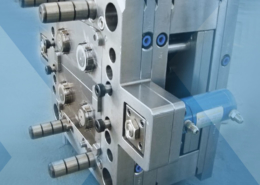
how to calculate the injection molding cost - plastic injection molding cost
Author:gly Date: 2024-10-15
When it comes to the injection mold cost involved in the cooling phase, evaluating the time taken by this phase is crucial. It can evaluate this time through the wall thickness and the thermodynamic properties of the plastic part. The longer or less time this phase takes, the faster or later the machine can stop working, and the mold can be opened.
Nave ISK-8, Parque Industrial y Logístico Sky Plus, Avenida Mineral de Cinco Señores No.100, del Parque Industrial Santa Fe, Silao de la Victoria, Guanajuato, México
Now the injection pressure usually ranges from 35-140 MPa. At the same time, you can evaluate the additional two factors by reading the hydraulic system in the machine once you complete the injection process for one product.
In this blog, we will explore the world of injection molding dies, specifically focusing on ACE, a renowned injection molding die manufacturer. We will delve into the top 10 tips for designing an effective injection molding die, walk you through the journey from concept to creation, and address common challenges in the manufacturing process and how to overcome them.
Material Selection: The choice of material for your injection molding die is crucial. ACE recommends using high-quality steel, such as P20, H13, or S136, to ensure longevity and precision.
8. Mold Maintenance: Regular maintenance is the key to prolonging the life of your injection molding die. ACE provides maintenance guidelines and services to keep your die in optimal condition.
ACE injection Moulding Company is an ISO 9001: 2015 certified mould manufacturer, providing services to the global plastic injection moulding industry.
Once the ejection is completed, the mold can be shut down and used for another shot’s ejection process. In this final stage, the pressure and time taken to eject the mold is also a factor that should be considered to determine the cost of injection molding.
Once you have evaluated every factor that may cost you a certain amount when using the injection molding process for a project, is that all? Probably not! It’s just as crucial to consider, understand, and evaluate how each expense takes place. The whole injection molding process may last from 2 seconds to 2 minutes. However, the limitation or extension of time for each phase involved in this process can also extend or minimize the costs.
To ensure a high-quality surface finish, ACE's expertise in mold texturing helps clients choose the right texture for their specific application.
Another crucial factor to consider when evaluating the cost of injection molding is the electricity expense. Since the entire injection molding process is carried out by machinery, electricity consumption is also exceeded.
The material cost is one of the high costs that affect the overall injection molding process budget. The material used for the part is of immense value in the molding process. The use of high-quality material for handling the injection process in the machine promises quality outcomes for the product/part, including better strength, durability, shape, and size.
And varying on the production type, complexity, and expected final product, these costs can either be very minimum or a decent part involved in the overall injection molding cost.
Nevertheless, Let’s look at the average cost of injection molds first. On average, the injection mold cost for small and simple cavity injection molds is around $1,000 – $5,000. However, as per the size extension and complexity of the molds, the injection molding cost can increase up to $80,000 or more. So different factors, processes, and types of expenses involved in the production process handled through injection molding can be different for different users.
Depending on the type of machine, the pressure the machine invests on the part, and the time the machine runs, the electricity cost can differ for producing one or more parts of different kinds.
In addition, the type of mold used in the machine is also involved in the material cost, as it affects the quality of the finished product.
4. Parting Line Placement: Carefully consider the location of the parting line to ensure minimal flashing and parting line marks on the final product. ACE's expertise in die design can help you optimize this aspect.
As we all know, mold is the premise of the injection molding process. When the amount of products produced by injection molding is large, the mold cost may be negligible. But when the amount of injection molding products is small, mold cost will be a large part.
One of the key advantages of ACE's Thin Wall Food Box is its lightweight construction. These boxes are specifically designed to be easy to handle, making them a preferred choice for food storage, transport, and service. Their low weight ensures that food remains fresh, preventing spoilage and waste. These boxes are also suitable for meal prepping, allowing you to portion out meals and organize your food efficiently.
5. Venting: Adequate venting is necessary to allow gases to escape during the molding process. Proper vent design is crucial to avoid defects like burning or gas traps. ACE has a long-standing commitment to ensuring optimal venting in their molds.
3. Draft Angles: Incorporating draft angles into your design is essential to facilitate easy ejection of the molded part. ACE suggests a minimum draft angle of 1-2 degrees for most applications.
To combat warping and shrinkage issues, ACE engineers pay careful attention to material selection, cooling channel design, and the overall mold structure. These factors are vital in minimizing these defects.
Before handing over the die to the client, ACE conducts extensive testing and validation processes to ensure it performs flawlessly during the injection molding process. This includes verifying the cooling system's efficiency, gate functionality, and overall mold performance.
Even with careful planning, challenges can arise during injection molding die manufacturing. ACE has a proactive approach to overcoming these challenges:
Once you understand every phase and the types of costs involved in every phase of the injection molding process, it is easier to determine the cost of plastic injection molding. As a result, with an estimated cost, you can ideally use, cater, and manage the injection molding cost to attain efficient part product outcomes.
In addition, additional production factors and demands like product complexity, expected production quality, material, and the product’s size also contribute to extending or minimizing the costs.
Of course, the above is just a list of the common basic costs of injection molding. There are also costs such as shipping, overhead, taxes, and other shared costs that affect the final injection molding cost. These costs are taken into account by the injection molding company during the injection molding quotation process.
So how do you evaluate the injection mold cost? Let’s go ahead and explore the detailed overview of these costs and how you can evaluate them per each process involved in injection molding.
1. Optimized Cooling Channels: Effective cooling is essential to maintain consistent quality. Design cooling channels for efficient heat dissipation to prevent warping or other defects in the final product.
Later, the pellets begin to melt due to the heat around the barrel and the pressure incorporated by the machine. As per the volume of the injected material, called ‘shots,’ the injection time and process are usually complete when the shots reach 95%-99% or the mold is filled.
Lastly, it’s the space or area cost where the injection molding process is conducted. Again, depending on the production scale and the number of parts you need to be manufactured in the given amount of time, the space demands can differ from project to project.
6. Tolerance Analysis: Pay meticulous attention to tolerances in your die design. ACE recommends using tight tolerances for critical dimensions while allowing for looser tolerances in less critical areas to maintain cost-effectiveness.
ACE, as a leading injection molding die manufacturer, excels in designing, manufacturing, and troubleshooting injection molding dies. By following the top 10 design tips, adhering to a systematic manufacturing process, and addressing common challenges, ACE guarantees top-quality dies that meet the demanding requirements of the injection molding industry. Whether you're in the automotive, medical, or consumer goods industry, ACE is a trusted partner in the world of injection molding die manufacturing.
2. Gate Design: Proper gate design is the key to controlling flow and pressure during the injection process. Work closely with ACE engineers to determine the ideal gate type and location for your specific project.
9. Prototype and Test: Before mass production, create a prototype and conduct thorough testing to validate your design. ACE can help with prototyping and assist in making necessary adjustments.
Lastly, the final phase of the injection molding process is the ejection process. As the machine’s last process, this process is handled by the ejection system. The machine pushes the part out with force when the mold is opened. Force is mainly used in this phase to smoothly push the shrunk part that may have stuck to the mold.
Another crucial factor to consider when evaluating the cost of injection molding is time. When you consider professional and reliable manufacturing companies that offer you various services and manufacturing process solutions like injection molding, they highly consider the time taken in the production process, varying on how long the machine is used. Simply put, manufacturing factories highly prioritize time when managing the injection molding process on a budget is an additional cost factor. Therefore, the time of an injection cycle is very important. That’s what we are about to talk about.
Once the prototype is approved, ACE proceeds with manufacturing the actual injection molding die. They utilize state-of-the-art machinery and precision tools to create the die with the utmost attention to detail.
Plastic thin-wall food boxes are designed to be space-efficient. They can be stacked neatly, taking up minimal storage space, and making them a practical choice for restaurants, kitchens, and food service establishments. In addition to efficient storage, these boxes are ideal for storing leftovers, and since they can be reheated in the box, they promote sustainability by reducing the need for additional containers or wraps. Labeling these containers for easy identification is a breeze, streamlining your kitchen organization.
Tolerances are critical in maintaining consistent product quality. ACE's precision tooling and quality control measures help minimize dimensional variability.
At every stage of the manufacturing process, ACE conducts quality checks and inspections to ensure the die meets the desired specifications. This includes checks for proper material hardness, dimensional accuracy, and surface finish.
The process starts with meticulous design and engineering. ACE's team of experts collaborates closely with the client to understand the project requirements, material choice, and design specifications. Using advanced software and industry expertise, they craft the initial design, keeping in mind the top 10 tips mentioned earlier.
Now varying on the machine type and size, which depends on the project and how much clamping power the machine needs to incorporate on the mold halves, the time of closing and clamping the mold can be more or less. Simply put, larger machines may take more time, resulting in more plastic injection molding costs, whereas the smaller ones may cost less.
Once the cooling period has elapsed and the part has wholly taken its form, the mold can be reopened in the final stage.
Hence, understanding the injection molding cycle and the time each process takes can make it easier to plan the injection molding cost estimate to acquire this result. Does that sound like an intelligent plan to manage budget planning and financial investment? Then, let’s dive into the details of each stage and the time it takes!
The journey from an idea to a functional injection molding die is a well-coordinated process. ACE follows these key steps to ensure the highest quality dies:
The location of the parting line is crucial in preventing flashing and parting line marks. ACE works closely with clients to optimize parting line placement during the design phase.
Inadequate venting can lead to gas traps and burning. ACE ensures that the molds they produce have optimal venting, and they also advise clients on proper maintenance to prevent vent clogging.
The very first stage that should be considered for evaluating the injection mold cost for your project is clamping. The primary purpose of the clamping stage is to close both halves of the mold before the mold is injected with the material. Hence, these halves are closed with the help of a clamping unit.
The artificial cost is also included in the overall injection molding cost estimate. This cost is mainly the expenses involved in the related departments. In simpler terms, the costs created by one department by utilizing other departments’ services within a company or manufacturing setup are known to be the artificial cost.
For instance, if we talk about making wooden tables, electricity costs, wood costs, base and structure cost of the table, machine and equipment cost for cutting and drilling the wood, and additional décor items cost to finish the final look of the table – all of these are essential to build and complete a table that is ready to be sold and used by a potential customer.
DongGuan Company Room 103,#41 Lian Ma Road,Dalingshan Town,Dongguan City,Guangdong Province,China ShenZhen Company Building 5,Juhui Mold Industrial Park,Tianliao Com,Yutang St,Guangming District,ShenZhen City, China
7. Mold Texture: The texture of the mold surface directly affects the appearance of the final product. Collaborate with ACE to determine the ideal texture for your specific application, whether it's matte, glossy, or textured.
If you’re opting for the injection molding process for shaping and manufacturing plastic and rubber items for your business, you may be curious to know ‘what is the injection molding cost estimate’? Generally, when you’re opting for any manufacturing process, it’s evident that multiple stages/processes, materials, and additional requirements may need funding for the manufacturing process to proceed and complete. Whether it’s the simple manufacturing of wooden tables or plastic and rubber materials used in different industries like tech, hardware, etc., producing anything and everything is only possible if you can fund it.
After finalizing the design, ACE creates a prototype die to test and validate the design's functionality and efficiency. This step is critical for making any necessary adjustments before moving forward.
When it comes to manufacturing plastic parts on a large scale, injection molding is the go-to method. A critical component of this process is the injection molding die, which plays a pivotal role in shaping the final product.
While this is a process of wooden table production and the different costs involved, manufacturing plastic or rubber items through the injection molding process also comprises multiple processes and relevant finance demands. Since the injection molding process is focused on shaping products by injecting heated material inside a mold, multiple products and processes involved in this manufacturing method are involved in the overall injection molding cost.
The second phase of the injection molding process is the injection phase. In this phase, the plastic pellets are fed to the mold using a hopper in the injection molding machine. The injection unit in the machine pushes these pellets toward the mold.
It can be challenging to determine the estimated time to evaluate the injection molding cost involved in this phase. The main reason it had to determine the time and cost of the phase is the consistent changes in the flow of the plastic and its dynamic. However, it can evaluate the injection time if we consider other factors, including the injection pressure involved, the power applied by the machine varying on the project size and complexity, and the shot volume.
Later, these halves are attached with an injection molding machine, where one-half is placed on the side. Once the machine starts running, the material is injected while the clamping unit consistently pushes the halves together. The machine holds these closed halves tightly together as the material is injected.
When determining the overall cost involved in injection molding for any kind of project, it’s essential to consider each expense you will have to bear during the production process. From the raw material to the operation, and even the repair costs as well as tool costs, each factor collectively contributes to evaluating ‘how much does injection molding cost?’
DongGuan Company Room 103,#41 Lian Ma Road,Dalingshan Town,Dongguan City,Guangdong Province,China ShenZhen Company Building 5,Juhui Mold Industrial Park,Tianliao Com,Yutang St,Guangming District,ShenZhen City, China
Next up is the cooling phase involved in the injection molding process. This phase involves cooing the plastic inside the mold, which begins once the plastic comes in contact with the interior mold. Slowly, as the plastic cools and starts hardening, it takes the desired shape per the mold. However, the plastic part often does shrink slightly during this cooling phase.
GETTING A QUOTE WITH LK-MOULD IS FREE AND SIMPLE.
FIND MORE OF OUR SERVICES:
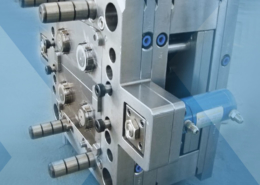
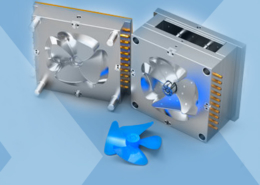
Plastic Molding

Rapid Prototyping
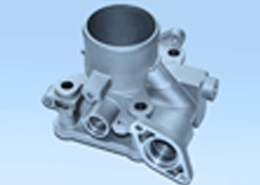
Pressure Die Casting
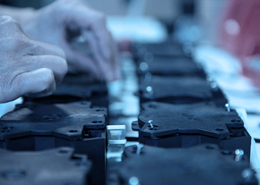
Parts Assembly
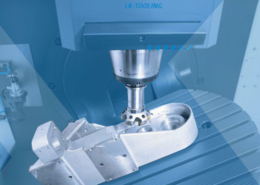