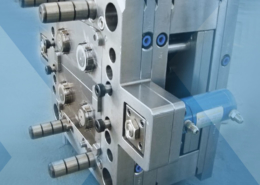
High-Volume Production and Injection Molding - high volume injection molding
Author:gly Date: 2024-10-15
4. The sprue of a three-plate mold should ideally be designed for automatic demolding. Special attention should be paid to ensure the reliable demolding action of the soft plastic sprue.
Backed by in-house 3D CAD and industrial design proficiency, our custom prototyping services can accommodate differing levels of concept maturity. Whether you have full CAD files, a few sketches, or need help getting the idea on paper (then into a computerised format), we can convert your assets into production-ready files for plastic and metal component manufacturing.
5. Choosing the right material is vital. Consider factors like the material’s adhesiveness, potential deformation during injection, and risks associated with melting.
Dual-color and multi-color injection molding has become a focal point in the evolution of injection molding technology, and its benefits are manifold. Various techniques allow for different hardness and resilience within the same component. Soft plastics like TPE offer diverse color options, transparent surfaces, and other appealing features, enhancing aesthetic design. This method eliminates assembly steps, shortens the molding cycle, reduces processing costs, and offers added value to the end-users in terms of design, quality, and functionality.
Taking TPE overmolding as an example, given the high cost of TPE material, designers must consider cost reduction during product design by using a thinner TPE wall. The tactile feel of TPE is directly related to its wall thickness and hardness. When the TPE thickness is less than 1.5mm, the softness or hardness is primarily influenced by the hardness of the underlying hard plastic. Reducing the thickness of TPE can severely affect its bonding strength with the hard plastic, mainly because an overly thin TPE cools too quickly in the mold, leading to reduced adhesion strength.
Additionally, prototyping can help to communicate design concepts to stakeholders, such as investors, clients, or team members. It can also help to generate excitement and interest in a product, which can be important for marketing and fundraising efforts.
2. It’s imperative to ensure that after the back mold rotates around its center, it aligns perfectly with the front mold. This aspect requires careful attention during design.
Want to set the highest standard from prototype to mass production? Send us some details of your prototyping project or arrange a one-on-one with an expert today.
The seal position refers to the junction or boundary between hard and soft plastics. A good design avoids a “feathered” appearance (i.e., the seal position shouldn’t gradually thin out), as overly thin edges can lead to poor adhesion and warping. Ideally, the design at the seal position should have a distinct step or recess to ensure consistent wall thickness. In some products, especially those with long flow paths or areas prone to wear, mechanical connections can be designed between the soft and hard plastics, ensuring a strong bond between the two materials.
Ready to step into the next dimension of plastic prototyping? Get in touch or book a meeting with our team to discuss your project.
Products made using multi-color injection molding have a significantly different structure compared to regular plastic products. When designing the structure and shape of these products, it’s essential to consider their intended use and purpose. It’s crucial to delve deep into the structural design of the injection-molded product, taking into account the compatibility features of the various materials used. Typically, the design aims to increase the contact area of the raw materials to enhance solidity. This can be achieved by incorporating numerous small recesses and protrusions within the product, which serve to increase the material’s contact area, thereby improving the product’s strength, lifespan, and practicality.
Prototyping is important because it helps to identify potential issues in a product or service early in the development process. This can save time and money by allowing design flaws to be corrected before a final product is produced.
In the design of multi-color/multi-material injection molded products, two primary methods are used to join adjacent components:
As products became more intricate, the demand for tri-color and even quad-color molding began to rise. Generally, there are two types of tri-color machines: the two-station tri-color machine (colloquially known as the “pseudo tri-color”) and the three-station tri-color machine (known as the “true tri-color”). The distinction between the two isn’t about authenticity but rather the product structure design and the turntable control method adopted.
Dual-color molds typically consist of two parts. One half is fixed on the stationary platen of the dual-color injection molding machine, which is the side with the injection gate. The other half is mounted on the rotating platen, which is the side from which the mold ejects. Both molds’ rear cavities are usually identical, while the front ones differ. After the first material is injected into the first mold, the machine’s stationary and moving molds open. The rotating platen, carrying the rear parts of both molds, rotates 180 degrees. At this point, the semi-finished product from the first mold isn’t ejected. Instead, the molds close again, and the second material is injected. After cooling, the molds open, and the finished product from the first mold’s moving mold is ejected. This cycle produces one semi-finished and one finished product each time.
10. In 99% of cases, the hard plastic part of the product is molded first, followed by the soft plastic part, primarily because soft plastic is more prone to deformation.
Nave ISK-8, Parque Industrial y Logístico Sky Plus, Avenida Mineral de Cinco Señores No.100, del Parque Industrial Santa Fe, Silao de la Victoria, Guanajuato, México
Add agility to your prototyping with this exciting additive manufacturing technology. Our advanced 3D printing services make ideas materialise before your eyes, efficiently and cost-effectively. In expert hands, 3D printers are ideal for producing NPI (new product information) models for products comprising plastic components, quickly delivering a prototype you can present, test, and refine.
Multi-shot injection molding, also known as multi-color injection molding, refers to the process where two or more colors or different materials are molded using a mold with one or more channels. Historically, dual-color injection molding was the pioneer in this field. A common example many of us interact with daily is the toothbrush. The handle of most toothbrushes is produced using dual-color injection molding, typically combining PP (hard plastic) with TPE (soft plastic). TPE is chosen because of its excellent compatibility with PP, and the soft plastic overlay enhances the grip.
Need physical proof of your latest and greatest invention? Something you can present to management, a client, potential investors, or even just show off to your friends? Our rapid prototyping services can help. Drawing on our 3D printing capabilities, our efficient experts deliver punctual prototypes to your specifications.
3. Before designing the mold, it’s crucial to understand the parameters of the multi-color injection molding machine intended for mass production. This includes data like maximum/minimum mold capacity, mold thickness, and the distance between ejector pins.
When only the highest-grade plastic prototype will do, or multiple prototypes are required for distribution to various stakeholders, it can be worth making a custom injection mould. Achieve near-perfect precision and repeatability with the most professional plastic prototyping method available.
Establishing a prototype can be critical to your manufacturing project and demands speed and precision in equal measure. With comprehensive capabilities across plastic and metal component manufacturing, weâll swiftly lay down building blocks for your success while ensuring quality control.
Get an injection mould worth its weight (without the wait). Send us a message or lock in a meeting with a CNC prototyping professional.
Multi-shot injection molding requires a high level of process and plant resources. This plastic-making method has changed how we design and make products, making them look and work better. As industries continue to seek innovative solutions, Prototool emerges as a leader in the field, specializing in plastic products and parts manufacturing using the two-shot injection molding process and multi-shot techniques. With a commitment to precision, quality, and cutting-edge technology, Prototool is not just a manufacturer but a partner for businesses aiming for excellence. As we navigate the future of plastic manufacturing, aligning with pioneers like Prototool ensures a journey marked by innovation, efficiency, and unparalleled expertise.
11. To achieve tighter bonding between materials, consider the “stickiness” between materials and the roughness of the mold surface.
8. It’s essential to consider whether the flow of plastic during the second injection might disturb the already molded product from the first injection, causing deformation. If this is a possibility, remedial measures should be taken.
6. When designing the cavity for the second injection, some voids can be incorporated to prevent the newly formed product from being scratched or scraped by the mold. However, it’s crucial to carefully assess the strength of each sealing position to ensure that no flash occurs due to high injection pressures.
With the development of the injection molding industry, innovative techniques have emerged, pushing the boundaries of what’s possible in manufacturing. One such groundbreaking method is multi-shot injection molding. At Prototool, we’ve harnessed this advanced process, allowing for the creation of intricate and multi-material components in a single cycle. This offers unparalleled precision and design flexibility. In this article, we’ll delve into the nuances of this technique, shedding light on its benefits, design considerations, and its transformative potential in the realm of injection molding.
The steps involved in prototyping may vary depending on the product or service being developed, but generally include the following:
Ready for a rapid assembly of your prototype that will progress your project to the next phase? Send us a message, give us a call, or arrange a time for an obligation-free consultation with an expert.
Adding a textured finish to the surface of TPE products can give a leather-like feel, enhancing tactile sensation and masking surface imperfections. Some textures can also adjust the surface hardness of TPE products, making them softer or harder than when made with a smooth TPE surface. If designers polish the TPE surface to a mirror finish, it may exhibit many flow lines and color streaks, or it may turn white during use, degrading the surface quality.
7. The product from the first injection can be slightly oversized. This ensures a tighter fit during the second molding, achieving a better sealing effect.
We offer constructive feedback and innovative inputs because we think your prototype deserves no less! Our experience has gifted us unique insights into what works (and what doesnât) in modern manufacturing, and we readily share these with you, while recognising your right to make the final call.
12. Provisions for venting during the first, second, or subsequent injections need to be thought out in advance to prevent defects and ensure quality.
Manage the demands of prototypes with metal parts with our prompt and precise CNC machining. Expertly automated to turn out metal components for instant assembly, or in combination with additional plastic parts as per your prototypeâs requirements.
It’s important to note that prototyping is an iterative process, and multiple rounds of testing and revisions may be necessary before a final product is produced.
GETTING A QUOTE WITH LK-MOULD IS FREE AND SIMPLE.
FIND MORE OF OUR SERVICES:
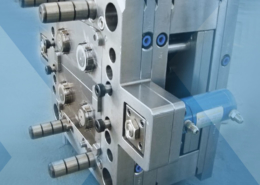
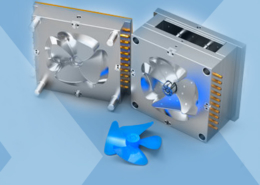
Plastic Molding

Rapid Prototyping
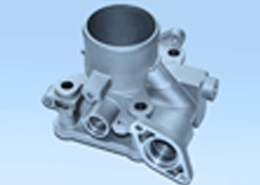
Pressure Die Casting
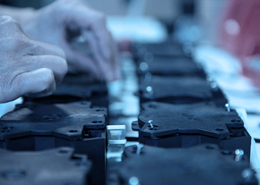
Parts Assembly
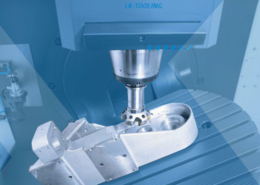