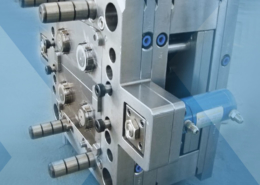
Exploring the World of Plastic Molded Products: Innovation and Versatility
Author:gly Date: 2024-06-08
Plastic molded products have become ubiquitous in our daily lives, revolutionizing industries and offering innovative solutions to a myriad of challenges. From household items to complex engineering components, the versatility and durability of plastic molded products have reshaped modern manufacturing. This article delves into the realm of plastic molded products, uncovering their significance, applications, manufacturing processes, and future prospects.
Introduction: Unveiling the Fascination
The world of plastic molded products captivates both engineers and consumers alike with its endless possibilities and transformative capabilities. As we navigate through our surroundings, we encounter an array of plastic molded products that seamlessly integrate into our lives, from the ergonomic design of kitchen utensils to the intricate components of electronic devices. Behind the scenes, a sophisticated manufacturing process transforms raw materials into precision-engineered products, showcasing the ingenuity and craftsmanship of human innovation.
Applications Across Industries
Consumer Goods
Plastic molded products play a vital role in the consumer goods industry, offering cost-effective solutions with customizable designs and vibrant aesthetics. From packaging materials to household appliances, plastic molded products enhance functionality and appeal while meeting consumer demand for sustainability and convenience.
Automotive
In the automotive sector, plastic molded products contribute to vehicle safety, performance, and aesthetics. From interior components such as dashboards and door panels to exterior parts like bumpers and grilles, plastic molding technologies enable lightweight yet durable solutions that optimize fuel efficiency and design flexibility.
Medical Devices
The medical industry relies on plastic molded products for a wide range of applications, including surgical instruments, implantable devices, and diagnostic equipment. With stringent requirements for biocompatibility, sterility, and precision, plastic molding techniques ensure compliance with regulatory standards while facilitating innovation in healthcare delivery.
Manufacturing Processes and Technologies
Injection Molding
Injection molding is the most common method used for producing plastic molded products, utilizing high-pressure injection of molten plastic into a mold cavity. This process offers fast cycle times, high production volumes, and intricate part geometries, making it ideal for mass production of complex components with tight tolerances.
Blow Molding
Blow molding is employed to manufacture hollow plastic parts, such as bottles, containers, and automotive fuel tanks. The process involves inflating a heated plastic parison inside a mold cavity, resulting in seamless, lightweight, and cost-effective products suitable for diverse packaging and industrial applications.
Compression Molding
Compression molding is well-suited for molding thermoset plastics into intricate shapes with high strength and dimensional stability. By applying heat and pressure to a preform or charge placed in a heated mold, compression molding offers superior material properties and surface finish, making it ideal for aerospace, electrical, and automotive applications.
Future Trends and Innovations
As technology continues to advance, the future of plastic molded products is poised for further innovation and disruption. Additive manufacturing, smart materials, and sustainable practices are shaping the next generation of plastic molding technologies, enabling customized solutions, reduced lead times, and enhanced environmental stewardship. By embracing these trends and investing in research and development, the industry can continue to push the boundaries of possibility and meet the evolving needs of a dynamic global market.
In conclusion, plastic molded products represent a cornerstone of modern manufacturing, offering unparalleled versatility, efficiency, and performance across a diverse range of industries. With a rich legacy of innovation and a commitment to continuous improvement, plastic molding technologies will continue to drive progress and shape the future of product development and design.
GETTING A QUOTE WITH LK-MOULD IS FREE AND SIMPLE.
FIND MORE OF OUR SERVICES:
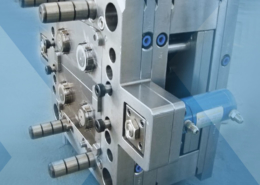
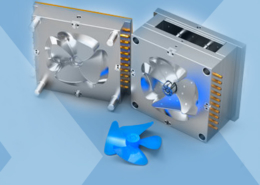
Plastic Molding

Rapid Prototyping
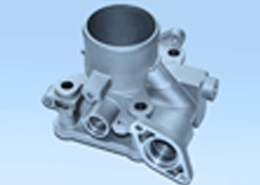
Pressure Die Casting
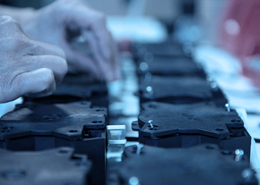
Parts Assembly
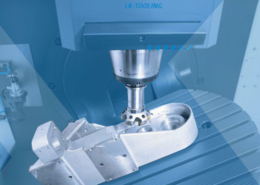