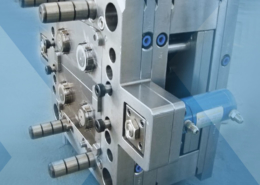
Hemp Bioplastics on Horizon, Pioneer Says - hemp injection molding
Author:gly Date: 2024-10-15
“Delivery looks great especially with the demand chaos that has been going on during June-July-August. We are back to the standards we appreciate from AMT. Everyone is doing a great job.”
“You can really tell there is a sense of pride here with your people and facilities … The amount of effort to prepare for our visit and your hospitality today was very appreciated.”
"Everyone at AMT did a fantastic job accommodating our needs and on the fly requests. We really appreciate all the support and look forward to our next opportunity to work together.”
Injection moulding technology has advanced significantly over the past few decades, providing manufacturers with more efficient and higher quality production methods. At Total Moulding Solutions, we are committed to staying at the forefront of these innovations, ensuring our clients receive the best possible products. In this blog, we will explore some of the latest advancements in injection moulding technology and how they enhance efficiency and product quality.
“We just really appreciated all of your effort, hard work and responsiveness, as we always do, but especially in this circumstance (to complete the development in the requested timeline) … The AMT team is amazing, and my thank you is really just a tiny token of the appreciation we have for all of you, for what you have done for this project and just in general. We love working with you guys, too!”
Multi-material and multi-component moulding techniques involve the use of different materials or colours in a single moulding process. This innovation allows for the production of complex parts with various properties, such as hard and soft sections or different colours. It reduces the need for assembly, lowers production time, and enhances the functionality and aesthetics of the products.
“Talking to my tooling engineers, they really like working with Advanced. They appreciate the efforts Advanced has put forth so far. I really excited to keep growing with Advanced.”
One of the key innovations in injection moulding is the development of new materials. These materials are designed to meet specific requirements, such as increased strength, flexibility, or resistance to extreme temperatures. High-performance thermoplastics and bioplastics are becoming more popular, offering sustainable options without compromising on quality. These materials can significantly reduce production costs and improve the lifespan of the final products.
Micro-moulding is a cutting-edge technology that allows for the production of extremely small and precise components. This is particularly useful in industries such as medical devices, electronics, and automotive, where miniature parts are essential. Micro-moulding requires specialised equipment and expertise, which Total Moulding Solutions possesses, enabling us to produce intricate designs with tight tolerances.
“First of all, I would like to thank you for all the support and time AMT has invested in the DFM discussion of the conceptual design of the disposable sheath … We believe you guys have partnered well with us and we look forward to collaborating again in the future … Thank you for the thoroughness your team provided on the quote and the DFM process.”
A leading tooling and injection moulding specialist, we offer customers a full service solution, taking your product from design through to manufacture.
Additive manufacturing, or 3D printing, has become an invaluable tool in the injection moulding industry. It is used for rapid prototyping, tooling, and even small-scale production runs. The integration of 3D printing with traditional injection moulding processes enables quicker turnaround times and cost-effective production of complex parts. This hybrid approach allows Total Moulding Solutions to offer more flexible and customised solutions to our clients.
The continuous advancements in injection moulding technology have significantly improved the efficiency and quality of manufacturing processes. At Total Moulding Solutions, we embrace these innovations to deliver superior products to our clients. By staying up-to-date with the latest trends and incorporating state-of-the-art techniques, we ensure that our injection moulding services remain at the cutting edge of the industry. Contact us to find out more.
"THANK YOU! - so much for expediting our order. This was such a huge help - our customer is now very happy because of your great team!”
“Our team was very impressed when we had an issue and you guys jumped on it and provided solutions without our team having to drive it. That tells me a lot about the molder and most of our other molders are not like that. It’s how you respond to issues that will set you apart.”
"I really want to thank the whole AMT team for your responsiveness on this expedite request. Your creativity to solve this capacity challenge and your willingness to go above and beyond has been outstanding.”
Based in the North-East of England, our family-run company works with brands across the globe and has a proven track record within the industry.
Advancements in real-time monitoring and control systems have made it possible to oversee the injection moulding process with greater precision. Sensors and software monitor various parameters, such as temperature, pressure, and fill rate, allowing for immediate adjustments if any issues arise. This ensures optimal conditions are maintained throughout the production cycle, leading to consistent product quality and reducing waste.
Recent global disruptions, such as Brexit and the COVID-19 pandemic, have exposed vulnerabilities in international supply chains. For UK manufacturers, reliance on overseas suppliers has led to increased lead times,
Cooling is a critical phase in the injection moulding process, directly impacting cycle times and product quality. Innovations in cooling techniques, such as conformal cooling channels created through additive manufacturing, have led to more efficient heat dissipation. This results in faster cooling times, reducing overall cycle times and improving the dimensional accuracy of the moulded parts.
The tool manufacturing process is a critical aspect of injection moulding, as the quality of the tool directly impacts the final product. At Total Moulding Solutions, we take pride in
"Thank you guys for getting together! We really enjoy working with AMT, you are all so friendly and helpful, we really appreciate that!"
Our Customer Loyalty Index is a metric we track through our annual customer survey. In the survey we pose the question, "On a scale of 1-5 (5 being highest), has Advanced earned the right to be considered for repeat business?". We average the scores for this rating into our composite customer loyalty index.
"AMT is great to work with and appreciate your responsiveness and support. We are currently discussing our next generation and are looking forward to working with AMT.”
The integration of automation and robotics into injection moulding processes has revolutionised the industry. Automated systems can handle tasks such as part removal, inspection, and packaging, reducing the need for manual labour and minimising human error. Robotics also improve cycle times and consistency, ensuring high-quality output. At Total Moulding Solutions, we utilise state-of-the-art automation to streamline our production processes.
Owned and managed by engineers, we specialize in technical applications of fluid path, critical shutoffs, and disciplined manufacturing. We pride ourselves on our approach to problem solving and how we unlock the best ideas through collaboration.
"There was never a time I couldn’t pick up the phone to ask questions and she was there to help answer my questions and problem solve.”
"...you and your team do a really great job documenting GR&Rs according to our Guidance Document, much better than all our other suppliers. We use an example of AMT’s to teach our other suppliers. Also, the way AMT documents rationale in reports is very clear and easy to understand. Thank you and keep up the great work.”
"We were able to place our first P.O. for these parts today! Thanks to the AMT team for sticking with us , and demonstrating excellent partnership throughout this program. We were able to complete a difficult, and time sensitive project resulting in a fantastic production output. We really appreciate you all and look forward to working with you on the next big creation. Thanks again.”
Sustainability is a growing concern in the manufacturing industry. New technologies in injection moulding are focused on reducing environmental impact through energy-efficient machines, recycling of scrap materials, and the use of biodegradable or recyclable polymers. At Total Moulding Solutions, we are committed to implementing sustainable practices, ensuring that our operations are environmentally friendly while maintaining high standards of product quality.
Twin-Shot Molding vs. Overmolding: Understanding Key Injection Molding Techniques In the world of plastic injection molding, two critical processes stand out: twin-shot molding and overmolding. Both techniques allow manufacturers to
"Brett, I want to thank you and your team for yet again the high level of collaboration. I think it’s safe to say that over the 17+ years we have worked together, we have truly formed what a true partnership should be!"
GETTING A QUOTE WITH LK-MOULD IS FREE AND SIMPLE.
FIND MORE OF OUR SERVICES:
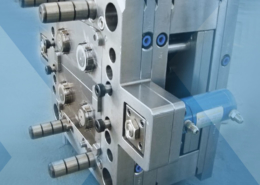
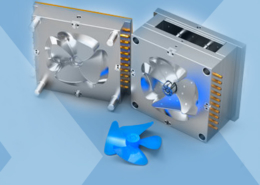
Plastic Molding

Rapid Prototyping
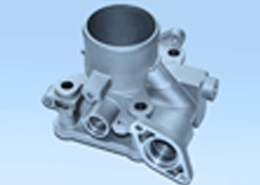
Pressure Die Casting
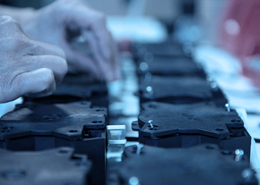
Parts Assembly
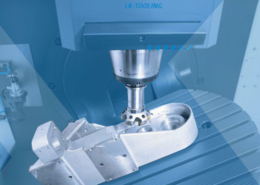