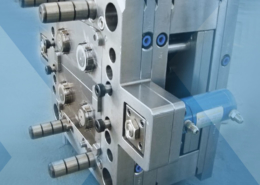
How To Make Plastic Toys Mold - Immould - molding plastic at home
Author:gly Date: 2024-10-15
Integrating the scientific approach with the traditional plastic injection molding process, we get a scientific molding process. This method optimizes the entire injection molding procedure. The scientific molding procedure hands over the reins of the product specifications to the process control engineer. It thereby enables him/her to control appropriate parameters to get an end product of desired specifications.
Creating molds for overmolding requires higher precision and a thorough understanding of the overmolding materials. The following are essential aspects to consider in overmolding mold design:
On the contrary, in a feed-forward process, the controller gets in action and eliminates the disturbance before it can disturb the process variable and disrupt the process.
Short Shot: Even a slight inadequacy in the injection can cause aesthetic defects, leading to product rejection. It’s crucial to design the gate location thoughtfully to prevent short shots. A Design for Manufacturability (DFM) assessment can be used to evaluate the suitability of gate placement, focusing mainly on the required injection pressure.
Generic scientific principals are what form the basis of scientific moldings. These principals include forecasting an issue (asking a question), developing a hypothesis for resolving the issue (answering the problem). Experimenting and then readjusting the idea (or theory) based on the results of the experiment.
From this distinction, it’s evident that insert molding usually requires just one injection mold, whereas overmolding necessitates at least two, and occasionally three, molds.
For material selection, an analysis of available data on the performance of previously used materials will help determine what materials to choose to produce parts of specified physical and mechanical properties.
To mitigate adhesion issues, it’s common to design holes or grooves at the edges of the overmolded area. These features, being larger internally, help to lock the overmold in place and reduce the reliance on adhesive strength, making it easier for the overmold to bond with the substrate.
DongGuan Company Room 103,#41 Lian Ma Road,Dalingshan Town,Dongguan City,Guangdong Province,China ShenZhen Company Building 5,Juhui Mold Industrial Park,Tianliao Com,Yutang St,Guangming District,ShenZhen City, China
While theoretically, overmolding can be repeated multiple times, such practices are rare in real-world applications and are not the focus of this discussion.
Insert molding typically involves inserting pre-fabricated parts, often made of metals like copper or stainless steel, into an injection mold. These parts can also be made from other materials such as glass, wood, or fiber.
This makes 2-shot molding more efficient and labor-saving. Additionally, since the substrate remains hot during overmolding in 2-shot processes, it often results in a stronger bond between the substrate and overmolding material.
ACE injection Moulding Company is an ISO 9001: 2015 certified mould manufacturer, providing services to the global plastic injection moulding industry.
In traditional overmolding, the substrate is first injection molded, removed from the mold, and then manually placed into another mold for overmolding.
Previously, when there was a defect in an injection-molded part, there were several machine parameters that the engineers had to sift through to find that one parameter that was affecting the quality of the product.
Researchers could trace back most of the defects of the part to these fundamental parameters in researches that studied the defects and their causes. Therefore, suggesting that by controlling the four basic parameters, molders and engineers can successfully eliminate most of the flaws in injection molding products.
In conventional injection molding, plastic injection molding companies first manufacture the parts and then check whether it fits the customers' specifications or not. The traditional process is a trial and error method and calls for multiple iterations to get the product specifications right.
This advanced process enables plastic injection molding companies to produce more products with fewer, almost negligible, rejections. Thus, the scientific approach of injection molding is saving the molders a lot of time and money.
We assure you we are not a broken record that keeps repeating 'scientific molding has many benefits over traditional molding.' But it does, and we feel compelled to elaborate it as well as we can.
Precision Fit Between Substrate and Mold: The fit between the substrate and the mold cavity in overmolding needs to be very precise. The gap between the substrate and the mold cavity after inserting the substrate should be between 0.01 to 0.03mm. This precision is crucial because materials like TPE, known for their fluidity, can easily cause flash if the gap is too large.
Traditional plastic injection molding employs the age-old method of molding molten plastic into the desired shape and size. It has four primary stages: the melting stage, filling and packing, cooling phase, and the ejection stage.
Overmolding is a process where a substrate, typically a pre-formed plastic part, is placed inside a mold. During the process, molten plastic is injected into the mold cavity, enveloping the substrate in the empty areas. Once cooled, the two materials fuse into a single product.
Commonly, the substrate in overmolding is a hard plastic like PA or PC. The overmolded material, however, can be a flexible plastic such as TPE or TPU, or even another hard material.
Although insert molding and 2-shot molding fall under overmolding, they are often referred to separately. In a narrower definition, overmolding specifically involves a plastic substrate manually placed into the mold.
During the mold designing stage, the scientific approach utilizes designing software and plastic flow simulators to design a mold capable of producing a product that matches the customer's specifications.
In summary, while overmolding technology offers enhanced functionality and aesthetics, it also brings challenges in cost, design, and material selection.
This approach, however, in use for the last twenty years, hasn't stayed stagnant. It has continued to evolve with the development of technology. Now plastic injection molding companies incorporate ultra-modern, futuristic technologies with scientific molding to further enhance the plastic injection molding process.
A scientific molding approach ensures consistency in the product specification by aiding in developing a process that controls the process parameters and does not let them deviate much from the setpoint values.
We don't think it'd be wrong if we regard traditional injection molding as a feedback process. And scientific injection molding as a feed-forward process. Of course, it is just an analogy. Still, it makes it easier to understand what a scientific approach does for injection molding.
In the first stage, plastic injection molding companies mold and feed the granulated plastic into a barrel. The barrel houses a screw-type plunger. The second stage is filling. In this stage, the screw-type plunger injects molten plastic through the mold's sprue and gates into the cavity. Then a certain amount of pressure is applied to ensure that the molten plastic covers the entire cavity. This stage is called the packing stage.
Plastic injection molding companies such as Ace-Mold have long optimized their processes using the scientific approach of molding, called the scientific molding. Scientific molding is an organized way of producing plastic pieces utilizing an injection molding procedure that ensures the manufacturing of identical, high-quality products in every cycle.
The substrates in over-molding often include materials like PA, PC, ABS/PC, and ABS, while TPE, TPU, TPR, and TPO are common choices for the overmolding layer. This blend of soft and hard plastics represents the most typical form of overmolding.
Overmolding usually involves a single overlay, requiring two injection molds. The final product is a combination of two materials or two color variations of the same material.
There are two types of processes in process control: the feedback process and the feed-forward process. After a parameter has undergone fluctuation in the feedback process, sensors sense the deviation in parameters and send signals to the control, making adjustments and bringing the parameter back to the setpoint value.
Although it may appear to be so but scientific molding is not an entirely different process on its own. Scientific molding is a systematic approach to your conventional plastic injection molding process.
More and more plastic injection molding companies are optimizing their injection molding procedure using the scientific molding approach. The reason? Many advantages that a scientific molding approach has to offer over the conventional method in injection molding.
Gate Design in Overmolding: The design of the gates in overmolding molds is highly critical. They must ensure complete filling while maintaining sufficient adhesive force. The key is to ensure that all areas to be overmolded are not too far from the gates. This is to avoid insufficient injection pressure or too low temperatures in those areas, which could affect the quality of the over molding.
However, the scientific molding approach utilizes previous data. It analyzes all available results to determine the right operating parameters and generates a process that can make high-quality parts one after the other with consistency.
After this comes the third stage or the cooling stage, where the molten plastic cools and solidifies. Following the third stage is the ejection stage, the fourth and final stage of the plastic injection molding. In this stage, the mold opens up, and the ejector pins present on the core plate of the mold push the solidified plastic piece out. Then the mold closes back and prepares for the next cycle.
Overmolding is a widely used plastic molding process with many advantages but also some limitations. Here are the main pros and cons of overmolding:
In conclusion, overmolding is a versatile and widely used plastic molding technique that enhances product functionality and aesthetics. Despite its complexity, with proper material selection, precise mold design, and attention to key issues like adhesion, short shots, and flash, overmolding offers significant benefits.
While the traditional approach uses constant pressure for filling and packing stages, the scientific method utilizes sensors and transducers' services. It divides the filling and packing stage into two different stages and adjusts the cavity pressure according to molten plastic properties' variation. Hence, some people often refer to scientific molding as the 'decoupled molding.'
Overmolding, also called plastic overmolding, molding over molding, or injection overmolding, is a crucial injection molding technique widely used in everyday items like toothbrushes, power tool housings, and car light panels. This article will explain overmolding, highlighting its common challenges and essential precautions.
However, 2-shot molding requires highly precise molds and thus involves greater initial investment costs. Therefore, the choice between these methods depends on the production volume:
These parameters included barrel temperature, speed of the screw plunger, packing pressure, filling time, packing time, and many others. Therefore, finding that one specific parameter that affects a particular specification of the product and then adjusting that parameter's value accordingly to eliminate the defect was not only excruciating but costly as well.
DongGuan Company Room 103,#41 Lian Ma Road,Dalingshan Town,Dongguan City,Guangdong Province,China ShenZhen Company Building 5,Juhui Mold Industrial Park,Tianliao Com,Yutang St,Guangming District,ShenZhen City, China
However, the scientific approach calls for adjusting and optimizing only four significant parameters. These parameters are the molten plastic's temperature, the pressure inside the mold's cavity, the velocity at which the machine is injecting the plastic in the mold (or fill time), and the cooling rate or mold temperature.
Conversely, a gap that is too small or negative, such as -0.01 to -0.02mm, can create indentations on the substrate surface. Therefore, the mold must be manufactured with high accuracy.
Flash: Excessive gaps between the mold cavity and the substrate can lead to flash (excess plastic). Moreover, if the gate design is improper, leading to excessive injection pressure (to avoid short shots), it can also result in flash.
Theoretically, the possibilities extend beyond these mentioned materials. Essentially, any plastic can be used for over-molding. For specific requirements, please feel free to contact us for more information.
Additionally, in scenarios where the maximum thickness of an injection-molded product is exceeded, a two-shot injection molding process may be used. This approach ensures each individual molding stays within the maximum allowable thickness.
Furthermore, because the controllers very tightly control the process variables in a scientifically optimized process, the quality of the plastic injection molding companies get after integrating the scientific approach with the conventional method is always top-notch. Production of high-quality products with great consistency also leads to fewer product rejections, ultimately saving the companies lots of raw material costs.
There are instances of double overmolding as well, which necessitates three molds, resulting in a product composed of three materials or color variations.
It’s crucial that the overmolding material has a melting point equal to or lower than the substrate’s. Using the same material for both is possible, but it requires careful adjustment of the injection molding temperature to prevent the substrate from partially melting.
Plastic injection molding companies are saving time and money by employing the scientific molding technique. Original equipment manufacturers (OEMs) are integrating scientific molding with their existing plastic injection molding processes. They are thus successfully producing better and more competitive products. Along with reducing the number of rejects, they are saving a lot of time and investment.
2-shot molding combines both substrate molding and overmolding in a single injection molding machine. Here, after the substrate is molded, it’s rotated to another station within the same machine for overmolding, eliminating the need to manually transfer the substrate.
Understanding the nuances between overmolding, insert molding, and 2-shot molding is crucial for selecting the right process for specific applications, balancing efficiency, cost, and production volume.
Scientific molding not only optimizes the designing of the production process. It also optimizes the process of material selection and mold manufacturing.
For almost two decades now, many plastic injection molding companies have been using the scientific approach to produce plastic parts. They manufacture these parts in high volumes for various industries. These industries include automotive, pharmaceuticals, and others. And by doing so, they have been reaping the scientific molding process's benefits and generating significant revenues.
Poor Adhesion: This issue often arises due to incompatibility between materials. For different materials, compatible overmolding materials must be selected. Additionally, a low temperature of the substrate’s surface can lead to poor adhesion. On the other hand, excessively strong adhesion can create recycling challenges for the product.
It’s also possible to use hard plastics for both the substrate and the overmold, usually the same material, often employed in multi-color combinations for aesthetic appeal.
GETTING A QUOTE WITH LK-MOULD IS FREE AND SIMPLE.
FIND MORE OF OUR SERVICES:
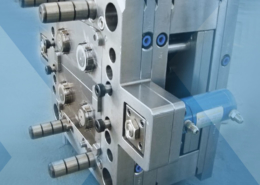
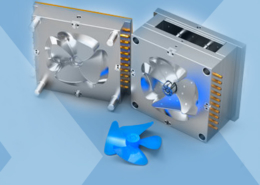
Plastic Molding

Rapid Prototyping
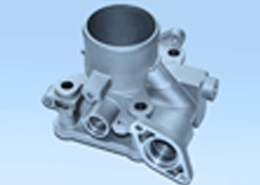
Pressure Die Casting
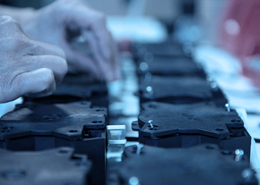
Parts Assembly
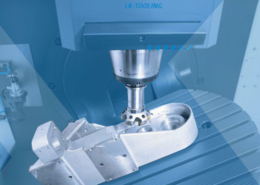