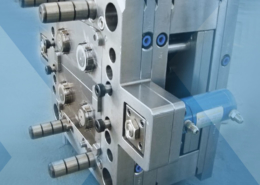
Glossary of Injection Molding Terms - injection part
Author:gly Date: 2024-10-15
On the one hand, as melt temperature increases, melt viscosity decreases; on the other hand, as melt temperature increases, the thickness of the solidification layer decreases, meaning an increase in the actual opening size, i.e. equivalent radius, of the melt filling channel, as shown in Figure 5. Providing that the injection pressure and melt flow rate are kept unchanged, the decreased melt viscosity and increased equivalent radius should conduce to an increase in melt flow length. Bear in mind that the increased temperature still shall be within the range suggested in the material manufacturer’s process guidance for the plastic material.
Note: Keep in mind that the melt flow length referred to in the formula is the distance between the injection point at the machine nozzle and the farthest position where the melt can reach in the part cavity; it includes the length of the runner section. Therefore, with a given melt flow length driven by the same conditions of pressure drop, flow rate, melt viscosity, and the equivalent radius, as one designs the runner shorter, the position where the melt can reach in the part cavity will be farther; it increases the chance of solving the short shot problem.
In a modern injection molding machine, the actual injection pressure is a result driven by the setting of injection speed. As the set value of injection speed increases, the flow rate increases, and the machine automatically increases the required injection pressure to bring about the desired injection speed unless one has set a pressure limit for the machine. Thus, the increases in both melt flow rate and pressure loss happen at the same time counteracting each other’s effect so that the simultaneously induced melt viscosity and equivalent radius effects become dominant to the melt flow length.
Additionally, for short shot type 2 as illustrated in Figure 4, it is advisable to place the gate at the opposite position from where the significantly thinner rib is far. In such a design, the melt turns back to fill the rib in a much shorter time after it has filled the other extremities of the part; at that time, the hesitation effect in the rib just starts and the melt state therein is still far from solidification.
Many people simply attribute short shot to an insufficient injection pressure provided by the injection molding machine’s pressure setting. However, theoretically speaking, a short shot should be holistically considered as the consequence caused by an incapable engineering system of injection molding, which cannot drive the molten plastic material to the place where it is expected to be on the part. When talking about an engineering system of injection molding, it involves the perspectives from not only its injection molding machine, but also process condition, mold design, part design, and plastic material.
Note: At first glance at the formula in Figure 2, one might argue that as injection speed increases, it also means the melt flow rate increases at the same time, so that the melt filling length should be shorter and it should be worse for solving the short shot problem? The reason why the effect of flow rate does not dominate the flow length herein is explained as follows.
As suggested by the formula in Figure 2, the contributive factor from a mold to an increase in the melt flow length is quite plain. Assuming that the injection molding engineering system performs under the same conditions in pressure loss, melt flow rate, and melt viscosity, as the equivalent radius of a cold runner and gate system increases, the melt flow length increases, and the risk of short shot decreases. Accordingly, the straightforward remedies are as follows.
Assuming that the injection pressure, injection speed (i.e. melt flow rate), and melt temperature are not changed, as mold temperature increases, the positive effect on the actual opening size of the melt filling channel takes place too. As illustrated in Figure 5, higher mold temperature brings about thinner solidification layers across runner diameter and part thickness, resulting in wider spaces (i.e. equivalent radius) along the melt flow path in runner sections and part cavity that facilitate the melt to fill farther in the part cavity and reduce the risk of the short shot problem.
First established in 1968 at Thane, Maharashtra, a small company located in an industrial estate has now expanded to 3 different locations across India and has created a global presence for itself. Our state of the art manufacturing unit is capable to produce any plastic component through the injection moulding process. We are the first choice for most multinational companies when it comes to moulding plastics for industries like Electrical, Automotive, Textile, Medical Lab Equipment, and Kitchenware. The trust our customers show in us constantly motivates us to innovate, come up with solutions and deliver outstanding quality and service.
Aurangabad - GUT No 30, Plot No 01, Ranjangaon (SP), Near MIDC Waluj Near K-74, Opp R K Press Turn Eng, Aurangabad, Maharashtra 431136, India.
Similar to increasing melt temperature but with a stronger effect, for short shot type 2, an increase in mold temperature also helps by rendering a longer time that the melt gets solidified in the rib; when the melt has filled all other extremities of the part, it turns back to fill the rib if the previously filled melt therein has not solidified yet.
Aurangabad - GUT No 30, Plot No 01, Ranjangaon (SP), Near MIDC Waluj Near K-74, Opp R K Press Turn Eng, Aurangabad, Maharashtra 431136, India.
<2> There is a problem called air trap, which often is confused with the short shot. Let’s talk about it separately in another article.
Before trying to find remedies for a short shot problem, one should distinguish between two types of the problem, which involve the distance between the short shot position and the mold cavity gate. In the first type, the short shot occurs at the extremities of the flowing melt far from the mold cavity gates, as shown in Figure 3. In the second one, the short shot happens at upstream positions of the flowing melt nearby the mold cavity gates, as shown in Figure 4.
For short shot type 2, an increase in melt temperature also helps by rendering a longer time that the melt gets solidified in the rib; when the melt has filled all other extremities of the part, it turns back to fill the rib if the previously filled melt therein has not solidified yet.
<1> With a set-up that is supposed to provide a fixed engineering system condition combining the effects on pressure loss, melt flow rate, melt viscosity, and the equivalent radius, do a progressive short shot test and short shot sample collection (with the pack/hold function switched off or set zero) to ensure that the problem is not caused by insufficient injection stroke or premature V/P switch from filling to packing/holding stage.
Likewise, an increase in part thickness means an increase in the equivalent radius and results in a longer melt flow length thus more possible to avoid the short shot problem. Notice that a minor increase in part thickness might bring about a great improvement in solving the short shot problem. As indicated in the formula, the increase in the equivalent radius can bring about an exponential effect on the melt flow length as high as the fourth power. In other words, a 10 percent increase of the equivalent radius would bring about a 46.4 percent increase in the melt flow length.
Therefore, for short shot type 2, a minor increase in the rib thickness would be a great help in solving the short shot problem therein.
In case the part thickness design and the diameter/size design of the runner/gate system cannot be changed, the process condition has set melt temperature, mold temperature and injection speed at their highest levels allowed, and the injection pressure limit is set at 90 percent of the machine’s capacity, but the short shot still exists while the actual maximum injection pressure has reached the pressure limit, one might consider molding the part at other machines which have higher capacities in injection pressure and injection speed.
This holistic consideration comes from the theoretical formula that we use to estimate the pressure loss needed to drive plastic melt advancement in a cold runner system, as shown in Figure 1. The scope of the formula’s conceptual application can be extended into its downstream mold cavity to estimate the pressure loss required to fill the length of a molding part, therein the effect of part thickness is equivalent to that of runner radius. Alternatively, by transforming the formula, one can estimate the melt filling length that an engineering system of injection molding is capable to reach, as shown in Figure 2.
<2> When doing the progressive short shot test and short shot sample collection, make sure that the injection pressure limit is set higher enough than the actual maximum pressure needed during the filling stage. It simplifies the situation so that the melt flow length increase is purely contributed by the required increase in injection pressure, rather than by the resulting decrease in the melt flow rate after the injection pressure has reached the set limit.
Short shot is a defect of injection molding parts on which the parts’ outlines or features are not completely formed by the injected plastic materials.
The formula in Figure 2 tells us that changing to a material that is more flowable with lower melt viscosity will help increase melt flow length and solve the short shot problem. Although theoretically correct, it should be the last resort to take without rushing into it before all other remedies have been tried. Generally, more flowable materials with lower viscosities are inferior, especially in mechanical properties; they could cause the molded parts not to meet application requirements in end-user environments.
With the theoretical concept imparted by the formula in Figure 2 in mind, one can develop corrective/preventive solutions for a short shot problem in process condition, mold design/manufacture/construction, part design, plastic material, and injection molding machine, respectively. Considering the effects on the factors involved in the formula – melt viscosity, equivalent radius, pressure loss (presented by injection pressure), and volumetric melt flow rate - any remedies that conduce to an increase in melt flow length mean opportunities for solving the short shot problem.
Different from increasing melt or mold temperature, for short shot type 2, an increase in injection speed also helps but by rendering a shorter time that the melt to fill the other extremities of the part; thus, it turns back to fill the rib in time before the previously filled melt therein gets solidified.
Additionally, one should select a machine on which the injection stroke required for the filling stage occupies more than 25 percent, as a start point, of the machine’s metering stroke capacity. Too short injection stroke might make a high injection speed setting in vain because the process could reach the V/P switch point before the high injection speed is performed.
There is a method available on the market that addresses issues in the area that may be difficult to resolve with just "tuning" of the moulding process. Have a look at www.roctool.com (or/and www.roctool.cn). By heating the mould to near the glass temperature (Tg) at point of injection and then cooling rapidly you can inject at reasonable speed, using moderate melt temperature and using the mould temperature that is the true right for each phase of the injection, holding and cooling phases. Call, mail or PM me to learn more!
For short shot type 1, it is the consequence that the injection pressure powered by the injection molding engineering system cannot produce the melt flow length long enough to completely form the extreme outline of a molding part. For short shot type 2, while the melt is advancing towards other extremities of the molding part, its advancement in the significantly thinner rib nearby the gate becomes slower and slower (called hesitation effect), resulting in the decreasing and decreasing melt temperature therein and eventually that the melt solidifies and stops filling halfway in the rib.
<1> The discussion in this article is specifically for solving a short shot problem. If other quality issues are involved and must be solved at the same time, further cross-issue and case-by-case consideration might be required.
In terms of the filling melt’s viscosity, as injection speed increases, it creates a greater shear heating effect that not only prevents the melt temperature from decreasing during the filling stage but produces even higher temperature on the partial melt adjacent to solidification layers, resulting in a decrease in overall melt viscosity. Additionally, such a shear heating effect due to increasing the injection speed conduces to thinner solidification layers and wider melt flow channels (i.e. bigger equivalent radii), as shown in Figure 5. As a result, the decreased melt viscosity and increase in the equivalent radius of the melt flow channel conduce to a greater flow length in the part cavity thus reducing the risk of the short shot problem.
GETTING A QUOTE WITH LK-MOULD IS FREE AND SIMPLE.
FIND MORE OF OUR SERVICES:
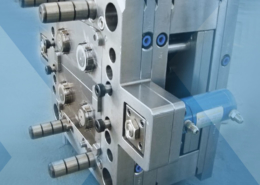
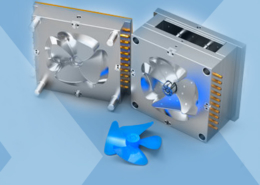
Plastic Molding

Rapid Prototyping
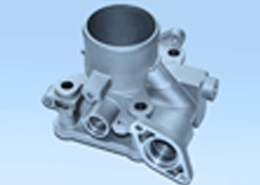
Pressure Die Casting
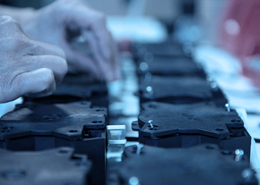
Parts Assembly
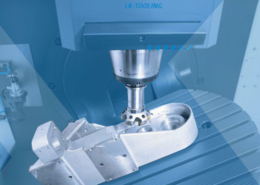