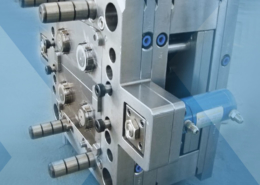
Hydraulic press in plastic molding - plastic press molding
Author:gly Date: 2024-10-15
Plastic injection molding is an advanced manufacturing process that involves creating parts in specially prepared molds. Injection molding machines enable precise manufacturing of parts for different purposes and with different parameters. Before starting the manufacturing process, Knauf experts focus on a careful preparation of the right mold to avoid production errors at a later stage. As a result, risks associated with potentially failed product prototypes can be reduced. A properly made molding insert makes it possible to obtain the right shape of each component.
We have worked with the leading manufacturers serving the healthcare industry for 25 years, including diagnostic laboratories and medical device companies. Our know-how in prototyping and medical device molding – coupled with our ever-growing production capacities here in the US – allows us to prototype, injection mold, and 3D-print parts of any complexity.
Ask your question in a 1 on 1 enquiry and we will give you a detailed answer, whatever the country/region you need our support.
With Xcentric, you can use plastic, tool steel, and other materials for your molds and start with prototypes to get the approval of the FDA. Then, once you are ready for high-volume production, we can upgrade your molds for continuous performance to create multiple pieces with as little mold degradation as possible.
The plastic injection molding process carried out by Knauf Industries enables the creation of high-quality products with specific shapes, sizes and parameters. Plastic components for the automotive industry are an important part of the offer – the automotive sector uses injection molded parts mainly due to their properties. The components manufactured this way include plastic bumpers, dashboard parts, fenders and many other parts. Knauf solutions are used by numerous automotive manufacturers around the world.
As a combined company, Quickparts and Xcentric offer an in-house, end-to-end solution from first prototype to short-run production, offering more to capabilities and benefits to customers both domestically and worldwide.
When Xcentric does the plastic injection molding of medical parts for you, we always create second-to-none pieces with the needed functionality. In addition, our technical engineering team is here to render assistance during all phases of your project and provide design recommendations if necessary.
Becoming part of Quickparts expands the capabilities and expertise Xcentric offers, delivering injection molding, CNC machining, and other critical services to customers across the globe.
From rapid prototyping to product creation at scale, Xcentric, together with Quickparts, brings speed and scale to your prototype, parts, and production projects.
Knauf Industries manufactures numerous components for the automotive industry using thermoplastic injection molding. The company's experts have extensive knowledge of this process, strengthened also through their work in other industries. This translates into creating high-quality solutions for the automotive sector as well. Knauf Industries offers a full range of services related to the process of plastic injection molding. You should also remember that the plastic injection molding machine is not the only tool used during manufacturing – the technological process begins well before the plastic goes into the mold.
The merging of Quickparts and Xcentric helps support customers’ continued growth and proficiency through improved U.S.-based, in-house, and quick-turnaround production. From 3D printing to injection molding, we do it all.
Injection molding is one of them – find out what the new plastic injection technology is all about and take advantage of cutting edge solutions for the automotive industry.
It can take as little as five days to create your prototypes so that you can handle potential compliance issues early on and bring your product to market faster. Both prototyping and medical device injection molding are carried out at our ISO-certified locations in Michigan.
Medical equipment has a lot to do with the quality of healthcare provided. That is why prototyping is a crucial part of the manufacturing process for validating design decisions and making modifications. If you want your components to perform at their best, look no further than Xcentric, a US-based medical plastic injection molding company.
Given that injection molding and additive manufacturing allows for consistent production, you are sure to avoid the risks of ill-fitting or improperly created implants and other parts with our services.
Once the right molds for the products are acquired, the actual part of the multi-step plastic injection molding process is carried out. First, the plastic is melted in special barrels; then the plastic is compressed and injected into the previously prepared molds. This way, precisely manufactured components can be created very quickly. This is why rapid injection molding has become so popular in many industries, including the automotive sector.
Plastic injection molding is performed with the highest manufacturing quality levels and in accordance with current standards. Modern technology combined with vast experience and expert knowledge allows us to produce the best injection molded plastic parts available on the market. Contact us for manufacturing of plastic elements – we will tailor our offer to your needs.
We offer extensive expertise in serving the medical industry through injection molding parts and prototypes, ensuring we meet your needs for every project.
Plastic injection molding and preparation for these processes is a key part of Knauf's services, but the company's support also covers other stages of production. Additional operations such as the assembly of sound-absorbing parts, clips and clasps are also carried out. Knauf also offers decoration of plastic parts in cooperation with an external company - an industrial paint shop - that provides paintwork for aesthetic details.
Injection molded plastics which are used to prepare modern components for the automotive industry are thermoplastic materials. Due to this property, it is possible to melt them and inject them into suitable molds. One of the materials used in this technology is liquid silicone rubber, which is characterized by high moldability. In the automotive sector, foamed polypropylene (EPP) and polystyrene (EPS) are widely used – their advantages include a high degree of flexibility and durability combined with low weight.
No matter how impeccable your pieces look on paper, they do not always translate into flawless parts. By leveraging the skills of the Xcentric team, you can achieve manufacturing perfection and streamline production while saving money and time.
Choose from over 40 stock materials for your medical components, or supply materials on your own to ensure the required mechanical properties!
As an innovator of on-demand digital manufacturing, Xcentric offers rapid injection molding, CNC machining, and additive manufacturing services from their Michigan facilities in the USA.
Excellent manufacturability is a must whether you are into the production of medical testing equipment, storage containers, or surgical tools. Otherwise, you may face warranty claims, litigation, and even the worst-case scenarios involving life-threatening concerns due to poorly made parts.
Injection molding services are gaining popularity in the automotive industry primarily because of the quality of the final components. Plastic injection molding enables the delivery of parts that are fully compliant with customer specifications. Knauf experts support original equipment manufacturers, through the entire production process of custom injection molded parts. Custom molding is much faster and more efficient when injection molding technology is applied – which is why it is especially worth considering.
Engineering plastics are deemed to be the materials of choice for prototypes and full-scale production for medical device components. They require less effort when it comes to the finishing stage and is contamination-resistant to ensure the end product’s safe uses.At Xcentric, we are happy to use engineering plastics and other commercially available materials or those supplied by you for your medical device components. When used as part of additive manufacturing or medical plastic molding, these materials are go-to options for implant positioning systems, drug delivery equipment, and housings for:
GETTING A QUOTE WITH LK-MOULD IS FREE AND SIMPLE.
FIND MORE OF OUR SERVICES:
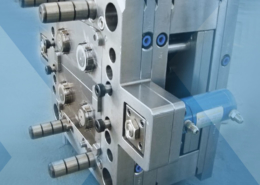
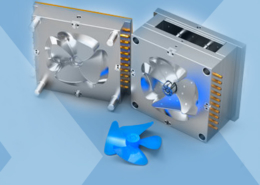
Plastic Molding

Rapid Prototyping
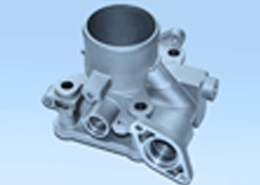
Pressure Die Casting
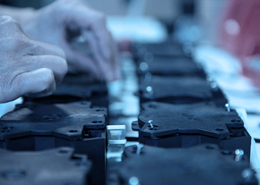
Parts Assembly
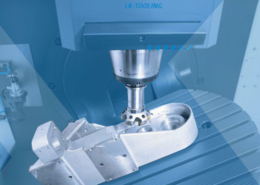