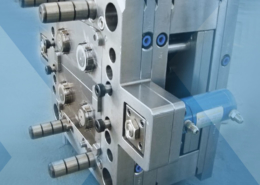
Glossary of Injection Molding Terms - injection part
Author:gly Date: 2024-10-15
10 The hopper The barrel The reciprocating screw The reciprocating screw is used to compress, melt, and convey the material. The reciprocating screw consists of three zones (illustrated below) the feeding zone the compressing (or transition) zone the metering zone
3 Overview Injection molding is the most widely used polymeric fabrication process. It is the primary process for manufacturing thermo plastic products. Injection molding can be used to form a wide variety of products. Complexity is virtually unlimited, sizes may range from very small to very large, and excellent control of tolerances is also possible. The major reasons that injection is so popular is that it produces light weight parts of specific color with built in surface texturing. Most polymers may be injection molded, including thermoplastics, fiber reinforces thermoplastics, thermosetting plastics, and elastomers.
1 Chemistry for Engineering Logistics POLYMERS AND POLYMER MATERIALS 1. Basic Terms in Polymer Chemistry 2. Manufacture of Polymer Products Department.
14 Hydraulic system Control system Clamping system The delivery system The delivery system, which provides passage for the molten plastic from the machine nozzle to the part cavity, generally includes: a sprue cold slug wells a main runner branch runners gates. FIGURE 6. The molded system includes a delivery system and molded parts.
9 Machine components Injection system The injection system consists of a hopper, a reciprocating screw and barrel assembly, and an injection nozzle, as shown in Figure 1. This system confines and transports the plastic as it progresses through the feeding, compressing, degassing, melting, injection, and packing stages. FIGURE 1. A single screw injection molding machine for thermoplastics, showing the plasticizing screw, a barrel, band heaters to heat the barrel, a stationary platen, and a movable platen.
5 Types of Injection Molding MachinesHand injection molding machine Piston type injection molding machine Reciprocating type injection molding machine
7 Injection molding machine is divided into 3 units i. eInjection molding machine is divided into 3 units i.e. a clamping unit, an injection unit and mold. The functions of the clamping unit are opening and closing a die, and the ejection of products. There are 2 types of clamping methods, namely the toggle type shown in the figure below and the straight-hydraulic type in which a mold is directly opened and closed with a hydraulic cylinder. The functions of the injection unit are to melt plastic by heat and then to inject molten plastic into a mold.
4 Injection molding Injection molding is a method to obtain molded products by injecting plastic materials molten by heat into a mold, and then cooling and solidifying them. The method is suitable for the mass production of products with complicated shapes, and takes a large part in the area of plastic processing. Advantages of Injection Molding High production rates Wide range of materials can be used Low labor costs Minimal scrap losses
17 Typical Applications Injection molding is widely used in a wide variety of industries: automotive, appliance, computer, communication and industrial equipment. Examples of injection molded parts in the automotive industry include sail panels, radiator end caps, door panels, lamp housings, and fuel rails. Radiator End Cap Automobile parts Automotive Sail Panel Fuel Rails with Injectors
12 The nozzle FIGURE 3. (a) Nozzle with barrel in processing position. (b) Nozzle with barrel backed out for purging. Mold system The mold system consists of tie bars, stationary and moving platens, as well as molding plates (bases) that house the cavity, sprue and runner systems, ejector pins, and cooling channels, as shown in Figure 4. The mold is essentially a heat exchanger in which the molten thermoplastic solidifies to the desired shape and dimensional details defined by the cavity.
18 Injection Molding Problems and SolutionsFault Air trap Black streaks Flash Short shot Sink mark Solution Reduce injection speed, Proper venting. Lower the barrel temp. Clean the injection unit. Adjust the clamp force. Reduce the injection pressure. Increase the injection value. Increase the cooling time.
We think you have liked this presentation. If you wish to download it, please recommend it to your friends in any social system. Share buttons are a little bit lower. Thank you!
11 FIGURE 2. A reciprocating screw, showing the feeding zone, compressing (or transition) zone, and metering zone.
Introduction to Engineering Plastics. During this unit we will review: Classifications of Plastics, Characteristics of thermoplastics, Definitions of.
16 Cycle time in injection moldingThe injection molding cycle can be divided into several stages. They aremold closing, filling, packing, cooling, mold opening and ejection as shown here. Cooling Time is a major fraction of the total cycle time. Materials for injection molding Acrylonitrile butadiene styrene (ABS) Polyethylene Polypropelene Polystyrene
Eco-Houses Based on Eco-Friendly Polymer Composite Construction Materials Conventional molding techniques applied for manufacturing of eco-composites Workshop.
20 References Injection Molding Hand Book Theory of Molds WWW.Google.comDominick V Rosato Donald V Rosato Theory of Molds R S Nagesh
2 Plastic Injection Molding· Overview · Injection Molding · Injection Molding machine · Injection molding processes · Injection molding materials · Injection molding problems and solutions · Typical applications and Products
19 Conclusion As the injection molding technology is now living its most rapid development times. The most important factors behind this situation is There is no potential competitors Injection molding is especially suitable for mass production. The profitable molding in today’s competitive market depends on precise clamping action coupled with both high plasticizing performance and reliability integrated with complete plant operating performance.
CAE Simulation software provides tools that help manufacturers validate and optimize the design of plastic parts and injection molds by accurately predicting.
15 Injection molding processesThe Injection molding process basically is divided into 6 major steps 1. Clamping 2. Injection 3. Dwelling 4. Cooling 5. Mold Opening 6. Ejection
UNIT 16: Extrusion and Injection moulding Manufacturing Engineering Unit 16 Copyright © 2012 MDIS. All rights reserved. 1.
GETTING A QUOTE WITH LK-MOULD IS FREE AND SIMPLE.
FIND MORE OF OUR SERVICES:
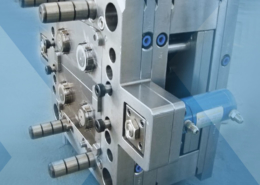
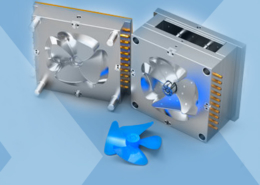
Plastic Molding

Rapid Prototyping
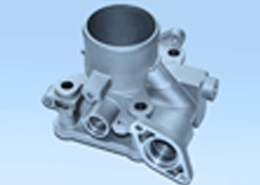
Pressure Die Casting
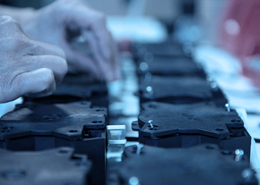
Parts Assembly
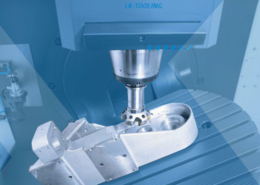