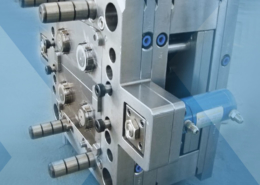
ICOMold® (Online Quotes in 30 Seconds) - plastic injection mold maker
Author:gly Date: 2024-10-15
In the medical field, we often see metal combined with the plastic part. This is called insert molding and is a very common practice for injection molders to do. You see this all over the medical arena from needles to EKG hook up leads and more.
The process is capable of making FDA approved medical devices that are both durable and reliable. This type of molding can also be used to make prototypes to send and get the much-needed FDA approval. Medical injection molding can be performed in a clean room and the components can be sterilized without harm as well. Let's take a look at injection molding.
When you contact us our experienced team will process your high impact polystyrene injection molding order quickly and economically without sacrificing quality.
Medical injection molding is a manufacturing process that produces plastic medical devices and components. It involves melting plastic resin pellets and injecting the molten material into a mold to create a specific shape. This process allows for precise control over the product's size and shape and is subject to strict quality and regulatory standards.
We service the Houston, Texas, Arkansas, Oklahoma, Louisiana, Gulf Coast regions, and all of North America including Canada and Mexico.
Once these new devices are produced, we assist our customers in transitioning the project into the production phase. Quality and customer satisfaction are our primary goals, and Aberdeen can work with both high and low quantity requirements with over 700 square feet of cleanroom injection molding space.
CTG, Inc. can assist you with engineering a new high impact polystyrene injection molding design and material selection.
In an economy that requires the balance of inventory and production, it's difficult to stay prepared when unforeseen issues result in equipment breaking down, power going out, or running over capacity. CTG, Inc. helps you avoid loss of production. We work around the clock to get your high impact polystyrene injection molding completed promptly while maintaining our high standards in quality and precision.
We provide assistance throughout each stage of your program, from design recommendation through mold tooling fabrication, prototyping, first article approval, process validation, full scale production medical molding, and transfer of turnkey system to customer facilities if requested.
No sample seal? No Problem! Our team can reverse engineer even the largest of OEM seals and provide you with a proper replacement design.
CTG is a one stop injection molding shop for manufacturing, sourcing, packaging and shipping parts on time, every time, even in an emergency.
From communication to delivery, our team works efficiently to provide the services you need through interaction and input from our clients. Every product we create is always made from top-quality materials on which you can depend.
Injection molding provides a low cost at moderate to large quantities. Almost any 2D or 3D shape can be achieved for making extremely versatile plastic parts with an excellent finish. Commonly used materials include PEEK, Nylon, Acetal, Polycarbonate, Polystyrene, Acrylic, PTFE, ABS, PVC.
Aberdeen’s primary goal is total customer satisfaction for even your most challenging projects. Our company culture is one of honor, respect and service with the highest degree of competence and professionalism that you will find anywhere.
In addition to high impact polystyrene injection molding we specialize in Oil & Gas Seals, Viton Seals, Kalrez Seals, Custom Seals, High Temperature Seals, Viton Molding, FFKM Molding, PEEK Molding, PTFE Molding, 3D-Printing and many other high-performance products and services detailed on our website.
Medical injection molding is a core technology of Aberdeen Technologies and represents a cutting edge solution to the manufacturing needs of healthcare companies who produce medical molded devices. As an insert molding manufacturer, we provide assistance to device manufacturers who approach us with new product concepts and ask us to mold parts for clinical trials and marketing evaluations.
Our products and services have been a top choice for chemical processing, oil and gas, semiconductor, pulp and paper, medical, industrial, research & development, OEM, and other industries.
The most common types of materials used in medical insert molding are thermoplastics. These are materials that can be heated up into a molten state and pushed through a barrel into a mold. These molds can simply be open and shut type designs, which are what you would expect for, say a simple product such as a cake mold. Or they can be very complex with moving side parts called slides. Of course, the simpler the mold the better for maintenance and longevity. However, complex parts will need these complex designs in order to produce the desired part.
Injection molding is a very common way to form plastic parts and components. Depending on the material, the parts can be very strict with their tolerances as well as easy to process. Injection molding is one of the most common types of forming plastics. It is used in a variety of industries and not just for medical injection molding. In fact, you probably have a wide variety of injection molded parts all around you and simply don't know it. Your basic pens, your keyboard, and even your phone have injection molded components in them.
Our high impact polystyrene injection molding emergency manufacturing and delivery is here to help when your equipment breaks down, power goes out, or you are running over capacity.
In addition to high impact polystyrene injection molding and reverse engineering we also provide emergency manufacturing and delivery, engineering, PTFE processing, Plastics Injection Molding, PEEK Processing, Rubber Molding and value-added manufacturing solutions.
Sometimes the components need to be manufactured separately and then assembled. This is very common in many cases and this can be done by hand or robot.
With over 100 years of engineering expertise we are dedicated to offering the highest quality high impact polystyrene injection molding and other products.
For your custom high impact polystyrene injection molding design, or reverse engineering, our exemplary service and efficient production ensures prompt deliveries coupled with outstanding service.
Prime examples were molding non-communicating passageways through a plastic manifold, molding critical tolerance pacemaker components, and even molding around glass formations without breaking or cracking. Our advanced injection molding equipment makes even the most difficult projects possible.
When designing custom high impact polystyrene injection molding, the staff at CTG, Inc. helps customers through the complete life cycle of customer input and design, prototyping (optional), tooling/mold production, and production. We may also make suggestions on seal modifications to design for assembly which will aid in installation, cleaning, and repairs.
However, there are other types of plastics called thermosets that also can be used for injection molding, but the process is far different. These materials are most likely not going to be used for medical molding as they cannot be recycled as easily as the thermoplastic materials. Because of this, you don't see thermosets used as often as you do thermoplastics. A good example of a thermoset is your car tires. This is where they cannot be melted down and reshaped into something.
In addition to high impact polystyrene injection molding our value-added manufacturing provides customers with a one stop solution shop.
GETTING A QUOTE WITH LK-MOULD IS FREE AND SIMPLE.
FIND MORE OF OUR SERVICES:
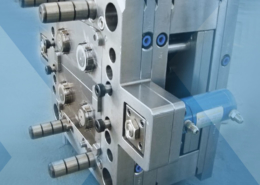
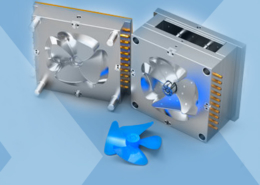
Plastic Molding

Rapid Prototyping
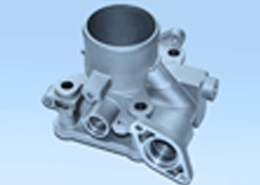
Pressure Die Casting
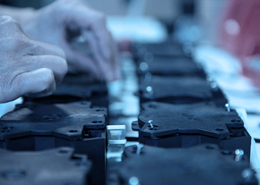
Parts Assembly
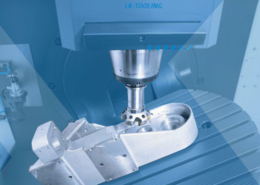