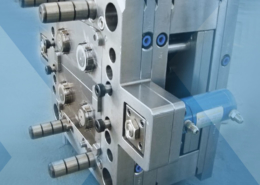
Hrrp Infotech Private Limited , Uttar Pradesh - injection molding company in gre
Author:gly Date: 2024-10-15
Our primary services include plastic product design, prototyping for industrial interests, tooling manufacture and plastic injection moulding in Melbourne. If you would like to discuss your next project with our team, give us a call.
Moreover, we rely on various scientific methods, moulding process technologies, and analytical tools to provide custom plastic injection moulding. It allows us to meet the performance and precision needs for complex plastic components and applications. We have experience in specialised, complex design, engineering and support and can perfectly align with your specific project needs.
A highly skilled workforce and stringent quality standards ensure we consistently meet or exceed our customer’s expectations. Experienced molders include mold designers, toolmakers, plastics engineers, and fabricators. Some of them once served as lead engineer or project manager at a prestigious molding company like Accurate, with enough capability to meet all your tooling and molding needs.
Raw plastic material melting. Injection of the molten material into a mould. Cooling of the molten material into a solid state. Removal of the hardened material from the mould.
As one of the leading plastic injection moulding manufacturers, we can help you with a quality injection moulding process.
Coming up with a design idea – A design idea doesn’t involve sketching up your vision but also other factors like your material preference, the environment in which you will use the product and the factors that can affect its performance, tolerance requirements etc. You can get a consultation regarding all these factors.
Learn more about our plastic injection moulding capabilities in Preston, Melbourne. We continuously invest in the most advanced processing technologies and optimise our techniques in manufacturing to ensure that we remain agile and competitive in the marketplace.
Injection molds are manufactured in separate parts that require assembly to form a complete mold. After production, we polish each part and evaluate it to ensure it is the right size and quality. The mold is then carefully assembled and tested for functionality.
RYD Tooling is well-versed in injection mold design and making for a variety of industrial applications. We utilize the latest techniques and machining equipment for efficient and precision mold manufacturing. Thorough analysis such as DFM, Mold Flow Analysis facilitates and expedites the production process, and enables the realization of your project.
Generally, making an injection mould can cost between $10,000 to $100,000. But the cost varies depending on several factors. As plastic injection moulders, we consider many things before estimating the final price, including your order size, part complexity, labour cost, and specifications.
As a leading plastic injection moulding in Australia, we have expertise in all aspects of the processes involved in plastic product manufacturing. We are known for producing superior quality tooling designs and products. In addition, we adhere to strict process and quality control systems to ensure quality service and products. Therefore, you can rely on us for design consultation, production, and distribution.
RYD Tooling has been in the mold making industry since 2006. During this period, our company has successfully worked on hundreds of injection mold projects for clients in various industries. We have gained vast experience in mold design and injection mold making through these project partnerships. They have also enriched our understanding of the injection mold requirements of different types of products. You can count on us to provide you with the right injection mold solutions.
Custom plastic injection moulding is the process that helps create a unique mould. It involves listening to your particular requirements and selecting material based on your specification, and production of plastic parts or products to meet your specific needs.
The injection moulding process involves using an injection moulding machine, raw plastic material, and a mould. First, the raw plastic material is melted in the injection moulding machine. It is then injected into the mould. Here it is allowed to cool down and get solidified into the final part.
We consistently achieve exceptional customer satisfaction through our seamless service and innovative ways to manage processes, products, and requirements. In addition, our business insight and keen eyes for detail allow us to understand market dynamics and customers’ expectations.
It appears we’re not the only ones excited about securing our latest contract for Australia Post’s new letter trays, with the Herald Sun publishing the…
RYD Tooling injection molds are made of steel. The type of steel that is used depends on the resin that will be used during the plastic injection molding process.
Large moldsare specially designed to form large plastic components like those used in the aeronautical and automotive industries.
Our team of innovative designers develops injection mold designs based on the plastic part our client wishes to produce. We use high-precision CAD software to ensure every structural detail is captured in our mold designs.
Moreover, as one of the leading plastic injection moulding manufacturers, we can develop game-changing prepositions for your business to support you throughout your journey. So, whether you want plastic product design, prototyping samples, injection moulding, mould design, mould manufacture, or plastic optimisation, we are your one-stop destination.
A bi injection molded structure is filled with resin using a plunger instead of the injection sprue that is used in ordinary injection molding.
It offers more advantages than metallic products because of its lighter, stronger, superior, and long-lasting characteristics.
The team at Sneddon & Kingston provide plastic injection moulding in Melbourne for various industrial sectors throughout Australia. We provide manufacturing solutions for; water filtration, food packaging, industrial packaging, automotive, construction, medical and pharmaceutical niches and so much more.
Our factory is spread across 4,000sqm and divided into departments that specialize in different stages of the mold-making process. It is equipped with 11 high-precision CNC machines and 9 EDM machines. These machines are controlled using advanced computer systems and are, therefore, very accurate. We also recalibrate them regularly to prevent errors.
The use of such advanced technology enables us to work fast without compromising quality. As a result, we manufacture about 400 mold sets in a year.
In addition to mold design and mold making, we offer comprehensive part design, 3D prototyping, and injection molding services. Each project is headed by a lead project manager who consults and updates the clients throughout the project.
Once the mold design is approved, mold production begins. We use high-accuracy CNC and EDM machines and top-quality steel to manufacture precision molds. They have high tolerances and are reliable for long-term use. We also optimize them to be high-performing and cost-efficient.
Injection Moulding Breathes Life into Australia’s Specialist Food Market! Since the turn of the century, food packaging has undergone a quiet transformation. Partly driven by…
RYD Tooling design engineers analyze the accuracy and viability of each mold design using Mold Flow Analysis technology. They also evaluate its structure to determine whether it is optimized for the type of resin that will be used for injection molding.
Sneddon & Kingston are industry professionals when it comes to plastic injection moulding in Melbourne, Sydney and all of Australia. We have the technical proficiency, the industry experience as well as access to modern facilities with automated processes to mass produce quality plastic products for various industrial needs.
It has been a long year now; we have been helping our clients turn their design ideas into finished products. Hence, you can contact us to discuss.
The plastic injection moulding technique necessitates incredible accuracy with maximum flexibility. This method has benefited many industries as the technology is used to produce products of different types and sizes for various purposes. Its application can be found in multiple industries like automotive, infrastructure, medical, food packaging, aerospace, household appliances, building and construction, etc.
We obtain all our injection mold materials from vetted top-tier suppliers. We further require each supplier to provide certification documents to ascertain the authenticity of their materials. These stringent quality policies ensure that we deliver durable and reliable injection molds to our clients.
Moreover, customised plastic components provide an ideal alternative for industries seeking to mass-produce high-quality, cost-effective parts. It is because they employ the moulds to replicate an item thousands of times.
Therefore, you can rely on us for mass-producing plastic components. We use a reliable and economical process to produce high-quality components with great dimensional consistency.
Our molds are designed to be durable and high-functioning. However, we understand that it is normal for tooling to develop faults. For this reason, we offer after-sale services to ensure our customers get the best user experience.
Choosing an appropriate manufacturing process – There are three main ways to manufacture a plastic part: injection moulding, CNC machining and additive processing. You will have to choose the most appropriate process depending on your requirement and budget.
Using the latest in technological equipment (EDM, multi axis CNC, and plastic injection molding machines), we are able to produce an injection mold with high quality and tight tolerance from simple to sophisticated design. Molds and parts produced by us have brought satisfaction to many clients from different industries like automotive, household appliances, electronic, furniture, aerospace, and other industrial markets.
Injection moulding can be an expensive affair to set up, but it will prove to be a cheaper deal over the long run. In addition, it works best for large production volumes. You can speak to our consultant to discuss your requirements and the cost of injection moulding.
Sneddon & Kingston Plastics is a Melbourne based company specialising in custom injection moulding. For over 60 years we have been a highly regarded and steadfast company supplying to many industries around the world.
Our team specialise in all aspects of product manufacturing. As a family owned business, we are focused on manufacturing and supplying high quality plastic injection moulded products for local Australian markets, and have been doing so for over six decades.
Prototype Building – Building a prototype is the final step before the production procedure. It reveals possible problems in real-world applications. Thus, it allows you to hone your designs and determine the functionality and efficiency of the plastic part.
For more information about our manufacturing capabilities and services, get in touch with our team today. Fulfil your need for specialised moulding and product design with Sneddon & Kingston.
With us, you rest assured that we will never pursue your custom injection moulding projects at the cost of material selection, part design, mould design and process control. On the contrary, we take utmost care of these key stages of the product development process to accurately achieve the type of product design you want from us. It also allows us to make you achieve your business goals.
Molds are used to form plastic parts during injection molding. This is done by injecting molten plastic resin into closed molds at high pressure and leaving it to cool and adapt the shape of the mold.
RYD Tooling is an injection mold maker for numerous manufacturers of plastic injection molding parts across the world. Our clients operate in different sectors including the home appliance, electronic, and automotive industries among many others.
Today, plastic injection moulding has become one of the most widely used plastic forming processes. It is known for having a wide range of manufacturing applications. In addition, the injection moulding process has many advantages, like customisability, high efficiency, speed, and affordability, which makes it different from other moulding and casting methods.
Each product is covered under warranty for 5 years or its indicated life span. We provide replacement parts for repairs during the warranty period if the fault is not caused by negligent use. Our technicians respond to injection mold repair queries within 24 hours.
As specialist plastic injection moulders, we design, optimise, manufacture and supply plastic injection moulded products. We meet the injection moulding requirements of high-quality engineered plastics. Our plastic injected moulded products provide an ideal replacement for heavier metal items.
GETTING A QUOTE WITH LK-MOULD IS FREE AND SIMPLE.
FIND MORE OF OUR SERVICES:
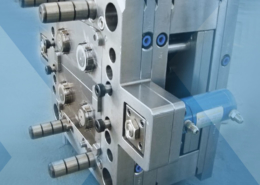
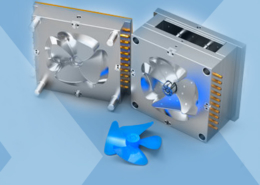
Plastic Molding

Rapid Prototyping
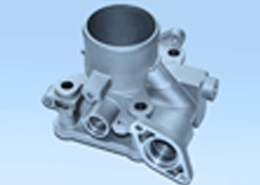
Pressure Die Casting
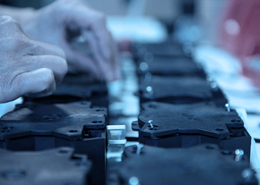
Parts Assembly
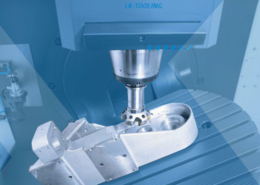