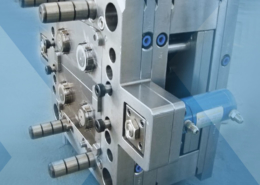
How to Mitigate Short Shots in Plastic Injection Molding? - short mold in inject
Author:gly Date: 2024-10-15
Mold manufacturer location: This was also mentioned while researching how mold size may affect your total injection molding expenses. To have your mold wherever it needs to go, an off-site plastic injection mold maker will charge you extra for shipping and handling.
The material properties of ABS make it a good choice when impact resistance, strength, and stiffness are required. A few key applications include:
If a plastic injection mold factory has the tools and materials, creating molds in-house may be the most cost-effective option if the technical expertise is also accessible. If the tools required for injection molding are not easily accessible, outsourcing lowers the cost of developing a mold.
Injection molding, the major cost driver is generally mold or tooling expenses. Molds for injection molding are typically created in one of three ways:
ABS is also widely used in prototyping because it is relatively inexpensive and has excellent dimensional stability for product testing.
3D printers can manufacture basic low volume 3D printed molds for as cheap as $100. A metal mold for a mid-volume service life of 1,000-5,000 units costs between $2,000 and $5,000. Mold costs can range from $5,000 to $100,000 for molds with more complicated shapes and prepared for higher production runs of 10,000+ pieces.
Creating more sophisticated molds necessitates technical knowledge. As a result, companies typically outsource specific aspects of injection molding, for instance, mold design and production.
The simple answer is that plastic injection molds range in price from $100 for a 3D printed injection mold to $100,000 plus for a sophisticated multi-cavity steel mold for greater manufacturing loads, which is typically the most important fixed start-up cost in injection molding. However, because these expenses are spread across hundreds or thousands of components, injection molding is a suitable method for mass-producing plastic parts at a low cost.
For injection molding, special-purpose equipment ranging from tiny personal molding machines that enterprises may use in-house to big industrial injection molding equipment primarily handled by providers, contractors, and major manufacturers is utilized.
Our injection moulding ABS materials are opaque thermoplastics available in black and natural colour options. The best material option will depend on your specific project needs. We offer various grades of ABS for injection moulding, including:
Acrylonitrile butadiene styrene (ABS) is a tough, impact-resistant plastic. Its low shrink, high dimensional stability, and good resistance to corrosive chemicals make it a versatile option used across a variety of industries. ABS has a glass transition temperature of approximately 105 °C and is an amorphous polymer, meaning it has high temperature resistance and no true melting point.
We offer several grades of ABS to meet the needs of applications in a variety of industries, including medical and automotive.
When it comes to injection molding prices, basic plastic injection molds might range from $3,000 to $6,000. A big, more sophisticated high-production, cross-cavity mold can cost between $25,000 and $50,000 or more. Although it may seem obvious, several factors contribute to the cost of injection molding.
Do you need a guide for selecting thermoplastic materials? Here you will find expert knowledge about thermoplastics and tips that will make it easier for you to choose a material for your moulded parts.
With small desktop injection molding equipment and 3D printed molds, creating modest volumes of components with injection molding is the most cost-effective. Small-scale automated injection molding machines are viable options for medium-series manufacturing of small components.Large industrial injection molding machines can range in price from $50,000 to more than $200,000. These machines also have more strict facility requirements and the need for specialized staff for operations, upkeep, and monitoring. As a result, although injection molding is a core competency, most businesses outsource mass manufacturing to service providers and contract manufacturers, with equipment expenses included in the service prices.
Typically, the cost of the mold, also referred to as the tooling cost, is the major cost driver in injection molding. Let’s take a look at some of the elements that influence the price of an injection mold.
Navigating supply chain issues is a constant challenge, especially in times of material shortages. To help, we created a detailed guide to resin substitutes for commonly moulded thermoplastics.
Material cost is determined by the design of a product, the material utilized, and the quantity of material needed to complete the injection molding process.
Depending on the needs of the finished products, a broad range of polymers can be utilized for injection molding. The cost involved when you buy plastic injection mold materials varies depending on the material selected. Thermoplastic pellets range in price from $1 to $5 per kilogram.
To a certain degree, asking for the costs of plastic injection molds cost is similar to questioning how much a car costs. Is your mold going to be a Pinto or a Porsche? Also, keep in mind that the cost of a mold is only the beginning. To calculate complete plastic injection molding costs for any projects, you must also include raw material, operating, and maintenance expenses in the future. These costs are a result of the aforementioned contributing factors.
GETTING A QUOTE WITH LK-MOULD IS FREE AND SIMPLE.
FIND MORE OF OUR SERVICES:
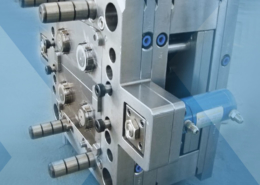
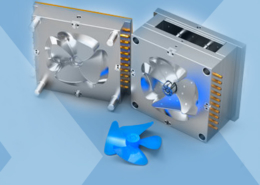
Plastic Molding

Rapid Prototyping
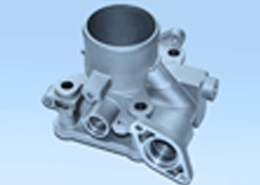
Pressure Die Casting
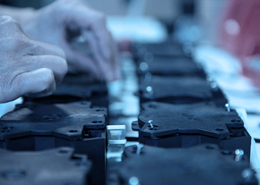
Parts Assembly
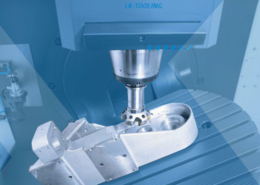