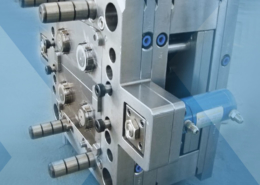
How Much Do Injection Molding Costs and How to ... - low cost plastic injection
Author:gly Date: 2024-10-15
Share on LinkedIn 0 E-mail 0 Facebook 0 Twitter 0Home - Added services - Project management for Injection Molding - Polyethylene (PE) Injection Molding
Molding works well for various kitchen products, such as plastic plates and utensils. These products must often be resistant to elevated temperatures, easy to clean, dishwasher safe, and non-toxic. Injection molds can mold materials that meet all these requirements at high volumes.
PE is available as HDPE (High Density Polyethylene) and LDPE (Low Density Polyethylene) among others. HDPE, with a higher density, is more applicable at higher temperatures and is more chemically resistant. LDPE is a softer material and therefore has a higher resilience.
LinkedIn 0 E-mail 0 Facebook 0 Twitter 0Home - Added services - Project management for Injection Molding - Polyethylene (PE) Injection Molding
All those lids for those plastic bottles? Yes, they also come from injection molds. Since these items tend to be small, it is easy to design mold tooling to produce enormous quantities at once. With the high demand for plastic lids and caps across many industry verticals, it should be no surprise that the rapid throughput of molding machines is the manufacturing method of choice.
Have you ever wondered where the various objects in your house come from? We’re not talking about the shop or even the country of origin, but rather how these objects were made before eventually arriving in your home.With so many manufacturing methods around, you might not know that most of these products come from the design and manufacturing process for injection molded plastics. You likely have hundreds of different objects in your home created with this technique, but to emphasize how common these items are, we’ve put together a list of everyday injection molded parts.
While injection molding doesn’t contribute much to the major hardware components on computer circuit boards, it touches almost every other aspect of these devices. Everyday items that undergo injection molding for use in computers include laptop shells, speaker housings, computer monitor bezels and even the keyboards you type on every day. The durability of these materials makes them well-suited to the long lifespan requirement for most computer hardware. Additionally, things such as light switches, other electronic housings, and a wide range of appliances also come from injection molds.
Toys for children are also among the most common injection molded plastic parts for several reasons. First, you can expect complex toy designs and true-to-life colors from injection molds. Second, the ability to combine materials allows the molding systems to produce huge volumes in a relatively brief time. Lastly, the material selection also contributes to the popularity of this method with toys, because it is easy to make non-toxic, non-porous, and easy-to-wash products.
Ultimately, this list only scratches the surface of how many everyday injection molded objects appear in the average household. However, it shows the versatility and reliability of the injection molding process. Most people never think about how the objects they use were made, but this information is crucial if you have plans to manufacture products yourself.
With such a versatile process available to manufacturers, it’s no surprise these products are found everywhere. Injection molding products have only gotten more popular in recent years.
Fleur Plastics is located in Boxtel (near Eindhoven, The Netherlands) and has been a producer of technical plastic products for more than 15 years. The core business of Fleur Plastics is plastic injection moulding and we want to continue to develop on this as much as possible. As an involved partner, we gladly discuss your entire project, starting from the product drawings and construction of moulds, to optimize the final production. We use top notch injection moulding processing techniques to produce these products in all types of thermoplastic plastics. As a family business in the plastic injection moulding industry, we are able to provide our customers with expertise, quality, service and flexibility.
Thanks to its unique properties, polyethylene can call itself the most widely used plastic in the world. PE can be found in various industries due to its favorable properties and low price. It is a soft plastic, which remains flexible and usable up to -50 degrees Celsius. In addition, PE has a high chemical resistance and negligible moisture absorption. Polyethylene is naturally transparent, but any desired color can be made by using pigments.
Terracotta pots are lovely, but they’re expensive. Plastic flowerpots provide the same stable space for plants to grow while resisting breakage and lasting for a far longer time. Thanks to the tooling design, these everyday items and garden products also come out of injection molds, as it is easy to create the necessary shape while leaving drainage holes at the bottom with few to no additional manufacturing costs.
If you have any medical devices at home, such as heart-rate monitors, blood-pressure monitors, or even syringes, the odds are high that they came from injection molds. For a home, the injection molding machine can mean the difference between affordable medical devices that meet strict requirements versus expensive products that only businesses can afford.
It is incredibly easy to find items around the home that are, in fact, injection-molded products. Many manufacturers prefer the injection molding production method for a few key reasons. Across large commercial manufacturing runs, injection molding offers several significant advantages, such as:
Because polyethylene softens the moment it is heated, you can easily process it and use the material for a wide variety of applications. By melting the polyethylene granules (granulate), we can convert them into various end applications, such as lids, packaging and seals.
Given the uncountable number of different beverage products on the market, you are more likely to have at least one injection-molded plastic bottle in your home. PET, a common plastic material for bottle design, flows easily through injection molds and creates durable yet lightweight products for use as liquid containers. Even reusable plastic products, such as refillable water bottles, come from injection molds.
In addition to 3D product drawings, injection moulds and plastic injection moulding, the various plastic materials are also important for the quality of your products. For each new injection moulded product, we consider which material is best to use. After all, the type of material must match the application of the injection moulded product. The wide range of types of plastics each have unique mechanical properties, but in general, plastics offer greater design freedom, weight savings and are widely applicable. Due to the different prices of the plastic materials, choosing the right material can immediately save costs for you. One of our sustainable and high-quality raw materials is polyethylene (PE).
In plastic injection moulding, plastic is melted and injected into an injection mould under high pressure. The mould is shaped after the desired product. During the cooling process, an additional amount of material is pressed into the mould to account for the shrinkage of the material. When the product has cooled sufficiently, the mould opens and the product is ejected.
Our modern moulding facility is optimized to work day and night. Our machines produce polyethylene injection moulded products, ranging from 1 to 420 grams. In addition, we share our expertise through project management in the Netherlands. If you have any questions about your project or PE injection moulding, gladly get in touch with us.
At Reliant Plastics, a Texas-based injection molding provider, we have decades of industry experience and cutting-edge equipment available to use for your next production run. Please consult with our team on designing, fabricating, and running the molds that will supply the products for your next major business push. Contact us to learn more and get a free quote today.
So what are some of the most common injection molded objects often found in households? The average homeowner can easily find just about every single one of the following objects in their homes. Let’s consider what’s made by plastic injection molding and why.
There are more plastic parts in and on a toilet than you might expect, but the toilet seat is the most prominent example. With various shapes and sizes, such an injection molding product takes advantage of the same plastic properties other products do. These properties include bacterial resistance, a non-porous surface that can undergo sterilization and a high degree of long-term durability. The toilet hardware itself will likely wear out long before the seat ever does.
While the classic wooden chair still has its place in the home, a wide variety of modern furniture, especially chairs, now feature all-plastic construction. Injection molds can produce these parts to exact tolerances for consistency between production runs. At the same time, making molds large enough to create full-sized furniture or components that will undergo assembly by the user at home is also straightforward.
From the hangers in your wardrobe to the plastic frames of some mirrors or plastics used to house makeup, injection molds have a footprint everywhere. Since quick turnarounds and big orders are a key requirement for these industries, injection molds are the obvious best way to get it done.
GETTING A QUOTE WITH LK-MOULD IS FREE AND SIMPLE.
FIND MORE OF OUR SERVICES:
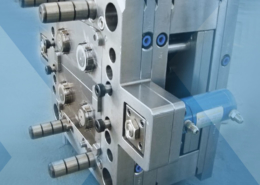
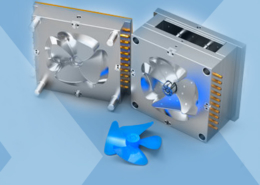
Plastic Molding

Rapid Prototyping
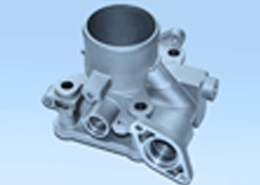
Pressure Die Casting
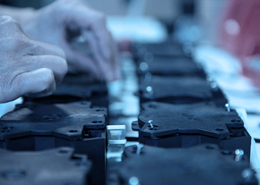
Parts Assembly
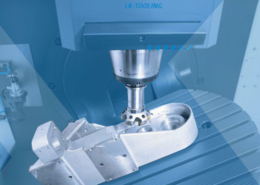