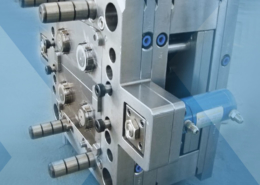
How is the process of manufacturing plastic pallets ... - pallet injection
Author:gly Date: 2024-10-15
This technology allows the production of small series with the right material. The applications of thermoplastic injection are very varied in the plastics industry and, in particular, cover the automotive, packaging, medical and electronics fields. In a field that requires many tests and certificates, such as the medical sector, a thermoplastic injection can satisfy the regulatory requirements and constraints. The parts produced are mechanically equivalent to series production. In addition, the thermoplastic injection manufacturing technique is used to produce parts that are very small, such as electronic components, or very large, such as car body parts.
Abstract: Roll-to-roll extrusion coated films were bonded onto polymer parts by back injection molding (BIM). The polypropylene (PP) coated polyethylene terephthalate (PET) films were pre-patterned with microstructured V-shaped grooves with 3.2 µm and 53 µm width, and other geometries. Bonding on PET and poly(methyl methacrylate) (PMMA) parts was facilitated by either higher tool or melt temperatures but was particularly enhanced by applying a mild oxygen plasma to the backside of the PET film prior to injection of the polymer melt. Silver wires from conductive nanoparticle ink were embedded into the PP coating during the BIM process by controlled collapse of the V-grooves. Thus, the feasibility of combining standard carrier film materials for printed flexible electronics and packaging into a non-flat polymer part was demonstrated, which could be a helpful step towards the fabrication of polymer parts with surface functionality. Keywords: printed flexible electronics; back injection molding; roll-to-roll extrusion coating; conductive nanoparticle ink; thermal bonding
A thermoplastic injection is intended for the production of small series from 100 to several thousand parts. A prototype mold is manufactured to be able to inject the plastic materials under high pressure.
ZIP-Document (ZIP, 362 KiB)
Thermoplastic injection by low-pressure vacuum casting is used for production exceeding one hundred parts. The robustness, mechanical properties, and industrialization information are very close to the injection-molded part.
Xie, S.; Werder, J.; Schift, H. Back Injection Molding of Sub-Micron Scale Structures on Roll-to-Roll Extrusion Coated Films. Polymers 2021, 13, 1410. https://doi.org/10.3390/polym13091410
Xie, S.; Werder, J.; Schift, H. Back Injection Molding of Sub-Micron Scale Structures on Roll-to-Roll Extrusion Coated Films. Polymers 2021, 13, 1410. https://doi.org/10.3390/polym13091410
This process also called “thermoplastic molding” or “thermoplastic injection molding”, involves injecting a molten polymer (thermoplastic material) into a mold under high pressure. The injection tools are manufactured according to a very specific process. The use of aluminum (instead of the commonly used steel) allows investment costs to be reduced because it can be machined more quickly. The cost of the mold depends on the number of cavities and the complexity of the shapes of the part to be molded. Once the mold has been manufactured, the plastic material is injected under high pressure using an injection molding machine.
Feature papers are submitted upon individual invitation or recommendation by the scientific editors and must receive positive feedback from the reviewers.
Xie, Sijia, Jerome Werder, and Helmut Schift. 2021. "Back Injection Molding of Sub-Micron Scale Structures on Roll-to-Roll Extrusion Coated Films" Polymers 13, no. 9: 1410. https://doi.org/10.3390/polym13091410
Xie S, Werder J, Schift H. Back Injection Molding of Sub-Micron Scale Structures on Roll-to-Roll Extrusion Coated Films. Polymers. 2021; 13(9):1410. https://doi.org/10.3390/polym13091410
Editor’s Choice articles are based on recommendations by the scientific editors of MDPI journals from around the world. Editors select a small number of articles recently published in the journal that they believe will be particularly interesting to readers, or important in the respective research area. The aim is to provide a snapshot of some of the most exciting work published in the various research areas of the journal.
All articles published by MDPI are made immediately available worldwide under an open access license. No special permission is required to reuse all or part of the article published by MDPI, including figures and tables. For articles published under an open access Creative Common CC BY license, any part of the article may be reused without permission provided that the original article is clearly cited. For more information, please refer to https://www.mdpi.com/openaccess.
The use of an aluminum mold (instead of the commonly used steel) allows the investment costs to be reduced. This rapid prototyping technology is more expensive but is the most effective, because it allows plastic prototype parts made of the “real material” to be obtained. The parts obtained are identical to series injection-molded parts. They can be marketed or used in transition production.
Feature papers represent the most advanced research with significant potential for high impact in the field. A Feature Paper should be a substantial original Article that involves several techniques or approaches, provides an outlook for future research directions and describes possible research applications.
Xie, Sijia, Jerome Werder, and Helmut Schift. 2021. "Back Injection Molding of Sub-Micron Scale Structures on Roll-to-Roll Extrusion Coated Films" Polymers 13, no. 9: 1410. https://doi.org/10.3390/polym13091410
Xie S, Werder J, Schift H. Back Injection Molding of Sub-Micron Scale Structures on Roll-to-Roll Extrusion Coated Films. Polymers. 2021; 13(9):1410. https://doi.org/10.3390/polym13091410
Thermoplastic injection with a prototype mold is the most expensive and slowest rapid prototyping technology. It is also the most efficient because it allows plastic prototype parts made of the “right material” to be obtained. The strength, mechanical properties, and industrialization information are identical to injection-molded series parts because the manufacturing process is the same. The parts can be marketed or used in transition production. The speed of production and unit costs are much more attractive than other technologies. The obstacle to this technology is the often considerable investment in the creation of a mold.
GETTING A QUOTE WITH LK-MOULD IS FREE AND SIMPLE.
FIND MORE OF OUR SERVICES:
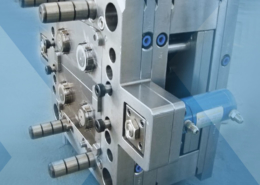
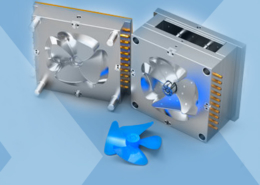
Plastic Molding

Rapid Prototyping
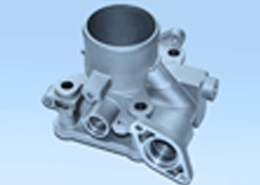
Pressure Die Casting
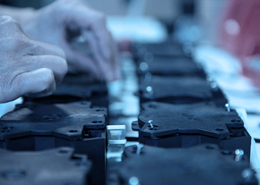
Parts Assembly
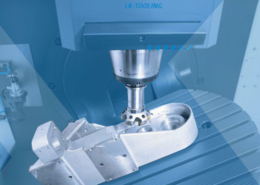