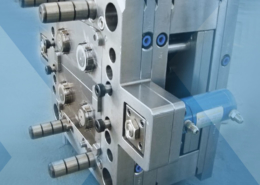
How to Estimate Injection Molding Cost? - plastic injection mold fabrication
Author:gly Date: 2024-10-15
Calendering is the process of shaping plastic. It involves a series of hard pressure rollers to finish or smooth a plastic sheet. It is used mainly for producing films, thin sheets, and flooring.
By signing up, you agree to our Terms of Use and Privacy Policy. We may use the info you submit to contact you and use data from third parties to personalize your experience.
As discussed above, the primary shaping processes are critical in plastic manufacturing. There are quite some methods to be distinguished. Some of the more important ones are listed below:
Furthermore, both AMPCO® 18 and AMPCO®21 are superior metals used for friction applications in molds, which can solve most wear and seizing issues. Our precise, high-conductivity, high-performance AMPCOLOY® alloy range is the ideal supplement to AMPCO® specialty bronzes. These high-conductivity copper alloys are produced with greater care than commercial alloys, with virgin metals and stringent controls to guarantee uniformity and unvarying quality. For these reasons, AMPCOLOY® alloys are extensively used in molds as inserts for the injection, extrusion, and blow molding of plastic parts for various industries – especially the automotive industry, as well as the greater plastics industry.
By signing up, you agree to our Terms of Use and Privacy Policy. We may use the info you submit to contact you and use data from third parties to personalize your experience.
Medical injection molding can be used for prototyping or low-volume production, but it’s often used in high-volume manufacturing for medical devices. In part, that’s because products can be injection molded at-scale with consistent quality and with minimal human intervention. Here are some common examples of injection-molded medical products:
Designers also need to select plastics that meet medical industry standards. This article examines the standards that affect the production of injection-molded medical products. By selecting materials that meet these standards, designers do more than meet requirements from independent bodies and regulatory agencies — ultimately, they promote quality, performance, and safety.
Our trained employees ensure your parts will be delivered on time and to spec.
We exist to eliminate bottlenecks in new product development by integrating the people, processes, and platform you need to source custom parts.
Aluminum bronze offers moderate hardness and outstanding conductivity. Thanks to their excellent heat transfer properties, aluminum bronze can drastically speed up the cooling phase, leading to reduced cycle times, increased productivity, and ultimately reduced manufacturing costs.
In blow molding, a thermoplastic preform is inflated in a mold. The compressed air causes it to adhere to the inside of the mold and hold it in place as it cools. This process is mainly used to manufacture bottles, drums, car tanks, and the like.
Reducing cycle times is hereby just one reason for the saving potential of aluminum bronzes. The other half includes a reduced rejection rate. In addition, warpage can be greatly reduced thanks to the superior thermal conductivity of copper-based alloys. This is due to improved cooling as molds made of aluminum bronze distribute heat more evenly than steel molds.
Even though aluminum bronze is already a good solution, the premium solution for injection molding is beryllium bronze. These alloys combine good strength, wear resistance, high-temperature resistance, and high toughness with excellent conductivity. That is why beryllium bronze is widely used in plastic injection molding, inner mold inserts, cores, die-casting punches, and many more.
Create high quality custom mechanicals with precision and accuracy.
Rotational molding is a special production process used to manufacture large, hollow, seamless plastic parts. During production, molten plastic granules are deposited on the inner surfaces of the rotating mold as it cools. Due to the nature of the rotating mold, different wall thicknesses can be achieved even within a single mold.
By signing up, you agree to our Terms of Use and Privacy Policy. We may use the info you submit to contact you and use data from third parties to personalize your experience.
Patented alloy with properties equivalent to berillium copper with lesser cost and without the health hazards of berillium-copper
In extrusion, the plastic is fed via a hopper into a barrel in which a screw runs. This is the extruder. The screw has different sections with different pitches. These are used for melting, homogenizing, degassing, and compressing. Extruders are used in a wide variety of ways. They are used to produce granules, recycle plastic, and manufacture profiles, sheets, textile fibers, and films. In film production, the extruders are equipped with a slot die and/or work with a calender. In the case of multilayer films, several extruders are often required simultaneously to manufacture a film product.
ISO 13485 outlines the requirements for a quality management system (QMS) when producing medical-grade products. It is the most common standard used in medical device manufacturing. ISO 13485 is not limited to plastic injection molding but rather covers the general requirements for all manufacturing technologies that are used to produce medical equipment. This standard was developed to ensure that consistent quality is maintained and that medical devices and equipment are produced in a safe and effective manner.
By signing up, you agree to our Terms of Use and Privacy Policy. We may use the info you submit to contact you and use data from third parties to personalize your experience.
ISO 10993 focuses primarily on the biocompatibility requirements for medical devices. It encompasses products that are designed to come into direct or indirect contact with the body. The goal of ISO 10993 is to reduce the risk of adverse effects on patients when exposed to materials that include, but are not limited to, injection molded plastics. ISO 10993 compliant materials are non-toxic, do not affect the immune system, or do not potentially cause cancer.
These are nominal values as these tables are used for comparative purposes. If specific figures are required, please go to the product page and download the technical data sheets for exact specs.
Medical devices are classified according to their potential for causing harm to patients, the general public, or to other personnel who use or operate the medical device. This classification determines the degree of required regulatory oversight.
By signing up, you agree to our Terms of Use and Privacy Policy. We may use the info you submit to contact you and use data from third parties to personalize your experience.
By signing up, you agree to our Terms of Use and Privacy Policy. We may use the info you submit to contact you and use data from third parties to personalize your experience.
For processing, the plastic in the form of granules or powder is usually heated and cast, sprayed, calendered, extruded, pressed, blown, or foamed. Accordingly, the primary shaping processes are of particular importance in plastic processing. In addition, if additives are added to plastics to achieve or improve specific properties, this is referred to as compounding.
The U.S. FDA (Food and Drug Administration), and the EU MDR (Medical Device Regulation) both divide medical devices into three classifications, where Class I refers to the lowest-risk medical devices and Class III refers to the highest-risk. The EU MDR further breaks down Class II devices into two subcategories: IIa and IIb.
Fictiv can produce injection-molded products for a wide range of medical applications. We have the resources, know-how, and manufacturing network to deliver the injection molded parts that you need, far faster than other manufacturers. And, we deliver 95.4% of orders on time and to spec, thanks to our network of highly-vetted partners, on-site quality engineers, and robust quality management system. Create an account and upload your medical device design today! Along with your quote, you’ll receive expert design for manufacturing (DFM) feedback and guidance to ensure you get great outcomes.
To achieve these goals, ISO 13485 outlines processes and procedures to manage risk and regulatory compliance while providing mechanisms to continuously improve the QMS whenever a gap or potential for improved performance is noted. The standard defines best practices for documentation, training, traceability, research and design, production, and how to handle non-conformances. For both the part designer and the injection molders, there are well-defined responsibilities.
By signing up, you agree to our Terms of Use and Privacy Policy. We may use the info you submit to contact you and use data from third parties to personalize your experience.
Plastic injection molding is used in many different applications within the medical industry. Examples include enclosures for medical equipment, the overmolding of surgical tools, and spinal implants. Designers have a choice of materials, but the selected plastic must meet the application’s requirements. For example, plastics that will be sterilized with steam need to resist high temperatures and moisture, while those that will come into contact with patients must be biocompatible, meaning that they’re not harmful to living tissue.
By signing up, you agree to our Terms of Use and Privacy Policy. We may use the info you submit to contact you and use data from third parties to personalize your experience.
Foaming can be divided into three categories. During the chemical foaming process, the gases that foam the material are released during polymerization. During the physical blowing process, low boiling liquids are added to the reaction mixture, which evaporates during polymerization to foam the typical gas bubbles. Finally, during the mechanical blowing process, a gas is injected into a melt of the plastic while stirring.
ISO 14644 regulates the use of cleanrooms during medical device manufacturing. It defines the various cleanroom classes from Class 1 to Class 9, where Class 1 has the most stringent cleanliness requirements.
However, injection molding is the most popular primary shaping process used in plastic processing. It is a great manufacturing process, which is especially well suited for mass production. Any parts produced in large volumes made of glass, rubber, metal, or plastic are typically created through injection molding. The process is straightforward: Molten plastic is injected into a mold, cooled down, and out pops the plastic product. It comprises four stages: clamping, injection, cooling, and ejection.
In cleanrooms, the amount and size of airborne particles are carefully controlled to reduce the chances of exposing sensitive medical components to these particles. ISO 14644 also outlines specific requirements for designing, manufacturing, and maintaining cleanrooms for optimal performance. Designers may need an injection molder with a Class 7 or Class 8 cleanroom to limit the potential for contamination during manufacturing.
AMPCO METAL has developed special high copper alloys called AMPCOLOY®. This polished hard version of copper alloys without coating or lead and clean trace elements are engineered with exceptional conductivity, high strength, and unique wear characteristics, delivering unique benefits.
Plastics processing refers to the manufacture of plastic products. In plastics processing, products are manufactured by processing and producing semi-finished products, molded parts, films, or fibers from plastics. The raw plastic product is usually supplied as granules, powder, sheets, or films.
The ISO 10993 standard consists of 23 parts or subsections. This includes processes and procedures for animal welfare requirements, tests for carcinogenicity, reproductive toxicity, in vitro cytotoxicity, and various sterilization techniques. USP (United States Pharmacopeia) Class VI covers similar biocompatibility requirements for plastics and, as such, is sometimes used in place of ISO 10993 or as a supplement. For designers, this standard can play an important role in material selection.
As the cooling phase is the stage that takes up the most time, it is also the lever to increase productivity. This is where the secret weapon of injection molding comes into play: Copper! Thanks to its unique properties, copper-based alloys like aluminum bronze or beryllium bronze can reduce cycle times and increase productivity by up to 80 percent! This allows companies to save 10 – 40 % of their production costs.
Access a wide breadth of capabilities through our highly vetted network.
By signing up, you agree to our Terms of Use and Privacy Policy. We may use the info you submit to contact you and use data from third parties to personalize your experience.
For designers, it’s important to remember that not all polymers are suitable for medical devices. However, injection molding supports the use of many different materials, typically commodity plastics but also specialty plastics and polymer blends. Designers can also choose medical plastics that have specific trade names like ULTEM®, a polyetherimide (PEI) that can withstand repeated cycles in an autoclave. Below are some common injection molding plastics and their salient characteristics:
The medical device industry is tightly controlled to ensure patient safety. Listed below are some of the common standards that affect manufacturing, including plastic injection molding.
Class II encompasses any medical device for which general controls are deemed insufficient to provide reasonable safety and effectiveness. Examples include contact lenses, syringes, and pregnancy tests. The EU MDR adds two subcategories:
Accelerate development with instant quotes, expert DFM, and automated production updates.
Of course, proper product design is also critical for medical devices, so check out our free Injection Molding Design Guide for best practices — it complements the info in this article. Download Fictiv’s Injection Molding Design Guide
For over a century, AMPCO METAL has pioneered and produced the best metal solutions for the world’s products, applications and industries.
We exist to eliminate bottlenecks in new product development by integrating the people, processes, and platform you need to source custom parts.
Class III medical devices are usually designed to sustain or support life and may present an unreasonable risk of injury or illness. Examples include pacemakers, defibrillators, and implanted prostheses.
The QSR (Quality System Regulations), also referred to as 21 CFR part 820, as outlined by the FDA, has many parallels with ISO 13485. In the United States, the QSR may be used as a supplement or replacement for the ISO 13485 standard.
Class I medical devices are not intended to support or sustain life and will not present an unreasonable risk of illness or injury to a patient. Examples include wheelchairs, glasses, hospital beds, and test tubes.
Industry standards play an important role in the design and manufacture of medical products, especially medical devices. For designers, these standards help ensure that patients, the end-users of injection molded products, are not exposed to excessive risks during medical treatment. So injection molders must implement stringent processes and procedures to control all stages of production and comply with standards.
GETTING A QUOTE WITH LK-MOULD IS FREE AND SIMPLE.
FIND MORE OF OUR SERVICES:
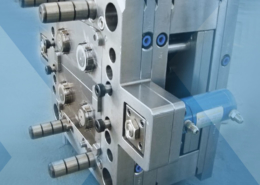
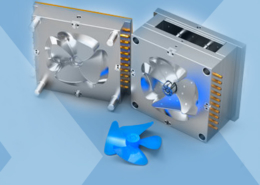
Plastic Molding

Rapid Prototyping
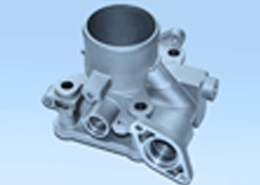
Pressure Die Casting
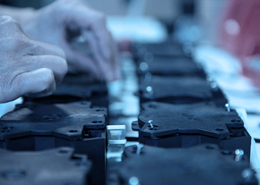
Parts Assembly
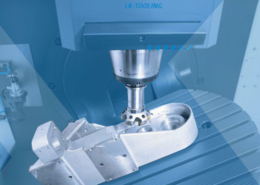