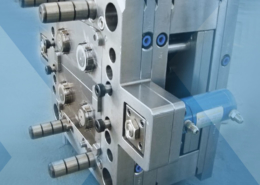
HDPE vs. UHMW: Material Differences and Comparisons - uhmw injection molding
Author:gly Date: 2024-10-15
While injection molding is traditionally considered a manufacturing process only for mass production due to its high tooling costs, leveraging 3D printing to fabricate injection molds empower you to use this process to produce high-quality and repeatable parts for prototyping and low-volume production.
The system is designed to iterate, innovate, and improve. By making a plastic prototype, we learn, adapt, and get better, not just in the context of a single product, but evolving the broader understanding of manufacturing capabilities and constraints.
In addition, the cost per unit of an injection molded part decreases with volume, making it a cost-efficient way for mass production. This is particularly beneficial for companies planning to produce a high volume of products. The prototype mold making process also allows for the use of a wide range of materials, including less expensive plastics, further contributing to cost savings.
From understanding the concept to exploring its economic benefits, it’s clear that injection molding prototyping is a powerful tool in product development. It offers high precision, material versatility, design flexibility, and production equivalency, all while reducing time-to-market. With sustainability considerations and future trends in mind, the injection molding prototype process is set to continue playing a pivotal role in bringing innovative, successful products to market.
Monitoring costs: Despite the reliance on automation, equipment operators are expected to monitor the progress of the injection molding process. Operator wages accrued during the process are added to the total cost of injection molding.
The prototypes produced through injection molding aren’t simply rough drafts of the final product—they mirror exactly how the final product will look and perform. This level of equivalency goes beyond physical properties; prototypes can also incorporate colors, textures, and finishes that the final product will feature.
It’s hard to overstate the importance of this. When stakeholders can see and feel a prototype that matches the finished product quality, it greatly instills confidence in the product’s success. This advantage also extends to the product testing phase, as the findings from prototype tests can be directly applied to full-scale production.
Part size: The larger the item or part to be molded, the larger its mold will be to accommodate the part. Larger parts tend to require more injected materials to complete production cycles. Larger mold designs usually come at an increased cost compared to fabricating the same design but with smaller dimensions.
When it comes to reliable and high-quality injection molding prototyping, FOWmould stands out. With a proven track record, the extensive network of partners, and commitment to innovation, FOWmould is the go-to choice for businesses seeking to streamline their product development process and bring successful products to market.
The journey of how to make a plastic mold prototype starts with feeding raw material, usually thermoplastic polymers, into a machine. This material is heated until malleable, then injected into a mold cavity designed according to the CAD model. The material cools and solidifies, adopting the shape of the mold to give a plastic prototype reflecting the shape and dimensions of the intended final product. This plastic prototype manufacturing process enables fabricators to optimally design and make adjustments before proceeding to full-scale production, thereby saving time, reducing tooling costs, and enhancing the product’s quality.
The three scenarios in the table show the methods and the mold types that result in the lowest cost per part depending on the production volume.
The process involves using a 3D printer to create a mold from a CAD model. This mold can then be used in the injection molding process to create a plastic prototype. The advantage of this method is that it allows for quick iteration and testing of designs without the need for expensive tooling.
The cost of purchasing materials for molds differs according to the material chosen. Thermoplastic pellets cost approximately $1 to $5 per kg.
One of the key advantages of using an injection molding prototype in product development is the flexibility it offers in terms of design and iteration. While the initial creation of the mold requires a certain investment of time and resources, once it’s made, it can be used to produce multiple copies of the part quickly and efficiently.
Understanding the different types of costs associated with injection molding requires an in-depth analysis of the process.
Setup/configuration cost: The setup labor focuses on the time taken to configure the utilized equipment to produce the mold and the finished product.
There are numerous examples of successful products that started their journey as injection molding prototypes. Let’s look at a couple of case studies:
Sustainability is an increasingly important factor in manufacturing practices, and injection molding prototyping isn’t exempt from these considerations. When it comes to environmental impact, different stages of the prototype injection molding process have various factors to consider.
3D printing has revolutionized the world of prototyping, offering a rapid and cost-efficient way to create physical models from digital designs. In the context of injection molding, 3D printing can be used to create prototype molds, thereby speeding up the prototyping process and reducing costs.
Apply a core cavity approach that simplifies the design of Side B of a mold. The core cavity approach involves sinking the wall cavities into the mold base, thereby reducing the need to mold steep draft angles while improving surface finish.
Moreover, injection molding prototypes can be used to demonstrate the product to potential investors, stakeholders, or customers. This can be a powerful tool for gaining feedback, securing funding, or generating pre-launch buzz. By making a plastic prototype, companies can also gauge market interest and gather valuable user feedback before committing to full-scale production.
Large industrial injection molding machines can cost anywhere from $50,000 to $200,000+. These machines also come with more stringent facility requirements and require skilled labor for operation, maintenance, and monitoring. As a result, unless injection molding is a core competence, most enterprises outsource mass production to service providers and contract manufacturers, in which case the equipment costs are included in the service costs.
Injection molding is one of the leading processes for manufacturing plastics. It is widely used for mass-producing identical parts with tight tolerances. It is a cost-effective and extremely repeatable technology that yields high-quality parts for large series production.
Prototyping, including injection molding prototype creation, is an exciting phase in the product development process. It’s where the rubber meets the road – concepts turn into physical objects, ideas turn into reality. This space is ripe for creativity and innovation.
In this white paper, learn how to combine rapid tooling with traditional manufacturing processes like injection molding, thermoforming, or casting.
The equipment associated with injection molding is generally self-regulating and relies on automation to get the job done. CNC machines, EDM machines, and 3D printers rely on the specifications of the CAD design to produce a mold. The injection molding machine also relies on automation to inject materials into the mold, and industrial IM machines often cool and eject the finished item autonomously.
Furthermore, once the mold is created, parts can be produced at a high rate, making it possible to move from prototyping to mass production in a relatively short period of time. This can give companies a competitive advantage, allowing them to get their products to market faster than their competitors.
Special-purpose machines are used for injection molding that can range from smaller desktop injection molding machines that businesses can use in-house to large industrial injection molding machines that are mostly operated by service providers, contract manufacturers, and large manufacturers.
Simple low-volume 3D printed molds can cost as little as $100, while the cost of designing and manufacturing complex molds for high-volume production may hit the $100,000 mark. Despite the considerable fixed start-up costs, the injection molding process has low variable costs due to the inexpensive thermoplastics materials, short cycle times, and the labor needs decrease progressively due to automation and economies of scale. This means that the variable costs of production are low and the process becomes more efficient and the cost per part decreases at higher volumes as the costs get distributed among hundreds or thousands of parts.
Making a plastic prototype is crucial for not only evaluating the idea, but also for demonstrating this concept to potential investors or stakeholders. An injection molding prototype helps to physically visualize the concept in 3D, communicate the idea more efficiently, and receive constructive feedback early in the game. Prototyping also allows ample room for design flexibility and iteration in injection molding prototyping, streamlining further design processes.
In this video, we've partnered with injection molding service provider Multiplus to walk you through the steps of the injection molding process using 3D printed molds.
The industry is continuously exploring new methods, materials, and technologies to reduce the environmental impact, including researching biodegradable plastics and developing more efficient machines.
Both methods have their place in the prototyping process. 3D printing is excellent for initial prototypes and design iteration, while injection molding is often the preferred choice for later-stage prototyping and final product manufacturing.
For enterprises with the equipment and tools for injection molding, choosing to create molds in-house could be the least expensive option if the technical know-how is also available. If the tools needed for injection molding are not readily available, then outsourcing reduces the cost associated with developing a mold.
Online injection molding cost estimators or quotes from injection molding service providers can provide benchmarks and help you estimate the cost of injection molding specific parts.
Developing more complex molds requires technical expertise. As a result, enterprises often outsource specific aspects of the injection molding process such as the design and fabrication of the mold.
* Equipment costs are not calculated into the production costs in this example as the cost of these tools can be distributed among multiple projects. Purchasing a desktop injection molding machine and an SLA 3D printer allows businesses to get started with injection molding for less than $10,000.
Production volume: The number of items to be produced using injection molding determines the production technology and the quality of material to use when creating the mold. Low volume projects might require 3D printed or lower-grade machined aluminum molds, while large production volumes will require high-grade steel molds or even multiple molds to manage the process without wear and tear affecting the quality of produced items. This affects the cost of the mold, but of course, the increased cost of high volume molds is distributed among more parts, which normally leads to a lower per part cost.
Evaluate the CAD model to determine its feasibility before undertaking an injection molding project. Eliminate potential bottlenecks such as steep angles, undercuts, and other complex geometries.
When producing in-house, these costs are calculated into the labor costs. When a business outsources injection molding, the labor and the markup of the service provider are added to the service cost.
Simple low-volume 3D printed molds can be produced on an SLA 3D printer for as little as $100. An aluminum mold for a mid-volume production run of approximately 1,000-5,000 units falls within the range of $2,000 to $5,000. For molds with more complex geometries and primed for larger production runs of approximately 10,000+ units, the cost of mold can range from $5,000 to $100,000.
Injection molding offers unparalleled versatility in terms of the materials that can be used. Unlike 3D printing, which can typically only utilize a specific type of plastic or resin, injection molding can accommodate a wide array of materials. The most commonly used is a variety of thermoplastic polymers, which offer a range of properties to meet the requirements of different applications.
As we forge ahead into the future, the process of making an injection molding prototype will continue to evolve. New materials with enhanced properties, such as biodegradable plastics and composites, are expected to emerge. Technologies like AI and machine learning are anticipated to make the process more efficient and accurate.
On the other hand, injection molding, while initially more time-consuming due to the mold-making process, becomes highly efficient for larger production runs. The prototype injection molding machine can produce multiple copies of a part in a relatively short period of time once the mold is created.
The feasibility of complex designs, the range of materials accessible, and the process’ inherent nature to refine an idea make prototype injection molding a powerful tool for innovation. Designers can experiment with new shapes, incorporate novel features, and trial unconventional materials. Mistakes here cost less and teach more compared to later production stages.
The resulting cast from the injection molding process can then be further treated or modified as necessary, for example through painting, metallization, or the application of other surface treatments. This flexibility in material choice and post-processing allows for a great deal of customization and optimization, enabling the production of prototypes that closely mimic the final product’s functionality and aesthetics.
Producing low volumes of parts with injection molding is the most cost-effective with smaller desktop injection molding machines and 3D printed molds. If you are new to injection molding and are looking into testing it with limited investment, using a benchtop manual injection molding machine such as the Holipress or the Galomb Model-B100 could be a good option. Automated small-scale injection molding equipment such as the desktop machine Micromolder or the hydraulic machine Babyplast 10/12 are good alternatives for medium-series production of small parts.
The table below highlights the cost associated with injection molding a hypothetical plastic item, such as a small enclosure of an electronic device, which makes the cost dynamics of injection molding easier to understand:
Mid-volume production is the most efficient with machined aluminum molds that have a lower cost than traditional steel mold, but are durable enough to last a few thousand shots, depending on factors like the material and the design. In most cases, low-volume injection molding is only reasonable with 3D printed molds—in our example, if we were to use an aluminum mold to produce 100 parts, its cost would account for $30 for each part, while a traditional steel mold would mean $200 for each part.
Stay updated with the latest 3D printing news, interviews with experts from around the world and tutorials on how to leverage 3D printing.
When it comes to high precision and consistency, the injection molding prototype process stands out. The use of CAD models and CNC machining to create aluminum or steel molds means that each and every part produced is virtually identical. This consistency is crucial in industries like healthcare, aerospace, and automotive where a tiny variation can have big consequences.
It is important to note that a majority of the injection molding process is dedicated to cooling. The quicker a mold cools down the faster the injected material solidifies and the faster the production cycle can be repeated. Thus, cooling channels play an important role, especially for high-volume production, and should be included in the design of the mold. For low-volume production with 3D printed molds, manual cooling using compressed air is an option.
A wide variety of plastics can be used for injection molding depending on the requirements of the final parts, including ABS, PS, PE, PC, PP, or TPU.
Normally, the main cost driver in injection molding is the cost of the mold, also known as the tooling cost. The cost of designing and building a mold depends on the required production volume, the complexity of the part design, mold material, and the process used to create the mold.
In the context of product development, prototyping plays an integral role. Specifically, creating a prototype injection molding machine model is a cost-efficient way of identifying and rectifying any design flaws at early stages. Imagine you’re working on a new product, perhaps a piece of custom consumer electronics or an innovative kitchen gadget for a wide range of materials. Before diving directly into mass production, you’d want to ensure the idea is practical and cost-effective.
In general, injection molding is the most efficient at higher volumes, as the costs then get distributed among thousands of parts. But even though the cost per part for low-volume injection molding is slightly higher, it is still substantially more affordable for low-volume production than other manufacturing methods.
The cost of the mold is largely defined by the complexity and the amount of time it takes to produce it. We advise adhering to design for manufacturing principles to drive down part costs with injection molding.
In terms of trends, we can expect to see even greater synergy between prototyping methods as the lines between processes like injection molding and 3D printing become ever more blurred. Despite what the future holds, one thing is clear: injection molding prototypes will continue to play an essential role in product design and development.
In context, that’s how to make a plastic mold prototype with a high degree of precision, offering the advantage of producing more complex and accurate prototypes in comparison to other methods. This precision, coupled with relatively high output rates once molds are created, makes injection molding prototyping a viable choice for projects with detailed requirements and high volume needs.
3D printing: 3D printing is a powerful solution to fabricate injection molds rapidly and at a low cost. It requires very limited equipment, saving CNC time and skilled operators for other high-value tasks in the meantime. Manufacturers can benefit from the speed and flexibility of in-house 3D printing to create molds that can be used on both desktop and industrial molding machines. Furthermore, product development benefits from the ability to iterate on the design and test the end-use material before investing in hard tooling for mass production. Stereolithography (SLA) 3D printing technology is a great choice for injection molding. It is characterized by a smooth surface finish and high precision that the mold will transfer to the final part and that also facilitates demolding. 3D prints produced by stereolithography are chemically bonded such that they are fully dense and isotropic. Desktop SLA printers, like those offered by Formlabs, start below $5,000 and can seamlessly be integrated into any injection molding workflow as they are easy to implement, operate, and maintain.
From an economic perspective, investing in an injection molding prototype can yield significant benefits. While there are upfront costs associated with creating the mold, these can be offset by the savings realized through early identification and resolution of design issues.
Part volume and cavities: Part volume refers to the cavity size of a mold. The more cavities or cavity volume a mold requires the longer the press time. Increased press time slows down the production process which leads to increased cost.
This allows for rapid iteration and testing of designs. If a design flaw is identified in the prototype, the CAD model can be adjusted and a new mold created. This process can be repeated as many times as necessary until the design is perfected. This is particularly beneficial in the early stages of product development, where designs often undergo significant changes.
These case studies highlight the versatility and effectiveness of injection molding prototypes in product development across a range of industries.
On top of that, injection molding allows for complex geometries and designs that other methods might struggle to replicate accurately. The raw material is injected into the mold under high pressure, which helps to fill any small or intricate features in the mold, resulting in parts that closely match the original design.
It is a fast, intensive process where high heat and pressure are involved to inject molten material inside a mold. The molten material depends on the scope of the manufacturing project. The most popular materials are various thermoplastics, such as ABS, PS, PE, PC, PP, or TPU, but metals and ceramics can be injection molded as well. The mold consists of a cavity that accommodates the injected molten material and is designed to closely mirror the final features of a part.
Furthermore, having a physical prototype can help secure funding from investors or pre-orders from customers, providing an early source of revenue. It also reduces time-to-market, allowing companies to start selling their products sooner.
Moreover, injection molding is capable of producing complex and intricate designs that might be difficult or impossible to achieve with other prototyping methods. This includes features like undercuts, threads, and inserts, which can be incorporated directly into the mold design.
Embrace the use of self-mating parts to reduce the need to create multiple molds when one universal mold can be used to achieve similar results.
This process is not only a cost-effective way to create prototypes but also a powerful tool for testing and refining designs. It allows for a short period of time to make adjustments and improvements before moving on to mass production. And with the use of injection, even complex shapes with undercuts can be achieved, offering a competitive advantage in various industries.
Use 3D printed injection molds with both benchtop and industrial machines to efficiently and affordably produce hundreds to thousands of functional prototypes, parts to accelerate product development, reduce costs and lead times, and bring better products to market.
A molding cost comparison table also serves a similar purpose. Injection molding service providers use cost comparison tables to provide prospective customers with a rough estimate of the process.
This white paper showcases the cost-dynamics for real-life use cases, and presents guidelines for using SLS 3D printing, injection molding, or both.
The process of making an injection molding prototype is a fascinating journey from a concept to a tangible product. It begins with a CAD model, which is a computer-aided design of the product. This model is then used to create a mold design, which is essentially a negative of the product. The mold is typically made from aluminum or steel, and it’s where the magic happens.
Electrical discharge machining (EDM): The EDM method is generally used to create highly complex mold designs that cannot be easily reproduced using standard machining methods. EDM involves the use of a workpiece and a tool electrode to create the desired mold shape. The tool electrode and workpiece electrode are separated by a dielectric fluid and subjected to voltages that cause recurring current discharges. The discharges are responsible for shaping the workpiece electrode into the final mold. EDM is highly accurate and does not generally require any additional post-processing. Similar to CNC machining, EDM is also an industrial process that many companies outsource to machine shops.
By allowing for early detection and resolution of design issues, injection molding prototypes can help avoid costly delays later in the production process. They also enable companies to test and validate their designs quickly, accelerating the development cycle.
Perhaps one of the most compelling advantages of injection molding prototypes is the seamless transition they provide from the prototype stage to full-scale production. The prototype plastic injection molding process uses the same materials, machinery, and tooling as the final production stage, which is an immense advantage when you’re aiming for production equivalency.
When it comes to rapid prototyping, both 3D printing and injection molding have their unique advantages. 3D printing, often associated with plastic prototype manufacturing, allows for quick turnarounds and is especially useful for low-volume production. It’s a go-to for many who wonder how to get a plastic prototype made in a short period of time. The process is direct: from a CAD model to a physical product without the need for molds.
The short answer: plastic injection molds cost anywhere between $100 for a 3D printed low-volume injection mold to $100,000+ for a complex multi-cavity steel mold for high-volume production, which generally represents the most significant fixed start-up cost in injection molding. However, as these costs get distributed among hundreds or thousands of parts, injection molding is an ideal process to mass-produce plastic parts affordably.
Material cost is defined by a model’s design, the material chosen, and the amount of material used to execute the injection molding process.
Download our white paper for guidelines for using 3D printed molds in the injection molding process to lower costs and lead time and see real-life case studies with Braskem, Holimaker, and Novus Applications.
Evaluate the model’s design to eliminate unnecessary features. This reduces the mold’s size and the material used to develop the model.
Product development is a complex process, often involving numerous iterations and extensive testing. An injection molding prototype can significantly streamline this process, providing a cost-effective way to test and refine designs before moving on to mass production.
Repair cost: Repair and maintenance tasks involve the replacement of defective parts and the use of tools to execute the maintenance process.
However, it’s important to note that while 3D printing is a powerful tool for prototyping, it may not always be the best choice for every project. Factors such as the complexity of the design, the required material properties, and the intended production volume should all be considered when choosing between 3D printing and traditional injection molding for prototyping.
CNC machining: CNC machines are the most commonly used tools for manufacturing aluminum and stainless steel molds with high precision levels. CNC machining removes material by a spinning tool and fixed part. Machining can produce molds where the cavity design is highly complex, but they might require multiple tool changes that can slow down the process, which means that costs increase in line with complexity. CNC machines are industrial tools that require a skilled workforce and a dedicated space, which means that many companies outsource mold production to service providers.
In today’s fast-paced market, speed is of the essence. Companies are under constant pressure to develop and launch new products as quickly as possible. Prototype injection molding can play a crucial role in reducing time-to-market.
In this guide, we provide an extensive breakdown of the different factors that make up the total injection molding cost.
Conceptually, an injection molding prototype serves as a critical step in the product development cycle. It’s a powerful tool for creating a physical product from a CAD model that mirrors the design and functionality of the final product. Building an injection molding prototype leverages the plastic mold prototype making process, incorporating a wide range of materials which aid in determining the viability of the design and its potential for mass production.
Tooling costs for injection molding are very high and depend on a number of parameters and design complexity. Molds for injection molding are normally CNC machined out of aluminum or tool steel, EDM machined to shape a workpiece, or 3D printed. The machined or printed part is then finished to achieve the desired standard. The finished mold consists of features such as the surface geometries needed for a part, a runner system to guide the flow of injected materials, and cooling channels to ensure the mold cools down quickly.
The prototype injection molding process allows for the creation of a physical product that can be tested for functionality, durability, and user experience. This hands-on testing can reveal design flaws or areas for improvement that may not be apparent in a digital model. By identifying and addressing these issues early in the development process, companies can avoid costly redesigns and production delays.
Once the mold is ready, it’s placed in the injection molding machine. Raw material, usually plastic, is fed into the machine, where it’s heated until it becomes liquid. This molten plastic is then injected into the mold under high pressure. As the plastic cools, it solidifies and takes the shape of the mold. The resulting cast is a plastic prototype, a physical representation of the product that can be tested for functionality and design.
Part design: Complex part designs with intricate geometries require complex molds to execute the project. Mold designs usually have 2 sides: sides A and B. Side A, also known as the cosmetic side, is usually the side seen by the user. Side A is expected to be smooth and aesthetically pleasing. Side B contains the hidden structures that support the usage of the part. Side B structure may include ribs, bosses, etc., and its finish is usually much rougher than that of Side A. Molds with complex Side A and Side B designs are generally more expensive to fabricate compared to simpler molds. Complex designs that feature undercuts might also require sliding side-actions and cores, increasing the cost of the mold.
Materials commonly used in injection molding include ABS, polycarbonate, nylon, and various types of polyethylene, each bringing its own set of properties to the table. ABS is known for its toughness and impact resistance, whereas polycarbonate is used for its excellent clarity and heat resistance.
ACIS®, Autodesk Inventor®, CATIA® V5,Creo™ Parametric, IGES, Parasolid®, Pro/ENGINEER®,Siemens PLM Software’s NX™, SolidEdge®, SolidWorks®, STEP
GETTING A QUOTE WITH LK-MOULD IS FREE AND SIMPLE.
FIND MORE OF OUR SERVICES:
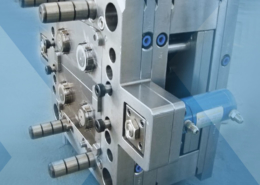
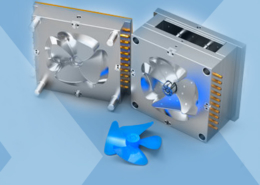
Plastic Molding

Rapid Prototyping
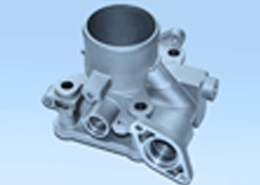
Pressure Die Casting
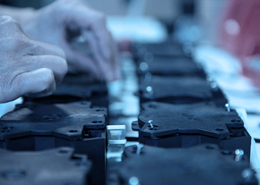
Parts Assembly
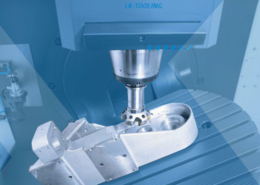