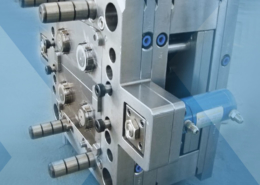
How Much Do Injection Molding Costs and How to ... - custom plastic molding cost
Author:gly Date: 2024-10-15
The SLS method also makes use of a strong laser. It creates a 3D model by sintering powdered materials as opposed to SLA. The print quality produced by this method is better than that of FDM. This process produces prototype pieces that are more functional and have higher resolution. They typically outperform FDM prints in terms of flexibility and durability.
Let's look at how 3D printing, CNC machining, and vacuum casting can be used to make a prototype. Knowing the inner workings of the technology, compatible materials, and typical applications will help you choose which quick manufacturing approach is most suited for your prototype.
After finishing the master model (by either using 3D printing or CNC machining) silicone-based casting moulds are created. Using a vacuum bell jar, the raw materials are injected into the mould cavity. The process of hardening the resulting cast to produce an exact replica of the prototype typically takes between 30 and 40 minutes.
The term "additive manufacturing," more popularly known as "3D printing," actually refers to a variety of production techniques. Fused Deposition Modelling (FDM), Stereolithography (SLA), and Selective Laser Sintering are the three most widely utilised techniques for creating sample prototypes (SLS).
Thermoforming often utilizes lightweight aluminum molds, minimizing both tooling costs and lead times. Thermoforming molds are typically single-sided and can be fabricated more swiftly due to the material's malleability, making it an efficient and cost-effective alternative to traditional injection molding.
The low volume injection molding process begins with the creation of a custom-designed injection mold. The mold is then mounted onto an injection molding machine, where thermoplastic pellets are fed into a heated barrel within the machine, where they are melted to a liquid state. The molten plastic is then injected under high pressure into the mold cavity, conforming to its shape and intricacies.
Additionally, a CAD model demonstrates how the components join and how the device works as a whole. It will assist you in making a physical prototype model, either visual or functional.
Get started today by receiving a free quote tailored to your project for plastic parts and products. Contact us now by calling us at 919-404-2080 or filling out the online contact form. Don't delay—unlock the potential of custom plastics manufacturing with us today.
Choosing between low volume injection molding or thermoforming methods requires careful consideration of various factors to ensure the optimal manufacturing solution for your specific project requirements.
Fabricators can produce prototypes with enhanced strength using industrial-grade FDM printers, dependent on the materials utilised. Furthermore, it is a flexible process that works with a variety of materials, such as Nylon, PETG, Polycarbonate, PLA, ABS, etc.
Potential investors would be able to examine your product first through a prototype, and designers would have opportunities to make the necessary adjustments throughout this procedure. Thus, it is beneficial for both producers and consumers.
The success of your prototype will largely depend on your knowledge of the different prototyping technologies. Here we have discussed the three most effective and popular methods: 3D printing, CNC machining, and vacuum casting. You should be able to make the decision on which one is suitable for your business's needs and requirements.
Thermoforming is a versatile manufacturing process involving the heating of large plastic sheets until pliable, which are then shaped around a custom-fabricated aluminum tool.
Low volume injection molding, also known as "short-run manufacturing," serves as the vital bridge between product prototyping and high-volume production, catering to orders typically fewer than 10,000 pieces.
With a commitment to precision, efficiency, and cost-effectiveness, our injection molding company specializes in providing comprehensive solutions tailored to your unique plastic part needs. Whether you're aiming for intricate details with low volume injection molding or seeking the versatility of thermoforming, our expertise ensures that you can make informed decisions to propel your project forward with confidence.
Fabricators can reproduce several prototype parts using vacuum casting. To build pieces that are appropriate for testing, a master model is used. The process of vacuum casting includes injecting the raw material into a silicone mould to create prototypes. A master model is required first, though, before a silicone mould can be made.
Since 1988, Advanced Plastiform, Inc., has been providing superior custom plastic molding and fabrication services to companies in North Carolina, South Carolina, Maryland, Georgia and Pennsylvania. Contact us to make an appointment Mon-Fri 8-5.
Consider the anticipated production volume for your project. Low volume injection molding is typically suited for production runs of fewer than 10,000 pieces, making it ideal for smaller quantities. Thermoforming, on the other hand, offers flexibility for both low to mid-volume production runs, with the ability to scale up or down as needed.
A digital depiction of your planned product, the Computer-Aided Design (CAD) model, demonstrates to you and the manufacturer how the product should look. This is the first thing that you should consider before manufacturing prototypes.
Another practical and quick way for making prototypes is CNC machining. This technique builds a 3D model of your idea out of solid materials using a variety of tools. As opposed to 3D printing, which uses an additive process, CNC machining is subtractive, meaning it takes away from a material.
While FDM uses filaments, SLA printing uses polymer resin to make prototype polymer items. It entails utilising a powerful laser to harden the model that was created using a container of resin. It allows manufacturers to apply this technique to the development of a variety of components, such as for the dental, and medical industries.
Navigating the realm of manufacturing processes can be a daunting task, especially when considering options like low volume injection molding or thermoforming. At Advanced Plastiform Inc., we understand the critical importance of choosing the right method for your project.
After cooling, the mold opens, and the newly formed plastic part is ejected. Depending on the complexity of the part and the requirements of the project, secondary operations such as trimming, machining, or assembly may be performed to achieve the final desired product.
Prototyping is a good way to make sure your production process generates high-quality results. A physical product should always be evaluated before mass production starts.
JavaScript seems to be disabled in your browser. For the best experience on our site, be sure to turn on Javascript in your browser.
We proudly serve the Mid-Atlantic and Southeast, including North Carolina, South Carolina, Pennsylvania, Maryland, Tennessee, Georgia, and Virginia.
Consider your project timeline and production speed requirements. Thermoforming typically offers faster lead times and shorter production cycles compared to low volume injection molding, making it a preferred choice for rapid prototyping and quick-turn projects. However, if precision and tight tolerances are critical, low volume injection molding may be the better option despite longer lead times.
Prototyping is a crucial step in almost every type of product development, regardless of the industry. User testing is possible with prototypes, giving designers insightful input and feedback on their creations.
In contrast, low volume injection molding often employs aluminum molds, operating at lower pressures to safeguard against mold damage. This strategic choice significantly reduces tooling costs by 5 to 25 percent, with aluminum's malleability facilitating quicker mold creation, thereby expediting the overall injection molding process timeline.
Twin sheet forming is an advanced technique where two plastic sheets are heated simultaneously and formed together to create a hollow, double-walled structure, offering enhanced strength, insulation, and structural integrity for applications such as automotive components, farming equipment, outdoor furniture, and more.
It will eventually determine whether your production efforts are successful. It is now simple and economical to quickly develop a sample prototype thanks to the growth of fast prototyping. The product development process will be optimised if you know which manufacturing technology to use because there are several that can choose from.
This approach not only reduces initial investment but also enhances the overall flexibility and scalability of the thermoforming process, making it well-suited for low to mid-volume production runs.
Traditional plastic injection molding is renowned for its high-volume manufacture but entails significant upfront costs, primarily due to tooling expenses. Injection molds, usually crafted from steel or copper alloy, endure the intense pressures of the injection process, necessitating intricate and heavyweight designs, thereby escalating fabrication costs and lead times.
Take into account the size and weight of the parts you need to produce. Thermoforming is well-suited for forming large parts with minimal material thinning, making it ideal for applications requiring lightweight yet durable components. Low volume injection molding can also accommodate a range of part sizes but may be more suitable for smaller, more intricate parts.
The process is facilitated using digital milling machines. Fabricators can assure optimal process automation by employing a computer to control a milling machine with 3D files that have been uploaded. Moulds are not required to produce prototype CNC parts. As a result, it is affordable. CNC prototyping can be started with just a CAD rendering.
Thermoforming boasts several advantages that make it an attractive plastic manufacturing method for low- to mid-volume production:
The most widely utilised type of 3D printing for producing prototypes is FDM. Extrusion is used in this procedure to deposit polymer ingredients one layer at a time until the finished product is created.
Compare the tooling costs and lead times associated with each method. Low volume injection molding typically requires the fabrication of aluminum molds, which offer cost savings and shorter lead times compared to steel molds used in traditional injection molding. Thermoforming molds are also cost-effective and can be fabricated more swiftly due to their single-sided design and lightweight materials.
Whether you need 1,000 or 100,000 custom plastic components, the thermoforming experts at Advanced Plastiform Inc. will work with you to determine the best method of manufacturing to provide you with the durable, high-quality plastics you need. This includes prioritizing a low per-unit price with as quick a lead time as possible.
Consider the material requirements for your parts. Both low volume injection molding and thermoforming offer versatility in material selection, with a wide range of thermoplastic resins available. Evaluate factors such as material properties, performance requirements, and cost to determine the most suitable material for your application.
Vacuum forming involves suctioning out the air between the plastic sheet and the tool to ensure a snug fit, ideal for larger pieces with less intricate details. Conversely, pressure forming utilizes highly pressurized air to blast the plastic sheet while simultaneously applying vacuum suction, allowing for sharper angles and finer details, making it a compelling alternative to injection molding.
Low volume injection molding offers several distinct advantages that make it a preferred choice for small to medium-sized production runs:
Low volume injection molding finds application across a wide range of industries where precision, flexibility, and cost-effectiveness are paramount. Some of the key industries utilizing low volume injection molding include medical, telecommunications, consumer packaging, and more.
Advanced Plastiform offers guidance on the optimal manufacturing process to maximize efficiency and cost-effectiveness for low run, plastic parts.
A wide variety of materials, from transparent to opaque, are compatible with vacuum casting. Fabricators can also create up to 25 prototypes using the silicone mould that they already have. This procedure aids them, so that mass production and product development can happen concurrently.
Evaluate the complexity of the parts you need to manufacture. Low volume injection molding excels in producing parts with intricate details, tight tolerances, and complex geometries, making it suitable for applications requiring high precision. Thermoforming is better suited for larger parts with simpler geometries, although pressure forming techniques can achieve finer details compared to traditional vacuum forming.
GETTING A QUOTE WITH LK-MOULD IS FREE AND SIMPLE.
FIND MORE OF OUR SERVICES:
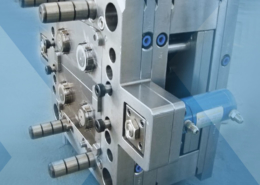
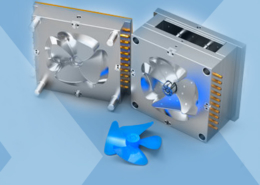
Plastic Molding

Rapid Prototyping
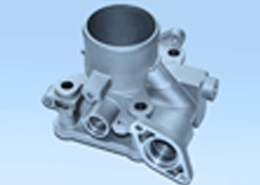
Pressure Die Casting
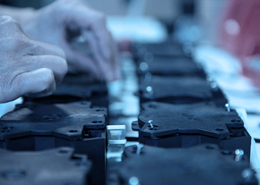
Parts Assembly
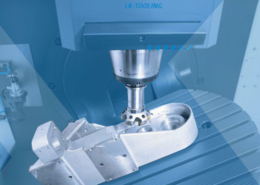