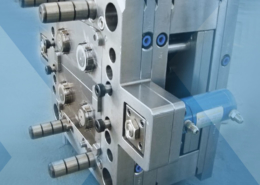
How Much Do Injection Moulding Projects Cost? - abs injection molding cost
Author:gly Date: 2024-10-15
Once you have melted it accordingly depending on various properties of the plastic, you then pour the molten plastic in the casting mold to allow it to cool and also harden.
It refers to a plastic part manufacturing process which involves the introduction of a liquefied plastic material allowing its solidification in a mold.
The customer needed a sturdy lightweight plastic handle for a cooler, however also desired a non-slip over-mold for comfort and function.
In simple terms: one mold, two injections, one cycle. The first plastic injection runs through the mold and then gates are closed, the mold is automatically rotated (rotary mold), or a part is transferred within the same mold (pick and place) and a different type of plastic is injected into the mold.
On the other hand, in plastic thermoforming, a plastic sheet is heated then pressed between two mold halves to enable it to form a part.
When choosing the mold for plastic casting it is necessary to make sure that you go for those that match the recommended quality specifications.
A suitable approach for this defect is by getting rid of slag particles from molten plastic material before pouring it in mold cavity.
It is necessary to ensure that the quality of the plastic material you are using reaches to the level of the required standard to prevent defects such as residuals, sticky sands, and air holes.
It has a better tolerance on the thickness and you can still achieve tighter tolerances by prior arrangement with extrusion mill.
The plastic material fills the casting mold model which is subsequently allowed to harden to a point of removing it from the cavity and beginning of casting of the component.
It is also fundamental to ensure that you select reasonable casting methods depending on the size, structure, weight, and properties of the plastic sheet material and work conditions as a way of producing high-quality parts.
In some instances, plastic can fill in the cracks in sprues or casting mold thus making it a necessity for you to finish the plastic following casting.
Extruded plastic, on the other hand, refers to a type of plastic materials manufactured by a continuous production process.
Once you achieve proper appearance and texture, you can as well proceed to further post-treatment process like a painting of electroplating depending on various elements.
It is a defect caused when molten plastic material that contains slag particles is poured inside mold cavity and gets solidified.
A two-shot mold offers different resins in the same part and same mold. Those different resins in a second shot could be for:
It refers to the type of casting or embedding of a wide range of objects in epoxy resin where silicon or resin casting molds are used.
It occurs as a result of enlargement of mold cavity due to molten plastic pressure that leads to enlargement of the entire casting.
The process operation needs to be reasonable and the technical level of workers also should increase to enhance production quality and rates of plastic tool casting.
Mold closes and the lower four cavities are filled with the first shot of hard plastic. Mold slides are retracted after the mold opens. Robotics will remove the parts from the lower cores as the ejector plates advance. Parts are placed on the cores of the upper (over-mold) side. Slides are advanced to capture the parts, the mold closes and is filled with the second non-slip soft shot.
Cast plastic is manufactured by a process whereby MMA liquid is pressurized into a monomer which is submerged in warm water resulting in the polymerization process.
Our product manager will give you a quick demand portrait according to your design, drawing, standard, testing methods and other requirements. And we have a strong supporting team to fulfill your demand with our deep technology and know-how base. We can offer you a solution or a few options. And you will decide which one you prefer.
It is always vital to make sure that you depend on plastic material and work condition during designing as a way of determining shape as well as the size of machine tool casting.
It is a defect commonly as a result of entrapped gases on the surface of the casting due to plastic resin solidifying and causing a rounded cavity.
It is usually caused either by extremely high pouring temperature or inconsistent or unregulated solidification of molten plastic material.
On the other hand, plastic molding refers to the act forming a cavity which carries a reverse or negative impression of an original model.
This defect occurs when molten plastic solidifies before entirely filling the mold cavity then leaves a space in the mold.
A common cause for this defect is low temperatures of molten plastic which reduces fluidity and improper gating system as well as a thin section.
It arises as a result of misalignment of the lower and upper parts of the casting and misplacement of the core at the parting line.
Plastic casting is basically the act of pouring the plastic liquid into the mold cavity which cures after a particular duration through a chemical reaction and cooling under set parameters.
Double shot, or two-shot mold design, combines two materials into one part in a single mold. One mold helps in the reduction of secondary machines, processes and molds. When designed right, two-shot molds significantly reduce the amount of scrap, cycle times, resin, work-in-process, and assembly, thus, driving down costs and improving the quality and consistency of the finished product. Two-shot molds can even be used with Rotary or Pick and Place mechanical actions.
You can achieve this by carefully designing the mold, understanding properties of plastic, controlling both heating and pouring processes.
It is the second step in the process which involves placing of solid materials inside the mold cavity as a way of creating interior surfaces of a casting.
WeProFab is a joint-venture company between WeeTect Material Limited and a Chinese local plastic fabrication manufacturer. We hold full capabilities on plastic fabrication, which can support us to offer you one-stop solutions for OEM/ODM customers.
You also need to know the kind of temperature and pressure it needs to withstand as well as any possibility of the chemical or any other element exposure.
GETTING A QUOTE WITH LK-MOULD IS FREE AND SIMPLE.
FIND MORE OF OUR SERVICES:
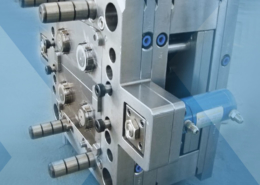
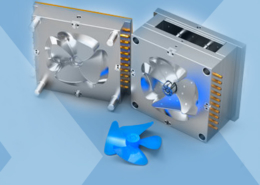
Plastic Molding

Rapid Prototyping
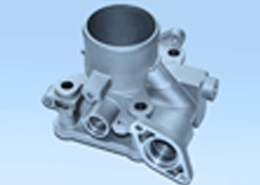
Pressure Die Casting
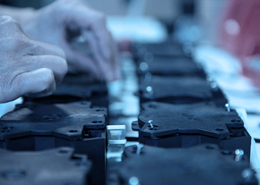
Parts Assembly
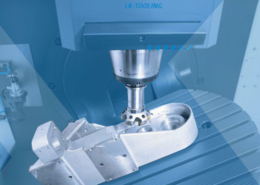