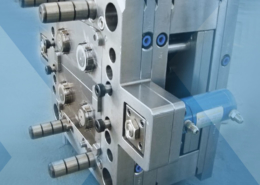
How a 2-shot Plastic Injection helps Molding Companies - 2 shot injection moldin
Author:gly Date: 2024-10-15
By allowing for early detection and resolution of design issues, injection molding prototypes can help avoid costly delays later in the production process. They also enable companies to test and validate their designs quickly, accelerating the development cycle.
Micro molding is a specialized branch of injection molding which results in extremely small, high precision parts. We have the capability of producing parts as small as 0.5g.
On top of that, injection molding allows for complex geometries and designs that other methods might struggle to replicate accurately. The raw material is injected into the mold under high pressure, which helps to fill any small or intricate features in the mold, resulting in parts that closely match the original design.
Moreover, injection molding is capable of producing complex and intricate designs that might be difficult or impossible to achieve with other prototyping methods. This includes features like undercuts, threads, and inserts, which can be incorporated directly into the mold design.
However, it’s important to note that while 3D printing is a powerful tool for prototyping, it may not always be the best choice for every project. Factors such as the complexity of the design, the required material properties, and the intended production volume should all be considered when choosing between 3D printing and traditional injection molding for prototyping.
There are numerous examples of successful products that started their journey as injection molding prototypes. Let’s look at a couple of case studies:
From an economic perspective, investing in an injection molding prototype can yield significant benefits. While there are upfront costs associated with creating the mold, these can be offset by the savings realized through early identification and resolution of design issues.
Product development is a complex process, often involving numerous iterations and extensive testing. An injection molding prototype can significantly streamline this process, providing a cost-effective way to test and refine designs before moving on to mass production.
The prototype injection molding process allows for the creation of a physical product that can be tested for functionality, durability, and user experience. This hands-on testing can reveal design flaws or areas for improvement that may not be apparent in a digital model. By identifying and addressing these issues early in the development process, companies can avoid costly redesigns and production delays.
When it comes to high precision and consistency, the injection molding prototype process stands out. The use of CAD models and CNC machining to create aluminum or steel molds means that each and every part produced is virtually identical. This consistency is crucial in industries like healthcare, aerospace, and automotive where a tiny variation can have big consequences.
The process involves using a 3D printer to create a mold from a CAD model. This mold can then be used in the injection molding process to create a plastic prototype. The advantage of this method is that it allows for quick iteration and testing of designs without the need for expensive tooling.
Injection molding offers unparalleled versatility in terms of the materials that can be used. Unlike 3D printing, which can typically only utilize a specific type of plastic or resin, injection molding can accommodate a wide array of materials. The most commonly used is a variety of thermoplastic polymers, which offer a range of properties to meet the requirements of different applications.
The process of making an injection molding prototype is a fascinating journey from a concept to a tangible product. It begins with a CAD model, which is a computer-aided design of the product. This model is then used to create a mold design, which is essentially a negative of the product. The mold is typically made from aluminum or steel, and it’s where the magic happens.
The prototypes produced through injection molding aren’t simply rough drafts of the final product—they mirror exactly how the final product will look and perform. This level of equivalency goes beyond physical properties; prototypes can also incorporate colors, textures, and finishes that the final product will feature.
This allows for rapid iteration and testing of designs. If a design flaw is identified in the prototype, the CAD model can be adjusted and a new mold created. This process can be repeated as many times as necessary until the design is perfected. This is particularly beneficial in the early stages of product development, where designs often undergo significant changes.
The feasibility of complex designs, the range of materials accessible, and the process’ inherent nature to refine an idea make prototype injection molding a powerful tool for innovation. Designers can experiment with new shapes, incorporate novel features, and trial unconventional materials. Mistakes here cost less and teach more compared to later production stages.
Making a plastic prototype is crucial for not only evaluating the idea, but also for demonstrating this concept to potential investors or stakeholders. An injection molding prototype helps to physically visualize the concept in 3D, communicate the idea more efficiently, and receive constructive feedback early in the game. Prototyping also allows ample room for design flexibility and iteration in injection molding prototyping, streamlining further design processes.
In the context of product development, prototyping plays an integral role. Specifically, creating a prototype injection molding machine model is a cost-efficient way of identifying and rectifying any design flaws at early stages. Imagine you’re working on a new product, perhaps a piece of custom consumer electronics or an innovative kitchen gadget for a wide range of materials. Before diving directly into mass production, you’d want to ensure the idea is practical and cost-effective.
Materials commonly used in injection molding include ABS, polycarbonate, nylon, and various types of polyethylene, each bringing its own set of properties to the table. ABS is known for its toughness and impact resistance, whereas polycarbonate is used for its excellent clarity and heat resistance.
Moreover, injection molding prototypes can be used to demonstrate the product to potential investors, stakeholders, or customers. This can be a powerful tool for gaining feedback, securing funding, or generating pre-launch buzz. By making a plastic prototype, companies can also gauge market interest and gather valuable user feedback before committing to full-scale production.
It’s hard to overstate the importance of this. When stakeholders can see and feel a prototype that matches the finished product quality, it greatly instills confidence in the product’s success. This advantage also extends to the product testing phase, as the findings from prototype tests can be directly applied to full-scale production.
One of the key advantages of using an injection molding prototype in product development is the flexibility it offers in terms of design and iteration. While the initial creation of the mold requires a certain investment of time and resources, once it’s made, it can be used to produce multiple copies of the part quickly and efficiently.
When it comes to rapid prototyping, both 3D printing and injection molding have their unique advantages. 3D printing, often associated with plastic prototype manufacturing, allows for quick turnarounds and is especially useful for low-volume production. It’s a go-to for many who wonder how to get a plastic prototype made in a short period of time. The process is direct: from a CAD model to a physical product without the need for molds.
On the other hand, injection molding, while initially more time-consuming due to the mold-making process, becomes highly efficient for larger production runs. The prototype injection molding machine can produce multiple copies of a part in a relatively short period of time once the mold is created.
Medbio capabilities include insert molding with small inserts with very little material. Insert molding is a process in which plastic is injected into a mold that contains an pre-placed insert. The result of insert molding is a single molded plastic piece with an insert surrounded by the plastic. Inserts can be made of metals or different types of plastic.
Furthermore, once the mold is created, parts can be produced at a high rate, making it possible to move from prototyping to mass production in a relatively short period of time. This can give companies a competitive advantage, allowing them to get their products to market faster than their competitors.
From understanding the concept to exploring its economic benefits, it’s clear that injection molding prototyping is a powerful tool in product development. It offers high precision, material versatility, design flexibility, and production equivalency, all while reducing time-to-market. With sustainability considerations and future trends in mind, the injection molding prototype process is set to continue playing a pivotal role in bringing innovative, successful products to market.
The journey of how to make a plastic mold prototype starts with feeding raw material, usually thermoplastic polymers, into a machine. This material is heated until malleable, then injected into a mold cavity designed according to the CAD model. The material cools and solidifies, adopting the shape of the mold to give a plastic prototype reflecting the shape and dimensions of the intended final product. This plastic prototype manufacturing process enables fabricators to optimally design and make adjustments before proceeding to full-scale production, thereby saving time, reducing tooling costs, and enhancing the product’s quality.
Furthermore, having a physical prototype can help secure funding from investors or pre-orders from customers, providing an early source of revenue. It also reduces time-to-market, allowing companies to start selling their products sooner.
In context, that’s how to make a plastic mold prototype with a high degree of precision, offering the advantage of producing more complex and accurate prototypes in comparison to other methods. This precision, coupled with relatively high output rates once molds are created, makes injection molding prototyping a viable choice for projects with detailed requirements and high volume needs.
Medbio is dedicated to using the latest technology to drive manufacturing costs down while ensuring customer satisfaction.
When it comes to reliable and high-quality injection molding prototyping, FOWmould stands out. With a proven track record, the extensive network of partners, and commitment to innovation, FOWmould is the go-to choice for businesses seeking to streamline their product development process and bring successful products to market.
The industry is continuously exploring new methods, materials, and technologies to reduce the environmental impact, including researching biodegradable plastics and developing more efficient machines.
Our mission is to reduce overall part to part variation by implementing rigorous mold tryouts, along with IQ/OQ/PQ during the launch phase of a product and establishing a robust process that meets the customer’s specification. We are driven by technology and through the use of OPC UA, we are able to drive off one centralized controller monitoring various pieces of auxiliary equipment.
In today’s fast-paced market, speed is of the essence. Companies are under constant pressure to develop and launch new products as quickly as possible. Prototype injection molding can play a crucial role in reducing time-to-market.
These case studies highlight the versatility and effectiveness of injection molding prototypes in product development across a range of industries.
The resulting cast from the injection molding process can then be further treated or modified as necessary, for example through painting, metallization, or the application of other surface treatments. This flexibility in material choice and post-processing allows for a great deal of customization and optimization, enabling the production of prototypes that closely mimic the final product’s functionality and aesthetics.
In terms of trends, we can expect to see even greater synergy between prototyping methods as the lines between processes like injection molding and 3D printing become ever more blurred. Despite what the future holds, one thing is clear: injection molding prototypes will continue to play an essential role in product design and development.
3D printing has revolutionized the world of prototyping, offering a rapid and cost-efficient way to create physical models from digital designs. In the context of injection molding, 3D printing can be used to create prototype molds, thereby speeding up the prototyping process and reducing costs.
Prototyping, including injection molding prototype creation, is an exciting phase in the product development process. It’s where the rubber meets the road – concepts turn into physical objects, ideas turn into reality. This space is ripe for creativity and innovation.
In addition, the cost per unit of an injection molded part decreases with volume, making it a cost-efficient way for mass production. This is particularly beneficial for companies planning to produce a high volume of products. The prototype mold making process also allows for the use of a wide range of materials, including less expensive plastics, further contributing to cost savings.
Conceptually, an injection molding prototype serves as a critical step in the product development cycle. It’s a powerful tool for creating a physical product from a CAD model that mirrors the design and functionality of the final product. Building an injection molding prototype leverages the plastic mold prototype making process, incorporating a wide range of materials which aid in determining the viability of the design and its potential for mass production.
With the use of cavity pressure sensors, scientific molding practices, and state of the art equipment we are able to manufacture lower cost medical/biotech products in our ISO Class 8 and Class 7 cleanrooms. We have over 100 molding machines ranging from 17 ton to 440 ton with variable shot sizes to make any project possible.
Both methods have their place in the prototyping process. 3D printing is excellent for initial prototypes and design iteration, while injection molding is often the preferred choice for later-stage prototyping and final product manufacturing.
ACIS®, Autodesk Inventor®, CATIA® V5,Creo™ Parametric, IGES, Parasolid®, Pro/ENGINEER®,Siemens PLM Software’s NX™, SolidEdge®, SolidWorks®, STEP
Privacy Policy — Terms of Use — Purchase Order Terms & Conditions — Copyright © 2024 Medbiollc.com, All Rights ReservedWeb design and digital marketing by Valorous Circle LLC
As we forge ahead into the future, the process of making an injection molding prototype will continue to evolve. New materials with enhanced properties, such as biodegradable plastics and composites, are expected to emerge. Technologies like AI and machine learning are anticipated to make the process more efficient and accurate.
Sustainability is an increasingly important factor in manufacturing practices, and injection molding prototyping isn’t exempt from these considerations. When it comes to environmental impact, different stages of the prototype injection molding process have various factors to consider.
This process is not only a cost-effective way to create prototypes but also a powerful tool for testing and refining designs. It allows for a short period of time to make adjustments and improvements before moving on to mass production. And with the use of injection, even complex shapes with undercuts can be achieved, offering a competitive advantage in various industries.
Once the mold is ready, it’s placed in the injection molding machine. Raw material, usually plastic, is fed into the machine, where it’s heated until it becomes liquid. This molten plastic is then injected into the mold under high pressure. As the plastic cools, it solidifies and takes the shape of the mold. The resulting cast is a plastic prototype, a physical representation of the product that can be tested for functionality and design.
The system is designed to iterate, innovate, and improve. By making a plastic prototype, we learn, adapt, and get better, not just in the context of a single product, but evolving the broader understanding of manufacturing capabilities and constraints.
Perhaps one of the most compelling advantages of injection molding prototypes is the seamless transition they provide from the prototype stage to full-scale production. The prototype plastic injection molding process uses the same materials, machinery, and tooling as the final production stage, which is an immense advantage when you’re aiming for production equivalency.
GETTING A QUOTE WITH LK-MOULD IS FREE AND SIMPLE.
FIND MORE OF OUR SERVICES:
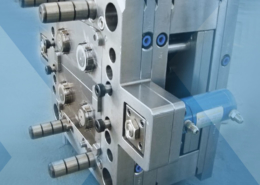
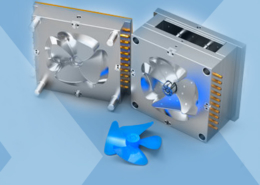
Plastic Molding

Rapid Prototyping
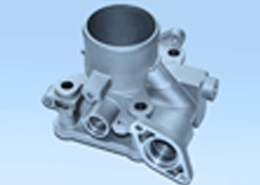
Pressure Die Casting
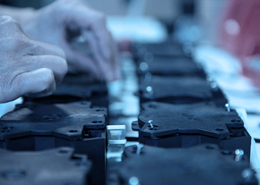
Parts Assembly
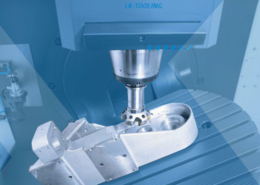