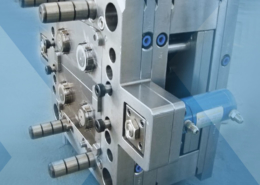
High-precision injection molding - automotive plastic injection molding
Author:gly Date: 2024-10-15
The curing phase is a critical step in the PTFE manufacturing process, as it ensures the optimal performance of both the raw material and finished parts. Effective curing of PTFE, which has a heat-sensitive range of fillers, necessitates a combination of time, experienced personnel, and high-quality curing ovens.
PTFE's unique combination of properties makes it a versatile material for various applications, including coatings, films, membranes, and engineering components, particularly in harsh environments where chemical resistance and low friction are essential.
Parkside Industries offers a wide range of precision molding capabilities and production services for a diverse group of industries. Learn more today.
Our products are offered in a diverse range of material combinations to cater to specific application requirements, ensuring superior sealing performance that surpasses current industry standards. Optimizing compression packing performance can be a complex process, and Parkside's team of experts is available to provide input and design assistance to address specific challenges.
Our proprietary interfering angle design features self-adjusting capabilities, enabling it to respond to minor pressure fluctuations and ensuring reliable sealing. In multi-ring packing sets, each lip provides independent sealing, further enhancing overall performance. We offer high-performance packing sets suitable for various applications, including food-grade seals and extremely high-pressure environments.
First Name *Email Address *Phone NumberMessage0 / 180Upload project filesDrag and Drop (or) Choose FilesRequest a QuotePlease do not fill in this field. Please do not fill in this field.
Extensive testing and years of high-quality service have demonstrated the superiority of Parkside's PTFE V-rings over conventional packings.
Parkside's V-rings are suitable for use in valves, pumps, and low-speed rotary services, operating in temperatures ranging from -120°F to 500°F, with an extremely low coefficient of friction. The finished Parkside PTFE rings exhibit the same chemical and solvent resistance for which PTFE is renowned. The Parkside V-ring design ensures maximum lip flare under gland pressure, enabling effective gland take-up and compensating for lip wear. Followers are designed to function as additional sealing rings, which is particularly important when packings must be installed in shallow stuffing boxes.
Valve stem compression packing plays a vital role in ensuring optimal valve performance, as it directly impacts process efficiency, safety, and regulatory compliance by minimizing or eliminating process leakage. Parkside's compression packing solutions undergo rigorous testing to guarantee effective sealing in various applications, including valves, pumps, agitators, and other rotary equipment.
A typical packing set comprises one "M"-ring, one "F"-ring, and a variable number of "V"-rings, depending on the application. These components can be fabricated via machining from bar-stock or "net" compression molding. Machining yields parts with tighter tolerances but incurs higher costs due to lathe turnings and chucking requirements. In contrast, "net" molding minimizes waste but may result in slightly wider tolerances and occasional out-of-round rings, which are often mitigated by PTFE's inherent flexibility.
Our V-rings are available in a wide range of materials and sizes, making them ideal for use in chemical processing, food service, and high-speed applications. By leveraging our expertise and innovative designs, we can provide customized packing solutions that exceed customer expectations and meet the most demanding application requirements.
The fundamental sealing mechanism occurs when pressure is applied to the packing set, causing the "V"-ring lips to flare against the stuffing box and shaft due to interfering internal angles. Unfilled PTFE V-ring packing sets exhibit excellent performance in both static and dynamic applications (including linear and rotary motion). A significant advantage of PTFE is its ability to be blended with various fillers, altering its physical properties.
First Name *Email Address *Phone NumberMessage0 / 180Upload project filesDrag and Drop (or) Choose FilesRequest a QuotePlease do not fill in this field.
Polytetrafluoroethylene (PTFE) is a synthetic fluoropolymer material composed of carbon and fluorine atoms, with the chemical formula (C₂F₄)n. PTFE is a thermoplastic polymer characterized by a high molecular weight, typically ranging from 10^5 to 10^7 g/mol.
Automatic compression molding is a significant aspect of our operations at Parkside Industries, enabling us to optimize PTFE material usage and reduce material costs for high-volume production runs. This manufacturing technique offers a more economical production alternative for our clients, while ensuring consistent quality and performance.
The working temperature range of -100°F to +500°F accommodates most applications, and PTFE's chemical resistance is well-documented. V-rings, also referred to as "packings," "chevron packings," "parachute packings," or "packing sets," can be fabricated from various elastomers, including PTFE with numerous fillers. They primarily serve as seals in pumps and valves, preventing leakage of the material being transported. PTFE's chemical resistance and low coefficient of friction make it an ideal material for these applications.
We handle all design and die work in-house, eliminating the need for customers to incur tooling costs when production quantities are sufficient. By maintaining control over the entire manufacturing process, we can guarantee the highest level of precision, quality, and reliability in our finished products.
PLA is a thermoplastic polyester produced using annually renewable biomass like maize, sugar beet, or sugarcane. Depending on the geographical area of production, the resources used may be certified GMO free.
PTFE's molecular structure consists of a carbon backbone fully fluorinated with fluorine atoms, resulting in a highly stable and inert material. The strong carbon-fluorine bonds (C-F) confer exceptional properties, including:
The required curing temperatures and time frames for all PTFE products are meticulously monitored and controlled by our knowledgeable oven operators, who oversee the entire process. Our conventional and custom-built ovens are among the finest in the industry, featuring cam-operated mechanisms, 7-day timers, and precise temperature control for every oven load.
Packing sets have been a stalwart component in hydraulic and pneumatic systems for many years, finding widespread application in cylinders, motors, pumps, and valves. The US Military standardized the internal geometry, diameters, and heights of these sets, designating them as A/N 6225 V-ring packing sets. Initially, leather was the material of choice, but the advent of plastic rings, specifically polytetrafluoroethylene (PTFE), enabled variations in shape and dimensions, yielding enhanced performance.
GETTING A QUOTE WITH LK-MOULD IS FREE AND SIMPLE.
FIND MORE OF OUR SERVICES:
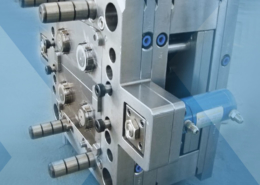
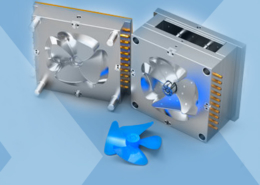
Plastic Molding

Rapid Prototyping
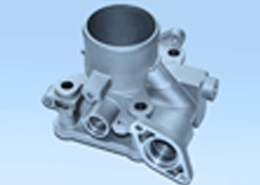
Pressure Die Casting
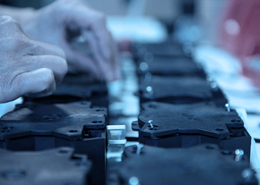
Parts Assembly
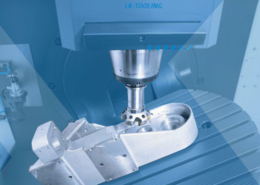