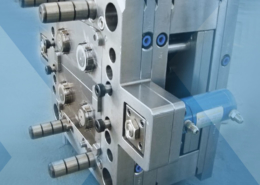
HDPE Moulding Essentials: Advantages in Applications - hdpe injection molding
Author:gly Date: 2024-10-15
Today, we use servo injection molding machine to accurately control the material flow; use high pressure water to control mold temperature; use dehumidifying dryer with dew point to eliminate moisture; use hot runner to reduce pressure loss and cost; use cavity pressure & temperature sensor to monitor the whole molding process etc., all these can help us to get more scientific. It is not enough to implement SIM that only know about them, because there are much more other tools like simulation/FEA, Minitab, TRIZ, DFSS, DMAIC etc. can make it more scientific.
What is scientific plastic injection molding? Scientific parameter setting? If the runner or the gate size is too small, for instance, the sink mark or warpage problem is still there no matter how excellent your process parameter is. So, the tooling design also be included.
A: The most common types of HDPE molding include injection molding, blow molding, and rotational molding. Each process is used to create different types of products with unique shapes, sizes, and properties.
You have a good tool, efficient cooling and gas venting, suitable and smooth movement structure, reasonable runner size and location etc. You implement scientific parameter setting, get the right drying temperature and time, get the right barrel temperature setting, completely know filling, packing, and holding. All your parameter settings are data and evidence based. But the crack issue, as an example, is still there. What happened? The reason maybe caused by melt flow hesitation, your plastic part wall-thickness here is too thin, and waiting for enough pressure to weld but meanwhile, it is cooling down. It shows that the SIM involves the plastic part design as well.
There are various types of HDPE plastics that are used for different applications, each with their own unique characteristics. Here are some of the most common types of HDPE plastics and their applications:
HDPE injection molding is a versatile manufacturing process that can be used to produce a wide range of plastic products with excellent properties and performance.
In summary, the various types of HDPE plastics have different characteristics that make them suitable for specific applications. HDPE HMW, Marlex 9006, DOW DMDA-8007 NT 7, and DOW DMDA-8907 NT 7 are all high-density polyethylene (HDPE) resins. They are commonly used in injection molding and blow molding applications due to their excellent processability, impact strength, stiffness, toughness, and environmental stress crack resistance (ESCR).
Sungplastic providers that offer custom HDPE plastic parts services. Our company uses HDPE injection molding to produce custom plastic parts according to our customers’ specific requirements.v. Here are some of the steps involved in custom HDPE plastic parts service:
All critical mentioned above points to plastic resin properties, temperature, melt flow, shrinkage, crystallization, orientation etc. To have a good part, not only the properties in plastic molding process, but also final part appearance and mechanical properties should be concerned. The most important is the heat resistance, chemical resistance, electrical properties etc. during the long-term use. Therefore, resin selection is the first and most important step, especially in insert molding and over-molding.
So, what is scientific injection molding do you think? In my view, it is to effectively prevent plastic defect caused by poor part structure design and poor mold design through in-depth understanding resin properties and selecting the right resin brand & grade with the lowest cost, rapidly find the root causes during mold try-run and then fix it. To achieve a robust and effective process, it also includes to remove the impact of inherent personal experience on products/molds/processes by way of using varieties of monitoring equipment and data analysis tools.
HDPE is a versatile material that is used in a wide range of applications across various industries. Some common uses of HDPE include:
Injection molded HDPE is a durable and versatile material with excellent chemical and weather resistance, making it suitable for a wide range of applications across industries.
An experienced and knowledgeable partner can help optimize the manufacturing process, reduce costs, improve quality, and accelerate time-to-market, resulting in a better outcome for the client.
1.Limited temperature resistance: HDPE has a relatively low temperature resistance compared to other materials, making it unsuitable for high-temperature applications. 2.Limited color options: HDPE is typically only available in a limited range of colors, which may not be suitable for all applications. 3.Difficult to bond: HDPE can be difficult to bond with other materials, which may limit its use in certain applications. 4.Limited mechanical properties: HDPE has limited mechanical properties compared to other materials, such as metals, which may limit its use in certain applications where high mechanical strength is required.
We offer a variety of manufacturing services: Rapid Prototyping, Tool Making, Injection Molding, Product Design and Development, CNC Machining and Metal Stamping. You can choose from a variety of plastics, silicone rubber, or metal for your product. Regardless of mass production or small batch customization, Sungplastic has always been committed to providing assured, efficient and more economical one-stop processing services for your projects.
HDPE injection molding is a manufacturing process that involves injecting molten HDPE material into a customized mold cavity. The molten HDPE material is then cooled and solidified,producing precise and high-quality plastic parts. HDPE injection molding process is known for its cost-effectiveness, speed, and ability to produce complex shapes and designs with high precision and consistency.
HDPE injection molding has a wide range of applications due to the unique properties of HDPE plastic. Some of the common applications of HDPE injection molding include:
High-density polyethylene (HDPE) is a type of thermoplastic polymer made from the monomer ethylene.It is a versatile material commonly used in the manufacture of a variety of products. HDPE is known for its high strength-to-density ratio, making it lightweight, strong, and durable.HDPE also has excellent chemical and weather resistance, making it suitable for use in severe environments. HDPE is a recyclable material with low environmental impact, making it a popular choice for sustainable manufacturing practices.
HDPE material properties may vary by specific grade and manufacturer. Injection molded HDPE material has some general properties:
By following these best practices, you can achieve high-quality HDPE injection molded parts with consistent properties and performance.
Is plastic injection molding a simple work? Yes, do not you see that anyone can inject a plastic part regardless of residual stress inside. Is it complex? Exactly it is, it is related to polymer science, fluid mechanics, material mechanics, metal technics, GD/T ……
A: Choosing the right HDPE molding technique depends on several factors, such as the shape, size, and complexity of the product, the required production volume, the material properties, and the cost.
Plastic Mold Manufacturing Plastic Injection MoldingRapid PrototypingCNC MachiningSheet Metal StampingPressure Die CastingSilicone & Rubber PartsSurface Finishing
There is no doubt that HDPE (High-Density Polyethylene) can be injection molded. In fact, injection molding process is one of the most common and widely used methods for manufacturing HDPE products. HDPE is a popular choice for injection molding due to its excellent strength-to-density ratio, chemical resistance, and ability to be molded into complex shapes with high precision and consistency. The process is also cost-effective, efficient, and capable of producing high-volume runs of identical parts. In short, HDPE injection molding is a versatile and efficient manufacturing method that is commonly used to produce a wide range of products, including packaging, automotive parts, medical devices, and more.
Sungplastic is a reputable manufacturer of high-density polyethylene (HDPE) injection molds and provides comprehensive HDPE injection molding services. Our experienced team of engineers and technicians work closely with our customers to understand their unique needs and provide solutions tailored to meet their specific requirements. We use cutting-edge technology and equipment to design and produce high-quality HDPE injection molds, consistently delivering reliable results. In addition to mold production, we also offer POM injection molding services that include the production of finished POM products such as gears, bearings, and other precision components. Our wide range of injection molded parts caters to various industries. At Sungplastic, we prioritize providing the highest quality products and services. We have strict quality control measures in place to ensure that every product leaving our facility meets the highest industry standards. Furthermore, we offer competitive pricing, guaranteeing our clients the best value for their investment. As your trusted partner for injection molding needs, Sungplastic is committed to excellence and customer satisfaction.
Sungplastic is a plastic product manufacturer with rich experience in injection molding. According to the different product development requirements, we flexibly adjust the manufacturing process to achieve high quality, high efficiency and more economical.
HDPE molding offers several advantages over other manufacturing processes. It allows for the production of complex designs and intricate shapes with high precision and consistency. It also offers high production rates and is ideal for large volume production runs. Additionally, HDPE molding is a cost-effective process, as it can reduce material waste and labor costs. 1.Versatility: HDPE is a versatile material that can be molded into various shapes and sizes, making it suitable for a wide range of applications. 2.Strength and durability: HDPE has a high strength-to-density ratio, making it strong, durable, and able to withstand harsh environments. 3.Chemical resistance: HDPE is highly resistant to chemicals, making it suitable for use in corrosive environments. 4.Recyclability: HDPE is recyclable and has a low environmental impact, making it a popular choice for sustainable manufacturing practices. 5.Cost-effective: HDPE injection molding is a cost-effective manufacturing process, allowing for the production of high-volume runs of identical parts.
Custom HDPE plastic parts service providers typically work closely with our clients throughout the entire process to ensure the finished part meets their specific requirements. We provide additional services such as material selection, design optimization and prototyping to help customers achieve the best results.
A: Challenges of HDPE injection molding include the hygroscopic nature of HDPE, the high melt viscosity of HDPE, and the high crystallization rate of HDPE.
HDPE (High-Density Polyethylene) injection molding is a manufacturing process that involves injecting molten HDPE material into a custom-designed mold cavity. The molten HDPE material is then allowed to cool and solidify, creating a finished plastic part.The process is also efficient, cost-effective, and capable of producing complex shapes and designs with high precision and consistency.HDPE molding offers several advantages over other manufacturing processes, including the ability to produce complex and intricate designs, high production rates, and consistent quality of the finished products. It is commonly used in the production of a wide range of plastic products, including bottles, containers, pipes, automotive parts, medical devices, and more.
GETTING A QUOTE WITH LK-MOULD IS FREE AND SIMPLE.
FIND MORE OF OUR SERVICES:
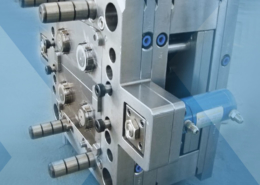
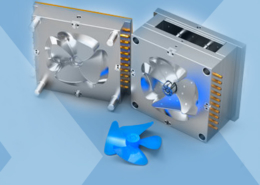
Plastic Molding

Rapid Prototyping
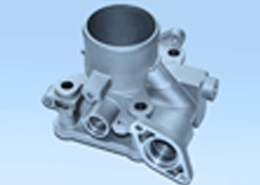
Pressure Die Casting
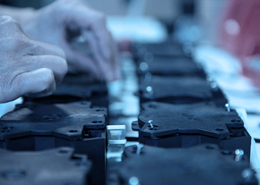
Parts Assembly
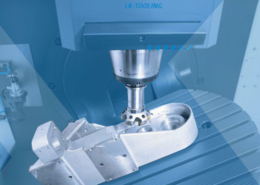