous standards to ensure that the material does not contain any harmful contaminants that could affect the safety of food or medical products.
The physical, mechanical, electrical, thermal, and processing properties of HDPE make it a popular choice for industries such as packaging, construction, automotive, and consumer goods.
The thermal properties of HDPE make it suitable for a wide range of applications where temperature resistance is important. Its high melting point and low thermal conductivity make it an effective insulator and help to prevent heat transfer. Its low coefficient of thermal expansion and HDT make it relatively stable and resistant to deformation under high temperatures.
Careful consideration must be taken when selecting the right injection molding machine and tooling to minimize excessive shear.
HDPE exhibits high malleability when heated. When HDPE is heated above its melting point, it becomes a viscous liquid that can be easily molded, modified and shaped into different forms using various techniques such as injection molding, blow molding, or extrusion.
HDPE’s impact strength and high elastic modulus allow them to absorb shock and high-level impacts without cracking or breaking and maintain good dimensional stability.
In addition, the resistance HDPE poses to chemicals, acids, bases, and UV makes them suitable for use on construction sites where they will be exposed to some chemicals.
HDPE is a sustainable and eco-friendly material offering various environmental benefits. One of the most notable benefits of HDPE is its ability to be produced from plant-based renewable resources, which reduces the dependence on fossil fuels and contributes to a more sustainable future.
Additionally, HDPE has a high surface resistivity. The high resistivity of this plastic allows them to resist the flow of electric current across its surface. This property makes them suitable for use as an insulating material.
The containers that are made of HDPE are also stackable, making them space-efficient and convenient for storage and transportation.
High-density polyethylene (HDPE) is a popular thermoplastic material used in a wide range of industries due to its durability, strength, and versatility. One of the most common methods of manufacturing products using HDPE is through molding processes.
From reusable thin-walled beverage cups to 5-gsl cans, all are important applications of HDPE in the injection molding process, here’s an in-depth look at what’s so special about HDPE plastic!
In consumer product applications, this kind of plastic is used to make toys, storage containers, and sporting goods, while in industrial applications, it is used to create pipe thread protectors, construction products, and hardware.
In addition to producing molds, we also offer POM injection molding services that include the production of finished POM products. Our extensive range of injection molded parts, such as gears, bearings, and other precision components, is widely used across various industries.
One of the main advantages of HDPE is its ability to withstand high temperatures and harsh environments, making it a popular choice for outdoor applications. In addition to that, polyethylene is lightweight, making it easy to transport and handle. HDPE is a versatile thermoplastic polymer that offers a wide range of material properties that make it suitable for a variety of applications.
High-density polyethylene is a kind of thermoplastic material that is versatile. They can be molded, and remolded multiple times without a loss of physical or structural property.
High shear is an essential aspect of the injection molding process as it helps to break down the HDPE pellets and ensure consistent melting. However, too much shear can lead to material degradation and poor part quality.
During HDPE injection molding, the molten material is subjected to high shear forces as it flows through narrow channels, and the nozzle is forced into the mold cavity. These forces help to melt and mix the material, reducing any inconsistencies or impurities in the material.
One of the reasons for the high malleability of HDPE when heated is its high molecular weight and crystallinity. When heated above its melting point, the polymer chains become more flexible and can be easily rearranged to form new shapes. However, the high molecular weight gives it a high degree of stiffness and resistance to deformation at room temperature.
Mixing and melting of HDPE is a critical step in polyethylene molding. Mixing the HDPE pellets thoroughly is essential to ensure consistent properties throughout the material.
The benefits of HDPE moulding include high production efficiency, low cost, excellent dimensional accuracy, and the ability to produce parts in large quantities. These benefits make HDPE injection molding popular for various applications, including automotive parts, packaging, toys, and consumer goods.
Also, it ensures that the final part has consistent dimensions and properties throughout, improving its overall quality.
HDPE stands for high-density polyethylene, a thermoplastic polymer widely used in various applications due to its excellent strength, durability, and chemical resistance. It is made from petroleum and is commonly recycled.
In addition, HDPE is 100% recyclable, meaning that it can be reused and repurposed, reducing the need for virgin material and decreasing waste.
HDPE has good electrical properties, making it an ideal material for electrical applications. They have a low dielectric constant of around 2.3-2.5 and a high dielectric strength. The high dielectric strength of HDPE allows them to withstand high voltages without breaking down.
GETTING A QUOTE WITH LK-MOULD IS FREE AND SIMPLE.
FIND MORE OF OUR SERVICES:
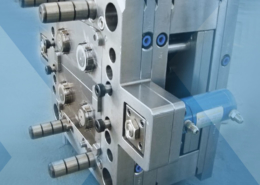
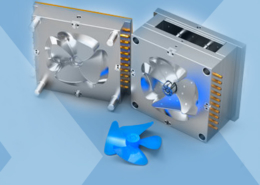
Plastic Molding

Rapid Prototyping
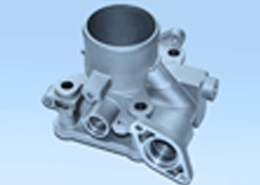
Pressure Die Casting
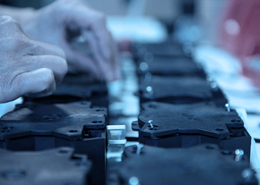
Parts Assembly
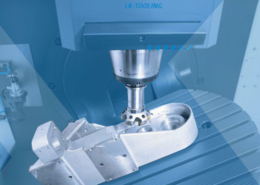