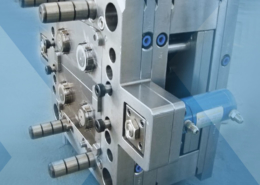
How is the longevity of plastic bucket moulds? - plastic bucket mould
Author:gly Date: 2024-10-15
When they think of plastics, most people have packaging products or caps in mind. Thermoplastics are used to produce these items. But the world of plastics offers more than just standard materials. WWith elastomer and thermoset injection moulding you can process silicone, rubber or polyester resins. ENGEL has the injection molding technology solutions for this in its portfolio.
As indicated above, injection molding is one of the most efficient and cost-effective ways of manufacturing parts that meet the strict specifications and standards of the medical and pharmaceutical industries. For example, the process is often used to manufacture the small, high-precision components found in diagnostic testing kits, such as the lateral flow in-vitro diagnostic test cartridge produced in large quantities by our team.
At The Sterling Healthcare Manufacturing, we understand the importance of quality in component manufacturing. By leveraging our extensive knowledge of the medical and pharmaceutical industries, we provide full-service, turnkey plastic injection molding solutions that fully comply with industry specifications and standards. For additional information about our plastic injection molding capabilities and how we serve the medical and pharmaceutical industries, contact us today.
To see an example of our work in the medical industry, check out this case study documenting how we optimized the mold design for a polystyrene diagnostic kit. You’ll also learn about how our custom capabilities — such as machine vision inspection — guarantee quality, cost efficiency, and 100% reliability for every order we complete.
Solid silicone rubbers (HTV) are high-temperature crosslinked and differ from liquid silicones in their molecular structure.
At Sterling Healthcare Manufacturing, we specialize in full-service, turnkey plastic component injection molding solutions. Our comprehensive part manufacturing capabilities allow customers to maintain oversight over the production of their parts, resulting in greater transparency and accountability. Additionally, we maintain ISO 9001:2015, our new ISO 13485 cleanroom certification and employ the use of FDA/medical-grade materials to ensure our injection molded components fully meet the strict specifications and standards of the medical and pharmaceutical industries.
Non-thermoplastic plastics include liquid silicone rubber (LSR), solid silicone (HTV), rubber, and bulk molding compound (BMC). These materials can be processed by injection molding if the machine is designed accordingly. They have one thing in common: temperature control in the machine works differently than in thermoplastic injection molding. The material is cooled in the barrel while the mold is heated. The machine design requirements are therefore different. ENGEL has the right solution for rubber injection molding with its elast machine series.
In thermoset injection molding, components with very high mechanical properties can be manufactured. In addition, thermosets are:
Rubber is used in sealing and engine technology. There are many different types, for example ethylene propylene diene monomer rubber (EPDM) or nitrile butadiene rubber (NBR). They are all processed in the same way.
Take advantage of our expertise, machines, and technologies. We will be happy to advise you on the design of your production cell.
Medical and pharmaceutical products play a vital role in the health and safety of patients. As such, ensuring the quality of each product and its individual components throughout the manufacturing process—from design to final inspection—is essential. For this reason, it is vital to partner with an experienced medical/pharmaceutical component manufacturer that emphasizes quality and offers complete part traceability from start to finish.
Advancements in material manufacturing techniques and technologies have led to the widespread use of plastics in modern manufacturing operations. In the medical and pharmaceutical industries, plastics are often used alongside the injection molding process to produce prototypes and full-production units of medical device and equipment components. As newer plastic materials and component designs are developed, injection molded plastics have increasingly contributed to lower infectious disease rates, better pain management, and lower medical costs.
ENGEL offers additional products such as universal injection compression and venting programs, wear-resistant plasticizing units, temperature-controlled nozzles, and corresponding peripheral equipment.
The injection molding process accommodates a wide range of plastic materials, making it well-suited to produce medical and pharmaceutical parts from whatever medical-grade plastic is required for the project. There are numerous plastics suitable for medical injection molding operations, each of which offers unique properties and performance characteristics. Common plastic material options for medical injection molding include:
As mentioned above, there are many types of plastics available for medical injection molding operations. Each plastic possesses distinct qualities that influence how it performs in specific applications. Some of the key factors to consider when choosing between the material options include:
Maximum output and highest precision - 32 infusion valves, slit during the processing, are produced on an all-electric e-mac 130.
Plastic injection molding is an efficient and cost-effective method of producing medical and pharmaceutical parts to high levels of precision, accuracy, and quality. It is used to create components from medical devices and equipment to laboratory tools and testing instruments. The following page provides an overview of the plastic injection molding process and its essential role in the medical and pharmaceutical industries.
Our injection molding machines can deal with the special properties of thermosets in injection molding. We offer wear-resistant and flexible systems for these challenging materials.
The production of 64 cavity umbrella valves made of liquid silicone with a part weight of just 0.06 g requires high precision and efficiency.
LSR (liquid silicone rubber) is processed using the LIM (liquid injection molding) method. The silicone is supplied as a homogeneous 2-component material. These two components are provided by special pumps.
Compared to other plastic manufacturing processes, plastic injection molding offers a number of clear advantages, especially when working with a knowledgeable and skilled injection molding partner. These benefits encompass the following:
Pellet-based molding compounds and wet polyesters (bulk molding compounds; BMC) are usually reinforced with various fillers. These are, for example, minerals, glass or even carbon fiber. This provides them with high mechanical properties .
Given the broad selection of suitable material options available, the first step in choosing a material for a project is narrowing down the list to the material family that fulfills the most part requirements (e.g., tensile strength, temperature load rate, etc.). From there, it is much easier to select the grade that best suits the project. Online databases—such as UL Prospector, MAT Web, and The British Plastics Federation—can provide information about materials that can further facilitate the selection process.
GETTING A QUOTE WITH LK-MOULD IS FREE AND SIMPLE.
FIND MORE OF OUR SERVICES:
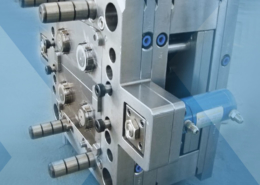
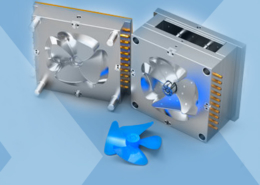
Plastic Molding

Rapid Prototyping
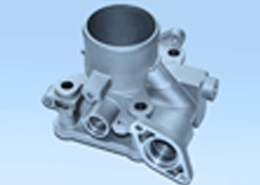
Pressure Die Casting
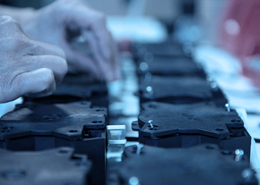
Parts Assembly
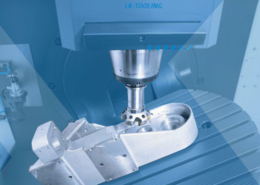