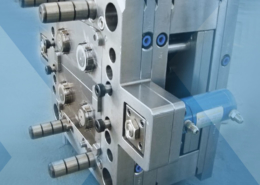
Exploring Plastic Molding in Electrical Applications: Innovations and Insights
Author:gly Date: 2024-06-08
Introduction
Plastic molding in electrical applications stands at the nexus of two dynamic industries, offering a blend of technological innovation and practical utility. From miniature components in consumer electronics to robust enclosures in industrial machinery, plastic molding plays a pivotal role in shaping the modern landscape of electrical engineering. This article delves into the intricacies of plastic molding within the realm of electrical applications, examining its significance, techniques, advancements, challenges, and future prospects.
Significance of Plastic Molding in Electrical Engineering
Integration of Plastics
Plastics have become indispensable in electrical engineering due to their versatility, durability, and cost-effectiveness. From insulating components to structural housings, plastics offer a myriad of benefits that enhance the performance and longevity of electrical devices and systems.
Miniaturization and Component Complexity
The advent of plastic molding techniques has facilitated the miniaturization of electrical components, enabling the design and production of intricate parts with precise tolerances. This advancement is particularly crucial in industries such as telecommunications, where the demand for smaller, more powerful devices continues to drive innovation.
Environmental Considerations
Plastic molding in electrical engineering is increasingly influenced by environmental considerations, with a growing emphasis on sustainable materials and manufacturing processes. The development of biodegradable plastics and eco-friendly molding techniques reflects a broader commitment to reducing the environmental impact of electrical products throughout their lifecycle.
Techniques in Plastic Molding for Electrical Applications
Injection Molding
Injection molding remains a cornerstone technique in the production of plastic components for electrical applications. Its ability to produce complex geometries with high precision and efficiency makes it well-suited for mass production of items such as connectors, switches, and enclosures.
Insert Molding
Insert molding enables the integration of metal components, such as terminals and contacts, directly into plastic parts during the molding process. This technique enhances assembly efficiency, improves product reliability, and reduces the need for additional fasteners or adhesives.
Overmolding
Overmolding involves encapsulating pre-formed substrates, such as circuit boards or cables, with thermoplastic materials to provide protection and insulation. This technique enhances the durability and functionality of electrical assemblies while offering design flexibility and aesthetic appeal.
Challenges and Innovations
Material Selection and Compatibility
Selecting the appropriate plastic material is critical to ensuring optimal performance and longevity in electrical applications. Factors such as mechanical strength, thermal conductivity, and chemical resistance must be carefully considered to mitigate risks of degradation or failure.
Thermal Management
The increasing power densities and operating temperatures of electronic devices pose challenges for thermal management in plastic-molded enclosures. Innovations in materials, design, and ventilation systems are essential to dissipate heat effectively and prevent overheating-related issues.
Design for Manufacturability
Designing electrical components for plastic molding requires careful consideration of manufacturability factors such as draft angles, wall thicknesses, and undercuts. Utilizing advanced design tools and simulation software can streamline the development process and optimize part quality and consistency.
Conclusion
In conclusion, plastic molding plays a pivotal role in advancing the field of electrical engineering, enabling the creation of innovative products that power our modern world. From enhancing miniaturization and component complexity to addressing environmental concerns and technical challenges, plastic molding continues to drive progress and shape the future of electrical applications. By embracing new materials, techniques, and design methodologies, engineers and manufacturers can unlock new possibilities and elevate the performance, reliability, and sustainability of electrical products. As we navigate towards a future defined by connectivity, efficiency, and sustainability, plastic molding remains a cornerstone of innovation and progress in the realm of electrical engineering.
GETTING A QUOTE WITH LK-MOULD IS FREE AND SIMPLE.
FIND MORE OF OUR SERVICES:
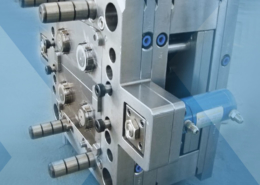
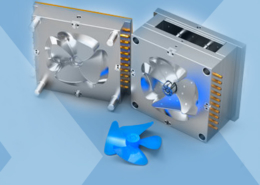
Plastic Molding

Rapid Prototyping
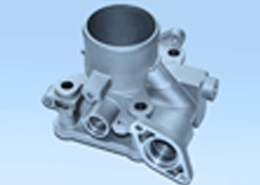
Pressure Die Casting
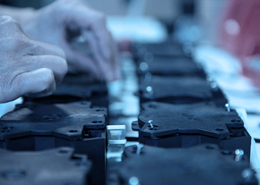
Parts Assembly
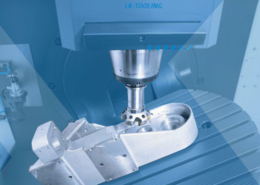