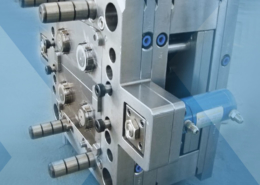
High Density Polyethylene (HDPE) Plastic Injection Molding - hdpe injection mold
Author:gly Date: 2024-10-15
Overview: 3D Scanning or 3D Imaging is a process where the digital shape an object can be measured with non-contact imaging systems. 3D laser scanners collect millions of data points in three dimensional space called a point cloud. This method provides extremely accurate measurements of these points in X, Y, Z positions. The resulting digital image can be drafted or modeled in CAD systems to create a model that can be reproduced or edited to the desired geometry. 3D scanning is very useful in reverse engineering where legacy parts produced prior to digital technology or parts with no CAD model can be created and used for documentation, modeling, 3D printing, production tooling, or quality inspection.
Where used: Polyjet is often used for manufacturing parts with gaskets, seals or need for soft grips combined with hard plastics. Combining colored and transparent resins also allow for illustration and creative design. Polyjet is also used for creating wax molds for investment castings
The plastic prototyping, modeling and “bridge-to-production” tooling technology is rapidly changing. Texas Injection Molding maintains in-house and an outside network of industry leading providers to deliver our customers a broad range of material, size and processes to model and replicate performance as close as possible to production units. We offer concept review, design consultancy, material selection, prototype and low volume production for projects that are planned to increase to volume production.
Unlock the potential of HIPS - where proven success meets unmatched durability and precision in high-quality plastic manufacturing.
At Advanced Plastiform, Inc. we work hard to provide our customers with durable, long-lasting plastics that offer the qualities they need while keeping lead times fast and prices low. In order to achieve the best results, we take care to match the most suitable thermoplastic to the project. One of those plastics we offer is high impact polystyrene, also known as HIPS.
Materials Used & Part Characteristics: A variety of UV curable polymers allow for simulation for a range of material substitutes. Polyjet has soft materials in Shore A hardness from 25 – 95, stiff but flexible materials similar in feel too polypropylene, and rigid materials with characteristics similar to ABS. Corners designed to be sharp may have a slight radius.
Injection molding works by melting the high impact polystyrene into a liquid, then injecting it into the double-sided mold with extremely high pressure. Once it’s cooled and solid, the product is painted, labeled, or coated as needed.
Overview: Polyjet provides the ability to print multi-material, highly accurate and tight tolerance parts. Parts can be black, white, transparent and have a range of softness from rubberlike to rigid in the same part.
HIPS injection molding is ideal for small plastic parts and products, especially those needed in large quantities, or parts that need high levels of detail or variable thickness. While the tooling cost is higher with injection molding than thermoforming, we strive to deliver affordable tooling designs that, once created, can be used for additional orders in the future. This means that for high unit requirements, the per-unit cost is very low.
We understand the requirements of high-volume manufacturing and offer design for manufacturing experience to ensure cost effective manufacturable products as products are delivered from prototype to high volume production.
Materials Used & Part Characteristics: Photopolymer (UVcurable) epoxy or acrylic-base materials are used to manufacture fine resolution cosmetic parts.
Overview: SLA provides the ability to print very tight tolerances, smooth surface finishes and high resolution of small features. The main downside is the lower mechanical strength and not suitable for exposure to UV or sunlight.
Where used: Often used in creating fixtures due to low cost and strong mechanical strength. Also used in early stage prototypes or concept models.
High impact polystyrene is affordable, versatile, and makes an excellent choice for many of the products we manufacture. With the best materials and innovative equipment and technology, we’re a leading plastics manufacturer, serving businesses across North Carolina, South Carolina, Pennsylvania, Maryland, Tennessee, Georgia, and Virginia.
Vacuum forming is used for large plastic pieces that don’t need high levels of detail or sharp corners or edges. While it is the most basic method of thermoforming, it’s also quick and affordable. Once the plastic is heated and fitted to the tool, a powerful vacuum is fitted between the tool and the plastic, suctioning out all air from between the two and pulling the thermoplastic firmly against the tool, creating an accurate shape. HIPS vacuum forming is often used to produce refrigerator liners and boat hulls.
Overview: Machining is a subtractive process where we start with a solid block of material and remove material to leave a finished part. Machining allows for use of specific grades of plastics or metals that are not available for printing.
Where used: Machining especially useful in evaluating mechanical performance in specific materials prior to finalizing part geometry and material specifications. Machining is suitable for prototyping and low volume production.
When defined edges, corners, and detailing is necessary, we use pressure forming. Like vacuum forming, we fit heated HIPS around a tool, but then, we use highly pressurized air to blast the plastic, pressing it firmly against the tool. Using air pressure uses three times the force of vacuum forming, creating a high level of detail. Pressure forming with HIPS is so precise, it can often be used in place of injection molding and is often used in creating automobile parts, including instrument panels and electronic equipment.
Where used: Cosmetic prototypes that require high resolution details and smooth surface finishes. Also used in molds for casting other materials:• Casting and Modeling• 3D Printing
Our plastic prototypes are high quality and are made with accuracy and consistency. Our network of providers has the expertise to consult on your design and make the appropriate changes easily and at a low cost.
Twin sheet forming is the most complex high impact polystyrene thermoforming method. We heat two sheets of HIPS simultaneously, then fit and fuse them together. While it sounds simple, great care must be taken to make sure the two pieces are able to fuse together at the pressed points. This method is used to create hollow and double-walled industrial products. Gas cans and air ducts can be made by twin sheet forming HIPS.
Overview: SLS provides the ability to generated complex geometry, highly accurate and durable parts that are suitable for use as functional parts.
Materials Used & Part Characteristics: PA12 is the most common, but PA6 and PA11 are also common. ABS, PC PMMA, POM and some TPU’s and compounds with additives are also available. Nylons offer strong, heat resistant and durable parts.
While general-purpose polystyrene is lightweight, clear, and brittle, HIPS benefits from rubber additives to make it much more is much more flexible and improve its impact strength. Though it has an opaque appearance, it can be painted, labeled, and designed with ease.
Since 1988, Advanced Plastiform, Inc., has been providing superior custom plastic molding and fabrication services to companies in North Carolina, South Carolina, Maryland, Georgia and Pennsylvania. Contact us to make an appointment Mon-Fri 8-5.
Rapid Prototyping is an additive manufacturing technology and comprises of techniques that can speed up the time it takes to fabricate a prototype with flexibility. It all starts with a design from modeling or CAD software. And then with 3D printing we can interpret the CAD data and create the 3D model.
Once heated, HIPS is highly malleable, meaning high-impact polystyrene thermoforming is an excellent way to manufacture the plastics our customers need. To do this, large sheets of HIPS are heated and fitted over a custom tool. Then, to achieve the ideal shape and design, we use one of three methods to complete the thermoforming process.
Materials Used & Part Characteristics: FDM is noted for it wide range of material options.Some of the major materials include ABS, PLA, Nylon (PA6 / PA 66), PETG and TPU materials are melted and extruded in round layers to build up parts. Because the extrusion is round, sharp corners and other fine features are limited.
Overview: Fused Deposition Modeling is a low-cost prototyping process that allows for mechanically strong parts to be created.
GETTING A QUOTE WITH LK-MOULD IS FREE AND SIMPLE.
FIND MORE OF OUR SERVICES:
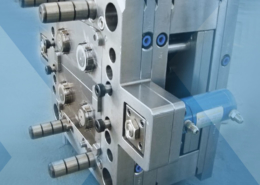
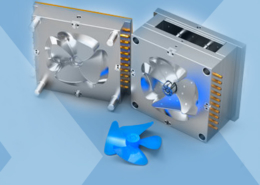
Plastic Molding

Rapid Prototyping
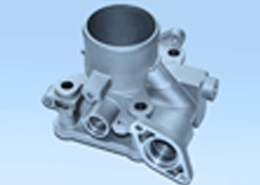
Pressure Die Casting
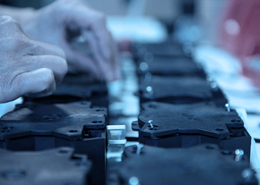
Parts Assembly
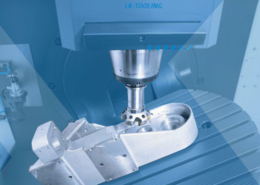