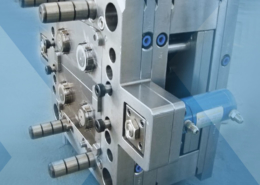
Haitian Injection Moulding Machines - haitian injection molding
Author:gly Date: 2024-10-15
For the manufacturing of more complex and complicated molds, an expensive process is used which is EDM. There are two types of molds, single cavity mold and double cavity mold and they used according to per need.
After working on product design now move to engineering phase of productions. The parts have to be engineered so they can be easily produced in steel or metal dies. The parts are drafted and designed so they can easily cool and ejected from molds. In this process engineers have to set the wall thickness and proper design so that plastic or acrylic prototypes don’t get trapped while ejection. There should be proper place for gate, injection of molten material and to analyze the proper flow of molten material after injection. In short, an engineer has to design a proper channel to make successful prototype.
Our high-quality, Italian-made Babyplast machines are specifically designed to offer the precision that’s necessary when working on small-scale parts. They have precise temperature and pressure controls for maximum efficiency, while using steel tools that on average are 40% less expensive than full-sized ones. This is just one of the many reasons why our micro molding services are a cut above.
Get 7-day standard lead times on simple parts between 0.5 in. x 0.5 in. and 4 in. x 3 in. Upload your part to see if it’s eligible.
Before PMMA prototypes, prototyping was a difficult task and it requires a lot of effort and expenses to fabricate a metallic prototype and poly-carbonate that which is harmful for human health as it has bisphenol-A. PMMA or acrylic is now in demand for fabricating flexible, light weight and scratch-resistant prototypes.
In last the everything is ready for injection of molten material but it works well less often for first time. Everything needs to be checked and adjusted properly so that it work perfect in first run.
PMMA parts can be made from both injection molding and traditional machining process, but injection molding has several advantages as compared to traditional machining which is given below
If you are looking for prototype in urgent and in haste then go for 3D prototyping but if you need functional and reliable parts then you should go for plastic injection molding. It is long stand assumption that when it comes to high volume production, injection molding is very expensive and non-reliable process while for prototyping or low volume production injection molding is suitable and reliable option.
At Wayken, we also excel at plastic optics and specialize in clear optical prototyping which is often the method of choice due to its rapid production, no waste material, ability to make complex parts and superior product finish.
PMMA prototypes are in demand for any industry looking to come up with a stronger and cheaper alternative to expensive and brittle glass. PMMA material is perfect substitute of glass and very feasible then glass. Security barriers, LCD screens, windows, tanks, medical devices and lenses – all incorporate the use of PMMA instead of glass. With many industries choosing PMMA over other materials for its products, there is a significant rise of PMMA prototypes in the recent decade.
Before diving deep into the topic, there is a need to understand what is PMMA and injection molding. PMMA is abbreviation of (poly-methyl methacrylate) and it is commonly called as acrylic. Although it as different other names like plexi-glass, Crylux, Acrylite, Lucite and many other. The demand of acrylic glass is increasing in manufacturing industry day by day because of its properties.In the modern Industrial era , Pmma (Acrylic) has been widely used in many applications due to its natural transparency & clarity and the impact resistance of certain variants, including lenses, acrylic nails, paint, security barriers, medical devices, LCD screens, furniture, windows, tanks, and enclosures around exhibits.
Is micro molding right for your next product development project? Contact our manufacturing specialists for a free quotation and design review. We can recommend the solution that best fits your schedule, order volume, material, performance requirements and more.
Micro injection molding is a specialized form of plastic injection molding, focused on next-generation parts that need to be small but still retain tight tolerances and complex features. Many product developers don’t know that smaller parts can be made faster and cheaper on small machines.
To grasp the attention of people, different automobile companies, manufacturing companies, furniture showrooms showcase their models made up of PMMA material because of futuristic looks of PMMA and PMMA material properties.
In injection molding process, material is first liquefied and change into molten form at high temperature and then injected into metallic dies under high pressure and then it id allowed to cool. After sometime, it gives you desired part of desired shape. PMMA injection molding is very popular and very effective manufacturing method for produce high quality plastic parts and prototypes. In this process, resin or PMMA material is heated at its melting point, when it is liquefied then it is injected under high pressure into metal dies and then cooled rapidly. After some time, it transforms into desired shape and then few finishing process is done on it to get what exactly is required. Injection molding process is widely used in different industries like electronics, manufacturing industry, automobile industry etc.
Get 7-day standard lead times on simple parts between 0.5 in. x 0.5 in. and 4 in. x 3 in. Upload your part to see if it’s eligible.
Get 7-day standard lead times on simple parts between 0.5 in. x 0.5 in. and 4 in. x 3 in. Upload your part to see if it’s eligible.
The process involved many steps until a final prototype or product is fabricated. The first step in prototyping of plastic injection molded parts is design of part. In initial phase you have to determine the feasibility of product and its production and nothing to do with size of product.
The inject molds often use steel but for production of injection mold prototype, Aluminum is used because it is best heat dissipater and it gets cool and heated very quickly. Another advantage of aluminum molds that it improves better flow of molten material in it and ultimately reduce risk of defective parts.
Now the next phase is designing the geometry of molds that give a shape to the part. The mold includes the pins that help in ejection of part after its formation and the flow of water lines in the mold that helps in cooling pf molten material in mold. The tool build is a way of creating molds. The design of mold is first drawn on computer which is called computer aided drawing.
There usually two options for making clear and fine parts i.e. glass and acrylic and glass become useless when we move away from plane and flat surfaces. Now we are left with acrylic which is used to fabricate translucent and high finished plastic parts. There exist several techniques for the rapid production of PMMA clear parts and its prototypes. At Wayken, we incorporate various rapid prototyping techniques in order to make sure that you get your prototypes in the most cost and time effective way possible along with superb quality. Besides acrylic injection modling, CNC machining is commonly used if any geometry is complex and requires hand polishing. In CNC machining, you can design prototype with huge complexities and with perfection.
Acrylic is widely used material and perfect substitute of glass. Because of its moderate properties and low cost it is now becoming a prototyping material for different manufacturing industries and even it is highly used by student in universities for making their projects or prototypes for their future projects.
Micro molding involves more than just using a small machine. The secret to making many tiny parts that are very close together is to control heat in the micro mold. To do this, micro injection molding machines have sophisticated temperature sensors and digital microcontrollers that are more precise than their larger cousins.
PMMA clear parts are an excellent substitute for glass. They are commonly used in aquariums at both commercial and residential scales. PMMA is also commonly used as viewing ports as well as complete pressure hulls for deep sea submersible because it is highly flexible, durable and low cost. The finished products made of its materials and pmma clear parts are also used in the lenses of the headlights and backlights of automobiles. Since it gives better protection against thrown objects, many safety vehicles such as that used for riot control often deploy PMMA as its main material for the windows. Many buildings use PMMA instead of glass for its windows due to its superior strength.
PMMA or acrylic is thermoplastic with high transparency, high flexibility, and chemical resistant, weather-resistant and light weight. It is preferred over poly-carbonate (PC) because of its properties i.e. easy to process, low cost and flexibility. PMMA material is widely used in rapid manufacturing industries to fabricate fine prototypes. As acrylic is thermoplastic which means it can be liquefied at its melting point and can be restored to its original shape upon cooling. So, this feature of PMMA or acrylic makes it perfect for injection molding.
Injection molding is another common method used for the rapid manufacturing of the prototypes. Low volume injection molding is ideal for 100 to 10,000 parts. Vacuum casting can also be used likewise. However, both these techniques are usually used for the lesser complex geometries. We will discuss PMMA injection molding in detail.
We leave nothing to chance when it comes to testing and verifying all raw material. People trust Star Rapid when the job absolutely has to be right.
Most conventional plastic resins are supported for micro molding, but it may not be possible to use additives (glass fiber reinforced) because this will impede the flow through a small gate.
Steel molds are used when there is high production of molded parts. Steel molds are not compatible with prototype injection molding.
PMMA prototypes and its products are commonly used in the medical industry as well. Contact lenses and eyeglass lenses are often made using PMMA since they are less brittle as compared to glass. PMMA also has such good compatibility with human tissue that allows it to be used in the treatment of cataracts. Parts made with PMMA have been widely used in bioprocess chromatography, treatment of tuberculosis and cosmetic surgeries etc. Along with these, for denture teeth, this is the best material of choice as well.
There are many cutting-edge technologies that need small, lightweight, and strong parts. For all of these and more, micro injection is an ideal solution. Our services can also scale up from a few grams to shot weights of 300 grams or more.
Our toolmaking specialists carefully analyze every project in advance. We work closely with you to optimize for speed, quality, and reduced cost.
Even micro parts can sometimes need some form of post-finishing. We polish, plate, and machine even small pieces just like full-sized ones.
If you need to manufacture small plastic parts and components with micron tolerances, micro molding is your solution. This specialized process uses tiny molds and dedicated machinery to create high-precision small parts with a minimal investment. To get your micro molding project done right, you need a team with experience working successfully at this small scale. Here’s why Star Rapid is the smart choice.
Since we launched our exclusive micro injection mold service, our customers are reaping the benefits that come from optimal cycle times and minimal waste.
Part size is mostly limited by gate size. Shot weight is limited to a few grams, and part size is normally 3mm2. Consult our engineers to discuss micro molded part sizes smaller than this.
The barrel of the micro injection molding machine is much shorter than its full-sized counterpart. This makes it fast and easy to clean when changing over to new material. The greatest advantage of micro injection is that the micro molding machine can be cycled much more quickly while at the same time consuming far less resin. This results in great cost savings and reduced production time.
Our proprietary algorithm generates accurate quotations fast. But every one is still checked by industry veterans for complete reliability.
Mold tools for micro molding are the equal of their full-sized counterparts and can last for 100K cycles or more, depending on resin.
GETTING A QUOTE WITH LK-MOULD IS FREE AND SIMPLE.
FIND MORE OF OUR SERVICES:
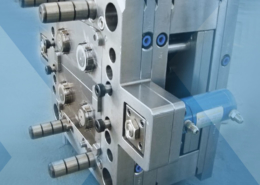
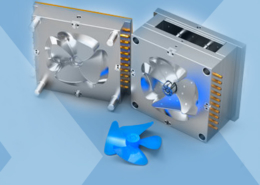
Plastic Molding

Rapid Prototyping
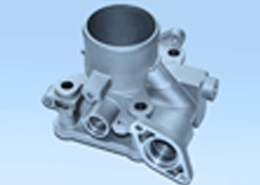
Pressure Die Casting
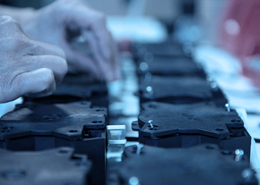
Parts Assembly
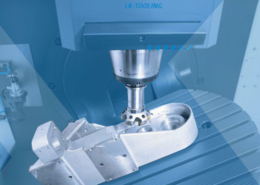