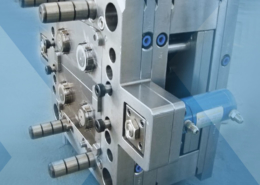
Heat & Cool for Plastic Injection Molding - cold molding plastic
Author:gly Date: 2024-10-15
PCS Company mold components are designed and manufactured to exceed demanding customer expectations for quality, reliability, and performance. With an extensive product selection supported with superior customer service, you can count on PCS to meet your needs.
After the mold close and the first-shot is injected, it then slides and the second-shot is set and injected. These steps form one full cycle.
Crush – This is the shutoff that protects the first shot material and prevents the second-shot material from oozing onto the first-shot.
For every cycle, the first-shot is molded along with the basic material. At the same time, the second-shot is molded with the parts of the first-shot that was used from the previous cycle.
A 2-shot plastic injection process can be referred to as several other names such as a dual-shot, multi-shot, or overmolding.
Rotary – This process utilizes a tool called a rotary plate which can either be built in already or activated either by a rack system or by hydraulics.
The method itself is not overly complicated as it is often perceived by people who are considering starting up their own molding company.
First phase – this phase has a likeness to the traditional way of injection molding where a resin is injected inside a mold. From that point on, the mold is cooled to form a solid structure.
Support – This is applied on the first-shot part to ensure that the pressure from the second-shot cavity does not deform the first-shot part.
In general, this method utilizes a vertical platen, which is positioned on one side of the clamp. This vertical platen will then rotate on a horizontal axis.
The hydraulic cylinder that activates the cores must be powerful enough against the pressure of cavity plastics. Doing so will ensure that there won’t be any flash in the finish products.
After injecting the shots inside the cavities, the molds are rotated. By doing so, the first shot will align with the second-shot cavity.
To sum it all up, a 2-shot plastic injection molding is not as complicated as most perceive it to be and it definitely yields numerous benefits.
Things you need to pay attention during the cycles, especially when the first shot is in the position of the second-shot, are crush and support.
For thicker wall stock, supplementary crush is added to make up for the extra shrinkage. More crush can be achieved by adding steel to the shutoff of the second-shot.
A wrong alignment may cause damage on the machine’s shutoffs, bushings, or leather pins, especially when the mold takes a 180° rotation.
There are plenty of misconceptions regarding a 2-shot plastic injection molding process. Molding companies often disregard the advantage of a 2-shot injection process due to the perception that it is a complicated method, very costly, and time-consuming.
More than one finished product can be finished in just one processing since a number of mold pieces can be processed simultaneously.
Second phase – The solidified part is then moved to a second mold. The transfer is either done through a robotic arm or a rotating platen. From that point, a second resin shot is injected through a certain part of the solidified structure. The point of injection varies depending on the design of the structure. A molecular bond is formed by the two plastic resins. Finally, the parts are first cooled before it is ejected from the mold.
Locators are essential parts of the mold because it ensured that pieces are accurately centered in the rotary platen. Concerns regarding alignment may arise if the mold is not centered.
A rotary and a movable core ate the two variations of a 2-shot injection molding process. These two processes both utilize a second injection unit and requires two processes and two runner systems.
Multi-colored parts are better produced using a 2-shot/multiple-shot molding process since it is possible to utilize several materials at just one run.
To produce a part per cycle, two pairs of identical ejector cavities and two sets of cover cavities must be used. One of the cover cavities is specifically intended for the first-shot, while the other is for the second one.
A second runner system and two sets of ejector plates must be kept running, and the movable parts must be rotating. The movable half is called “ejector cavities,” while the unmoving half is referred to as the “cover cavities.”
Although, the execution of the process is notably challenging to master. With the nature of the industry, which is producing immense amounts of products, even small errors can equate to a higher cost. That is why, for a 2-shot plastic injection process, workers must have expert-level technical skills and impeccable eye for detail.
Movable core – Unlike the earlier method, a movable core process does not require a rotary platen and utilizes a normal mold. This mold utilizes only one part and one cavity.
GETTING A QUOTE WITH LK-MOULD IS FREE AND SIMPLE.
FIND MORE OF OUR SERVICES:
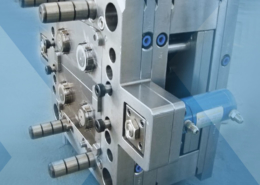
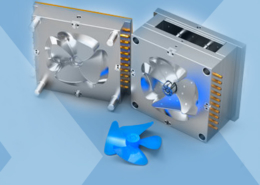
Plastic Molding

Rapid Prototyping
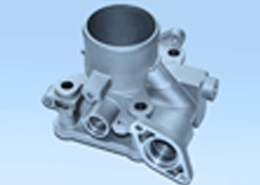
Pressure Die Casting
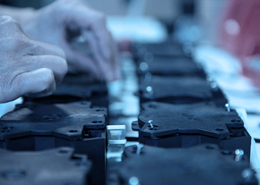
Parts Assembly
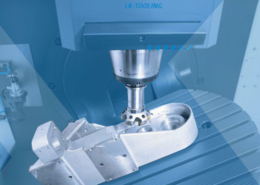