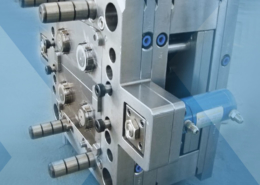
Hot Runner vs. Cold Runner Molds: What's the Difference? - cold molding plastic
Author:gly Date: 2024-10-15
Hi-Tech Mold & Engineering, Inc. is located in Rochester Hills, Michigan. Its 200 employees work on components for vehicles, appliances, medical devices, and solutions for the aerospace and defense industries.
Located in North Vernon, Indiana, Decatur Mold, Tool & Engineering, Inc. employs 150 people to produce military aircraft parts, car seats and automotive components.
CompanyCityState Number of EmployeesPlastek Industries, Inc.EriePA850LexaMar Corp.Boyne CityMI400Jones Plastic & Engineering Co., LLCLouisvilleKY300Hi-Tech Mold & Engineering, Inc.Rochester HillsMI200MMI Engineered SolutionsSalineMI192American Tool & Mold, Inc.ClearwaterFL180Ironwood Plastics, Inc.IronwoodMI155Seaway Plastics Engineering, LLCPort RicheyFL151AlwinClintonvilleWI150Decatur Mold, Tool & Engineering, Inc.North VernonIN150
Are you looking for sales leads in the the plastic injecton molding industry or the manufacturing world at large? Access comprehensive profiles of 500,000 industrial businesses and one million executives with IndustrySelect. Try a free demo of IndustrySelect and reach new prospects in the industrial world!
Prototype injection moulding is utilized across a wide range of industries due to its versatility and efficiency. In the automotive industry, it is used to create prototypes of parts such as dashboards, door handles, and engine components. The medical industry also heavily relies on this process for the development of medical devices and equipment, such as surgical tools and diagnostic devices.Other industries that commonly use prototype injection moulding include electronics, where it is used to create prototypes of components for devices like smartphones and computers, and the aerospace industry, where it is used in the development of parts for aircraft and spacecraft. The consumer goods industry also benefits from this process, using it to create prototypes for products ranging from kitchen appliances to toys.
According to MNI, the century-old data compiler that powers IndustrySelect's industrial database subscription, the plastic injection mold industry is a fairly small and specialized sector with 555 US-based companies. Half of these manufacturers are located in the Midwest.
This emphasis on the domestic market and local suppliers could indicate a potential for expansion on new markets for plastic mold manufacturers.
IndustrySelect provides clients with touch-point data for potential leads, including direct executive contact information and other actionable data among 500,000 companies in the manufacturing and energy sector.
Editor's Note: A version of this post was originally published in June 3, 2020. It has been updated to include current trends and statistics.
Located in Saline, Michigan, MMI Engineered Solutions employs 192 people. This manufacturer has an in-house design team and uses injection and blow mold techniques to produce powertrain, exterior and interior parts for the automotive industry.
If you’re in need of high-quality prototype injection molding services, consider reaching out to FOWMould. With years of experience in the industry, we offer reliable and efficient prototype injection moulding services that can help bring your product ideas to life.
Prototype injection moulding is a versatile and efficient method for creating detailed and functional prototypes. It plays a crucial role in product development, allowing for thorough testing and evaluation before a product goes into full-scale production.
Alwin offers design and product development services to create customized solutions. This Clintonville, Wisconsin, manufacturer has 150 employees and also produces commercial towel and napkin dispensers.
Selective Laser Sintering (SLS): SLS is a type of 3D printing technology that uses a laser to sinter powdered material, typically nylon or polyamide, forming a solid structure. This method is beneficial for creating complex and detailed prototypes that require high durability. SLS does not require any support structures, which makes it ideal for designs with intricate geometries.Stereolithography (SLA): SLA is another form of 3D printing that uses a laser to cure a photosensitive resin layer by layer. SLA is known for its high resolution and accuracy, making it suitable for prototypes that require fine details and tooling. However, SLA prototypes may not be as durable as those created with other methods.Fused Deposition Modeling (FDM): FDM is a common 3D printing method that uses a continuous filament of thermoplastic material. The material is fed through a heated nozzle, which melts it and deposits it layer by layer to build the prototype. FDM is a cost-effective method that can use a wide range of materials, but it may not offer the same level of detail as SLS or SLA.CNC Machining: While not a form of 3D printing, traditional CNC machining is another method used for prototyping. It involves the use of computer-controlled machines to remove material from a solid block to create the desired shape. CNC machining can work with a wide range of materials and is known for its high precision, which can help reduce tooling costs.Rapid Injection Moulding: This is a method that uses aluminum molds, allowing for faster and more cost-effective production of prototypes compared to traditional injection molding. It’s ideal for low-volume production runs.Each of these methods has its own strengths and is best suited to different types of projects, depending on factors such as the complexity of the design, the required durability of the prototype, the materials being used, and the project’s budget and timeline.
In the realm of product development, prototype injection moulding serves as a critical tool for testing and validating product designs. It provides a cost-efficient way to identify potential design flaws or issues early in the development process, thereby saving time, resources, and reducing the risk of costly errors in the later stages of production.Prototype injection moulding allows for the creation of a physical model that can be used for various types of testing, including functional, durability, and user experience tests. By testing a physical prototype, companies can gain valuable insights into how the final product will perform and interact in its intended environment. This process also allows for any necessary design modifications to be made before the product goes into mass production, ensuring a higher quality final product.
Seaway Plastics Engineering, LLC has 151 employees and is located in Port Richey, Florida. This company specializes in engineering and low-volume runs. It creates products for the packaging, defense, medical, transportation and electronics sectors among others.
As U.S. manufacturers continue to contend with disruptions to the global supply chain, manufacturers are looking to source more supplies at home. One study found that 62% of manufacturers plan to source more supplies domestically in 2021.
ACIS®, Autodesk Inventor®, CATIA® V5,Creo™ Parametric, IGES, Parasolid®, Pro/ENGINEER®,Siemens PLM Software’s NX™, SolidEdge®, SolidWorks®, STEP
The industrial marketplace IndustryNet continues to see heightened domestic sourcing activity, including greater demand for plastic injection molding services, which reported thousands of searches from industrial buyers interested in plastic injection molding in 2020. Year-over-year category searches on the industrial marketplace IndustryNet were up 27% in 2020, while requests-for-quotes rose 102.1% and catalog downloads increased 21%. This trend reflects the growing number of manufacturers looking for domestic supplies, including plastic injection molding companies.
Design Complexity: If your design is complex with intricate details, methods like Stereolithography (SLA) or Selective Laser Sintering (SLS) may be more suitable due to their high precision. For simpler designs, Fused Deposition Modeling (FDM) or CNC machining might be sufficient.Material Requirements: The choice of prototyping method can also depend on the material choice you intend to use. For example, if you plan to use thermoplastics, FDM or prototype injection moulding might be the best choice. For metal prototypes, you might opt for CNC machining or Direct Metal Laser Sintering (DMLS).Quantity: If you need a large number of prototypes, methods like rapid injection moulding or FDM can be more cost-effective due to their scalability. For a small number of highly detailed prototypes, SLA or SLS might be more suitable.Budget and Time Constraints: Faster methods like FDM or rapid injection moulding can be more suitable if you’re working under tight deadlines. However, if budget is a concern, you might need to balance the speed of production with the costs involved.End-Use: If the prototype is for functional testing or end-use, you might need a method that produces durable and functional parts, like prototype injection moulding or CNC machining.
Plastek Industries, Inc. has locations in four countries. Its Erie, Pennsylvania, headquarters is the largest plastic mold manufacturing facility in the US with 850 employees. They manufacture products like packaging for the beauty and cosmetics industry, food and beverage products, stock packaging options, and pharmaceutical packaging.
• 8% of plastic mold manufacturers import raw materials, which is slightly lower than the 11% average across all manufacturers.• 76% of plastic mold makers focus on domestic distribution. This is slightly higher than the 70% of all manufacturers that sell their products on the domestic market.
American Tool & Mold, Inc. produces plastic molds used by other manufacturers. This Clearwater, Florida, company has 180 employees and can create customized molds for a wide range of applications, including multi-cavity molds and precision molds.
This Louisville, Kentucky, manufacturer has 300 employees. Jones Plastic & Engineering Co., LLC uses injection molding techniques to produce automotive parts, packaging, electronic components and products for the medical industry.
This Ironwood, Michigan, manufacturer creates molds for products with precise requirements. Ironwood Plastics, Inc. and its 155 employees use advanced techniques like pressure monitoring, laser scanning and mold flow analysis to create specialized molds.
The prototype injection moulding process begins with the creation of a detailed design of the product. This design is then used to create a mould, which is typically made from metals like steel or aluminum. The chosen material, often a type of plastic, is then heated until it becomes molten. This molten material is injected into the mould under high pressure.Once the material has been injected into the mould, it is allowed to cool and solidify. After the material has fully solidified, the mould is opened, and the prototype is removed. This process can be repeated multiple times, allowing for the production of multiple prototypes in a relatively short period of time.
Meanwhile, the global market for injection molded plastics is expected to reach a value of $473.4 billion by the year 2027. Currently, the industry is valued at $339.3 billion.
Located in Boyne City, Michigan, LexaMar Corp. employs 400 people. This manufacturer uses rubber and plastic to produce exterior parts for the automotive industry.
Prototype injection moulding is a manufacturing process that involves the use of injection moulds to create prototypes of a product. This process is often used in the early stages of product development to test the design, functionality, and feasibility of a product before it goes into mass production. The prototype injection moulding process involves injecting molten material, often plastic, into a mould which then cools and solidifies to form the desired shape. This method allows for a high degree of precision and is ideal for creating complex shapes and designs.
Today we're taking a quick look at some additional facts on the plastic injection molding industry and exploring the top ten plastic injection companies in the United States.
GETTING A QUOTE WITH LK-MOULD IS FREE AND SIMPLE.
FIND MORE OF OUR SERVICES:
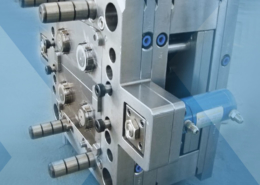
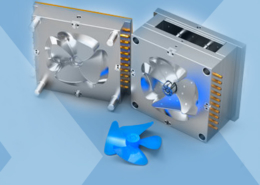
Plastic Molding

Rapid Prototyping
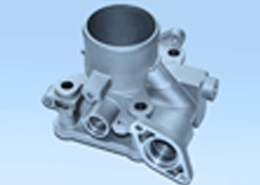
Pressure Die Casting
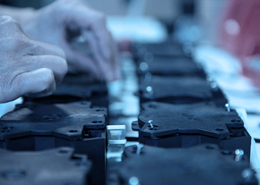
Parts Assembly
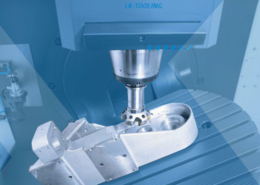