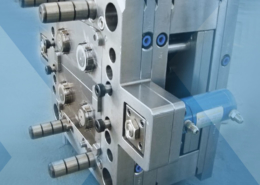
How Much Does Injection Moulding Cost? - plastic injection molding cost
Author:gly Date: 2024-10-15
Although double injection molding is a versatile and cost-effective manufacturing process, it is complex to achieve because of its complex molding process. It requires a high level of expertise which you can get from FOW Mould.
Injection molding is a popular manufacturing process for creating a wide range of plastic products, including containers, electronic products, medical equipment, toiletries, gardening tools, and plastic toys. Two shot molds are popular types of injection molding, which involves combining two different complex materials to achieve a design in a single manufacturing process.
Co-injection molding differs from the previous process in that the material injection metering zone become two and no longer one.The two materials are divided into the body (core) and the skin of the article. This innovative process allows to melt together recycled materials, obtaining an aesthetic of the product equal to the traditional molding with virgin material. In the process, the recycled material forms the core of the article, which is covered by the virgin material that makes up the skin. Moreover, in most cases the core is added with expanding granules to avoid the deformation of the article.
Traditional molding is the injection transformation technique for the production of items with small to medium thicknesses. The process starts with the insertion of virgin material through the injection metering zone into the machine, which once melted, is injected into the mold. The machine has a single plasticizing metering zone that brings the plastic into the melt and injects it into the mold. This is followed by a cooling time and subsequent extraction of the piece by an automated arm. On average, articles with a maximum thickness of 6/8 mm are produced.
The finished material from the injection molding will possess the qualities of the two materials used in the molding process. Also, they will have the colors and physical properties of the materials.
There are some disadvantages to 2-shot injection molding that must be considered. This includes high costs, long setup lead times, and part design restrictions.
The first step in 2 shot injection molding process is designing a mold that can accommodate two materials or colors in the same mold cavity. Once a suitable injection mold is designed, the first material is injected into the mold cavity, creating the first part of the finished product. The injection pressure, speed, and temperature are carefully controlled to ensure the material fills the mold cavity completely and accurately.
Double injection molding is quite cost-effective. By producing a finished part in a single molding cycle, the process reduces the need for assembly and secondary operations, which can save time and money. Additionally, the two materials used in double injection molding are bonded together in the mold. This eliminates the cost of using fasteners or adhesives.
In many cases, in the traditional transformation process, some points of the article are subjected to too much pressure during the process, thus causing possible deformation of the final article. However, in Co-injection since the articles are thicker, they are able to withstand higher pressures without generating any type of distortion. The articles obtained have thicknesses from 15 to 40 mm.
For instance, the two-shot injection molding process can create phone cases with soft-touch grips or dual-colored designs, which can make the product more visually appealing to consumers. The process can also be used to create computer keyboards with rubberized keys, which can provide a better typing experience for users.
Two-shot injection molding can create toiletries with specific properties such as chemical resistance and high temperatures, which can be crucial in certain applications. For example, some toiletries may need to withstand exposure to harsh chemicals or high temperatures during use or storage.
Two shot molds are molds gotten from the mixture of two distinct materials in a mold cycle. Two-shot molding is a plastic injection molding process that enables the production of complex parts in a single molding cycle by using two different materials or colors. It involves injecting two different materials or colors into a single mold cavity to create a finished part with two distinct parts.
In this article, we will delve deeper into the benefits and applications of two-shot molding and the services offered by FOW Mould for injection molding.
© 2021 © MASPI S.R.L. | Via Castegnate, 86 - 24030 Terno d'Isola (BG) | Tel. +39.035.4944117 | P.IVA IT00781490164 Web Horizondesign
Two shot injection molding offers enhanced product quality. This is because the two materials are bonded together in the mold, and the finished product is more durable and resistant to wear and tear. Additionally, the process allows for greater design flexibility, resulting in products with more intricate shapes and details.
Two-shot injection molding has a wide range of applications across various industries due to its versatility and design flexibility.
The second material is then injected over the first part, to form a bond between the two materials. The second material is also carefully controlled in terms of injection pressure, speed, and temperature to ensure it bonds properly to the first material. After the second material has cooled and solidified, the mold is opened, and the finished product is ejected.
One of the services offered by FOW Mould is the utilization of first-class plastic materials for making injection mold storage. This ensures that the plastic molds are of the highest quality and will meet the specific needs of their clients.
Soft-touch grips can also reduce hand fatigue, allowing gardeners to work for longer periods without experiencing discomfort.
One of the key advantages of using two-shot injection molding for medical equipment is that it allows for the production of parts with multiple materials or colors. This can help differentiate different components of the equipment. This can be particularly useful in complex medical devices, where ensuring that each component is easily identifiable and distinguishable is important.
One of the key advantages of two-shot molding in the production of gardening equipment is the ability to create tools with soft-touch grips, ergonomic handles, and dual-color schemes. These features improve the overall user experience by making the equipment more comfortable to use and easier to identify.
Two-shot molds are widely used in the toy industry to produce plastic toys such as action figures, dolls, and cars. The process allows for the creation of toys with intricate designs and features, as well as improved durability and safety. Additionally, two-shot injection molding can be used to produce toys with unique features, such as a soft-touch finish or multiple colors.
Two-shot injection molding is commonly used to produce containers such as cups, lids, and bottles. The process allows for the creation of containers with intricate designs and features, such as soft-touch grips and dual-color schemes, which can enhance the consumer’s experience. Additionally, the two materials used in the process can provide greater durability and resistance to wear and tear, making the containers more long-lasting.
If you are in need of injection molding services, consider working with FOW Mould, who offer a full range of services to meet your needs, from utilizing high-quality plastic materials to custom design services and short lead times. We have the expertise and experience to deliver high-quality two-shot molds made to precision within a quick turnaround time.
Traditional molding is the injection transformation technique for the production of items with small to medium thicknesses. The process starts with the insertion of virgin material through the injection metering zone into the machine, which once melted, is injected into the mold. The machine has a single plasticizing metering zone that brings the plastic into the melt and injects it into the mold. This is followed by a cooling time and subsequent extraction of the piece by an automated arm. On average, articles with a maximum thickness of 6/8 mm are produced. Co-injection molding differs from the previous process in that the material injection metering zone become two and no longer one.The two materials are divided into the body (core) and the skin of the article. This innovative process allows to melt together recycled materials, obtaining an aesthetic of the product equal to the traditional molding with virgin material. In the process, the recycled material forms the core of the article, which is covered by the virgin material that makes up the skin. Moreover, in most cases the core is added with expanding granules to avoid the deformation of the article. The first great advantage of this technique is the reduction of CO2 emissions, obtaining articles with recycled material of great aesthetics, the second is the possibility to have larger thicknesses of the article reducing the risk of deformation. In many cases, in the traditional transformation process, some points of the article are subjected to too much pressure during the process, thus causing possible deformation of the final article. However, in Co-injection since the articles are thicker, they are able to withstand higher pressures without generating any type of distortion. The articles obtained have thicknesses from 15 to 40 mm. The Restylon technology allows the realization of Co-injection products with the use of second life material, producing high quality articles without deformation.
The Restylon technology allows the realization of Co-injection products with the use of second life material, producing high quality articles without deformation.
FOW Mould also offers custom plastic crate mold design services that experienced experts carry out. This ensures that their clients receive plastic crates that meet their exact specifications and are of the highest quality.
Two shot injection molding has a wide range of applications, including automotive interior parts, medical equipment, tools, and toys. This versatility is due to the process’s ability to combine two different materials or colors in a single molding cycle, providing designers and engineers with greater flexibility in creating unique designs and functionality.
Double injection molding is widely used in the production of electronic products such as computer keyboards, phone cases, and remote controls. The process allows for the creation of electronic products with complex shapes and designs, as well as improved functionality and durability.
FOW Mould is a reliable and experienced company that offers a variety of injection molding services, from utilizing high-quality plastic materials to custom design services and short lead times.
Some of the key benefits of double injection molding include cost-effectiveness, enhanced product quality, and versatility.
ACIS®, Autodesk Inventor®, CATIA® V5,Creo™ Parametric, IGES, Parasolid®, Pro/ENGINEER®,Siemens PLM Software’s NX™, SolidEdge®, SolidWorks®, STEP
In addition, FOW Mould is known for its short lead times when it comes to fulfilling its customers’ plastic container mold needs. They are able to deliver high-quality molds made to precision within turn-around times as short as 10 days, ensuring that their clients can meet their production deadlines and keep their businesses running smoothly.
The first great advantage of this technique is the reduction of CO2 emissions, obtaining articles with recycled material of great aesthetics, the second is the possibility to have larger thicknesses of the article reducing the risk of deformation.
Two-shot injection molding is commonly used in the medical industry to produce equipment such as syringes, surgical instruments, and drug delivery devices.
Two-shot injection molding may have restrictions on the part design due to the limitations of the process. For example, the rotating or sliding mechanism required for 2-shot injection molding may limit the size or shape of the part that can be produced. Additionally, the two materials used must be compatible and able to bond properly, limiting the types of materials that can be used.
Two-shot injection molding requires longer setup lead times than traditional injection molding processes. The molds and tooling used for two-shot injection molding must be designed and manufactured to specific specifications, which can take longer than the setup for traditional injection molding processes.
Two-shot injection molding is used to produce a wide range of toiletry products, such as toothbrushes and cosmetic containers. The process allows for the creation of toiletries with complex designs and features, as well as improved functionality and durability.
GETTING A QUOTE WITH LK-MOULD IS FREE AND SIMPLE.
FIND MORE OF OUR SERVICES:
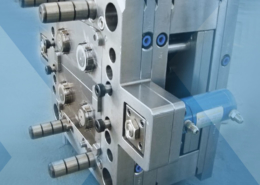
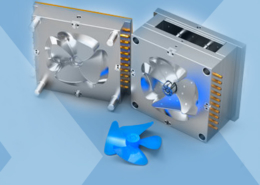
Plastic Molding

Rapid Prototyping
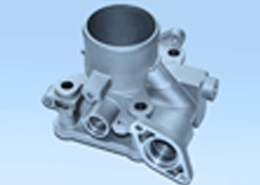
Pressure Die Casting
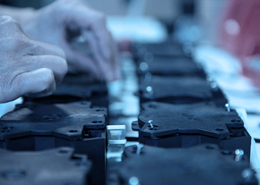
Parts Assembly
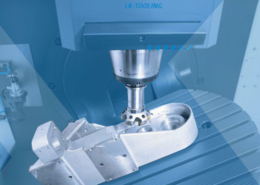