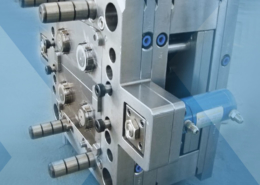
ICOMold® (Online Quotes in 30 Seconds) - low cost injection molding
Author:gly Date: 2024-10-15
PEEK can be machined or injection molded to the nth degree of precision. As mentioned above, PEEK has several grades which makes it ideal for a number of applications in the automotive industry. For e.g. CF30 PEEK’s mechanical properties make it ideal to manufacture car components such as seals, washers, and bearings.
PEEK resins are very popular in the medical industry. PEEK is insoluble in most solvents. They also do not undergo hydrolysis, even at high temperatures. This property along with PEEK’s relative inertness to chemical reactions makes it a perfect resin for biomedical and dental applications.
To better understand how VEM tooling can serve you for your PEEK injection molding project, contact us or request a quote today.
Natural PEEK is an unreinforced general-purpose grade that is wear-resistant. As compared to the other PEEK grades, it exhibits the greatest elongation and toughness.
PEEK’s chemical name is Poly(oxy-1, 4-phenyleneoxy-1, 4-phenylenecarbonyl-1, 4-phenylene). The following diagram illustrates the chemical structure of PEEK:
PEEK is a very popular thermoplastic however, it is also not always suitable for every application. There are various considerations that one must take into account before applying PEEK resins to an application:
PMMA: PMMA is sensitive to moisture, so it requires thorough drying before processing to prevent defects such as bubbles, voids, or surface imperfections. Typically, PMMA pellets are dried in a desiccant dryer to reduce moisture content to acceptable levels. ABS: ABS is less sensitive to moisture compared to PMMA, but proper drying is still recommended to ensure optimal mechanical properties and surface finish. ABS pellets are also typically dried in a desiccant dryer before processing.
PEEK is a versatile injection molding material because the natural grade along with the reinforced varieties offers various properties that can be applied to a wide array of manufacturing projects. There are 4 major categories of PEEK:
PEEK retains its mechanical properties at high temperatures which makes it an excellent electrical insulator. It thus can be applied to the manufacturing of electrical instruments that operate at high temperatures, such as soldering machines.
PMMA: Due to its higher melt viscosity compared to ABS, PMMA typically requires higher processing temperatures and slower injection speeds to achieve optimal flow and minimize defects such as melt fracture, warping, or sink marks. The injection molding machine settings, including barrel temperature, injection pressure, and cooling time, need to be carefully adjusted to process PMMA effectively. ABS: ABS has lower melt viscosity and better flow properties compared to PMMA, allowing for faster injection speeds and shorter cycle times. The injection molding machine settings for ABS may involve lower barrel temperatures and higher injection speeds to optimize flow and fill the mold cavity efficiently.
PMMA: PMMA injection molds may require specific design considerations to accommodate its high shrinkage rate and minimize residual stresses in the molded parts. Proper mold venting is essential to prevent trapped air and ensure the quality of the surface finish. Cooling channels in the mold may need to be designed strategically to control cooling rates and minimize warpage. ABS: ABS injection molds may have similar design considerations as PMMA molds but may not require as much attention to shrinkage and residual stresses. Cooling channels are designed to efficiently remove heat from the mold, ensuring consistent part quality and minimizing cycle times.
PEEK resins have extremely unique properties thus, 3D printing of PEEK allows the construction of almost any complex design geometry, which cannot be manufactured using other technologies.
The versatility and superior mechanical properties of PEEK resin make it an ideal choice for various industries such as medical, aerospace, mechanical, and automotive industries. In this article, we have conducted an in-depth analysis of PEEK injection molding material to help you understand whether it’s the best-suited material for your project.
In summary, while the basic principles of injection molding apply to both PMMA and ABS, the process parameters, mold design considerations, and handling techniques may vary to accommodate the specific properties and requirements of each material.
PEEK plastic exhibits excellent physical and mechanical properties. It is highly resistant to chemicals and thermal degradation. PEEK resins hold up well against high temperatures and long-term liquid submersion. In addition, they are also very durable in harsh environments.
Natural PEEK is ideal for instrument components where aesthetics is a concern. In addition, it is also well-suited for plastic parts where ductility and inertness are important factors.
PMMA: Due to its higher stiffness and brittleness compared to ABS, PMMA parts may require careful handling during ejection to avoid stress-induced defects such as cracking or crazing. Proper mold release agents or ejector pin placement may be necessary to facilitate easy part removal. ABS: ABS parts are generally more forgiving in terms of ejection and handling, but care should still be taken to prevent part damage or distortion during demolding. Smooth ejection and part separation help maintain the integrity of the molded parts.
PEEK, abbreviated for Polyether ether ketone, is one of the most versatile and popular injection molding resins. PEEK is a high-performance thermoplastic that has an increased tolerance to gamma radiation exposure. It also demonstrates resistance to sterilization processes such as autoclaving which is why it’s ideal for manufacturing medical devices.
The step-growth polymerization for the formation of PEEK polymers included reacting 4,4’-difluorobenzophenone or 1,4-bis(4-fluorobenzoyl) benzene with hydroquinone. This is done in the presence of alkali carbonates after which the PEEK polymer is isolated. The PEEK polymer is isolated by removing alkali metal fluoride and the polymerization solvent.
CF30 PEEK refers to a type of PEEK resin that has 30% of carbon fibers. The addition of carbon fibers greatly lowers its expansion rate and enhances the compressive strength and stiffness of PEEK. This grade provides greater thermal conductivity than natural PEEK thus, allowing for increased heat dissipation from surfaces.
Standardization and quality are part of our companies core values. We deliver the best possible experience and product to our customers, every single time consistent. Take a look at our certificates!
PEEK (polyether ether ketone) is a part of the broader family of ketone polymers known as PAEK, abbreviated for polyarylether ketones.
VEM Tooling has the expertise for your PEEK injection molding project. At VEM Tooling, we offer dependable service and ensure that you have a great experience with a seamless manufacturing process.
PVX Black PEEK is reinforced with graphite and PTFE lubricants. This type of PEEK offers the lowest coefficient of friction and the best machinability of all PEEK grades. It is an excellent combination of low friction, low wear, high LPV, low mating part wear, and easy machining thus, making it ideal for plastic parts that are exposed to extreme environmental conditions.
GF30 PEEK refers to a type of PEEK resin that has 30% of glass fibers. The addition of glass fiber greatly reduces the expansion rate and increases the flexural modulus of the resin. GF30 PEEK is great for structural applications that require strength, stiffness, or stability, especially at temperatures higher than 148ºC / 300ºF.
PEEK can be processed through injection molding, extrusion, printing and compression molding. You should note that the processing conditions greatly influence the resin crystallinity thereby, also changing its mechanical properties. Let’s understand some of the processing guidelines for PEEK resins:
The process of injection molding for PMMA (Polymethyl Methacrylate) and ABS (Acrylonitrile Butadiene Styrene) involves similar steps but may differ in certain aspects due to the unique properties of each material. Here's a comparison of the injection molding process for PMMA and ABS:
Unfilled PEEK is FDA-approved for food contact which is why it has a potential application in the food packaging industry.
PEEK resins meet safety and regulatory compliance and are thus an FDA-approved polymer. PEEK plastic can tolerate chemicals and exposure to extreme temperature ranges. Its often applied in the food packaging industry and in the production of oven parts.
PEEK plastic has distinct mechanical properties. It is thus a popular injection molding material It can be applied to a wide array of applications that include both, industrial and commercial industries. Let’s take a look at some of the sectors PEEK Plastic can be applied to:
PEEK polymers are manufactured through a chemical reaction known as step-growth polymerization. This is obtained through the dialkylation of bisphenol salts.
PEEK Plastic is a popular injection material but we must note that it has advantages as well as disadvantages. Let’s understand them in-depth:
GETTING A QUOTE WITH LK-MOULD IS FREE AND SIMPLE.
FIND MORE OF OUR SERVICES:
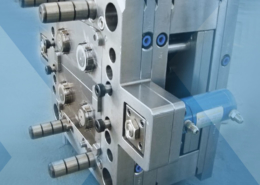
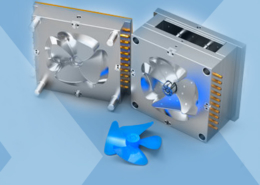
Plastic Molding

Rapid Prototyping
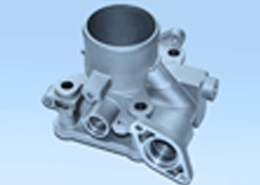
Pressure Die Casting
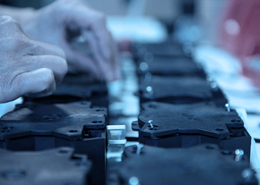
Parts Assembly
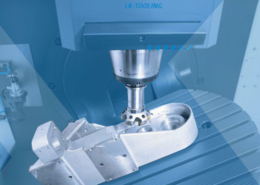