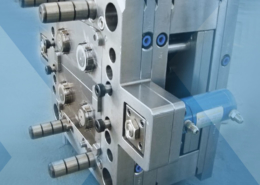
How to mold parts with undercuts and through-holes - complex injection molding
Author:gly Date: 2024-10-15
The thermoplastic injection molding industry churns out literally thousands of products and supports hundreds of industries. As of the 1990s, nearly 20,000 different types of thermosetting and thermoplastic materials were used for injection molding. Industrialists commonly use dyes and other agents to alter the properties of the molten plastic resin, such as its color, hardness, and springiness. The molds used to shape the molten plastic generally must be precut in a separate process, using sophisticated tooling procedures to properly prepare them. A device called a sprue allows the molten resin to enter the mold and fill up the cavity. Molds also are typically designed to allow air bubbles to escape. Otherwise, during compression and heating, the air bubbles might deform the plastic and even create internal burning of the finished components.
The company offers a variety of products, ranging from polylactic acid (PLA), a bioplastic blended with 25 percent hemp, to traditional fossil-fuel-based plastics — including ABS, PE and PP — blended with 25 percent hemp. The company also offers an HDPE that’s made from sugarcane.
The company is concentrating its sales on sheet producers and injection molders, Kayll said. It isn’t targeting certain products, including blow molded water bottles, because of the heat required to produce the bottles, the fact that PET is cheap and because regular PET water bottles routinely are collected in post-consumer recycling streams.
Company executives said their goals are to reduce greenhouse gas emissions and a reliance on fossil fuels in plastics manufacturing and to find a more environmentally friendly and less expensive means of handling hemp waste.
“We all have an obligation, in my opinion, to do right by the planet,” Kayll said. “We’re making an awful lot of plastics right now, and it’s filling up our planet. We have to do something about it.”
Thermoplastic injection molding is a process used in manufacturing to create a variety of parts and components for industries ranging from aerospace to automotive to construction. Thermoplastics, such as phenolic and epoxy, are heated into a molten resin and then injected into a mold that’s usually made from aluminum, steel or a metal alloy. The molten plastic then gets compressed inside the mold and allowed to cool. Machines remove the plastic component or piece from the mold, and this hardened part can then be used to construct a larger product, such as a child’s toy or an automobile door.
While hemp-filled PLA eliminates the use of petroleum-based plastics, the company’s line of traditional resins compounded with hemp will reduce plastic use by 25 percent.
“A lot of these bioplastics or sustainable plastics are a lot more expensive than fossil-fuel-based plastics,” Kayll said. “A lot of fossil-fuel-based plastics are based on natural gas, and natural gas is dirt cheap … It’s difficult to compete from a cost perspective.”
While everyone is looking for a perfect solution — a biodegradable plastic that has the properties and cost of a petroleum-based plastic — that is not yet available, Kayll said. Instead, the company is offering processors a chance to take a step toward achieving their ultimate goals, he said.
“I look at this as a migration,” Kevin Tubbs, a company co-founder, said. “Customers who have been running raw resin for decades, they need a steppingstone to get off raw resin, and that’s what Hemp Plastic provides. Maybe the first one they try isn’t 100 percent vegetable, maybe it is 20 to 25 percent, but, eventually, once they get to running it, they will see that bioplastics are indeed comparable performance-wise and easy enough to run with very slight adjustments to their gear.”
Pre-hardened steel molds tend to be more expensive but may be longer lasting; thus, manufacturers often use these harder, higher-quality steel molds for high-volume thermoplastic injection molding jobs. For more boutique industrial work, manufacturers may use aluminum molds, which can be more cost effective for scaled-down operations. To tool molds for industrial plastic injection work, manufacturers typically employ one of two time-tested processes: electrical discharge or standard machining. With the electrical discharge process, a robot applies a voltage from a tool to alter the shape of the base metal. With standard machining, a more conventional process, a machine or tool physically warps the mold into its final shape.
Senior Staff Reporter Bruce Geiselman covers extrusion, blow molding, additive manufacturing, automation and end markets including automotive and packaging. He also writes features, including In Other Words and Problem Solved, for Plastics Machinery & Manufacturing, Plastics Recycling and The Journal of Blow Molding. He has extensive experience in daily and magazine journalism.
The company offers the variety to meet the needs of a wide range of processors, said Glen Kayll, CEO. Some companies want bioplastic that is commercially compostable, but others may operate in markets where commercial composting is not available or may not be able to afford the cost of a fully bio-based polymer.
In many cases, though, hemp-filled plastics’ benefits, especially a reduction of carbon dioxide emissions, outweigh its drawbacks, Kayll said. In addition, compounding hemp with traditional plastics as opposed to bioplastics helps reduce the cost.
Hemp Plastic Co. works with customers to custom compound resins that are compatible with their existing equipment and have the needed mechanical properties for their applications, Kayll said.
More than 25,000 acres of hemp was grown in the U.S. in 2017, with 9,700 acres of the crop in Colorado, according to the company. Hemp is used for producing rope and fabric and to meet the growing demand for CBD oil. However, companies engaged in growing and using hemp face the problem of how to dispose of waste. As an alternative to burning it or landfilling it, Hemp Plastic compounds it with plastic resin.
With almost 50 years of injection molding experience, our experts can find the perfect solution for your project. We look forward to the challenge of designing and producing your custom polyurethane foam product.
GETTING A QUOTE WITH LK-MOULD IS FREE AND SIMPLE.
FIND MORE OF OUR SERVICES:
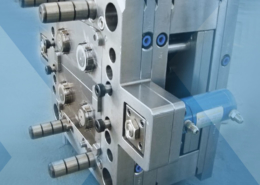
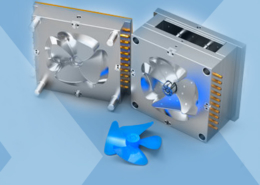
Plastic Molding

Rapid Prototyping
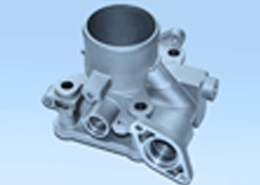
Pressure Die Casting
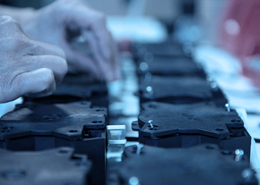
Parts Assembly
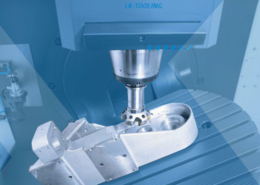