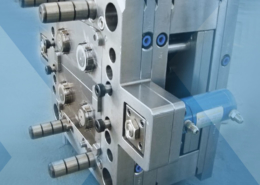
HDPE Injection Bulky Rigid Plastics - hdpe injection
Author:gly Date: 2024-10-15
To simplify the tooling process, IMS engineers utilize the principles of Design for Manufacturing (DFM). By employing intelligent mold design strategies, we can achieve complex geometries using simple precision tooling methods. Our goal is to engineer cost-effective tooling solutions while maintaining the highest levels of precision and delivering on customer requirements. By collaborating closely with toolmakers, we guarantee that the tooling is precisely crafted to meet the specific requirements of each project. We also perform routine maintenance and upkeep on each precision mold to ensure mold longevity.
The future outlook for rapid injection molding in the manufacturing industry is promising. As technologies evolve and demand for faster, more efficient production continues to rise, rapid injection molding will remain a crucial tool for innovators and manufacturers alike.
Rapid injection molding stands out for its ability to streamline the journey from conceptual design to finished product, offering plenty of advantages.
Heat staking is another permanent bonding technique. This bonding concept takes advantage of the base material being malleable plastic. The base material is heated up and the plastic reformed using a combination of heat and pressure to model the plastic around the second piece forming a hardware-free bond. One advantage is that we can use it to combine two alike or dissimilar materials. Also, it is a reasonably easy bonding process that does not require any additional parts or materials.
Plastics are a growing industry that is becoming prominent in the healthcare sector. The medical industry is establishing a foothold in plastic 3D printing as a modern solution. Plastic molds help doctors to see a CT scan in 3D physically. The dental occupation often uses 3D plastic molds to custom fit parts before surgery. Research suggests that Medical grade polymers used in healthcare will positively impact growth in the medical field over the next decade.
Electronics are still a leading sector in the use of plastic resin parts. Plastics do not conduct electricity. Electronics often need plastics to insulate the electricity running through them. Consequently, a plastic part can make the perfect insulator for electronics and electrical devices. Plastics also have a lower conductivity for heat. Meaning, that plastics do not transfer heat well due to their insulating properties. This particular property works to the advantage of the plastics industry when it wishes to shield heat from other more delicate parts or the user. You may also treat plastics with special flame retardant finishing applications to further support their fire-resistant properties.
Selecting the right partner is crucial for the success of your rapid injection molding project. Here are key factors to consider:
Precision begins with the design phase. Our engineering team thoroughly reviews part drawings, evaluating them for molding and tooling issues. We examine features that may pose challenges for molded plastic, such as undercuts, texture requirements, draft angles, and thickness. By addressing these concerns early on, we ensure that the final design will meet the required form, fit, and function while optimizing the manufacturability of the part.
To provide customers with a clear understanding of the final product, IMS employs advanced 3D printing technology. Our precision 3D printers produce prototypes that closely resemble the actual model dimensions. This allows customers to visualize and test the part’s form, fit, and function before moving into production. In alignment with our goal of customer satisfaction, IMS utilizes the highest quality 3D printers to deliver prototypes with tight dimensional tolerance.
Lastly, rapid injection molding allows companies to respond swiftly to market changes. Whether adjusting to new consumer preferences or incorporating the latest technological advancements, this process supports dynamic adaptation, ensuring businesses remain relevant and competitive.
During the FAI process, we utilize the Cp/Cpk (Process Capability Analysis) method to assess the precision and consistency of the parts. By running our own sample lot and checking the primary dimensions of each sample injection molded part, we can determine the mold’s capability to produce parts that meet the desired specifications. Our target Cp/Cpk value is greater than 1.33, and we are proud that our regular results exceed this threshold, ranging from Cpk 2.5 to 3. This level of consistency assures our customers that each plastic part will be consistently produced with the utmost precision.
Before proceeding to production, IMS experts conduct thorough tool verification and First Article Inspection (FAI). The toolmaker runs samples and ships them to IMS for evaluation. We measure the tolerances of these samples to ensure that the injection mold can consistently produce precision plastic parts within the given requirements. Once the customer approves the samples, the mold is shipped to our facility for FAI.
In a nutshell, you can get your injection molded plastic part within a short span of time to market. To get the best quality of Rapid Injection Molding Services, get in touch with 3ERP for a free quote. We’ll gladly offer advice about your best options. Combining our expertise, engineering capabilities, and advanced technology we can offer rapid tooling solutions
A direct consequence of the process’s speed and efficiency is a substantial reduction in time to market. Companies can swiftly move from concept to commercialization, gaining a competitive edge in fast-paced markets. This agility is crucial for responding to consumer demands and market trends.
Below are 8 key industries that significantly benefit from rapid injection molding, showcasing the diverse applications and use cases of this innovative technology.
To demystify the process, it’s crucial to break down the main stages involved in rapid injection molding. Each phase plays its role in ensuring the final product meets the specified requirements with precision:
They are capable enough to manufacture anywhere from a few parts to thousands. There are many manufacturers who use this process for producing molding parts as per their client’s requirements. Most essentially, this is the most convenient way to meet the client’s needs and specifications effectively sans hassle.
In order to maintain the highest standards of quality, IMS utilizes the concept of Acceptable Quality Limits (AQL) based on Mil standard 105D. AQL is a heavily utilized sampling plan across our manufacturing processes. It enables us to conduct Out of Box Audits (OAB’s) and statistically assess the quality of finished products. By referring to the AQL chart (see below), we determine the number of parts in a lot that need to be tested to ensure compliance with quality standards. This rigorous sampling plan allows us to identify any potential deviations and take corrective actions promptly, ensuring that our products consistently meet the desired level of precision. By employing AQL, IMS further strengthens our commitment to making parts right the first time and upholding our reputation for delivering precise, high-quality plastic components.
Specialize in CNC machining, 3D printing, urethane casting, rapid tooling, injection molding, metal casting, sheet metal and extrusion
Our commitment to precision extends to our production processes. We employ proactive Quality Assurance (QA) techniques to prevent defects and rejections. By identifying potential risks and areas of improvement, we ensure consistent and high-quality production. Our operators perform regular inspections throughout the production run, and we conduct maintenance on molds and injection machines to ensure longevity and precision.
The process offers remarkable versatility, accommodating a wide range of materials and design specifications. Whether you’re working with engineering resins, ABS, polypropylene, or polycarbonate, rapid injection molding meets diverse material requirements. Additionally, it supports complex designs, ensuring that the final parts meet precise specifications.
Although there is always a premium to pay for an exceptionally speedy turnaround, rapid injection molding is quite affordable as compared to the traditional process. The cost is of it inexpensive than might be expected owing to the automation procedure of this sort of mold making.
The precision of rapid injection molding leads to minimal waste production, aligning with sustainable manufacturing practices. The efficient use of materials not only conserves resources but also reduces the overall environmental footprint of the manufacturing process.
At Integrated Molding Solutions, we deliver precision plastic injection molded parts to your door. IMS provides innovative plastic solutions offering guidance and help for small and large businesses alike.
The cost-effectiveness of rapid injection molding depends on the project scope. For low to medium volume productions and prototyping, it’s often more cost-efficient than traditional methods due to lower tooling costs and faster turnaround times.
Mechanical fasteners have the distinct advantage of offering disassembly and reassembly. Components include screws, nuts, bolts, rivets, pins, and inserts are examples of mechanical fasteners. Tapping is a process used to place threading inside a plastic injection molded hole. Advantages mechanical fasteners provide are a stronger, longer-lasting bond, durability, and disassembly. When you need to ensure the strength of the hold, mechanical fasteners are likely the correct choice.
Ultraviolet (UV) bonding is another permanent bonding process. The ultraviolet bonding process carries the advantage of bonding plastics to other materials such as glass, ceramic, and metal. Bonding using ultraviolet light is a highly intense concentration of ultraviolet lighting that instantly dries or cures the adhesive. Moreover, UV bonding works in seconds to bond plastic components with other materials. A solid bond forming in moments lessens production time and often reduces rates.
Tapping and threading make for easy disassembly. Both processes produce threads on a part. “Threads” means a small threadlike ridge or groove. Tapping and threading both create threaded surfaces. The threading process makes threads on the outside surface. Like a bolt or screw, for example. Similarly, tapping creates threads inside a hole, such as a nut. Threading is performed with a die tool, while tapping uses a tapping tool. When opposite features come together, the threads interlock.
Rapid injection molding is a type of injection molding designed to produce parts quickly and efficiently, bridging the gap between initial prototypes and mass production. It is exceptionally suited for generating anywhere from a few units to 10,000 parts within a matter of weeks. It embodies the intersection of speed and accuracy, making it a go-to choice for companies across various industries.
Our injection molding process is guided by an unwavering commitment to precision and consistency. Customer satisfaction is our primary goal, and we ensure that the tools and processes we use serve that goal. We utilize hydraulic and hybrid hydraulic electric machines that offer exceptional precision, as opposed to an injection molding machine focused solely on speed. By leveraging our expertise in process control and material behavior, we can achieve precise and consistent results.
Rapid injection molding method is revolutionizing how products come to life, blending efficiency and speed with engineering. This process makes it possible to manufacture many durable consumer and industrial items cheaper than everything else. It produces around 32% of plastics by weight.
Rapid injection molding is cost-effective, especially for low to medium volume productions. The use of aluminum molds, which are less expensive and quicker to manufacture than traditional steel molds, significantly reduces upfront costs. This affordability enables companies to manage their budget more effectively while still achieving high-quality outputs.
Rapid Tooling: Offers a cost-effective solution for producing molds for injection molding, especially beneficial for short production runs and prototyping. This application is crucial for industries that require molds quickly to test market reactions or to start production of parts without the delays associated with traditional tooling methods.
While both processes share the core principle of injecting molten material into a mold, rapid injection molding is distinguished by its speed and flexibility. Standard injection molding is typically geared towards high-volume production, necessitating more extensive tooling and setup time. In contrast, rapid injection molding focuses on accelerating the production process, making it ideal for short runs and tight deadlines.
The automotive industry is controlling fuel efficiency by switching to lightweight plastics. Using plastics for many auto parts reduces the vehicle’s overall weight and increases fuel efficiency. With the need for better fuel economy solutions, the automotive business has turned to plastics manufacturing for many automotive components. Additionally, government regulations recently are pressing the automotive industry to move from iron and steel to plastics. This push from the government is shifting the automotive industry towards higher-grade plastics in place of metals. The recent drive for a plastic manufacturing process in the automotive segment allows us to anticipate that injection molded plastics will increase rapidly under these new regulations.
One of the most significant advantages of rapid injection molding is its unmatched speed and efficiency. The process allows for the swift development of prototypes, facilitating a faster transition to production stages. This rapid progression is crucial for beating competitors to market and testing concepts without costly delays.
Rapid injection molding provides unparalleled flexibility in product development. Design changes can be quickly implemented without significant cost penalties, allowing for iterative design improvements. This adaptability is essential for optimizing product design and functionality.
Yes, rapid injection molding can manufacture complex parts. Advanced mold design and manufacturing technologies, like 3D printing and EDM, allow for intricate features and precise tolerances, making it ideal for complex components.
Integrated Molding Solutions understands that precision and consistency require skilled operators who are well-versed in the intricacies of the molding process. To ensure that our team meets the highest standards of expertise, we provide comprehensive training programs for our employees. Through these programs, our operators receive in-depth knowledge about injection molding principles, machine operation, mold maintenance, and quality control procedures. We also offer opportunities for our employees to become certified operators, equipping them with the necessary skills and knowledge to handle complex molding projects with precision and efficiency. By investing in training, certification, and continuing education, we empower our team of industry veterans to deliver exceptional results and uphold the utmost precision in every aspect of our operations.
At its core, rapid injection molding involves injecting thermoplastic resins into a mold at high pressure, which then cools and solidifies to form the desired part. This technique is renowned for its speed, which does not compromise the quality or the versatility of the produced parts. Whether for prototyping or small to medium-sized production runs, this method stands out for its ability to deliver reliable results swiftly.
In the event of a defective plastic part, we implement reactive Quality Control (QC) measures. We employ a corrective action process, starting with a corrective action report to contain the issue and prevent further defective parts from being released. Through root cause analysis, we identify the underlying cause of the defect and implement the necessary corrective solutions, such as process adjustments or molding machine operator training. This information is then fed back into our Quality Assurance system to further refine our precision plastic injection molding process and maintain the highest level of dimensional accuracy in each plastic component we manufacture.
From the very beginning of a project, IMS engineers identify the key parameters required to establish and maintain consistency throughout the manufacturing process. We adjust injection mold temperature, material temperature, injection speed, and injection pressure to optimize the mold cavity filling and ensure the parts come out exactly as intended and avoid pitfalls like sink or shrinkage. Our mastery of process control and material behavior allows us to minimize unnecessary post-processing requirements, such as trimming, and deliver high precision parts that meet the strictest tolerances. For necessary post-process treatments like assembly, painting, or fastening, IMS upholds our precision injection molding standards.
Precision is a crucial element in the world of manufacturing, and IMS engineers have the expertise to achieve precision consistently. When it comes to plastic injection molding, precision is often required for the form, fit, and function of a plastic product or part. At IMS, we specialize in precision injection molding, employing state-of-the-art technologies and our years of experience to deliver consistent, high-quality plastic parts. Our precision-focused approach includes design for manufacturing (DFM), tooling, production processes, and quality assurance and control.
Molds for rapid injection molding differ significantly from those used in traditional injection molding, mainly due to the focus on speed and flexibility.
These two forms of painting apply color to the part. The painting application is ideal after molding. Painting can be any color or even metallic finishes painted over plastic. This application also helps with particular requirements such as non-static parts. In comparison, pad printing permanently places an image onto the components. Pad printing is similar in nature to a rubber stamp. An inverted image is coated with paint and laid against the part to transfer the image to the part’s surface.
Insert molding is a systematic process of modeling thermoplastic material around an additional component. Most pliable thermoplastic resins are suitable for the insert molding process. The added piece is often a metal part. The main advantage of mold-in inserts is that generic threaded inserts are readily available in standard sizes. Generic inserts help keep costs down and avoid further customization costs. Metal inserts provide properties that plastic alone wears down over time, such as threading.
Central to rapid injection molding is a range of specialized equipment, each serving a critical role in the creation of high-quality parts, tooling and prototypes.
At Integrated Molding Solutions, precision is at the core of everything we do. From the initial design phase to the production process and quality control, we strive for consistency and accuracy in delivering high quality plastic parts. By employing cutting-edge technologies, adhering to rigorous quality control standards, and leveraging our expertise in material behavior and process control, we ensure that every part meets the required specifications. Partner with IMS for precision injection molding services that meet your needs, and experience the difference that true precision can make in your molded parts and products. Contact us today for additional information.
Embracing rapid injection molding is a strategic decision that can significantly enhance your product development process.
Electroplating or electro-deposition is a process whereby a metal material coats the surface of a part. In the electroplating process, a permanent bond connects the metal to the surface of another piece. The process involves an electrolyte or plating bath charged with electricity. The electricity-charged bath deposits small particles of the metal over the part’s surface. Therefore, this process effectively coats the plastic piece in a completely shiny, smooth metal finish.
Rapid injection molding represents a significant advancement in manufacturing, offering speed, flexibility, and high-quality production.
Absolutely. By utilizing high-quality materials and precise manufacturing processes, rapid injection molding produces parts that meet or exceed the durability and performance standards of traditional injection molding methods.
Achieving precision and consistency is paramount in manufacturing. Rapid injection molding excels in producing parts with tight tolerances and uniform quality. This precision ensures that every part functions correctly, meeting or exceeding the performance standards set by the project.
GETTING A QUOTE WITH LK-MOULD IS FREE AND SIMPLE.
FIND MORE OF OUR SERVICES:
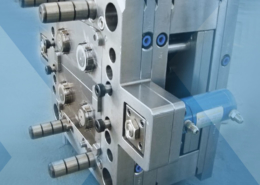
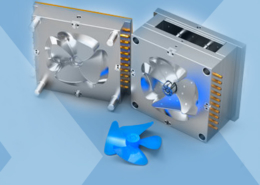
Plastic Molding

Rapid Prototyping
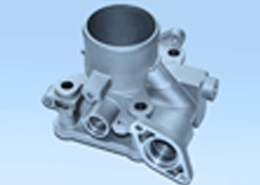
Pressure Die Casting
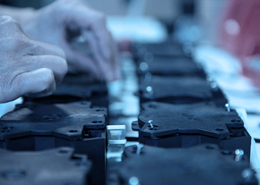
Parts Assembly
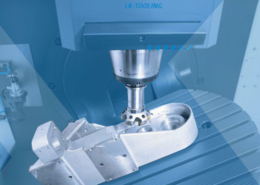