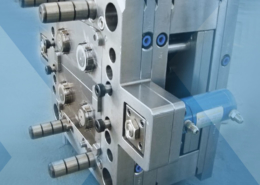
Plastic Molding for Wire 1 2: Revolutionizing Wire Management
Author:gly Date: 2024-06-08
Wire management is a crucial aspect of various industries, from electronics to automotive. The efficiency and effectiveness of wire management can significantly impact the overall performance and safety of systems. In recent years, plastic molding for wire 1 2 has emerged as a revolutionary solution to address the challenges associated with traditional wire management methods. This article explores the significance of plastic molding for wire 1 2, its applications, benefits, challenges, and future prospects.
Introduction: Embracing Innovation in Wire Management
In a rapidly evolving technological landscape, the demand for efficient wire management solutions has never been greater. Traditional methods, such as cable ties and conduits, while functional, often present limitations in terms of flexibility, aesthetics, and durability. Plastic molding for wire 1 2 offers a paradigm shift in wire management, providing customizable, cost-effective, and versatile solutions that cater to diverse industry needs.
Applications Across Industries
Plastic molding for wire 1 2 finds extensive applications across various industries, including automotive, aerospace, telecommunications, and consumer electronics. In the automotive sector, molded wire harnesses enhance the reliability and longevity of electrical systems, ensuring optimal performance and safety standards. Similarly, in aerospace and telecommunications, molded wire assemblies offer lightweight yet robust solutions for complex wiring configurations.
Benefits of Plastic Molding for Wire 1 2
Enhanced Durability and Protection
Plastic molding provides superior protection for wires against environmental factors such as moisture, heat, and mechanical stress. By encapsulating wires within durable plastic enclosures, the risk of damage or corrosion is significantly reduced, prolonging the lifespan of electrical components.
Customization and Flexibility
One of the key advantages of plastic molding is its ability to accommodate complex geometries and configurations. Manufacturers can tailor the design of molded wire assemblies to meet specific requirements, optimizing space utilization and minimizing installation time.
Cost Efficiency
While the initial investment in plastic molding equipment may seem substantial, the long-term cost savings are considerable. Molded wire assemblies eliminate the need for additional components such as brackets and fasteners, streamlining the manufacturing process and reducing overall material costs.
Challenges and Considerations
Material Selection
Choosing the right plastic material is crucial to ensure compatibility with the intended application and environmental conditions. Factors such as temperature resistance, chemical resistance, and electrical insulation properties must be carefully evaluated to prevent performance issues or safety hazards.
Design Complexity
Complex wire harness designs may pose challenges during the molding process, requiring advanced techniques and specialized tooling. Design engineers must collaborate closely with molders to optimize the manufacturability of intricate wire configurations without compromising quality or functionality.
Quality Control
Maintaining consistent quality standards is essential in plastic molding for wire 1 2 to ensure reliability and performance. Rigorous testing protocols and inspection procedures are necessary to detect any defects or imperfections that could compromise the integrity of the molded assemblies.
Future Outlook and Recommendations
As technology continues to advance, the evolution of plastic molding for wire 1 2 is poised to accelerate, driven by innovations in materials, processes, and design methodologies. To capitalize on this potential, stakeholders must prioritize research and development efforts aimed at enhancing product performance, sustainability, and cost-effectiveness.
In conclusion, plastic molding for wire 1 2 represents a transformative approach to wire management, offering unparalleled versatility, durability, and efficiency. By embracing this innovative solution and addressing associated challenges, industries can optimize their operations, improve product quality, and drive sustainable growth in the digital age.
GETTING A QUOTE WITH LK-MOULD IS FREE AND SIMPLE.
FIND MORE OF OUR SERVICES:
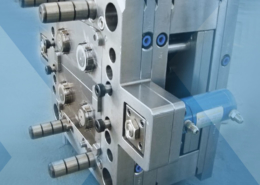
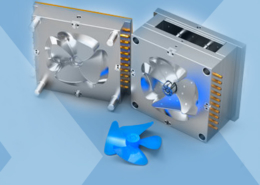
Plastic Molding

Rapid Prototyping
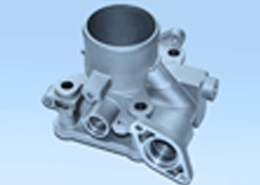
Pressure Die Casting
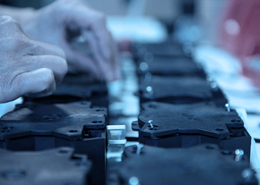
Parts Assembly
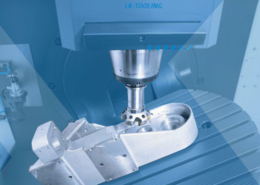