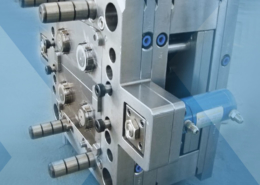
HDPE Injection Molding - polyethylene injection moulding
Author:gly Date: 2024-10-15
In assessing mold finish, SPI (Society of the Plastics Industry) Classes play a crucial role, with SPI Class 105 being the designated class for prototype quantities. However, SPI encompasses a range of mold classes, each tailored to specific production volumes:
One crucial aspect to remember is that 3D printing and injection molding have different design rules, including minimum wall thickness. Walls that are too thick, too thin, or non-uniform can often lead to failures in production injection molding. To avoid such issues, proto molds and prototype injection molding is recommended as it allows you to identify potential production challenges and make necessary adjustments.
The good news is that we offer expert Design for Manufacturability (DFM) assistance through 3D visualization for injection molded part design. Additionally, we provide an online checklist that can help you determine if you’re ready to transition from 3D printing to injection molding. It’s worth noting that you can request injection-molded samples even before your parts are fully production-ready, allowing you to evaluate the results and make any necessary refinements.
Plastic Mold Manufacturing Plastic Injection MoldingRapid PrototypingCNC MachiningSheet Metal StampingPressure Die CastingSilicone & Rubber PartsSurface Finishing
PH Molds further expands by adding a 6,200 square foot warehouse onto the building to accommodate the growing plastics business.
A major product developed by PH Molds along with one of our oldest customers, Homax Corporation, was reviewed by Popular science as the first marketable functional Power Painter Roller for the retail market.
Should any of this resonate with you, it’s time to reconsider your production and prototyping alternatives as well as unlearn some of the advice you’ve been given. Injecting plastic is indeed a high-volume manufacturing method. However, it can also be used for low-volume production and prototyping at times. It’s not simply aluminum vs. steel when it comes to injection molds.
One advantage of injection molding is the adaptability in choosing various mold materials. For instance, the base of proto molds can be crafted from aluminum or soft/semi-hardened steel, while the inserts may be made of soft, semi-hardened, or hardened steel. Additionally, if your mold requires movable components like lifters, these elements can also be fashioned from steel.
When your part design is still in its early stages, you might contemplate the use of more cost-effective commodity plastics, even if they do not possess the same mechanical properties as your intended production materials. As an illustration, consider PEEK, an engineering plastic frequently employed in medical devices. PEEK comes at a notably higher cost compared to other polymers and might involve a high minimum order quantity (MOQ) if your supplier does not purchase it in quantities substantial enough to secure a discount.
From his days in Marine school in Piran, Renato has never lost his love for the ocean. When he is not spending time with family, playing golf, or caring for his gardens, he will take every opportunity to get back to the ocean to enjoy some scuba diving and fishing. A passion both he and his son enjoy.
With increasing requirements in both mold manufacturing and injection molding, PH Molds built a 24,000 square foot facility in Pitt Meadows, BC where we are currently located.
Having always wanted to live in BC, Canada he decided to travel again and successfully immigrated to Maple Ridge, BC in 1976.
However, when it comes to works-like and pre-production prototypes, the scenario changes. Designers often necessitate part quantities in the tens rather than single digits. Depending on the volume required, it might be more economical to opt for injection molding instead of 3D printing, even though injection molding involves tooling expenses and isn’t the intended production process.
Are proto molds expensive? Yes, however as this article will show, there are ways to cut costs. Does it take a long time to make injection molds? You’ll be happily surprised to hear that the proper manufacturing partner can generate tooling in a matter of weeks, if you were expecting mold-making to take several months. Consider your part design, material choice, tooling costs, and machining times while keeping an overall perspective. Additionally, keep in mind that you can get assistance when you share the part design with us. For instance, our DFM specialists will recommend a higher draft angle if your design doesn’t have enough draft to ensure that your parts eject cleanly.
Is it absurd to use proto molds and prototype injection moulding? As most designers know, plastic injection molding is best used for large quantities of production-quality (i.e., non-prototype) items. It’s possible that you’ve also heard that aluminum injection molds are meant for smaller volumes, steel injection molds for larger numbers, and both kinds of proto molds are too costly.
In February of 1979, Renato Paulic joined a small one-man Tool and Die shop in Vancouver, BC. This was PH Molds. Within a few months, Renato negotiated to purchase the company. He incorporated it and PH Molds Limited begins. With Renato’s drive and experience in injection mold manufacturing, we go from a small Tool Maker specializing in packaging molds to a full-service technical manufacturer of plastic products.
In summary, the selection of mold materials and the consideration of SPI classes play a pivotal role in achieving your goals for proto molds and prototype injection molding, allowing you to strike the right balance between cost, tolerances, and production volumes.
Additionally, the file formats used in 3D printing and plastic injection molding differ. 3D printing relies on STL files, which define objects as a triangle mesh, while injection molded parts are typically defined using CAD files that are parameter-driven. To utilize 3D printing files for injection molding, a conversion process is required to transform the mesh into a shape and then into a solid.
Mat decides it is time to leave his engineering career with Engel and join the family business with a plan of succession for taking over the reins.
Renato, a proud Canadian citizen, was born and trained as a Tool Maker in Maribor, Slovenia. With his desire to explore the world he decided to emigrate to Australia in 1968. It was in Australia that he began to really learn his trade of Mold Making.
Over the next seven years,he worked with Diecraft Australia, a division of Tupperware Company International, British Plastics, a large molding operation making household plastic products and Fisher Tool and Die Company Mold Maker supplying injection molds to the Australian Automotive Industry, GM Holden and Chrysler.
As a manufacturer with 20 years of manufacturing experience, at Sungplastic we can assist you with the entire product lifecycle, from prototyping to manufacturing. You may use the procedure that you need when you need it because we provide a wide range of capabilities through a single platform, including 3D printing, CNC machining, and injection molding. We offer comprehensive services to clients worldwide, and we are able to create intricate components—including proto molds and prototype parts and products—to meet particular requirements.
Aluminum vs. Steel MoldsThe choice of mold material is of paramount importance. While aluminum is the most cost-effective option, it may not deliver injection-molded parts with the tight tolerances required for precision applications. Steel molds, on the other hand, excel in achieving precise tolerances, with the capacity to machine to tolerances as tight as +/-0.001 inches, a marked contrast to aluminum’s typical +/-0.005 inches.
As a part of our long-term succession planning, Mat, Renato’s son, joins PH Molds as a Molder to learn injection molding processing after completion of his Control Systems Technology Diploma. To further gain valuable experience, Mat leaves to join Engels’ Service Training program in Ontario after a year as a molder.
After working in the local Mold Making industry for three years he purchased a small one person Tool Room in Vancouver. This was PH Molds.
PH Molds develops a strong relationship with Richards Packaging which leads to the forming a partnership for the manufacturing of single stage injection stretch blow PET containers. Richards adds an Aoki machine to PH Molds production floor and runs it exclusively for Richards.
PH Molds finds its strength in the market with injection molding. Plastics manufacturing quickly became our primary business.
For a works-like prototype, you may opt for a less expensive material, such as polyphenylsulfone (PPSU), which can be a suitable choice. However, it’s important to note that selecting a material other than PEEK might not offer a comprehensive assessment of your part’s moldability. Given that both PPSU and PEEK are available as 3D-printing filaments, you might explore the possibility of utilizing additive manufacturing instead. This approach not only reduces tooling costs but also grants you the flexibility to use your preferred plastic material. It seems straightforward, doesn’t it?
An additional 5,200 square foot warehouse was added to accommodate demands. PH Molds continues developing its reputation as a technical molder through further growth of plastics production, increasing use of engineering resins and involvement with complex products.
While this may be promising, it’s crucial to recognize that achieving perfection in 3D-printed proto molds doesn’t guarantee a smooth transition to equally flawless injection-molded parts. The production process can introduce new challenges and variables that demand a comprehensive evaluation, emphasizing the significance of thorough testing and validation.
The maturity of your part design plays a pivotal role in determining the next steps. If you haven’t reached the manufacturing phase, chances are you’re still immersed in the prototyping stage. But the type of proto molds you require depends on your specific objectives:
Proto molds or Prototype injection molding and production injection molding share the ability to utilize the same plastics. However, it’s crucial to be aware that certain abrasive materials, such as glass-filled nylon, can accelerate wear and tear on proto molds. This is primarily because proto molds are typically crafted from softer materials. Nonetheless, if your intention is to prototype 100 parts, the issue of wear becomes less critical compared to the wear and tear associated with a full-scale production run of 10,000 parts.
Continuously looking for better opportunities PH travels to India in search of Tool Rooms. After an exhaustive and interesting trip, we decide to continue working with our Asian Tool Maker.
Tolerances, which refer to the allowable part-to-part variations, also differ between 3D printing and injection molding. Most additive manufacturing technologies have dimensional tolerances of at least 0.1 mm, resulting in greater deviations compared to injection molding. Moreover, injection molding typically involves two types of tolerances: commercial and fine.
Soft and semi-hardened steel molds, despite being pricier than aluminum, offer an excellent compromise for proto molds. These steel variants can attain tighter tolerances while remaining reasonably easy to machine, reducing the time required for tool creation, often within a timeframe of 10 to 14 days.
Here was the opportunity needed to allow PH Molds to make the jump to injection molding. PH Molds bought its first small 28 ton Engel machine, built a Honey Bear Cap mold, began producing Honey Bear Caps and launched itself into the injection molding business!
In response to the needs of our customers and increasing global competitiveness, we travel to China to visit and select a mold-making partner for lower cost molds. Having visited over twenty molders we successfully secure a quality Asian tool maker.
We travel again to China and now Taiwan to evaluate a possible source of higher quality Tool Making suppliers. After a successful trip, we decide to begin working with a new supplier in Shenzhen, China.
However, this approach may not always fulfill your requirements. 3D-printed materials do not replicate the end-use properties found in their injection-molded counterparts. For instance, 3D-printed PEEK may not possess the same level of strength as injection-molded PEEK. In situations where your part is intended for use in a medical device, obtaining representative samples for the first article inspection (FAI) becomes imperative.
Precision in Gate Selection and Mold FlowLastly, proto molds and prototype injection molding is designed to ensure that your mold incorporates the appropriate gate type and location. This guarantees even filling of the mold cavity and the application of adequate pressure to yield parts with consistent quality. While mold-flow-analysis software can be utilized, proto molds and prototype injection molding offers a tangible, real-time solution to place the finished part directly in your hands, making it a valuable choice for rapid prototyping.
It’s important to consider the differences in design rules, part features, and tolerances between 3D printing and injection molding. These factors play a significant role in the success of production injection molding and can impact the quality and functionality of the final parts.
Alenka Middleton, Renato’s daughter, joins the company as Vice President & CFO after a twenty year career in finance and leadership.
For many proof-of-concept and looks-like prototypes, the expenditure on an injection-molding tool may not be justified. Typically, in these early stages, designers only require a limited quantity of one or two parts. The cost of an injection mold, when divided among such a small production run, often makes it an impractical choice.
For 3D Printed Prototypes:3D proto molds appropriate for evolving designs in the conceptual phase.Suited for very low quantity requirements.Lead times typically range from 1 to 15 days.
Hardened steel is typically reserved for production molds, given its greater durability (i.e., more cycles) and the ability to achieve stringent tolerances. For applications demanding tight tolerances, such as in the medical or aerospace sectors, aluminum falls short.
With Renato’s significant experience in injection mold manufacturing, he begins branching out and started producing injection molds. It was during this time that he began exploring the idea of expanding PH Molds to take on injection molding.
For Injection-Molding Prototypes:Proto molds Ideal for finished designs that demand real-world testing.Best for prototype quantities exceeding 100 pieces.Lead times typically span 2 to 5 weeks.
Now, consider the concept of design for manufacturability (DFM), a process that focuses on designing parts for ease of manufacturing. Let’s say you 3D print certain components and assemble them seamlessly, allowing you to test the product’s functionality effectively.
PH Molds incorporates. Finding a high demand for packaging molds, we begin specializing in the manufacturing of blow molds for the packaging industry. Within a year we grew to a staff of five Tool Makers.
Having built many molds, Renato developed a strong relationship with a large local blow molder. While working with this blow molder, a honey packager came to them looking for a new idea for packing honey. This lead to one of the first Honey Bear blow molds ever seen on the market and this mold was built by Renato!
Requiring a larger space for mold manufacturing and needing a dedicated space for more injection molding PH Molds moved to a much larger 4,000 square foot facility in Maple Ridge, BC, a suburb of Vancouver.
When it comes to proto molds, the choice of materials goes beyond the traditional steel versus aluminum debate. While production molds can be constructed from either steel or aluminum, the versatility extends to proto molds, which can also be fashioned from both steel and aluminum, with variations within each category.
The most effective way to obtain these representative samples is by employing the same material and production process you intend to use for full-scale production, which typically involves injection molding. If you have any questions or uncertainties regarding your part design, our team of Design for Manufacturing (DFM) experts is readily available to provide you with further information and
Many of PH Molds’ committed employees have been with the company long enough to share in its ongoing growth and the changes that have occurred over the years.
With the ongoing growth of value-added services, PH Molds converts a portion of the warehouse to a two floor dedicated 3,600 square foot area for our pad printing and assembly.
Consider this scenario: molding one proof-of-concept prototype versus crafting 100 pre-production prototypes, both requiring a $10,000 tool. The per-part tooling cost for one proof-of-concept prototype is $10,000, while for 100 pre-production prototypes, it’s a significantly reduced $100—a substantial cost differential.
While these categories aren’t the only way to classify prototypes, they provide a structured framework for the discussion of proto molds that follows.
Master Unit Die (MUD) inserts, featuring a standard mold frame with customizable, removable inserts, provide a cost-effective alternative for initial tooling, potentially reducing costs by up to 66%. Despite the cost savings, MUD molds maintain the complexity often needed for proto molds designs, allowing for efficient modifications to the insert in response to design changes.
PH Molds is proud to deliver high-quality service with technical expertise, prompt product completion and competitive prices to customers in Metro Vancouver, British Columbia and worldwide.
When comparing 3D printed prototypes with injection-molded counterparts, several key factors should guide your decision:
It was during this time that Renato began seeing global competitiveness with countries like China. With the experiences gained over his career, he began working more with customers who required more technical support in the development of their products and higher quality plastics manufacturing. PH began taking on more engineering projects of complex assemblies.
PH Molds further expands it assembly value-added services with the creation of an assembly department to support the growing needs of its customers.
GETTING A QUOTE WITH LK-MOULD IS FREE AND SIMPLE.
FIND MORE OF OUR SERVICES:
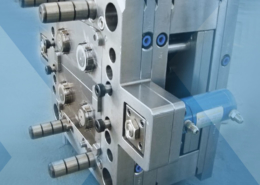
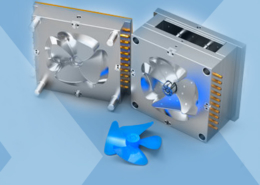
Plastic Molding

Rapid Prototyping
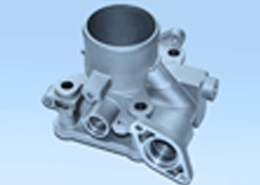
Pressure Die Casting
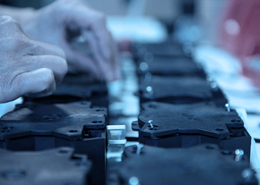
Parts Assembly
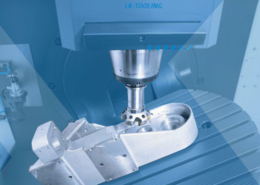