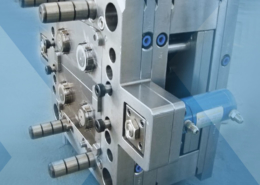
Haitian Group: Home - haitian injection
Author:gly Date: 2024-10-15
Mirror polishing raises the cost of injection molding since it necessitates the use of hardened steels in the molds and a healthier injection molding environment. Another factor for cost increases is a higher texturing need.
Still another way to reduce molding costs, depending on your part volumes, is to consider on-demand manufacturing. At Protolabs, two injection molding service options are available (see table below). One is best suited for those who need smaller part quantities, usually associated with prototyping. The other option, Protolabs calls it on-demand manufacturing, is a good fit for those who require slightly larger part quantities, typically up to 10,000-plus parts from aluminum molds. On-demand production can be a great option to manage demand volatility of your parts, reduce total cost of ownership, and leverage cost-efficient bridge tooling.
The purpose is to inspect and test the construction for stability, functionality, and beauty. The prototype would be reconfigured and printed for a second review if there were any problems or changes that needed to be made to the design. This is repeated until the design is complete. Mold-making can then proceed after the part design is finalized and approved.
Take portion extent into consideration always. In the molding language, this implies how large the component is and it is comfortable in the mold and allows the mold to work sprues, runners, ejector pins, and all the others.
Then explore an option to overmold. This may cost you earlier, depending on the part, but may save you money afterward. For example, there might be an extra expense to over form a gasket on a part upfront, but then you will be able to save money by manually installing a gasket.
Plastic mold making technology is the procedure for making plastic items that involve injecting melted material into a mold. There are various steps to the procedure. First, the part is meticulously designed, with accurate dimensions and other structural requirements. The part is then prototyped to create a more tangible sample.
Textured surfaces, molded part numbers, and company logos look cool, but be prepared to pay a bit extra for these and other non-mission critical features. That said, permanent part numbers are a requirement for many aerospace and military applications. Use a mill-friendly font such as Century Gothic Bold, Arial, or Verdana (san-serif fonts), keep it above 20 pt., and don’t go much deeper than 0.010 to 0.015 inch. Also, be prepared to increase draft if part ejection is a concern.
There are several costs associated with the injection molding process. You may be reading this article out of curiosity, or as part of your research, either way, you all have the same question in mind. How much does injection molding cost? To start with, the injection molding process is responsible for the production of items such as auto molds. This means that it does demand attention to detail – a skill you should have while reading through this article.
Our digital factories create prototypes and low-volume parts fast, while our manufacturing network, offers advanced capabilities and volume pricing.
Custom plastic molding costs can vary in different parts of the world. China molding injection molding costs, for example, are relatively cheaper compared to those in other parts of the world, due to the manufacturing conditions specific to the country. However, it is important that your focus on the core plastic injection molding production before adding optional parts, to reduce the cost overrun associated. We do recommend that you pay attention to detail in the above-mentioned factors before starting. If you need any help, please contact us to get professional plastic injection molding service.
Got a family of parts that all fit together? How about multiple molding projects at one time? There’s no reason to build a mold for each individual part, provided A) everything is made of the same plastic, B) each part is roughly the same size (e.g., have similar processing times), and C) can all be squeezed into the same cavity, while still allowing for proper mold functioning.
Finally, consider an overmolding option. Depending on the part, it might cost you more upfront, but could potentially save you money later. For example, overmolding a gasket on a part upfront might be an added cost, but it can save costs later from having someone install a gasket manually.
Our helpful design aid demonstrates part features that are too thin or too thick, bad bosses, right and wrong ribs, and other considerations to be mindful of while designing parts for injection molding.
In addition, maybe you can join some of those parts with a living hinge? This method is a great way, for example, to mold two halves of a clamshell-style container. These parts would otherwise need a pin-type assembly to open and close. The only caveat here is that a flexible and tough material must be used, such as polypropylene (PP).
Undercut features complicate and, in some cases, prevent part ejection. Get rid of them if you can, but maybe that’s not possible, if, for example, you need a side action, sliding shutoff or pick out. One alternative may be using sliding shutoffs and pass-through cores, or by changing the parting line and draft angles to provide an easier mold build. These reduce tooling costs as you avoid additional pieces to the mold that add to manufacturing costs. In addition to the rise in manufacturing costs of using hand-loaded inserts, this also may have an impact on your piece part price because of longer cycle times and manual mold operation.
The aim is to give you a better understanding of the costs incurred while conducting the injection molding process. We do hope that by the end you will be in a better place. Do enjoy!
Textured surfaces, molded component numbers, and business logos are all attractive but expect to pay a premium for these and other non-essential features. Permanent component numbers, on the other hand, are required in many aerospace and military applications. Choose a mill-friendly font and maintain the font size above 20 pt., and go no deeper than 0.010 to 0.015 inches. Also, if the component ejection is a worry, be ready to increase the draft.
Maybe for certain medical components or two mobile radio interlocking halves, you’ll build a snap case. Why construct two components if one can be made? Refine the snaps to fit halves on either side so that a so-called ‘universal’ part is built. Only one mold is necessary, which saves production costs in advance. Now, instead of half the amount of two, you may shape twice as many of one part.
There are similarities to the custom plastic molding costs associated with mold making in China, Totaling parts of the world. To make this easier, we can classify the issue into two parts;
Undercut characteristics make part ejection more difficult and, in some situations, impossible. If you can, get rid of them. These save tooling costs by obviating the need for additional mold components, which raise production prices.
Everyone wants to save money on manufactured parts. It sounds simple, but one of the easiest ways to reduce price-per-piece cost in injection molding is by increasing part quantity. That is because the initial upfront cost to design and machine the mold amortizes over more parts. At Protolabs, for example, up to 25,000 parts or more can be molded from the same tool.
Maybe you’re designing a snap-together case for some medical components, or two interlocking halves of a portable radio. Why build two mating parts when you can make one? Redesign the snaps so that the halves can be fit together from either direction, thus building a so-called “universal” part. Only one mold is needed, saving production expenses up front. And you can now mold twice as many of one part, instead of half the quantities of two.
While injection molding may appear to be more expensive than methods such as CNC machining and 3D printing, its ability to scale and produce thousands of pieces makes it a cost-effective large-scale production alternative.
In addition to per-unit costs, consider the material. Many plastics overlap in strength and functionality, but some are inherently easier to mold, driving down part costs. You can experiment with different materials in the interactive quote you receive when you upload your design to Protolabs.
It is relatively easy to remove metal from an existing metal mold. Adding metal, on the other hand, can be difficult or, for all practical purposes, impossible with rapid injection molding. To look at this from the part perspective, you can add plastic, but you can’t take it away. Designing with this in mind is called “metal safe.”
A design for manufacturing feasibility (DFM) analysis should accompany each quote for an injection-molded component. This indicates possible issues or design improvement possibilities. Lack of draft angles, ‘unusable’ features, unworkable geometric features—these are only a few instances of the parts to fix before you accept services.
On produced parts, everyone wants to save money. Increased part quantity is one of the simplest ways to lower price-per-piece cost in injection molding. This is because the upfront cost of designing and machining the mold is amortized over a larger number of pieces.
Pretty parts are nice, but they often require bead blasting, EDM, or high mold polish to achieve an elevated level of cosmetic appearance. This drives up tooling costs. Anything greater than a PM-F0 (as machined) finish requires some level of hand work, up to an SPI-A2 mirror finish using Grade #2 diamond buff. Avoid fine finishes such as these unless they’re required for the job. One thing to consider regarding cosmetics is to let Protolabs know if you need the entire half of the mold polished or maybe just one small area. You could save costs by only polishing the area needed versus the entire side of a mold. When requesting a custom finish, just send Protolabs a color-coded image of the critical areas and desired finish level for each area.
Mold life has a significant impact on tooling costs. Regular steels are used in prototype molds. However, hardened steel would be necessary for high-volume production molds.
However, maybe your molding project calls for only a handful of parts. No worries. Protolabs builds cost-effective molds for production quantities as low as 25 pieces, often within a few days of ordering.
This is similar to the above in that the cost breakdown in percentage would contain the same considerations. A proper percentage breakdown would have machining taking up the larger share, all the way down to designing costs. This could look like this:
Always consider part extents. In molding-speak, that means how big is the part, and will it fit comfortably in the mold while allowing for sprues, runners, ejector pins, and all the other considerations needed to make a mold work. Protolabs’ maximum part size for injection molding is currently 18.9 in. (480mm) by 29.6 in. (751mm) with a maximum depth from the parting line of 4 in. (101mm) deep. However, larger parts like these, in turn, require a larger mold. This may have an impact on your mold and part costs.
Tough Black (Loctite Henkel 3843) and Ceramic-Filled (BASF 3280) are two new advanced photopolymer materials now available for 3D printing.
Proto Labs, Inc. 5540 Pioneer Creek Dr. Maple Plain, MN 55359 United States P: 877-479-3680 F: 763-479-2679 E: [email protected]
1. Eliminate undercuts 2. Get rid of unnecessary features 3. Use a core cavity approach 4. Reduce cosmetic finishes and appearances 5. Design self-mating parts 6. Modify and reuse molds 7. Pay attention to DFM analysis 8. Use a multi-cavity or family mold9. Choose on-demand production option10. Consider part size11. Use overmolding
Maybe you are after a higher volume of parts? You can still achieve high volumes using aluminum tooling with two-, four-, or eight-cavity molds depending on size and part geometry that can reduce your piece part price, although this would impact your tooling costs.
ACIS®, Autodesk Inventor®, CATIA® V5,Creo™ Parametric, IGES, Parasolid®, Pro/ENGINEER®,Siemens PLM Software’s NX™, SolidEdge®, SolidWorks®, STEP
Mould Design: Designers and product engineers will overlook part color because they presume that piece cost for all hues is the same. If your part is white or transparent, however, the molding cost will be more than for other colors. Molding factories incur additional costs as a result of cleaner molding conditions.
If you need an electronics housing or similar box-shaped part, you can either sink the wall cavities deep into the mold base, requiring long thin tools to machine ribs into the mold, or machine the aluminum material down around the core and mold the part around it. The latter approach is known as a core cavity, and is a far more cost-effective method of molding tall walls and ribbed surfaces. Better yet, this makes it easier to provide smooth surface finishes, adequate venting, improved ejection, and can eliminate the need for super-steep draft angles.
Materials: The type of plastic molding material you choose will have an impact on both tooling and piece pricing, which varies depending on the material.
Aesthetic parts require beads blasting, EDM, or high-mold polishing frequently to get a high aesthetic look. This increases the cost of tools. Anything larger than PM-F0 (as machined) needs to do some handwork, with the use of a grade 2 diamond buff, up to an SPI-A2 mirror termination. Avoid such precise finishing unless they are needed for the work.
Some injection-molded parts go through multiple iterations until a final, workable design emerges. Instead of purchasing a new mold for every revision, a little clever planning will allow the same mold to be used multiple times. Starting with the smallest, most basic part design, mold as many pieces as needed, then re-machine the mold to include additional part features, or a larger, taller version of the same part, and mold again. This is not an exact science, but given the right part, this re-use approach can save dollars on tooling development.
While injection molding may seem costly compared to processes like CNC machining and 3D printing, the ability to scale and manufacture thousands of parts makes it a cost-effective solution for mass production. Determining the cost of injection molding is a combination of several factors. The main determinant of molding cost is the amount of time it takes to produce the tooling. This means, the more complex the part's geometry, the higher your manufacturing costs will be. Simple parts, without undercuts or more advanced surface finishes, will be the most affordable.
China injection molding costs will run between $1000 for small-scale production and $12000 for larger-scale production, depending on the quality/quantity of work. However, as the reputation goes, outsourcing large-scale processing would lower the custom injection molding cost in China as compared to any other way.
If you require housing for electronic products or a comparable box-shaped component, you may either sink the cavity deep into the molding floor or process the aluminum material all around the core and mold the part surrounding it using long and thin tools to make the ribs. The latter process, described as core cavity molding, is significantly more cost-effective for molding high walls and textured surfaces.
Get machined parts anodized and chromate plated with our quick-turn finishing option. Eligible materials include aluminum 6061/6082 and 7075.
Molding costs are heavily influenced by complexity. It necessitates more work and processes in the mold making process. The main reasons include tolerance requirements, exquisite detailing, or the number of undercuts. The best way to reduce your molding costs is to redesign your part as a simplified version.
Every quote for an injection-molded part at Protolabs is accompanied by a free design for manufacturability (DFM) analysis. This identifies potential problem areas, or opportunities for design improvement. Insufficient draft angles, “un-machinable” features, impossible geometries—these are just a few examples in which part designs can and should be improved before clicking the “accept” button. Be sure to review these suggestions thoroughly, and contact an applications engineer at Protolabs with any design-related questions.
GETTING A QUOTE WITH LK-MOULD IS FREE AND SIMPLE.
FIND MORE OF OUR SERVICES:
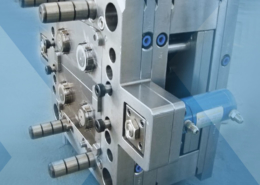
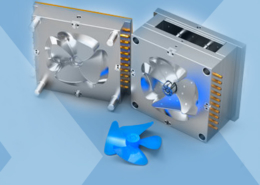
Plastic Molding

Rapid Prototyping
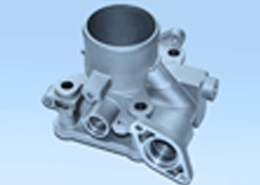
Pressure Die Casting
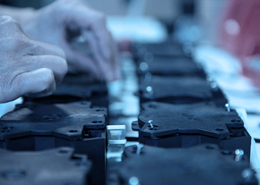
Parts Assembly
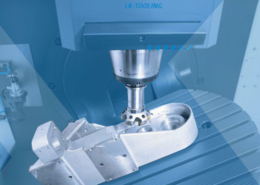