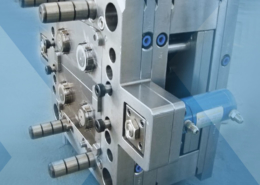
In-Mold Label - Heat transfer machine - in mold labeling injection molding
Author:gly Date: 2024-10-15
Known for incredible accuracy, acceleration and deceleration, our Sodick presses deliver best-in-class injection speeds, performance and repeatability. With up to 15.3- G’s of acceleration, our presses inject plastic 10-to-20 times faster than other conventional Injection Molding presses. What does this mean to you? It means we have the capability and ‘know-how’ to efficiently produce product that other injection molder’s continuously struggle with.
Micro Injection Molding makes you question every aspect of the manufacturing process—and that’s what we’ve done at Matrix. With well over a dozen degreed plastics and mechanical engineers on staff, we have a deep bandwidth of engineering talent who continuously drive innovation. Over 10% of our work staff are degreed engineers! We take a thorough and a systematic approach to Mold design and layout, runner and gate sizes, cavity spacing, total flow lengths, part ejection, inspection and post-molding part handling. That’s what it takes to mold parts that weigh .002 grams or have a gate diameter measuring .075 millimeters!
Two of the major keys to successful Micro Molding is having the right injection molding machines and proper ‘know-how’. Matrix has partnered with Sodick for all of our Micro Molding needs. We utilize Sodick Injection Molding Machines, customized at Matrix, that have a barrel ounce capacity of 0.15-to-0.91 ounces and a tonnage range of 20-to-60 tons.
That is because 3K and more material or colour injection processes entail more detailed studies on the bonding of materials, geometry parts, and many other considerations.
For a double-shot plastic injection moulding to work, the substrate and over-mould plastic material has to be chemically compatible in order for them to form a solid bond.
It is important to note that such method is ideal for surfaces with maximum friction, i.e. first shot hard plastics with a second shot soft rubber designed to enhance grip non-slip surfaces for industrial hand-held devices and infant products.
For any technical consultation or to get a quick quote, please contact us by filling up the form below. We’ll get back to you as soon as we can.
The definition of what is considered “Micro” varies—but it generally refers to part size or part feature sizes that are a fraction of traditional parts. Matrix Tool has built a reputation on building extremely high precision, complex injection molds. It was a natural transition for us to pursue Micro Tool Building and Molding capabilities once our customers’ product became increasingly smaller with tighter tolerances.
Unsurprisingly, the most common type of multi-shot moulding is the double-shot injection moulding, or what is commonly known as 2K injection moulding.
First, the substrate is injected into its respective mould cavity, while the second shot over mould is injected into its own cavity over the substrate from the first half of the injection moulding cycle.
This is an application for employment with Kore Industries. This application will be considered current for a period of sixty (60) days following the date of application. If, at the end of this period, you still wish to be considered for employment by Kore Industries. It will be necessary for you to complete another application. Kindly complete the attached Consent Form before the application is considered valid.
Since double-shot injection moulding is the most common multi-shot injection type, we will discuss this topic in further details below.
Next, the mould opens and the moving half or the core side of the mould is rotated 180 degrees and closed for the second half of the injection moulding cycle.
To be a Micro Injection Molder you have to be willing to step out of the conventional paradigm of modern injection molding technology. Imagine molding 11 parts from a single pellet of resin—then imagine trying to mold that part with a conventional injection molding press. It can’t be done effectively.
Alternatively, in cases where the substrate and over-mould plastic material are not chemically compatible, the substrate geometry has to incorporate mechanical bonding features such as through holes or other similar features.
If you are interested in obtaining additional information about Matrix Tool’s Injection Molding Services, please Contact us!
Multi-shot moulding is a process that moulds two or more more materials onto each other, in a single injection moulding cycle.
Overall, Matrix is a world class supplier with excellent technical support, technology and business processes. Matrix is a tremendous partner to have in our supply chain.
GETTING A QUOTE WITH LK-MOULD IS FREE AND SIMPLE.
FIND MORE OF OUR SERVICES:
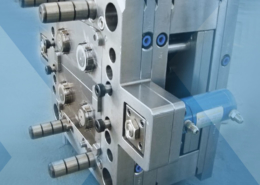
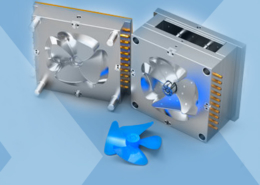
Plastic Molding

Rapid Prototyping
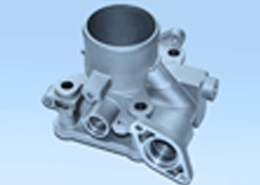
Pressure Die Casting
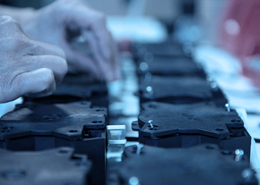
Parts Assembly
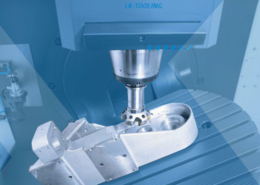